Cerexio Service Request Management System
Cerexio Service Request Management System is a unified digital solution that piled up the true essence of Industry 4.0 capabilities to provide the best service management for the manufacturing industry. This smart, consolidated platform assembles people, data, and systems through Predictive Analytics, GIS, Digital Twin, AI, and IoT to ensure smooth machinery operation within the manufacturing plants. The Cerexio solution guarantees error-free workflow automation with its traceability, analysis, and request configuration capacities for the end user.
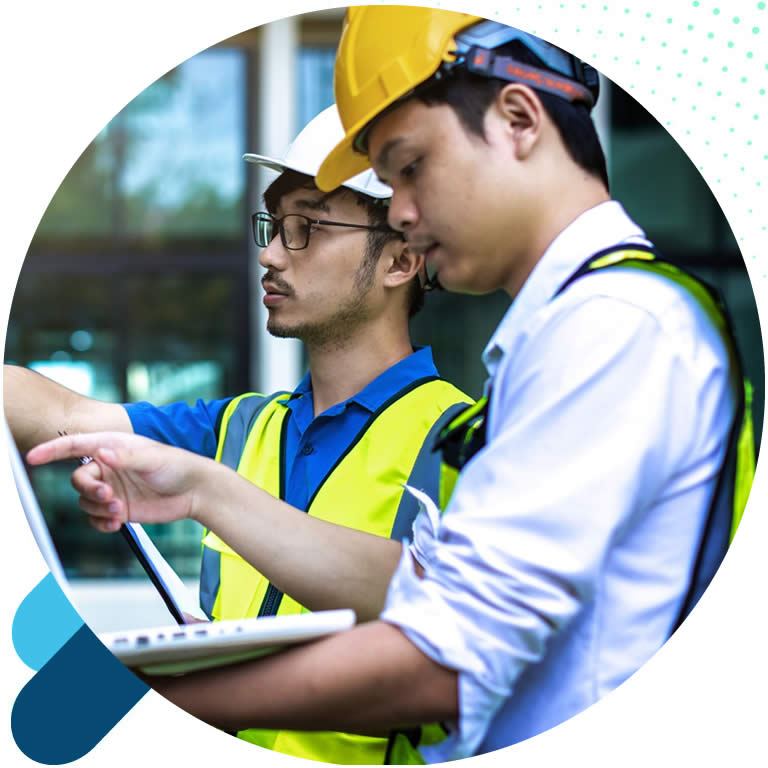
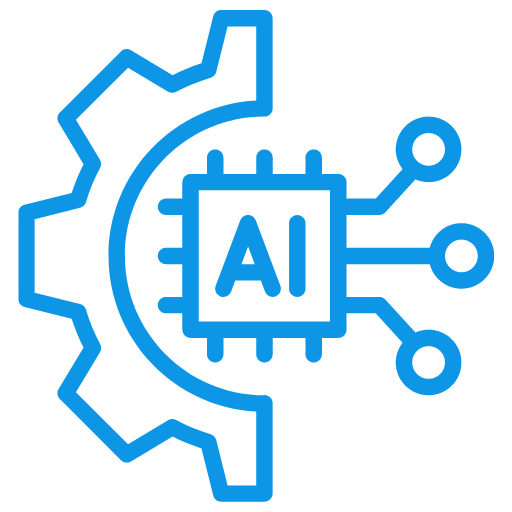
AI-Powered AutomatedHub
AI integration transforms servicing workflows, optimising efficiency and responsiveness within the factories as it is capable of automating service request configuration processes, from request initiation to resolution, ensuring precision and speed, and providing an unparalleled solution.
