Every manufacturer today faces the challenge of defects, rework, and wasted resources. These problems not only drain time and money but can damage a company’s reputation. So, how do you measure and improve your quality output? The answer lies here-‘ First Pass Yield (FPY)’, which is a critical performance indicator that shows how effectively you produce quality parts on the first try. FPY highlights where waste originates, giving supervisors the insights they need to streamline production and maximise efficiency.
Let us walk you through some practical strategies to enhance First Pass Yield and take your manufacturing quality to the next level!
We will explore
What is First Pass Yield?
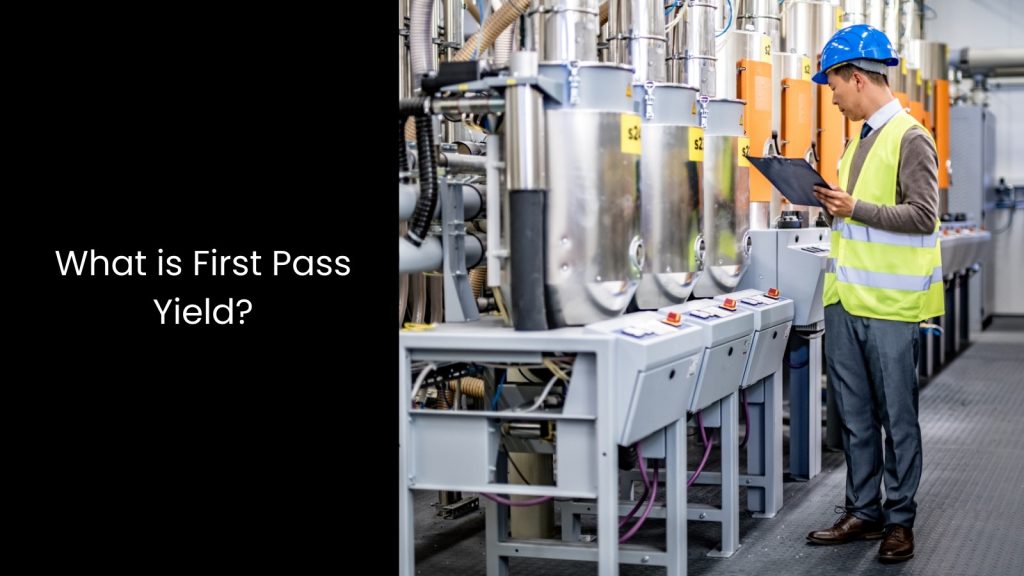
- FPY is a key metric in manufacturing that shows how efficiently a process produces quality products on the first attempt. It calculates the percentage of units that meet quality standards without needing rework or repairs.
- It works like this: A high FPY signals a smooth and efficient process with little waste, which keeps production costs down. Defects and rework create waste in multiple ways, materials get scrapped, labour hours get wasted fixing mistakes, and machines wear out without producing sellable products.
- Companies lose opportunities to create quality parts when rework wastes time and resources!
- This is why Improving FPY has become all about finding and fixing the root causes of defects. When FPY stays high, manufacturers benefit from happier customers, reliable delivery times, and better pricing competitiveness. This efficiency turns into a real competitive edge.
- However, focusing only on FPY can hurt overall performance if you ignore other important metrics like Overall Equipment Effectiveness (OEE). A balance of metrics gives a clearer view of production health.
- One thing manufacturers need to understand is that FPY is not a magical fix-all, but it acts as a strong indicator of process quality.
How to Improve First Pass Yield-Top 5 Ways
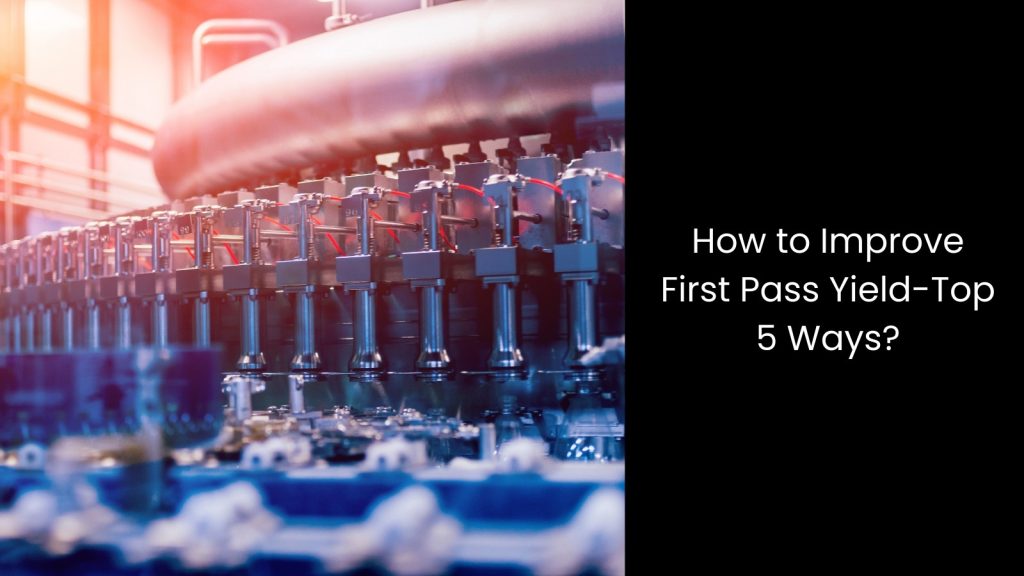
Refine Standardised Workflows
Improving First Pass Yield generally starts with refining standardised workflows on the production floor.
