Over 2.1 million manufacturing jobs could sit empty in the U.S. by 2030, and that is just one country! It is noticeable that the manufacturing talent shortage stretches across continents, crippling productivity, innovation, and economic growth. As factories modernise faster than the workforce can adapt, the gap between open jobs and qualified workers keeps growing. No, this is not just a local HR problem, but it is a global emergency. Do you think bold, fresh strategies can really reverse this trend?
This article breaks down five powerful global approaches that could reshape how industries find, train, and keep the right talent for the future.
We will discover
- Why Is There a Global Manufacturing Talent Shortage?
- The Impact of the Talent Shortage on Manufacturing Output
- Can These 5 Bold Strategies Fix the Manufacturing Talent Shortage?
- What is Next for Manufacturers? Planning for the Future
- Cerexio Solutions for Manufacturing Talent Shortage
- Creating a Futuristic Talent Pool Using New Tools
- FAQ about Manufacturing Talent Shortage
Why Is There a Global Manufacturing Talent Shortage?
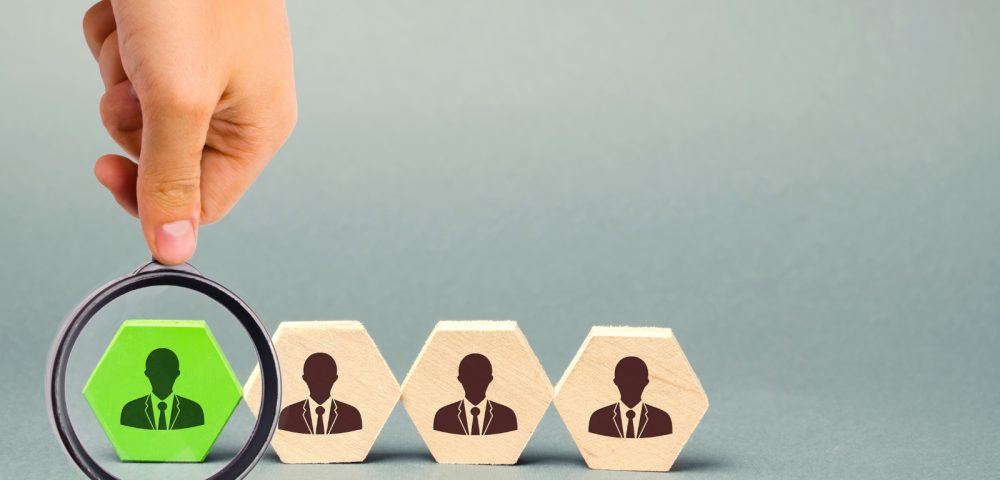
The global manufacturing talent shortage keeps growing as several real issues all come together at once.
First, a large number of experienced workers from the Baby Boomer generation continue to retire, leaving a wide skills gap behind. At the same time, many young people avoid manufacturing jobs because they think these jobs are dirty, low-paying, or stuck in the past, even though modern factories rely on high-tech tools and innovation.
On top of that, schools and industries do not always offer enough training or hands-on programmes that help people get ready for today’s complex manufacturing roles. Even if someone wants to join, they may not find the right path to learn new skills or switch careers.
As companies expand into global markets, they also need workers who understand automation, digital tools, and global supply chains, skills that were not as necessary before. So, between retirements, old stereotypes, and fast-changing demands, the talent pool keeps shrinking fast.
The Impact of the Talent Shortage on Manufacturing Output

- Manufacturers struggle to keep up with demand because fewer skilled workers slow down production and cause constant delays in fulfilling orders.
- Management finds it hard to push new ideas forward when they do not have enough trained people, which blocks progress and makes digital upgrades feel nearly impossible.
- Companies have to pay more to hire or keep skilled workers, which affects profits and sometimes forces them to move work to other countries.
- Supervisors ask employees to take on too many tasks, which leads to burnout and more mistakes on the job.
- Quality starts to drop because teams rush to meet deadlines without the right people or tools in place.
- Customers get frustrated when delays pile up, and some even switch to other brands that deliver faster.
- Managers skip long-term planning and focus only on short fixes, which puts the whole business at risk over time.
Can These 5 Bold Strategies Fix the Manufacturing Talent Shortage?