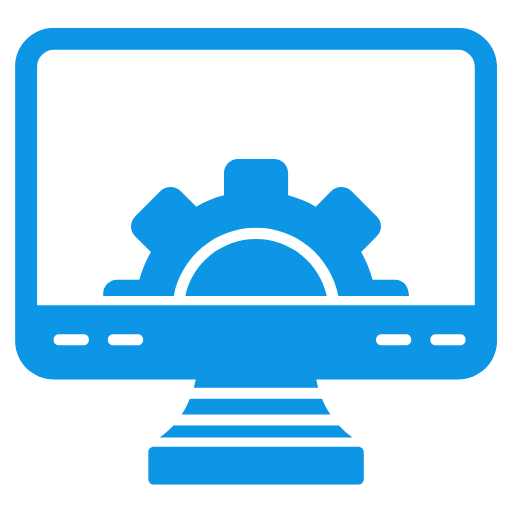
IoT-Dominated Asset Management
IoT connectivity backs up real-time monitoring, predictive maintenance, and a data-driven ecosystem as it provides a comprehensive view of assets. Integration with IoT ensures a smoother operational landscape to maintain heightened responsiveness and efficiency.
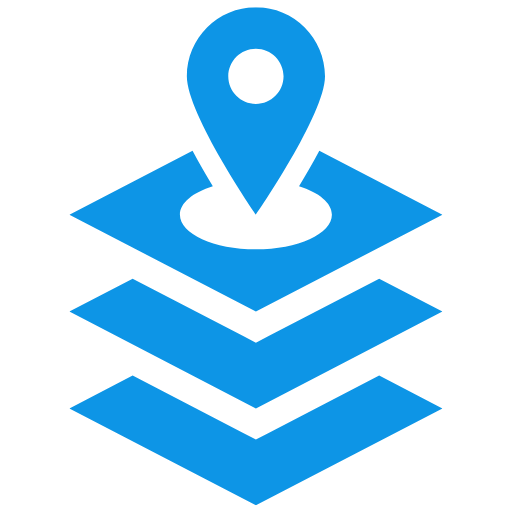
GIS Mapping Task Minder
GIS mapping power spans the overall task management from its initial point to the resolution from the supervisor’s extremity. The advanced dashboards offer a real-time view of the assigned tasks and the time taken to accomplish them.
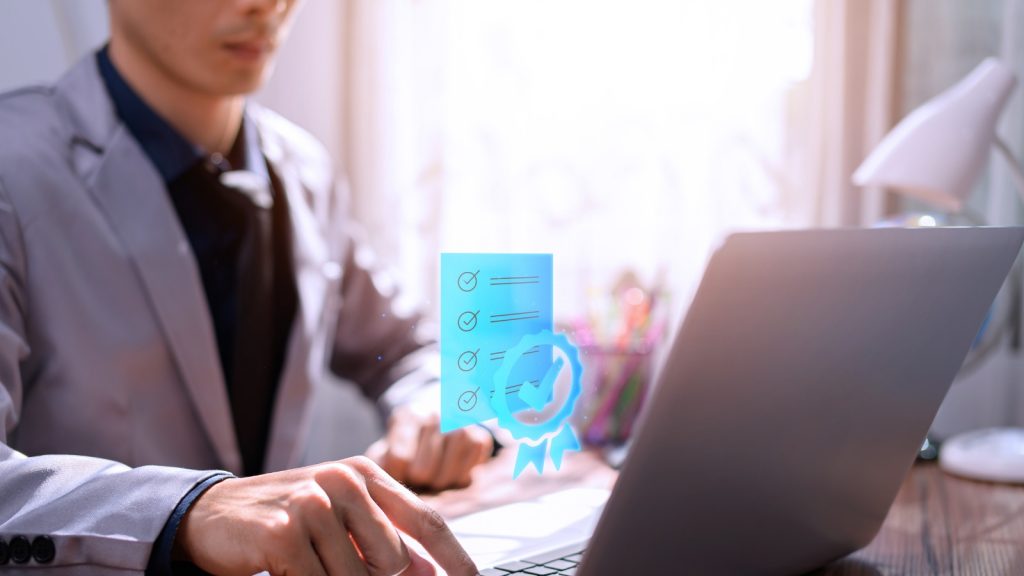
Why do you need the Cerexio Service Request Management System?
