Profit is what you expect above all when it comes to the manufacturing industry operations. This industry is overwhelmed with various aspects ranging from production, packaging, supply chain logistics, etc. Profitability can be boosted if the manufacturers are armed with the potential to look into such elements separately and accurately. A Manufacturing Execution System, or in short MES, has been introduced to the manufacturing sector to ensure that production processes are trackable and traceable.
In this article, we will explain what MES is and how it provides a helping hand to the challenges encountered by manufacturers when it comes to certain production elements.
Presenting ‘Manufacturing Execution System’
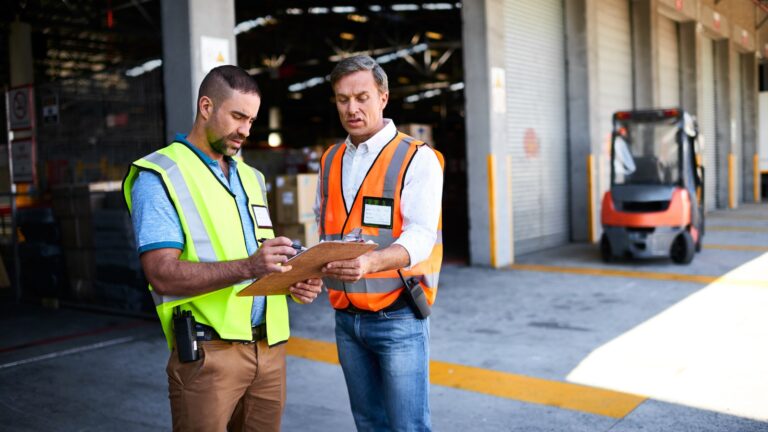
MES is a robust solution uniquely developed to gather and store production information within a manufacturing facility. MES is empowered by powerful integration with other software for ease of data collection. Specific training and skills are necessary for the Controllers and Managers to operate this software solution in their data-gathering process.
The best output is those manufacturing plants receive complete transparency, control, and manufacturing optimisation as a result of this robust networking. The authorities now have the ability to record and examine every stage of the production process, including order placement, product creation, and process control to output. It is easier to identify errors or dysfunctions that waste time or money and replace them on time. The efficiency and capacities of manufacturers, from small scale to large scale, are significantly increased by this seamless networking capacity.
Mainly Challenging Aspects in Production to Track and Monitor
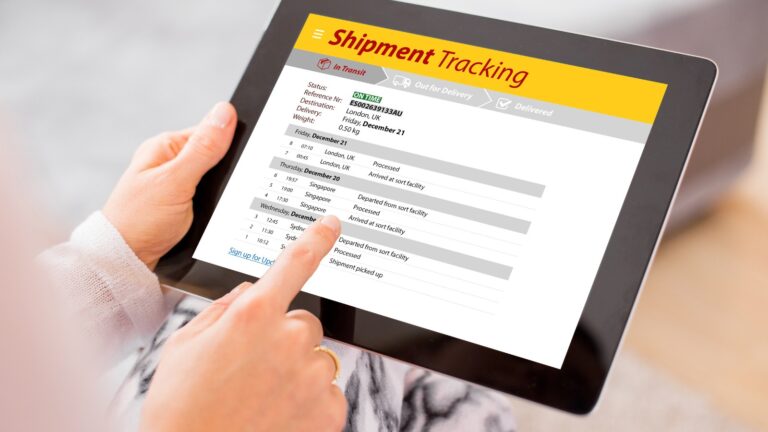
Work-in-Progress Inventory
Effective monitoring and management of Work-in-Progress (WIP) inventory is at the top of the list when it comes to the significant complexity of large-scale manufacturing operations. How does this occur? It becomes more difficult to properly trace the location, status, and amount of individual components or sub-assemblies as products move through several production steps.
Do you know how crucial it is to make sure the right components are used at the right time and place in the manufacturing arena? It can immediately affect production efficiency and product quality as a result. While manufacturers utilise technologies like RFID and barcode systems to track WIP inventory, achieving real-time visibility becomes a problem for sure. There is a high demand for a solution that can fill the gaps through continuing innovation and improvement in inventory management techniques.
