This article will help the reader note the 7 main types of industrial robots used by modern industrial establishments and a few technologies they can use as software counterparts to make more profit with fewer investments in industrial robots.
7 Types of Industrial Robots Your Industrial Vicinities Cannot Afford to Overlook
Articulated Robots
These robots are used mainly by manufacturers because they provide more freedom than other industrial robots. Their human arm-like motions make them a perfect robotic solution for flexible production line operations. They are applied in various activities due to their enhanced motion capabilities, adaptability and flexibility to required environments. They are used for material handling, part transferring, packaging, arc welding, palletising, machine loading and many other activities. Articulated Robots are one of the oldest types of industrial robots that are not replaced with innovative robotic inventions of the new age.
Many Articulated Robots require complicated programming and kinematics and a professional robot controller. Also, in terms of speed, Articulated Robots are slower compared to most Industrial Robots. But in terms of space consumption, Articulated Robots require minimal floor space, and they are easy to be aligned along multiple planes.
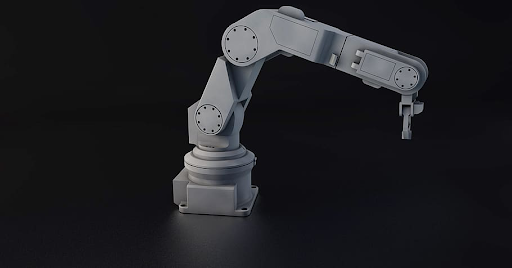
Cartesian Robots
Cartesian Robots are industrially applied for many purposes. They are mainly used for ‘Process to Process’ transfers, ‘Pick and Place’, assembling, sealants and adhesive applications, depalletising, palletising, precision spot welding, CNC (Computer Numerical Control) machine tooling and more. They are used for many general industrial production activities, including dispensing, stacking, material handling, storing, retrieving, sorting, cutting, scribing, sealing and many more actions.
Cartesian Robots are qualified in meeting the requirements of many industrial applications for their higher payload carrying potential, cost-efficiency and ease of programming. Many robot-driven industrial practitioners add compatible modules to the already existing mechanism to programme the motions of Cartesian Robots, which makes it easy to deploy and efficient. More advantages of this robot category are that it showcases higher skill in precision and accuracy, plus they consume smaller factory space to operate compared to other robotic counterparts.
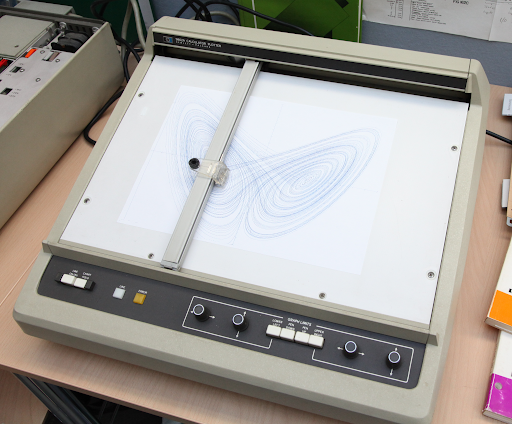
Collaborative Robots
They are primarily used to handle small parts, complete simple tasks, inspect products and other functions that require the intuitions and support of a human mind and body. Cobots are mainly used to complete actions like dispensing, assembling, tending, finishing, welding, removing, inspecting and more.
There are many types of collaborative robots; four of the major types of collaborative robots are ‘Hand Guiding’, ‘Speed and Separation’, ‘Safety Monitored Stop’ and ‘Power and Force Limiting’. They are categorised based on their functionalities and the unique technology blends they harness. The general feature of all these robots is that to operate efficiently they require a degree of safe and secured human interaction.
There are also a few cons to utilising Cobots in your factories. These robots require a restricted and large working area to ensure a comfortable and secure working environment for their human counterparts. Also, since these robots rely on humans compared to other robots, they are not very useful without human supervision or assistance. Furthermore, Cobots are usually slower during operations, especially when the working area is advanced to ensure the operator’s safety.
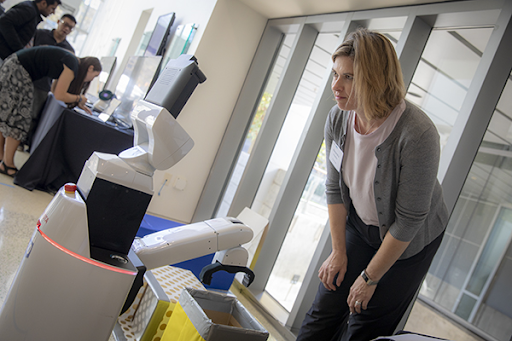
Cylindrical Robots
Cylindrical Robots usually have three axes of motion (one circular motion enabled by gears and a motor, and the remaining two are linearly enabled by a pneumatic cylinder). These robots are confined to a cylindrical work envelope because its axis creates a cylindrical coordinate system. Cylindrical robots are mainly applied in industrial vicinity in handling machine tools and die-casting machines, spot welding and during other assembly operations. Some Cylindrical Robots are advanced with a robotic ‘wrist’ at the rotary arm to add more degrees of freedom to gain more precision and advantages during utilisation.