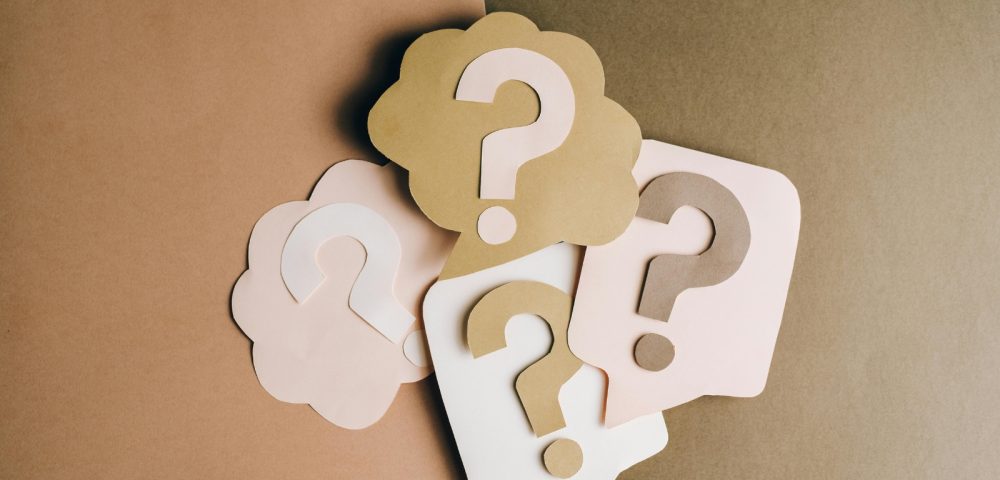
Rebranding Manufacturing for the Next Generation
First of all, manufacturers need to change how young people see the industry if they want to fill future jobs. Right now, many students think factory jobs are boring, dirty, or low-tech, as we mentioned, but that is far from the truth.
Also, companies should show how modern manufacturing uses clean tech, smart machines, and green practices. On the other hand, schools need to push more STEM and hands-on programmes that show students real career paths in this space.
When teens see cool robots, advanced tools, and purpose-driven work, they will start seeing manufacturing as exciting, not outdated.
Investing in Reskilling and Upskilling Programmes
If they need to fix the talent gap, companies and governments must team up to help workers learn fresh skills without starting from zero.
Many people already work in jobs that are disappearing or shifting fast, so they need faster, easier ways to move into manufacturing. This is when online training, short certifications, and real apprenticeships make a huge difference.
One great example is Germany’s dual training system, where students split their time between school and real work. This approach builds confidence and skill at the same time.
Global Talent Mobility and Immigration Reform
Countries facing worker shortages should open more paths for skilled talent from around the world. Right now, immigration rules tend to block capable people who want to help industries grow.
Manufacturers can fill urgent roles faster if governments adjust policies and make work permits easier to access for needed jobs. Programmes like Canada’s Global Talent Stream already show how fast-track visas can help tech-heavy sectors find talent without waiting years.
When governments and companies work together to invite people who actually want to contribute, they bring in fresh energy and ideas that fuel growth.
Embracing Automation and AI to Offset Shortages
Even with better hiring, manufacturers cannot rely only on people anymore, and that is the bitter truth. They also need smart machines.
Tools like robots, AI software, and Manufacturing Execution Systems (MES) can take on hard, dangerous, or repetitive jobs that scare workers away. These tools do not replace people, but they support them. As technology steps in, workers shift into higher-skill roles that focus more on managing systems and solving problems.
This change also creates fresh job types that did not even exist ten years ago.
Building Inclusive and Flexible Work Cultures
If you look closely, you may see that manufacturers miss out on great talent because they do not create spaces where everyone feels welcome. Many women, minorities, and young parents skip these jobs because they expect rigid schedules, harsh environments, or no support for family needs.
It is high time that companies change if they want to grow their teams. They should offer flexible shifts, mental health support, and clear career paths for everyone, no matter their background.
When teams bring in different ideas, experiences, and ways of thinking, they solve problems faster and grow stronger.
What is Next for Manufacturers? Planning for the Future
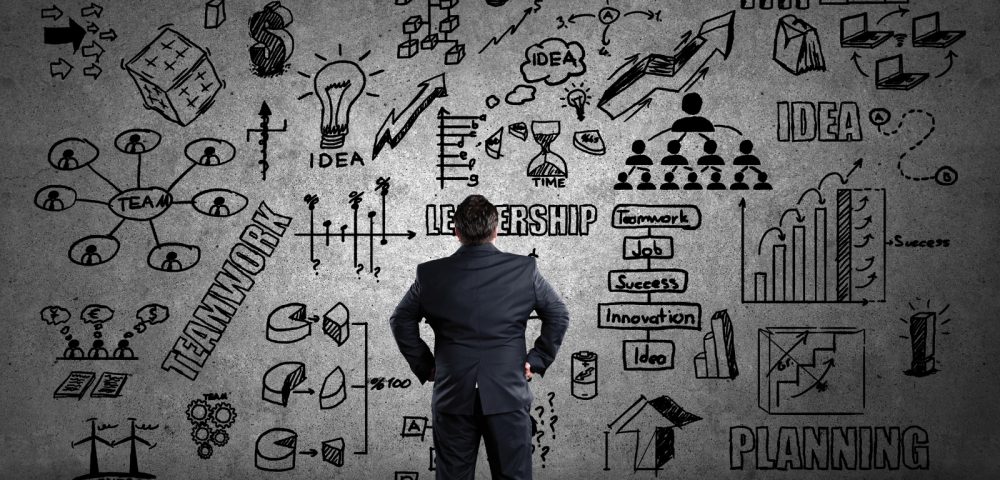
This is an era where manufacturers need to stop thinking short-term and start building real plans for the future of their workforce. They should work closely with schools, governments, and tech partners to create programmes that train people for today’s jobs and tomorrow’s challenges.