Quality Control and Defect Tracking
Maintaining product quality is a top priority in the manufacturing industry. However, it is especially challenging to manage quality control data and flaws efficiently when dealing with complicated merchandise or labour-intensive production processes. That is where a robust tracking system becomes essential to identify the sources of faults, whether they result from faulty machinery, defective raw materials, or human mistakes.
It is necessary to make sure that quality-related data is accurately and consistently documented. This includes test results and inspection records, and it carefully links these data to specific products or batches. Manufacturers can quickly detect, diagnose, and fix quality concerns through strategic approaches, protecting the integrity and reputation of their products in a highly competitive market.
Assets Utilised in Production
It is common knowledge that manufacturing relies heavily on various machines, tools, and equipment. Tracking the condition, maintenance history, and performance of these assets is critical for minimising downtime and optimising the production efficiency of the business.
Maintenance tracking systems, such as Computerised Maintenance Management Systems (CMMS), are used to monitor equipment health and schedule maintenance. However, ensuring that all relevant data is consistently recorded and taking actions according to them can be quite challenging. That is because some of the manufacturing facilities function with a large number of machines and maintenance tasks.
How MES Assists Production Process with Tracking and Tracing
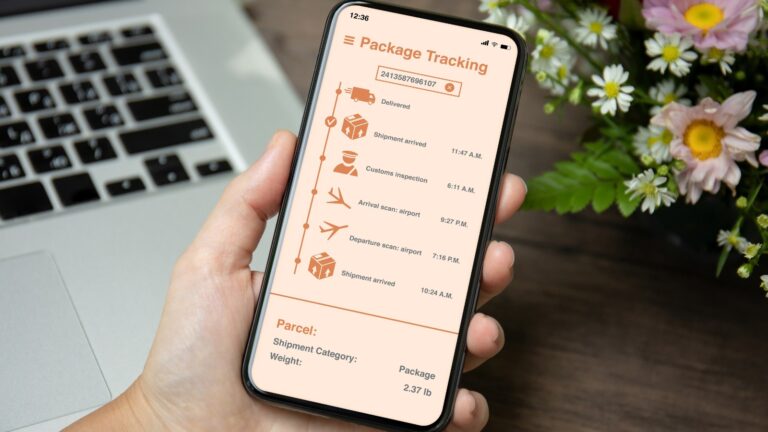
Data Tracking
MES plays a pivotal role in enhancing the production process through comprehensive data tracking. This effectively gathers real-time data from multiple manufacturing stages, providing a pretty smooth information flow. This information comprises factors for quality control, operator activities, and machine performance. Plus, it enables manufacturing businesses to make educated decisions quickly by offering a single platform for data monitoring and analysis.
If further explained, It makes it easier to spot problems, allocate resources more efficiently, and ensure that production schedules are followed on time. MES facilitates traceability by connecting every data point to particular goods or large batches while ensuring accuracy in tracking and responsibility.
Inventory Tracking for Optimal Usage
The latter is crucial for streamlining manufacturing procedures through efficient inventory management. If MES is concerned, it ensures that workers employ enough materials and components by continually tracking inventory levels and utilisation. You can witness that it makes real-time inventory management easier, eliminating shortages or overstocking as a result. If not properly handled, this issue might cause production delays and higher costs. Also, MES improves resource availability visibility, allowing for improved resource allocation and planning.
Is that all? No, It helps manufacturers reduce waste, lower carrying costs, and boost overall operational effectiveness. As a result, they can make wise judgments and optimise processes for better production. Another thing is they can consistently maintain product quality if correct inventory data is easily accessible.
Wastage Tracking
If MES is implemented, it allows for accurate tracking and waste analysis by constantly monitoring and documenting material consumption at every stage of production. Manufacturers can implement proactive steps to eliminate inefficiencies, minimise scrap, and save costs if they can recognise the origins and patterns of material wastage. This also makes it possible to see manufacturing processes in real-time, which gives them a hand in taking quick action when there is excessive wastage.
