This article explores how RFID reduces human error in manufacturing.
Understanding Human Error in Manufacturing
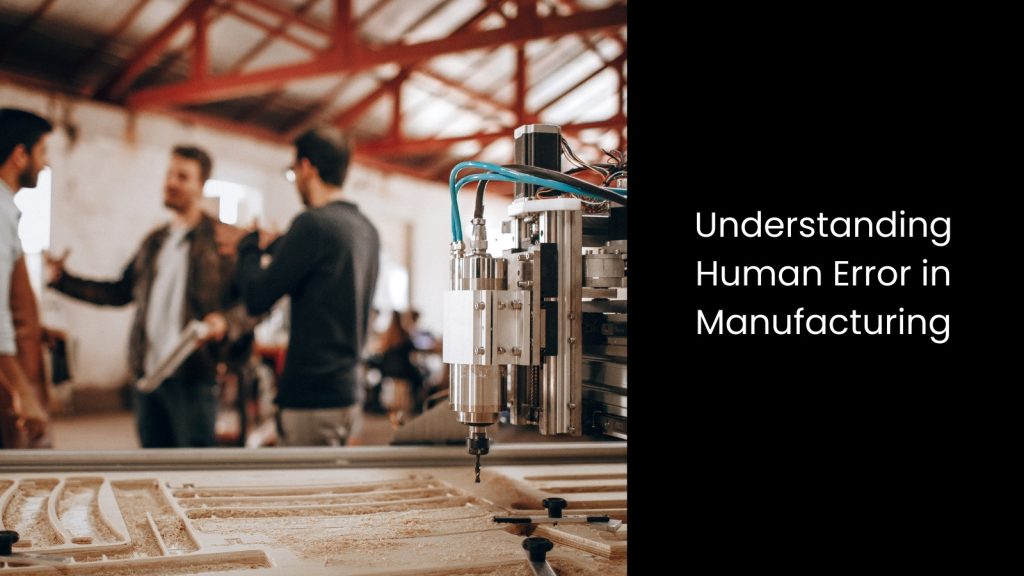
- In the simplest terms, human error refers to mistakes made by workers that disrupt or compromise production processes.
- In manufacturing, this can take many forms! It can be data entry errors, manual inventory miscounts, incorrect equipment operation, missed quality checks, etc. These small mistakes usually snowball into serious issues, such as defective products, wasted resources, or costly downtime.
- Human error is especially prevalent in environments with heavy manual processes, where even experienced staff may face fatigue, distractions, or inconsistent workflows. As manufacturers strive for leaner operations and tighter quality control, human error reduction becomes a strategic priority.
- Relying solely on manual tasks leaves room for error, but technologies like RFID offer a scalable solution to reduce such risks.
What is RFID Technology?
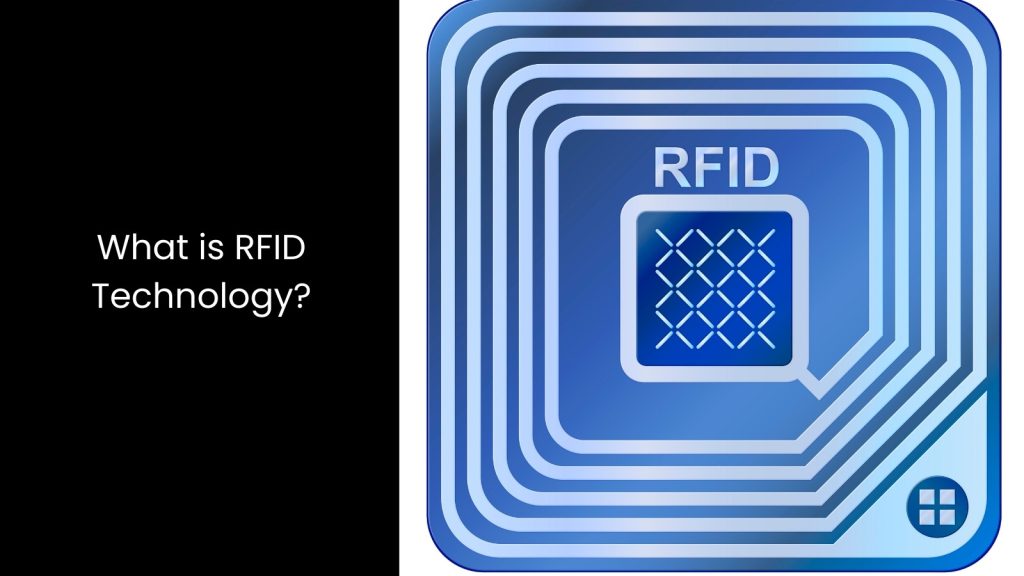
- RFID, or as we mentioned above, Radio Frequency Identification, is a wireless system that uses radio waves to identify and track objects or people.