Education must include both hands-on skills and digital tools, while companies should keep improving how they attract and support workers.
Smart policies can also help connect talent with the right jobs faster. When everyone works together, it gets easier to fill gaps, stay competitive, and prepare for what is coming next.
Without this kind of forward thinking, they risk falling behind fast.
Cerexio Solutions for Manufacturing Talent Shortage
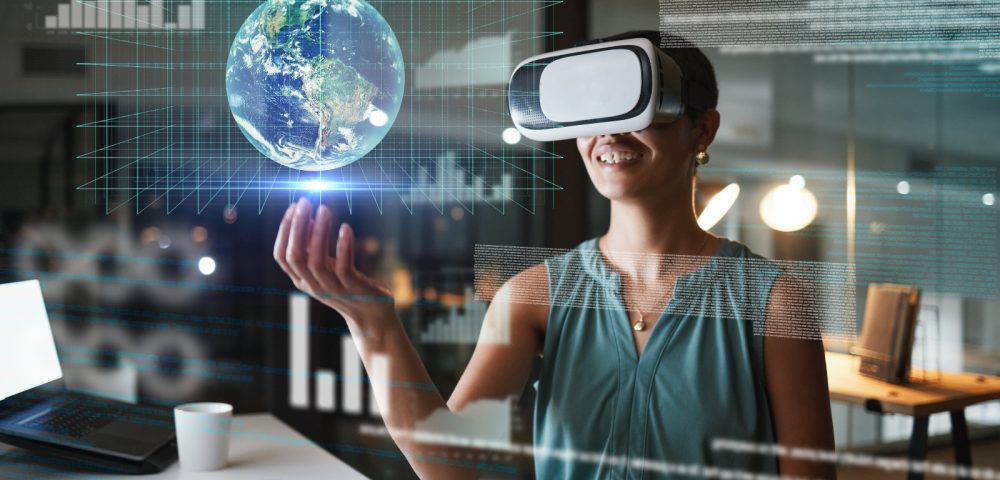
Cerexio brings AR and VR into the factory floor, helping manufacturing companies train employees with real-time, visual instructions and simulations. With our robust solutions, your workers will learn faster while avoiding risks, making training more effective. This innovation helps industries manage talent shortages while boosting productivity and making manufacturing more modern and exciting.
Creating a Futuristic Talent Pool Using New Tools
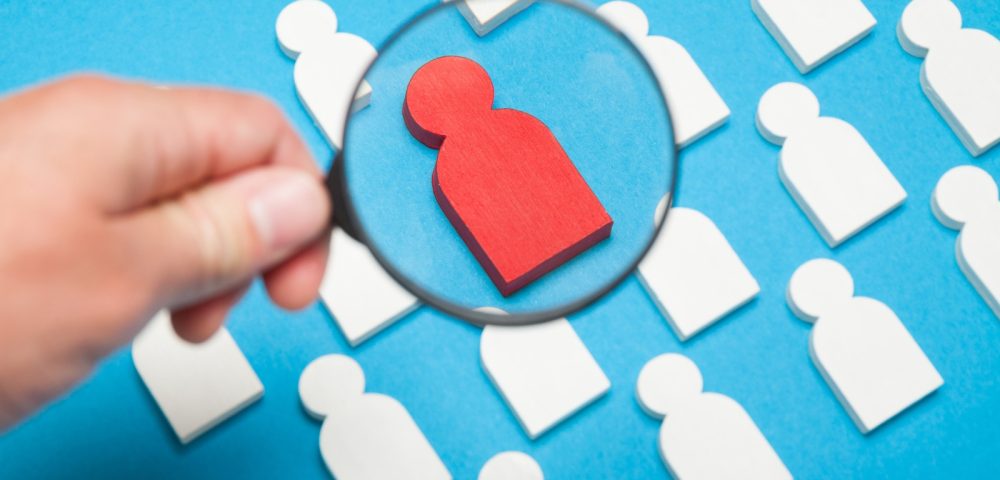
It is not fair if you expect to fill tomorrow’s roles with today’s toolbox. The smartest brands already use data, VR, and intelligent platforms to shape their future talent. Are you ready to outpace the talent drought and build something remarkable?
FAQ about Manufacturing Talent Shortage
Governments and industries can increase labour supply by investing in education, reskilling programmes, and immigration reforms. Encouraging workforce participation through flexible jobs, better wages, and training access helps bring more people into the labour market effectively.
It is possible to solve skill shortages by expanding vocational training, offering apprenticeships, and partnering with education providers. Promote continuous learning, use digital tools for faster upskilling, and retrain existing workers to meet evolving industry demands with modern, job-ready skills.
Manufacturing companies can attract more talent by modernising their image, offering career growth, and using advanced technologies like AR and automation. Providing flexible schedules, fair pay, and inclusive work environments also helps make manufacturing careers more appealing.