An updated calendar feature with status tags for the convenience of task tracking.
Asset malfunctioning spotting system powered by smart Sensors, CCTV, RFID, and IoT tracking solutions.
Automate process requests and robust request configuration to offer a personalised service experience.
Interconnects the end users and the service providers under one singular grandstand.
Laser Technology dominated real-time asset health monitoring to avoid unexpected downtime.
Efficient inventory management to ensure the service execution is unchallenged.
Tasks and time tracking embedded management from the service provider’s periphery.
Workflow management for real-time asset management being the ‘technological broker’.
Save Money and Time with A Full Spectrum Service Enabling Solution
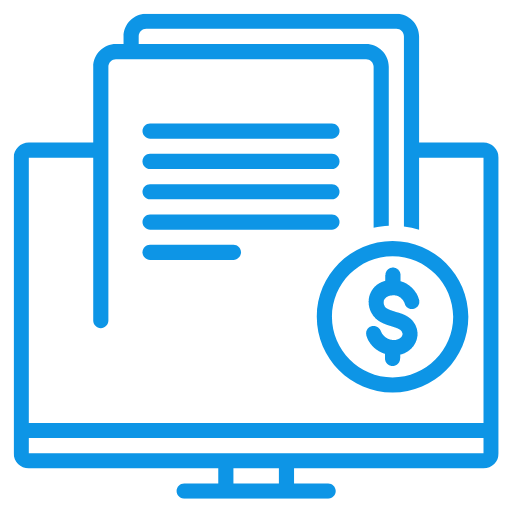
Automated Invoicing
The automated invoicing feature in our system streamlines the billing process by computerising the generation and delivery of invoices. Upon task completion, the system automatically calculates the expenses and generates the final bill, applying predefined rates or contractual terms.
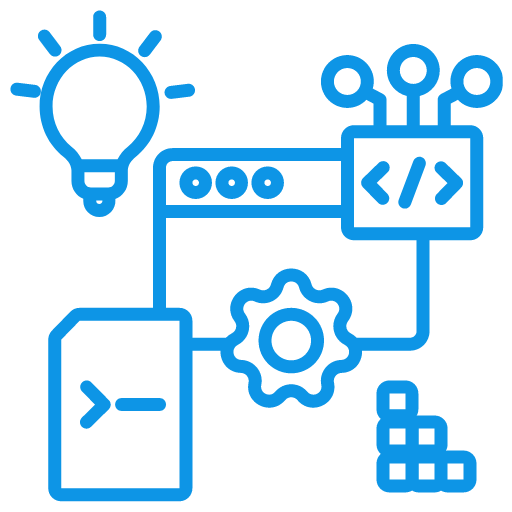
End-to-end Integration
With the help of our integration technology, you can track and trace assets in real-time, gain comprehensive unification among responsible parties, boost productivity, and save time and money. This smoothly integrates with MES, ERP, WMS, and more to ensure all aspects are covered.
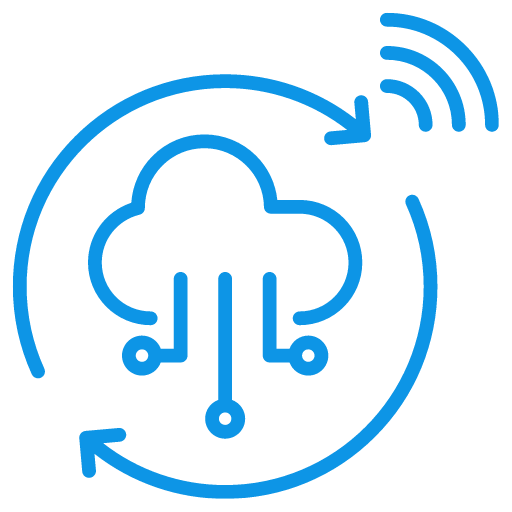
IoT and AI Backed-Up Request Configuration
This encourages a flawless process from request reception to task assignment through robust IoT and AI technologies. Upon receiving a service request, the software employs predefined configurations, swiftly categorising and prioritising the request based on parameters and assigning the tasks to the available employees.