- It consists of three main components: RFID tags (attached to items), RFID readers (devices that scan the tags), and software systems (which store and process the data).
- When an RFID reader scans a tag, it instantly collects information such as product ID, location, and movement history. Unlike barcodes, RFID does not require a direct line of sight and can scan multiple tags simultaneously. This makes it more efficient for high-volume environments.
- When integrated with manufacturing execution systems (MES) and warehouse management systems or platforms, RFID in manufacturing provides real-time data that improves decision-making and minimises errors.
Key Ways RFID Reduces Human Error in Manufacturing
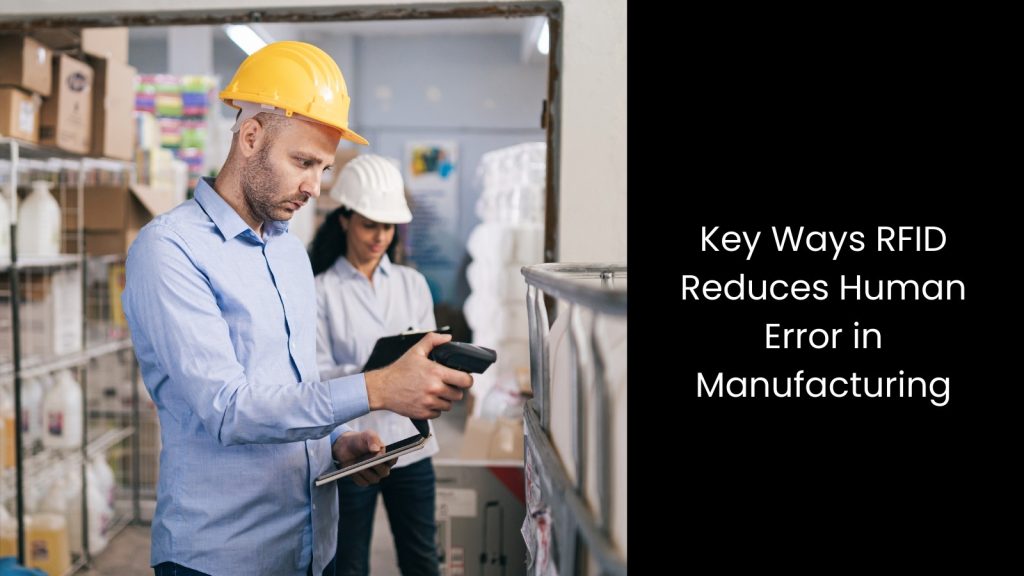
Inventory Accuracy and Tracking
As products move through the supply chain, RFID automatically logs their positions, quantities, and handling history. This prevents double scanning, misplacement, and manual entry mistakes.
In warehouse management systems, RFID tags help staff quickly locate materials, reduce out-of-stock issues, and avoid sending incorrect shipments. Unlike manual inventory audits that are time-consuming and prone to oversight, RFID systems can complete stocktaking in a fraction of the time with higher accuracy.
Since it minimises reliance on paper-based logs and manual scanning, RFID reduces both human workload and the risk of error, ensuring streamlined operations across storage and retrieval processes.
Process Automation and Workflow Control
For example, RFID systems can scan components before they enter an assembly line, ensuring that the required items are present and correctly matched. If something is missing or out of place, the system alerts operators before a mistake occurs. This reduces the burden on workers to manually cross-check parts and allows for more fluid and consistent workflows.
Additionally, RFID supports automated machine start-ups and shut-offs based on tag verification, helping prevent equipment from operating under unsafe or incorrect conditions. This level of process automation not only enhances safety but also standardises production routines, reducing the variability that leads to error.
