This article breaks down the four main production layout types used in manufacturing today.
Understanding Production Layout in Manufacturing
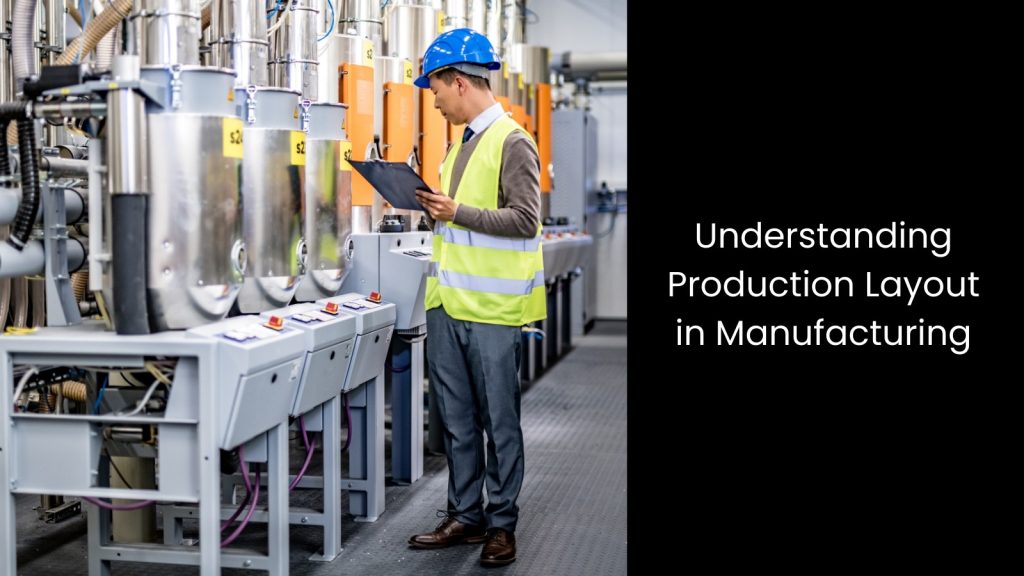
- This means how a company arranges machines, tools, and workers on the factory floor to build products in the best way possible.
- When a business sets up its machines in a smart and planned way, it makes work easier, faster, and smoother. This is what people call good production layout design.
- Manufacturers care about this a lot because the right setup can boost productivity, cut down costs, and help teams avoid wasted time moving things around. It also improves how work flows from one task to the next, making sure everything runs without confusion.
- For example, some manufacturing layout types are perfect for mass production, while others work better for customised jobs. Choosing the right one depends on what kind of products a company makes and how much of it they produce. If the layout does not match the type of work, the business ends up spending more money, time, and energy than needed.
- This is why good factory floor planning helps workers stay organised and keeps machines busy instead of sitting idle. It also makes the whole place safer and more productive.
The 4 Main Types of Production Layout Explained
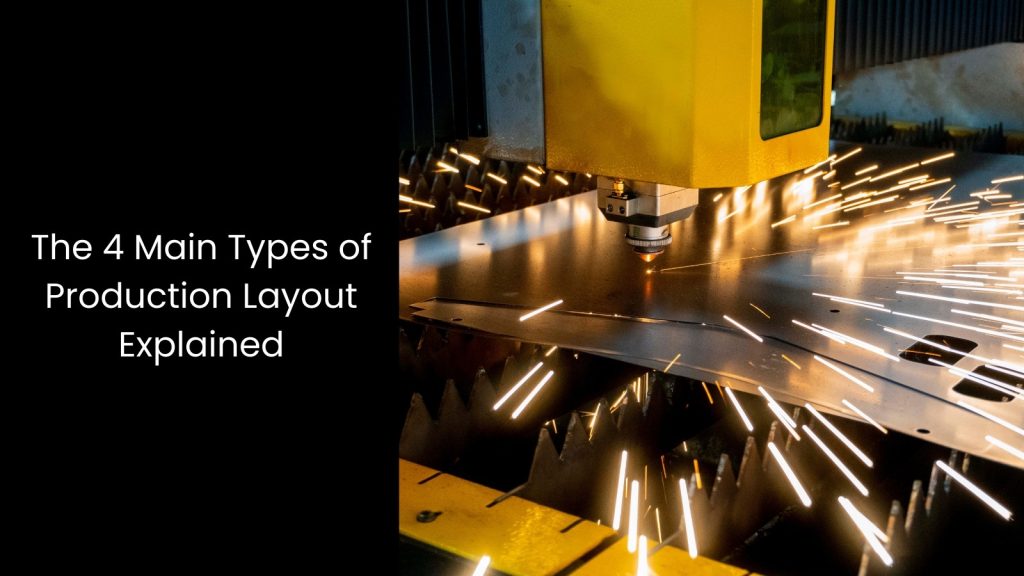
Product or Line Layout
In this setup, machines and workstations sit in a straight line, and each step of the job follows a fixed path. This means the product moves from one stage to the next without jumping around, making the whole process smooth and easy to manage.