If put in other words, Manufacturers can optimise resource use, and boost manufacturing processes as a result of this implementation. Also, they can promote sustainable practices completely relying on this data-driven strategy.
Energy Efficiency Tracking
Saving energy receives significant attention when it comes to the business world. The best thing about MES is it repeatedly tracks energy use throughout all production activities, delivering data and insights in real-time. Now, with this system in their hands, Manufacturers can detect regions of high energy use, spot inefficiencies, and put energy-saving measures in place by studying this vast data. Then again, the latter makes it easier to do predictive maintenance as it will lead to ensuring that machinery runs as efficiently as possible and minimising energy loss.
With easy access to comprehensive energy usage indicators, manufacturing facilities are now able to make well-informed decisions to streamline operations. That is not all; it can save energy costs and lessen their environmental impact as well. It is quite visible that MES gives manufacturing businesses the opportunity to prioritise sustainability giving it the utmost importance. Plus, it helps lower operating costs and improve overall energy efficiency across their whole production pipeline.
Cerexio MES Solution
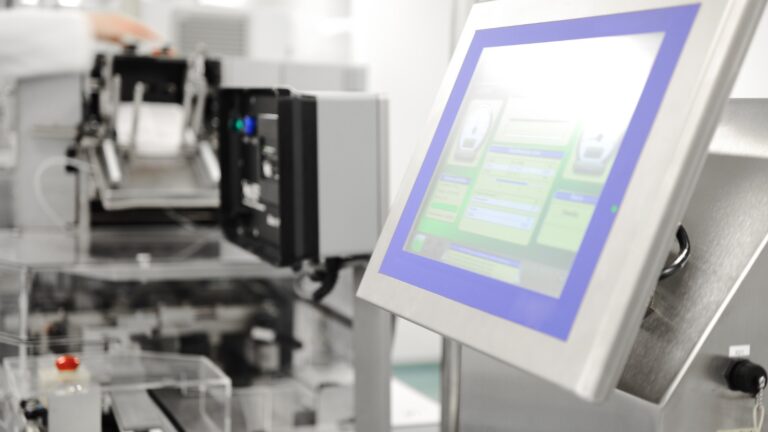
Cerexio-empowered MES solution enters the business world to revolutionise with its sophisticated features and functions ranging from Improving production quality and maximising labour utilisation to adherence to sustainability principles. Cerexio MES has become a strong pillar when it comes to manufacturing operations and its execution of various aspects through the strong integration with Digital Twin and Automated Process Scheduling tools. If you are looking into innovative and powerful ways to get the best out of your efforts, Cerexio MES is the best solution as it is empowered by Industry 4.0 capabilities.
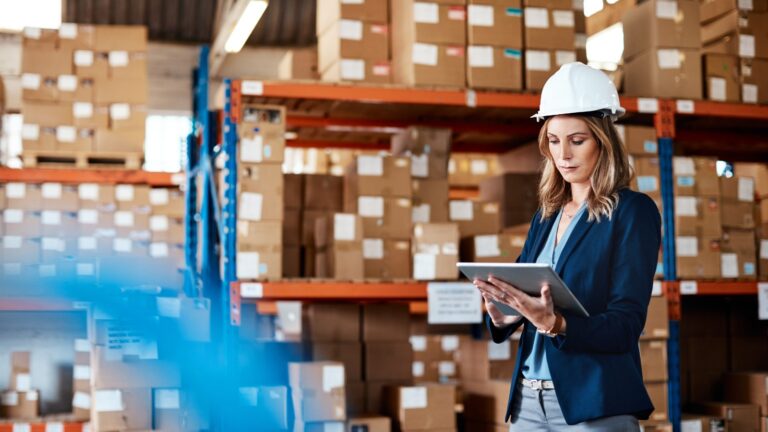
Expand Your Visions into Business Aspects with New Technology
Technology allows businesses to expand their capacities to another level by implementing them into their business operations. However, when you purchase a new software solution, it is always better to compare the features of your desired solution with the others in the market. This is a Cerexio reminder for you.