The overall idea is that clear and efficient processes lead to consistent quality and fewer defects. Engineers and managers must carefully review current workflows to spot inefficiencies, like bottlenecks that slow production or cause mistakes. They can use production data to visualise these problems and design better procedures.
When supervisors watch how workers make each component, they can adjust instructions to ensure every step makes sense and flows smoothly. Metrics like setup times, cycle times, and job durations become more accurate when teams continuously refine processes. Combining quality data with these metrics helps create realistic production goals that operators can actually meet.
The ultimate result is that workers feel more confident and less stressed when expectations match reality, which leads to higher-quality output. Instead of guessing how long a task should take or how to complete it, operators can follow clear, detailed instructions that are easy to understand. Refining workflows does not just make tasks faster; it also makes them smarter.
Implement Real-Time Quality Data Collection
This is undoubtedly a powerful way to boost First Pass Yield in manufacturing.
When the mechanism has automated systems, it instantly captures data from machines and operators, eliminating the delays and mistakes that come with manual data entry. These accurate, real-time data allow manufacturers to set realistic goals and spot defects as they happen. When operators use tablets to log defect reasons on the spot, the system provides immediate feedback, helping teams understand where things are going wrong. This profound insight into quality issues lets managers and engineers quickly adjust processes, preventing more defective products from being made.
In another way, real-time data helps trigger instant quality control actions, like alerting the right teams to fix problems before they snowball. Instead of wasting time guessing what went wrong, teams rely on up-to-the-minute data to take swift, targeted action. This approach not only reduces rework and scrap but also keeps production lines running smoothly. When manufacturers fix issues quickly, they save on labour, materials, and machine wear.
Track Machine Health and Performance
When equipment runs smoothly, quality improves, and fewer defects occur.
Real-time monitoring systems send automated alerts, like equipment failure or quality problems, when something goes wrong. These instant notifications let teams jump into action and fix issues before they get worse. Instead of discovering a problem after hundreds of faulty parts are produced, manufacturers can catch defects early and avoid massive waste.
Plus, keeping an eye on tool wear and breakage makes a big difference. Worn-out tools usually lead to defective parts, but tracking their condition helps stop these errors before they occur. Further, dashboards that display live machine performance give managers the power to spot downtime, performance drops, or quality dips immediately. This visibility helps teams make quick decisions to keep production on track.
The process stays efficient with fewer delays and breakdowns, and products meet quality standards on the first try.
Enhance Operator Training and Empowerment
When operators receive thorough training, they gain the knowledge and confidence to meet quality standards for every task. Providing clear instructions helps them understand each step of the process without confusion. If there are tools like tablets or dashboards, it helps to give operators real-time feedback and performance metrics, keeping them aware of how well they are doing. This instant feedback helps them quickly correct mistakes, improving efficiency and reducing errors.
When workers know exactly what the company expects and see their progress, they naturally focus on tasks that bring the most value. This awareness also encourages them to solve problems on the spot instead of waiting for a supervisor to step in.
Empowering operators with control over their productivity makes them feel responsible for the quality of their work, which increases their motivation.
Strengthen Supplier Quality Control
High-quality materials form the backbone of excellent First Pass Yield.
However, in order to achieve this, manufacturers must strengthen supplier quality control. Selecting reliable suppliers starts with choosing those with solid certifications, proven industry experience, and positive references. These factors act as guarantees that suppliers can meet strict quality standards.
Then comes the stage, which requires checking incoming materials through detailed inspections as it helps catch any defects before they affect production. Collaborating closely with suppliers also creates a clear understanding of your expectations. When both parties work together, suppliers know precisely what quality levels you need. This teamwork ensures fewer defective materials enter the production line, reducing waste and rework.
This consistency boosts FPY and helps avoid costly delays. Spotting problems early with supplier materials prevents bigger headaches down the line. Building strong relationships with suppliers makes them more likely to address concerns quickly and maintain high standards. Investing time in supplier quality control benefits the manufacturing process and keeps customers satisfied with reliable products.
