What is the one fact you give the most importance to in your manufacturing framework? That is the production quality, for sure! If you cannot deliver goods up to the client’s quality expectations, then there will be no further proceeding with orders. It surely impacts your ROI in the end. Most manufacturers opt for the latest technological solutions to guarantee their production line meets the standards. ‘Predictive Quality Analytics’ has been specifically developed to fulfil this requirement easily in the entire manufacturing domain.
In this article, we focus on the utilisation of Predictive Quality Analytics in the manufacturing realm and what it can offer you in return.
Understanding Predictive Quality Analytics
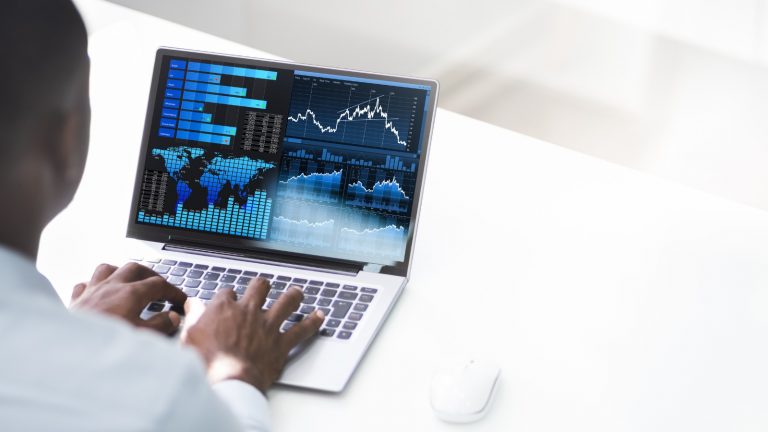
Understanding the concept that lies behind this is not that complicated. It indicates the utilisation of advanced data analysis techniques, such as machine learning and statistical modelling, to forecast and prevent quality issues before they expand into bigger problems.
How can this technology get this done in the first place? Since it comes with the capacity to analyse historical data, production variables, and environmental factors, manufacturers can easily match all of them to predict potential defects, equipment failures, and process deviations. This act will help them take the necessary precautions.
This is kind of an encouragement for the manufacturers to reduce scrap, rework, and warranty costs. It also improves operational efficiency and enhances customer satisfaction by up to 200%. On the other hand, manufacturers cannot do without such a tool to remain competitive in today’s market due to various serious quality challenges. Today’s market is full of high-quality products and efficient processes that target customer satisfaction heavily.
What is the ultimate destiny of the manufacturing company if it places a low weight on quality standards? This will progressively boost the chances of defects in products, equipment failures, process variations, supply chain disruptions, etc. Predictive quality analytics in manufacturing addresses these problems innovatively while giving hints in advance.
Therefore, we can say adopting predictive quality analytics for manufacturing operational frameworks is like having a tech-driven telescope!
Top 5 Ways Predictive Quality Analytics in Manufacturing Occurs
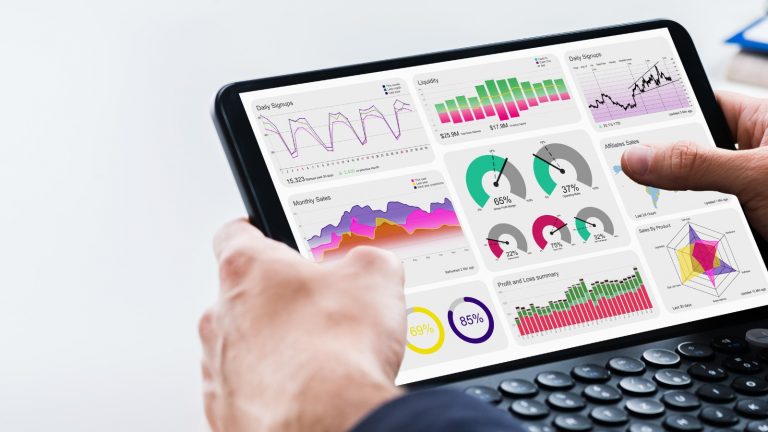
Continuous Improvement Initiatives
Identifying the areas of issue is important. Yet, trying out new improvements is more important! This is exactly where Predictive Quality Analytics creates the path for manufacturers. Continuous improvement initiatives in manufacturing are a cyclical process of data analysis, action, and evaluation.
As the basic process, historical data, real-time production metrics, and quality parameters are collected and integrated under one platform. Then, the systems that are powered with this strength develop some predictive models to identify potential quality issues and optimisation opportunities.
Targeted improvement methods are put into action based on these findings. For instance, fine-tuning supplier quality management procedures, improving equipment maintenance schedules, and modifying process parameters.
But these models do not end there. Real-time monitoring systems embedded under Predictive Quality Analytics track the effectiveness of these interventions, providing feedback for further refinement. Continuous evaluation of the predictive models ensures their accuracy and relevance over time. This is an ongoing process when it comes to improvements via the latter technology.
Demand Forecasting
This digital strength is powered by demand forecasting capabilities as well, which is highly productive in the manufacturing domain. You already know where the Predictive Quality Analytics begins! It collects and integrates data from various sources, including historical sales records, market trends, customer behaviour, and production capacity. Since these Predictive models are backed up by machine learning algorithms, which are specifically developed to analyse this data, they will forecast future demand for products and components accurately.