Also, workers or machines handle just one task at each point and then pass the product down the line. This layout fits mass production because it keeps everything flowing in order, from start to finish, without stopping.
You will usually see it in places like car factories or soda bottling plants, where the same product gets made over and over again.
One big plus of this is speed. This means things move fast because everyone knows their exact job. It also reduces wasted movement, lowers handling time, and makes scheduling simple. But it is not perfect for every situation. If the product changes often or machines break down, it can cause delays across the whole line.
Process or Functional Layout
This kind of setup works really well in job shops or places that do custom manufacturing because it allows workers to handle different tasks without being stuck in a fixed order. For example, a tool manufacturing shop or a repair centre tends to use this layout since each job might need a different path and set of steps.
This layout gives employees a lot of freedom to work on unique projects because they can adjust the order of operations based on the job.
It is great due to its flexibility. It becomes easier to make changes or introduce new products without redoing the whole floor. It also helps specialists focus on their tasks since similar machines and skills stay in one spot. Still, there are downsides. Products might travel longer distances between tasks, and scheduling can get tricky when many jobs compete for the same machine.
So while it works great for variety and customisation, it takes more planning to keep everything running smoothly.
Fixed Position Layout
It makes things way easier when moving the actual product is either impossible or just not practical.
In this setup, the product stays in one spot the entire time while all the workers, tools, and equipment move around it to get the job done. Think of shipbuilding or aircraft manufacturing for a moment. No one is wheeling a half-built plane around a factory floor. Instead, engineers and teams bring everything they need to the site and complete the work in stages. This method works well when the item is too heavy, oversized, or full of complicated parts that need attention from different specialists.
While this layout helps them stay focused on a single build without rushing things or wasting time shifting huge items around, it can create some headaches, too.
Space normally runs tight since people and tools crowd around one fixed product, and coordinating different teams takes extra effort to avoid delays or confusion. Still, for industries that handle big, custom, or one-off projects, this layout makes the most sense.
Cellular or Group Technology Layout
It works like this: instead of arranging machines by process or placing them in one long line, the company forms small sections called cells. Each cell has all the tools and machines needed to build a group of similar products, which makes everything quicker and smoother.
For example, one cell might handle small batches of custom electronic parts, while another might focus on wooden furniture pieces with shared cutting and assembly steps. What makes this layout really clever is how it blends the strengths of both process and product layouts; it acts like a hybrid, letting factories enjoy flexibility without losing the flow of production.
Workers in each cell usually stay focused on one product type, so they become faster and better at their tasks. This setup also helps teams spot problems early since everything occurs in a smaller, tighter space.
However, it too does not come without trade-offs. You might face higher costs setting up multiple cells, and if product types change too much, the system can get messy. Still, for companies making custom parts in small batches, this layout offers a smart balance between speed, skill, and space.