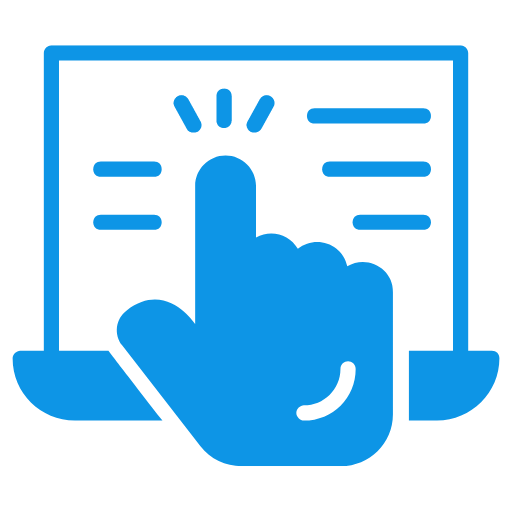
Service Availability Model
Cerexio solution gathers Industry 4.0 digital capabilities such as AI, IoT, Middleware, Event-Driven Architecture to present a robust service availability model, which outlines the system’s readiness to fulfil the service request adhering to the metrics like uptime and response time.
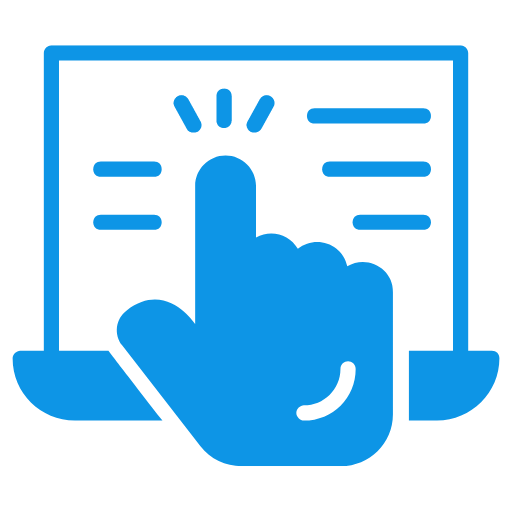
Automated Service Requests
This platform empowers the responsible authorities in the manufacturing company to create queries and requests for the relevant service and send them directly to the service providers through one consolidated canopy, which includes dashboards and task managers to generate alerts.
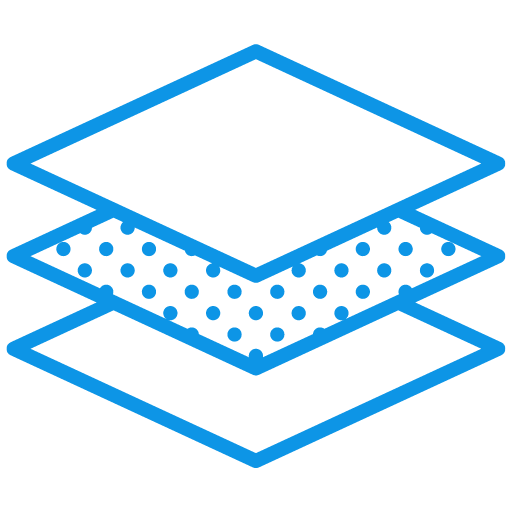
GIS Mapping Embedded Calendar
GIS mapping capacity levels up the visual representation of task locations and progress as this integration helps trace the completion status and latest updates on task requests from service providers. This status-tagging calendar system ensures real-time visibility into the operations.
