Is 3D printing Europe’s most underestimated green technology? As an industrialist, what are your thoughts on this? From the news reports, we hear that Spain is preparing to host the highly anticipated 10th European Additive Manufacturing Conference in Valencia. Proving the value of this concept, industry experts say this once-niche tool is now at the heart of a green industrial revolution. There is no secret that across the globe, additive manufacturing drives real progress, from zero-waste production to localised supply chains.
In this article, we explore how it supports the circular economy and puts Europe at the forefront of sustainable innovation.
What You Need to Know about 3D Printing’s Role in Europe’s Green Tech Boom
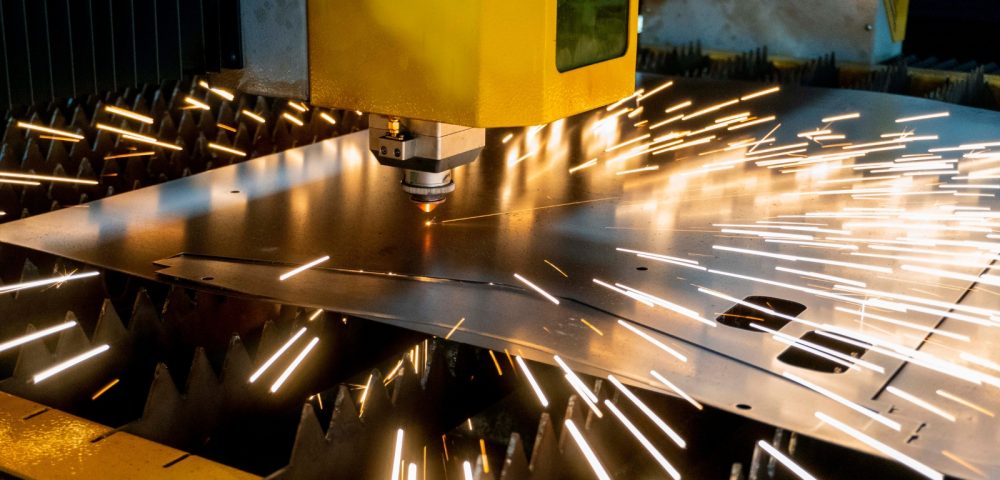
Near-Zero Waste
3D printing completely flips the script on how we use materials. Instead of cutting or shaping parts from large chunks and wasting what is left, manufacturers build objects layer by layer using exactly what is needed.
This method reduces scrap to almost nothing. In traditional factories, up to 90% of materials usually get thrown away. That does not happen with 3D printing.
Companies can now produce parts cleaner, faster, and smarter. In one way, it is about saving money; in another way, it helps Europe cut pollution and protect resources. Waste reduction has become one of the biggest reasons why 3D printing stands out in green manufacturing today.
Supports Circular Economy Goals
Europe pushes hard for a circular economy, which means keeping products, materials, and resources in use for as long as possible. 3D printing fits this idea perfectly.
Instead of creating parts that break and go to the landfill, manufacturers can now repair, redesign, or reuse items with ease. The European Commission believes these efforts could prevent up to €22 billion in environmental damage by 2030. It is certainly a huge opportunity.
As factories switch from mass production to smart design, 3D printing gives them the tools to build better, waste less, and support a greener economy that lasts beyond the next generation.
Local Production Reduces Emissions
Factories no longer need to ship parts across oceans. With 3D printing, companies can make products right where they are needed. This shift to local production cuts down on transport, fuel use, and carbon emissions.
It also means faster turnaround and fewer supply chain headaches. During recent global disruptions, many European firms saw how risky it felt to rely on distant suppliers.
Now, with 3D printing, they create spare parts and small batches in local hubs, sometimes even inside the same building where they will be used. This not only protects the environment but also brings production closer to the customer.
Spain Is Emerging as a 3D Printing Hub
Spain grabs headlines in the green tech scene as it rises fast in 3D printing innovation. The upcoming 10th European Additive Manufacturing Conference in Valencia proves the country’s seriousness about its role in Europe’s clean manufacturing future.
Spanish firms lead the shift toward smarter, sustainable design. They focus on making things better, not just cheaper. This is why cities like Valencia now attract top minds in digital manufacturing, design, and research.
Spain’s clear investment in eco-friendly production shows how 3D printing can power both environmental progress and economic growth. In the future, this will be a trend in other countries as well.
Recycling Plastics Into New Products
Europe now transforms plastic waste into 3D printing material, and that is one impressive initiative!
Researchers and manufacturers no longer treat used plastic as trash. Instead, they see it as valuable feedstock. Old vehicle parts, broken tools, and even plastic waste from oceans now find new life in industrial printing. This gives manufacturers a double win: they clean up pollution and save money on raw materials.
Projects like CircularSeas in the EU show how this idea works in real life. When plastic turns into something useful again, the planet benefits, and so do the companies ready to think beyond the bin.
Plant-Based Polymers Are Going Mainstream
As per news coming down from the manufacturing realm, manufacturers now turn to nature to create new materials for 3D printing. Plant-based polymers like cornstarch or algae blends offer a cleaner option compared to fossil fuel plastics.
These biomaterials break down faster, leave behind fewer toxins, and help reduce the carbon footprint of products. Europe’s scientists lead this push, making sustainable feedstocks that perform just as well as traditional options.
Some of these materials even come from farm waste or food leftovers, turning unwanted scraps into strong building blocks. As demand grows for planet-friendly products, bio-based 3D printing materials give companies a solid and sustainable path forward.
Design for Additive Manufacturing (DfAM)
If you look closely, you can see that DfAM completely changes how engineers think. Instead of shaping a product around factory limits, they design parts specifically for 3D printing. This method removes extra weight, improves strength, and cuts material use.