Cererxio Solution to Maximise Yield in Manufacturing
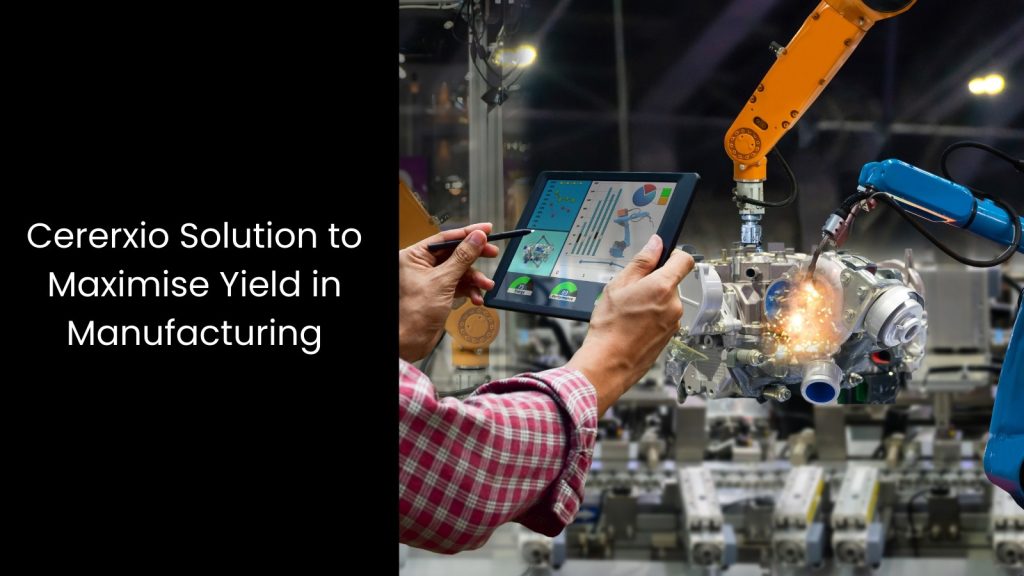
Cererxio presents an end-to-end solution- ‘Production Yield Optimiser System’, specifically tailored to maximise yield in manufacturing, using advanced data analytics, real-time quality monitoring, and automated systems to streamline processes. Our solution identifies defects early, improves machine performance, and refines workflows. Since it empowers operators with instant feedback and optimises supply chain quality, the Cerexio solution reduces waste and rework. If your problem is yield in manufacturing, Cerexio is where you find the perfect answer.
Improving First Pass Yield Easily for Manufacturing Brilliance
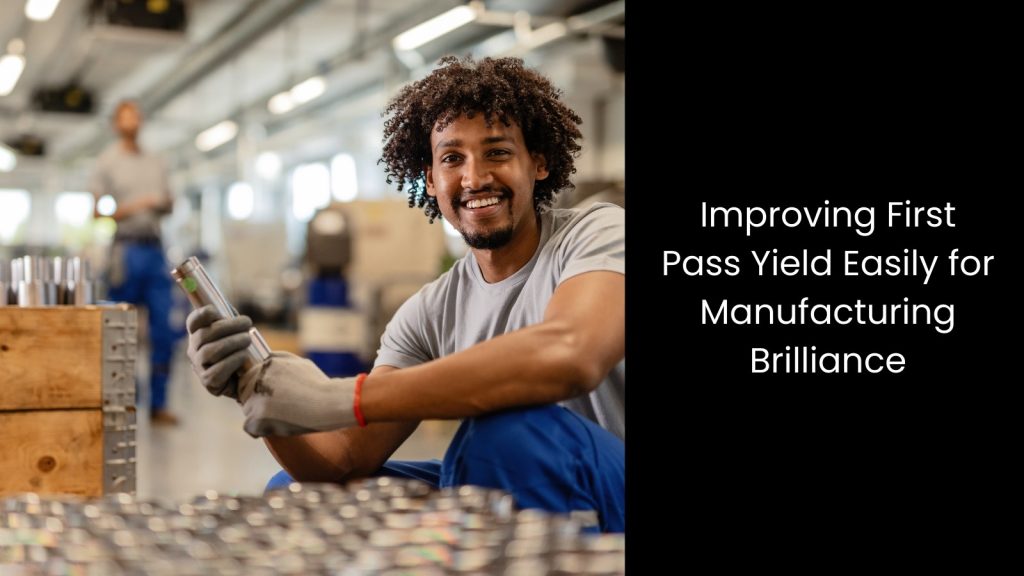
Achieving a high First Pass Yield does not need to be a struggle anymore! Implementing strategic approaches like real-time quality monitoring, advanced data tools, and efficient workflows transforms your manufacturing game. These new technologies reduce defects and waste, driving your production towards brilliance. You can easily embrace these solutions to maximise yield, satisfy customers, and stay competitive.