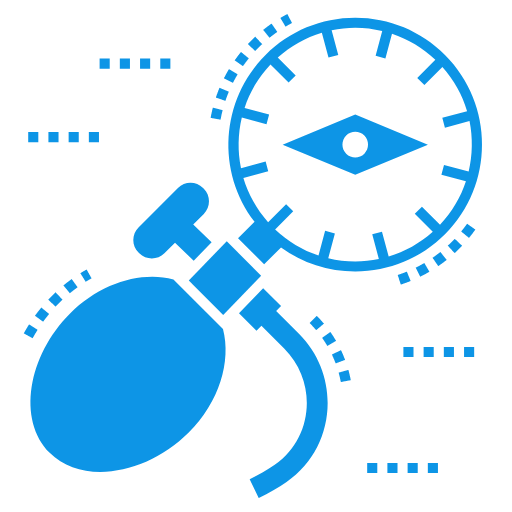
Real-Time Monitoring and Foreseeing Machinery Errors
The combination of AI tools, smart sensors, CCTV, and laser technology forms a powerful synergy in this solution, particularly in the early detection of machine errors. Utilising pattern recognition and anomaly detection helps to spot and foresee potential threats at the initial points.
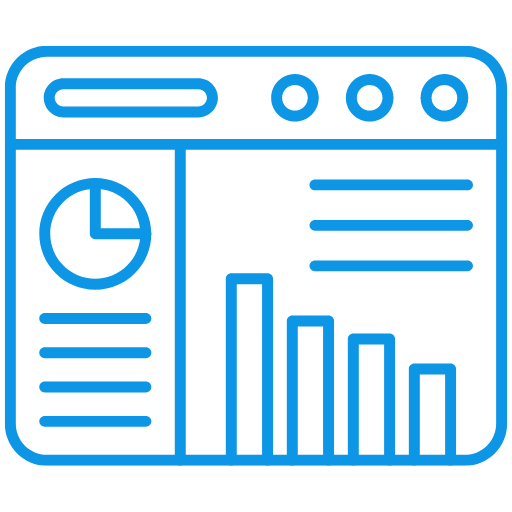
Consolidation through Visual Dashboards
The Cerexio software is powered by visual representation tools such as Gantt charts, calendar views, map views, and time tracking. It optimises the overall tracking system by providing intuitive, real-time insights. These analytical and innovative tools collectively establish a comprehensive understanding of the service request management manufacturing framework.
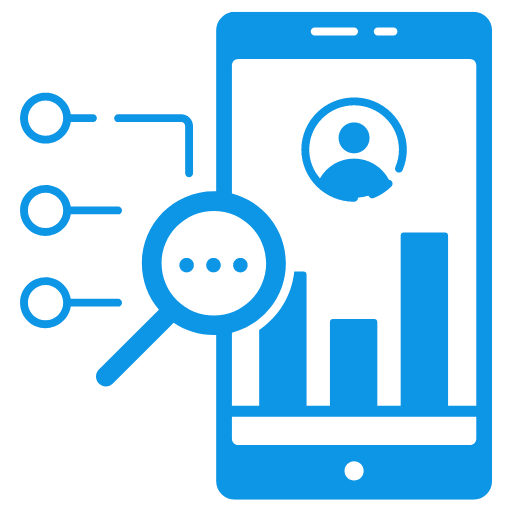
Inter-Connected Inventory Tracking System
Cerexio solution integrates with inventory systems to monitor stock levels, automatically updating them in real-time. When a service request triggers a need for certain materials, the system ensures the stock is available. When the goods are not available, they automatically follow the order management protocols.
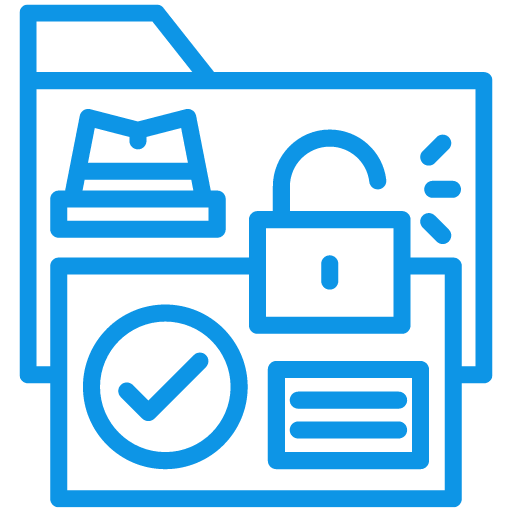
Remote Accessibility
Cerexio solution is a robust mobile app that extends remote visibility by enabling users to access service requests and queries from anywhere. Through the app, stakeholders can track task conditions in real-time, ensuring a comprehensive view of ongoing processes.