It is progress that some Spanish firms lead with this approach, creating smarter parts that need less energy and fewer resources to make. DfAM helps people build better products from the start, not fix them later. It also opens new shapes and features that were once impossible.
In the push for green manufacturing, this design shift matters, as it saves time, materials, and emissions all in one go.
Strengthens EU Resilience
Over the past years, what we have witnessed is that Europe needs strong, flexible manufacturing that will not break down during crises. 3D printing helps make that possible.
When global supply chains fail or slow down, local producers with additive technology can step up fast. They do not wait months for parts; instead, they make them. This reduces delays, protects businesses, and avoids panic buying or stockpiling.
During recent global issues, 3D printing filled gaps in everything from medical gear to machine parts. This is how European countries started seeing additive manufacturing not just as a smart tech but as a safety net. It keeps things running when the world gets unpredictable.
Cerexio's Backup for Sustainability
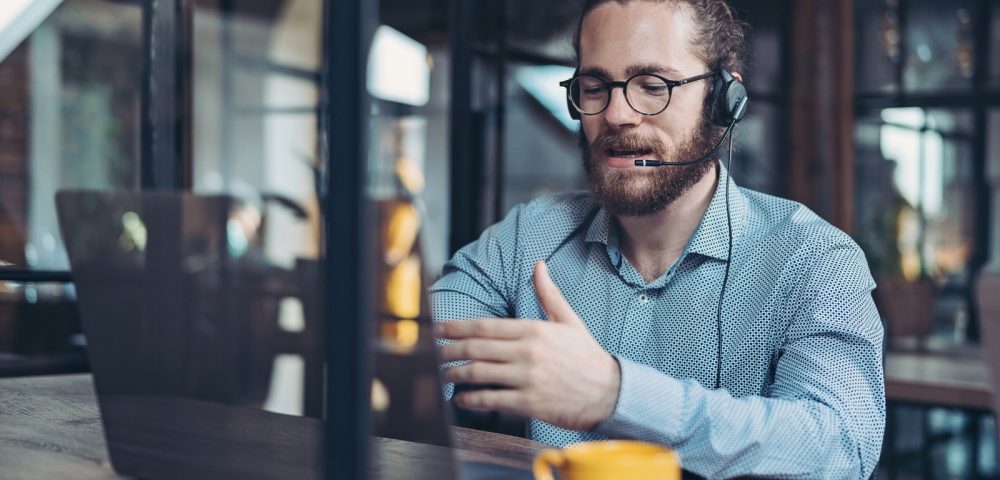
Using cutting-edge Industry 4.0 features, Cerexio’s line of software brings sustainability into every step of manufacturing. From monitoring energy efficiency to reducing waste through digital process optimisation, our software powerhouse supports greener production practices. Its embedded predictive analytics capabilities help avoid breakdowns, while the digital twin simulates improvements before real-world changes. This means lower emissions, smarter workflows, and stronger alignment with long-term environmental and business goals.
Setting Global Standards for Responsible Manufacturing via Modern Technology
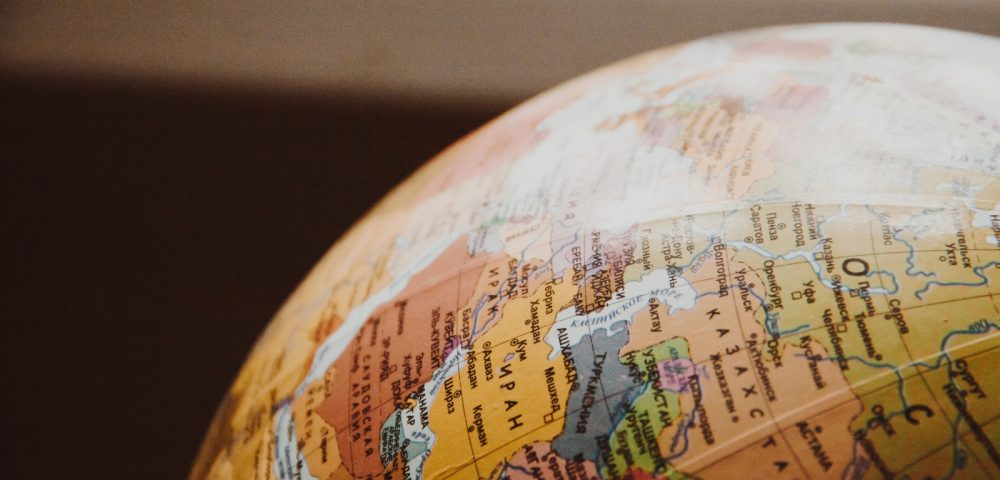
With green 3D printing unlocking ultra-efficient, low-impact manufacturing, Europe’s modern tech movement now doubles as a global wake-up call. It is not just about greener machines; it is about smarter systems, redesigned products, and ethical progress. Ready to see how technology redefines responsibility?
FAQ about 3D Printing
Yes, additive manufacturing and 3D printing refer to the same process. Both involve building objects layer by layer from digital models using materials like plastic, metal, or resin. However, additive manufacturing is the broader industrial term for 3D printing.
3D printed items cost more due to expensive materials, slow printing speeds, and high machine costs. Customisation, low production volumes, and design complexity also increase pricing. Unlike mass production, 3D printing focuses on precision and flexibility, not cheap scalability.
3D printing will not fully replace traditional manufacturing, but will enhance it. It suits custom, low-volume, or complex parts, while mass production remains more efficient for standard goods. Future factories will likely blend 3D printing with conventional manufacturing methods.