Some of the more useful functions that the Cylindrical Robot can complete in your factory is palletising, investment casting, applying coats, packaging, injection moulding and many other noteworthy operations that require wide ranges and complex motions to complete. It has the potential to carry payloads varying from 5KG to 250KG and inherits an average working speed of 1000 mm per second.
Some of the limitations of the Cylindrical Robots highlighted by industrial practitioners are the motions, precision and repeatability of these robots are limited to the direction of their rotary action; this also affects the mechanical rigidity of the machine. The lack of sophisticated control of the direction and motion of the decimal coordination system is another limitation discussed by most industrial practitioners. (Image Source)
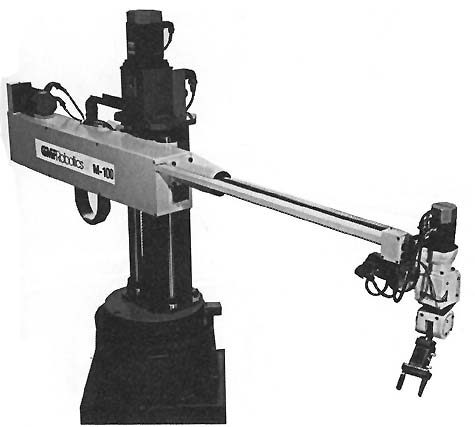
Delta Robots
Delta Robots are mainly used in the medical field, packaging and pharmaceutical industry, food and beverage industry due to their fast functionality, exquisite precision and acceleration when performing operations. For example, they can pick batches of products and place them in a container of the assembly line in seconds. These robots are also very light in weight which helps them move faster than other types of robots. The four main advantages of Delta Robots is their smaller footprint, assured safety, high productivity, and higher speed.
One limitation identified by Delta Robot maneuverers is that if the signal fluctuates or changes are less than the step size, these robots will be disconnected and stop operating. Therefore, its power systems and control systems must be steadfast at all times.
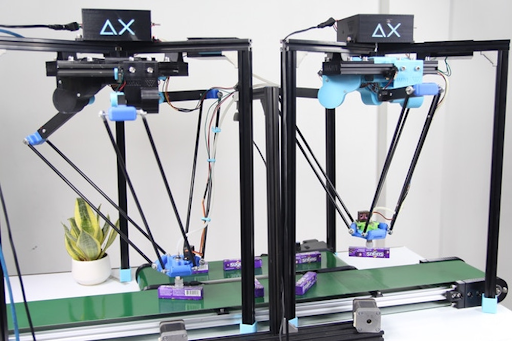
Polar Robots
Polar Robots are also called Spherical Robots, and they have two rotary joints and one combined joint. It is called spherical robots because the work envelope of these robots takes the form of a sphere. This is one of the oldest types of robots and was first created in 1950, but fascinatingly it is still used in the modern industrial context. Even with an old history, this robot has supplanted modern robots and innovations due to its amazing ability to boost productivity.
Polar Robots are used for assembly operations, machine tool tending, diecast processes, arc and gas welding, painting systems, spot welding, forging, glass handling and more. These robots are famous amongst robot-driven factories because they can flexibly reach areas and comparatively require less floor space. One of the main advantages of Polar Robots is their range of motion (360 degrees) and the capability of managing large work volumes.
The limitations of the Polar Robots are that they can’t reach above themselves, their structure allows them to vertically reach to shorter lengths, and they repeat unnecessary rotary movements. Robot specialists believe that with a sophisticated control system and better design, these robots can be even more useful in the industrial context. (Image Source)
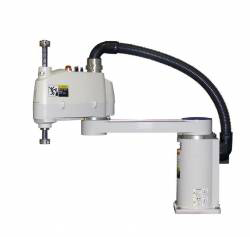
SCARA Robots
They are mainly used in the production lines due to many characteristics that make them a perfect choice for in-house operations. One advantage is that it has amazing precision during operations; due to its rigid axis, it is known for accuracy during operational performances. Another advantage is its amazing speed when cycle times are critical, and SCARA machines are the best robots to rely on. Another significant feature of SCARA robots is that they require smaller footprints compared to other robots like Delta or Cartesian Robots, which makes them handy and efficient during operations. They are the aptest choice of robots during repeatable actions.
Some of the common disadvantages of SCARA robots are the limited flexibility and dexterity compared to other types of industrial robots. Also, they can only carry light payloads which wavers between a weight span from 2KG to 10KG.
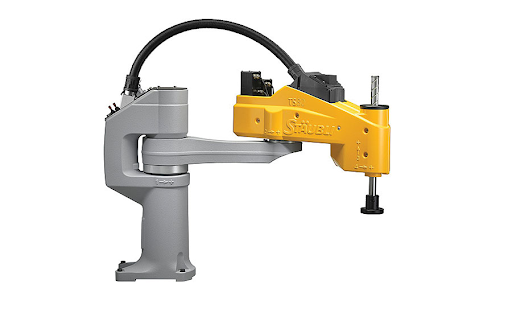