How Cerexio MES Can Support Any Production Layout
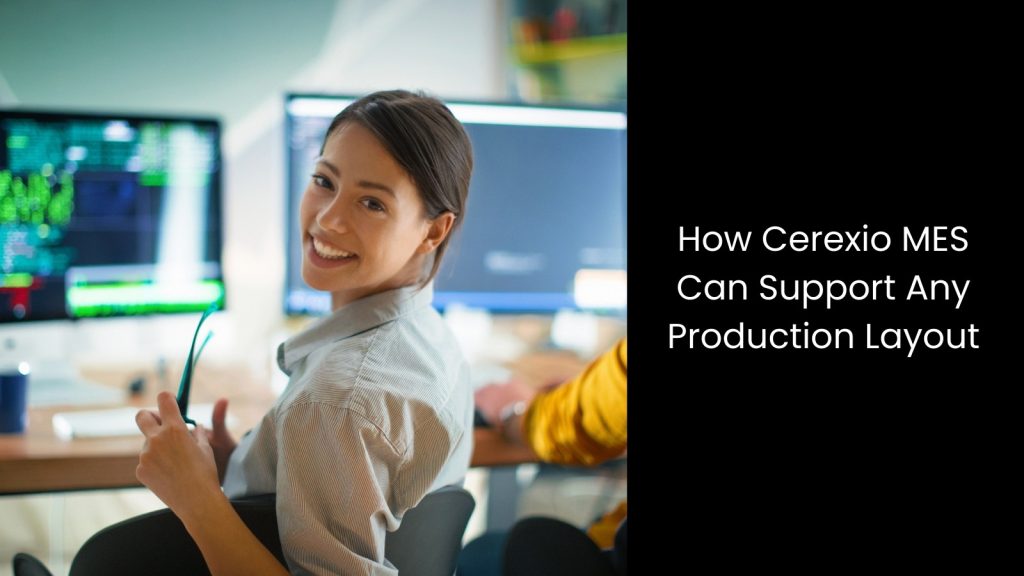
No matter the production layout, Cerexio MES offers centralised visibility across every operation. From line-based assembly to decentralised work zones, it tracks materials, labour, and machine efficiency in real-time. With Cerexio’s Industry 4.0-powered MES solution, manufacturers gain a clear, unified dashboard view, simplifying performance tracking even in the most complex or hybrid factory layouts.
Choosing the Right Production Layout, Aligning with Business Goals
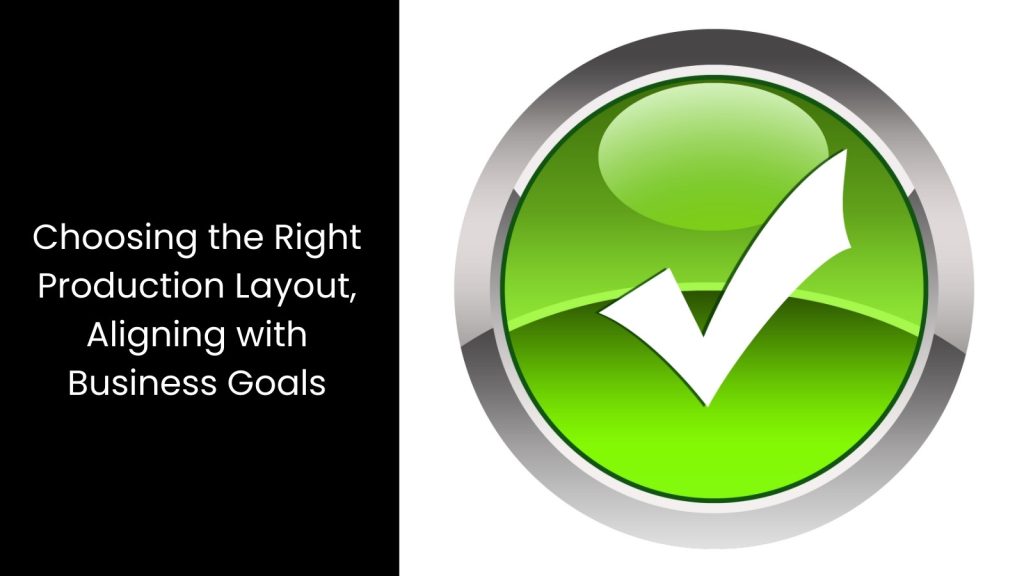
Choosing the right layout is not just a technical decision; it is actually about making your people’s work easier, your goals clearer, and your operations smarter. When your layout matches your business vision, everything flows better. You should take time to assess, plan, and align using the right technologies because it is a step toward long-term growth, not just day-to-day output.