How does this process occur within the predictive model? They are designed to consider factors such as seasonality, promotional activities, economic indicators, and changes in consumer preferences to generate reliable predictions. This is not as complex as the real-time monitoring systems, which continuously update the models with new data. Manufacturing systems like MES, ERP, and IoT make sure that predictive quality Analytics modules receive the newest data.
As it can predict future demands precisely, manufacturers have the ability to adapt their production schedules, resource allocation, and inventory levels dynamically. The ultimate result is quite impressive! They can pre-plan their supply chain, minimise stockouts and excess inventory, improve customer service levels, and enhance overall operational efficiency within no time.
Root Cause Analysis
If you encounter an issue, you need to find the actual reasons for it. This is what is meant by root-cause analysis in manufacturing. This is crucial for identifying and addressing the underlying reasons for quality defects, equipment failures, and process deviations. It not only helps manufacturers prevent recurring issues but also aids in minimising downtime, reducing waste, and enhancing overall operational efficiency.
Then how does Predictive Quality Analytics carry out root cause analysis? The system analyses vast amounts of historical data, production variables, and environmental factors to identify patterns, correlations, and anomalies in the first place. Then, the ML algorithms and advanced techniques work together to find the reason that is hidden in the roots of the problem.
The good thing about this capability is that manufacturers can predict and prioritise potential root causes before they occur using Predictive Quality Analytics. If you face issues during the manufacturing process, it means that your production quality can be compromised!
Supplier Quality Management
How can you ensure the quality of the outcome when you use elements that are of lower quality? This is what you should be careful about. However, when Predictive Quality Analytics is in place, you do not need to worry about this concern, as it looks into the necessary quality standards in real time.
Maintaining higher quality standards for your suppliers should be a top priority in production. If you can carry out strict regulations and standards for suppliers, you can minimise the risk of defects, production delays, and recalls while optimising operational efficiency, all while keeping up with cost-saving strategies. The latter proceeds with historical data, performance metrics, defect rates, and delivery times related to suppliers to assess their reliability and identify potential risks.
ML and advanced analytics do the prediction part for supplier performance and prioritise high-quality suppliers. If the models spot one tiny fact that compromises the material quality, it will trigger alerts to the relevant authorities.
Fault Detection and Diagnostics
This involves analysing real-time data streams from sensors and production systems to identify anomalies and deviations from the normal operational framework you have.
The digital capabilities that are hidden inside the Predictive Quality Analytics form a grid for baseline performance metrics and expected patterns. The abnormalities cannot be unseen when you have such a system in place. It will send you real-time notifications to indicate that there is a problem in your processes or assets.
With the aim of enhancing precision and dependability, predictive models undergo constant modifications and enhancements centred on fresh data.
This is the ideal technology to spot faults in your production line. Manufacturers can lower downtime, reduce waste and rework, and optimise equipment maintenance schedules if they are powered to identify faults in advance.
Cerexio Solutions for Predictive Quality Analytics
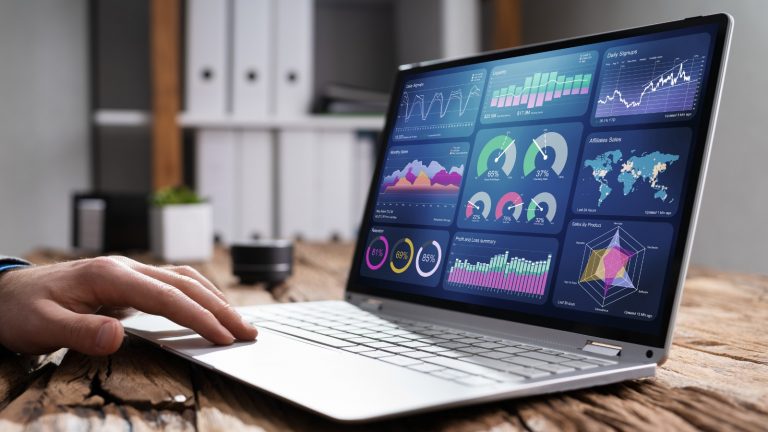
Cerexio-empowered Predictive and Prescriptive Analytics are the best solutions manufacturers can opt for in their quest for the ideal answer to quality breach challenges. It easily automates the quality checking framework, as our solution is dominated by Industry 4.0 capabilities.
Levelling Up Manufacturing Quality with Predictive Analytics
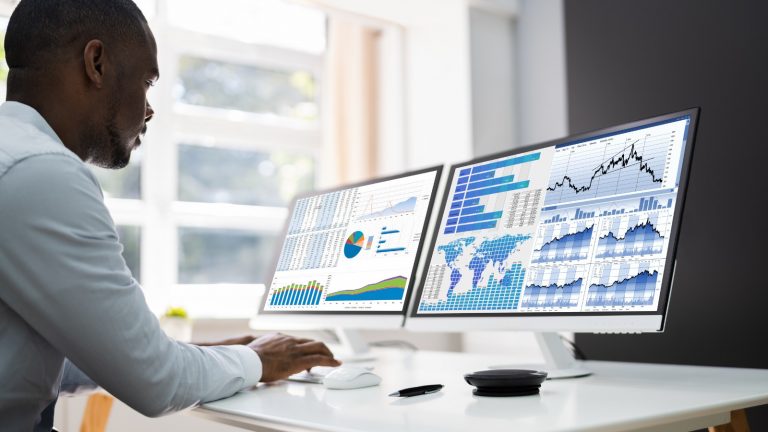
You never want to compromise the quality of your manufacturing outcome, and this is why we are suggesting that you should hold hands with an industry expert to save you from this situation. One tool for all the quality-checking tasks!