Our Experts Ready to Help You
How Does the Cerexio Service Request Management System Benefit You?
Real-time asset management has been one of the biggest challenges manufacturing companies encounter in today’s business world. Keeping the machinery up-to-date and receiving the best outcome is essential when running a manufacturing plant smoothly.
Cerexio- the best Service Request Management Software, enters the limelight as the ideal resolution for this burden with its advanced functionalities and powerful integration capabilities. Leveraging the essence of Industry 4.0 digital technologies, our solution offers an outstanding strength for manufacturers to boost asset visibility, traceability, and standardisation, saving an abundance of money and time. Here’s how the Cerexio Service Request Management System revolutionises the manufacturing realm:
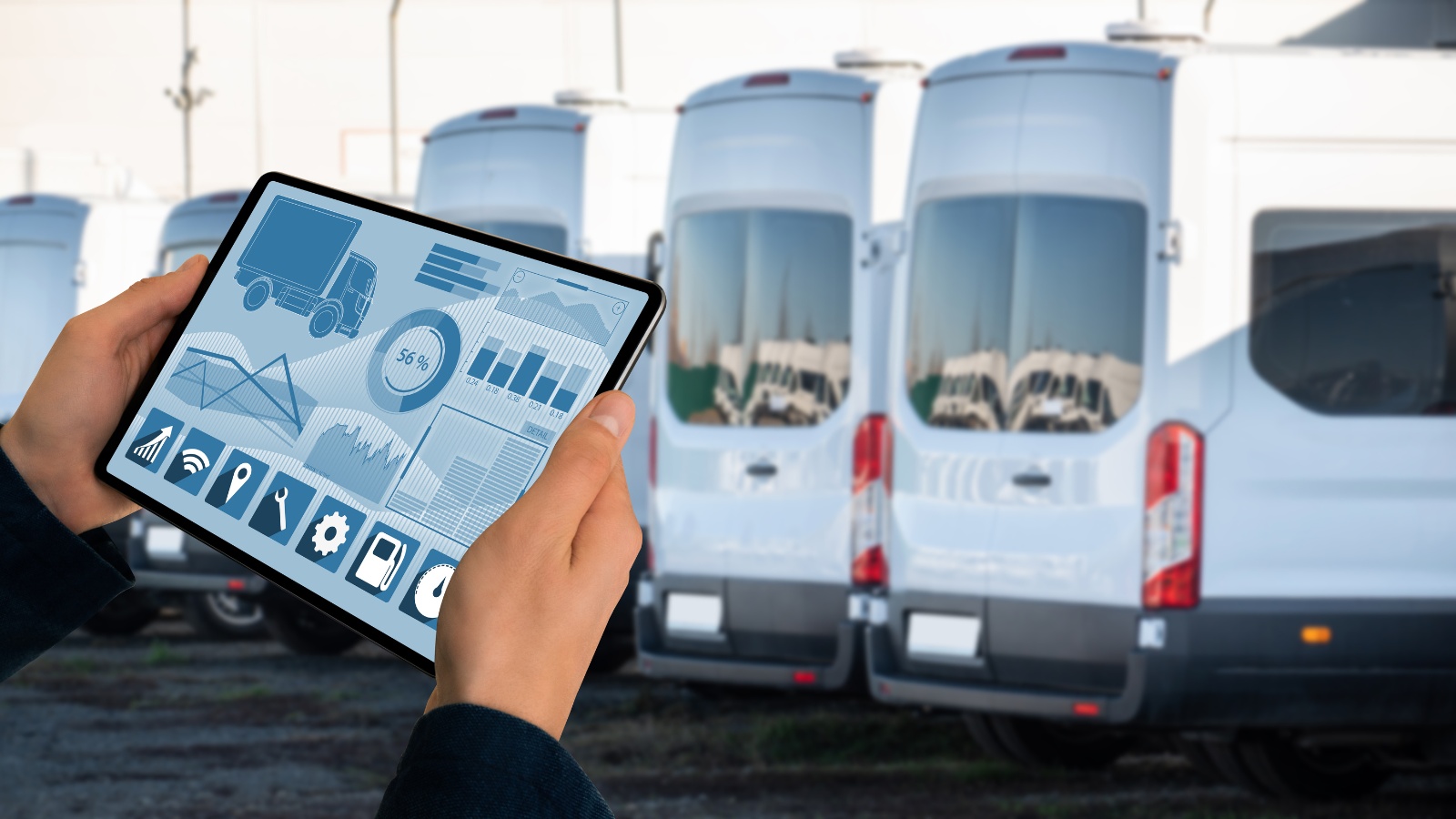


Cerexio solution offers unification through their consolidated platform for people, data, and systems to gather around and solve asset-related issues in real-time.


Through this platform, manufacturers are encouraged to create queries about the asset service request, and in return, they are informed about the specific time and date the operators arrive to fix the issue.


Since the system is dominated by inventory control and tracking software, service providers can ensure that they are well-equipped with the necessary tools and components that are needed for the repair.


Through GIS technology, task progress can be tracked as visual representations in real-time, which helps boost credibility and accountability from the service provider’s end.


Our system is powered by the integration of Industry 4.0 capabilities; it provides predictive insights, analytical forecasts, and details about possible threats through the use of sensors, CCTV, and laser technologies.
Benefits of Cerexio Service Request Management System
Fusion of Technological Capabilities
This solution is armed with powerful Industry 4.0 capabilities and embedded technologies such as GIS, Predictive Analytics, IoT, AI, etc., to collect the data under one digital canopy, boosting real-time visibility.
Real-Time Tracking and Implementing Workflow Automation
Our solution encourages workflow automation process management and backs up every responsibility that comes under asset management, ranging from creating requests and assigning tasks to request processing, etc., without making errors.
Omni-Channel Ticketing System
It has been challenging when the paths to connect with relevant parties are limited when solving asset repair and upgrade matters within a manufacturing plant. To provide the best solution for this, the Cerexio system encourages a 5G-powered connection.
Robust Request Configuration
This gives the service providers the capacity to identify the service requests on time, check for the employees by availability, skills, and previous records, assign tasks, manage tasks and close the request when the task is accomplished.
Feedback via User-Friendly Self-Service Portal
As the IoT and 5G technological mastery connect the two parties, it is convenient for everyone to stay on the same page through the web portal. Once the asset management task is wrapped up, the manufacturers can provide valuable feedback through this portal.
Improved Transparency in Asset Management
Cerexio Service Request Management System assists in improving transparency when it comes to asset management, as the web portal is open to all the relevant stakeholders from both sides, and everybody can investigate the progress of maintenance initiatives.
Guarantee Machine and Employee Safety
This solution not only enhances efficiency within the manufacturing realm but also acts as a safety pillar for the workforce. Once the service request is made via the portal, the employees who have access to the particular machine can see its critical condition through the mobile view.
Sustainability and Compliance
Machinery repairs and maintenance requirements are followed by unwanted energy consumption levels and excess heating issues, jeopardising the company’s sustainability initiatives. Real-time resolution through the Cerexio system makes the manufacturers walk away from these compliance challenges.
Foreseeing Threats to Assets
Cerexio Service Request Management System is a technological pinnacle developed with advanced algorithms and predictive capabilities that support your operators in spotting errors before they escalate into critical conditions.
Time and Money Saving
It costs millions of dollars to value every single minute the manufacturing plant holds its operations due to downtime and machine failures. With the swift service request processing system, time and money can be saved immensely.