Quality Assurance and Error Detection
If an item skips a required test or fails a check, RFID systems can detect the anomaly in real-time and prevent the item from moving further down the line.
This early error detection limits defective products from reaching customers and reduces the need for costly rework or recalls. For industries like automotive and aerospace, where quality standards are stringent, RFID helps meet strict compliance benchmarks by maintaining detailed traceability records.
These records enable rapid root cause analysis in the event of defects, accelerating quality improvement initiatives and reducing future occurrences of the same error.
Employee Accountability and Task Verification
RFID-enabled ID badges can track who accessed specific machines, completed certain tasks, or handled high-risk materials. This level of task verification ensures that only authorised personnel perform critical operations and that all activities are recorded for audit purposes.
It also allows managers to trace back the source of any issues to identify training gaps or process flaws.
With better visibility into individual contributions, manufacturers can implement targeted upskilling and performance evaluations.
RFID also discourages shortcuts or procedural deviations, promoting a culture of discipline and responsibility. As it makes every action traceable, RFID establishes a transparent environment where errors are less likely to go unnoticed or unaddressed.
Real-Time Data Collection and Decision-Making
Your managers can monitor operations remotely and receive immediate alerts if anomalies occur, such as materials arriving at the wrong station or production delays. Powerful real-time insights allow for faster decision-making, proactive issue resolution, and better overall coordination.
Data collected from RFID systems can also be used to analyse performance trends, optimise resource usage, and predict future bottlenecks.
Whether it is rerouting a stalled process or reallocating labour based on real-time output levels, the ability to act swiftly helps reduce inefficiencies and prevent compounding errors.
Benefits Beyond Error Reduction
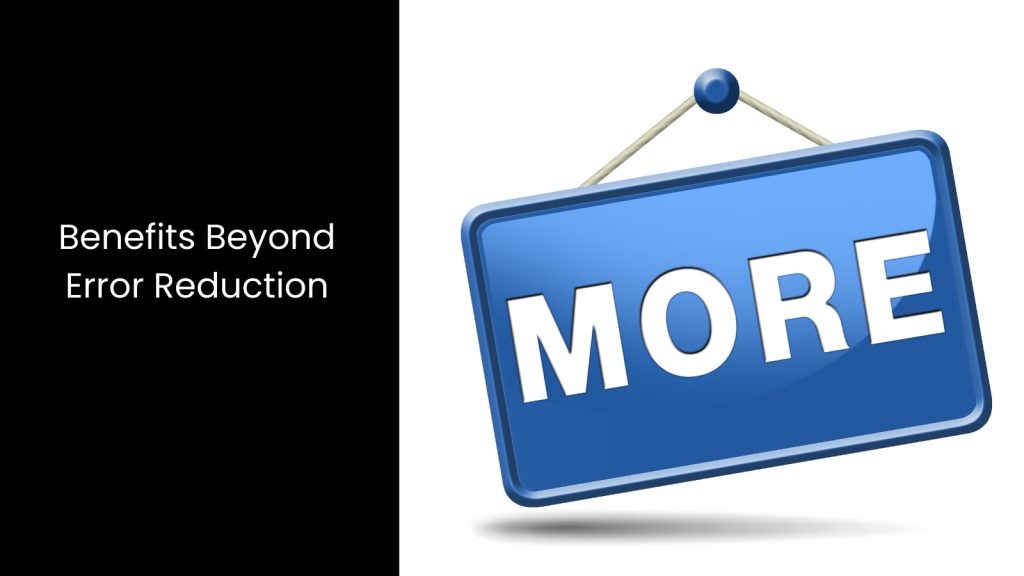
- These include increased operational efficiency, cost savings, better regulatory compliance, and enhanced customer satisfaction.
- RFID also improves traceability, making it easier to track parts and materials throughout their lifecycle, a vital feature for industries with strict safety and quality standards.
- RFID simplifies audits and ensures that documentation is automatically recorded and retrievable.
- As manufacturing becomes more connected and smart manufacturing evolves, RFID positions companies to embrace Industry 4.0 by laying the groundwork for intelligent systems and automation.
How Cerexio WMS Helps in Manufacturing Error Reduction
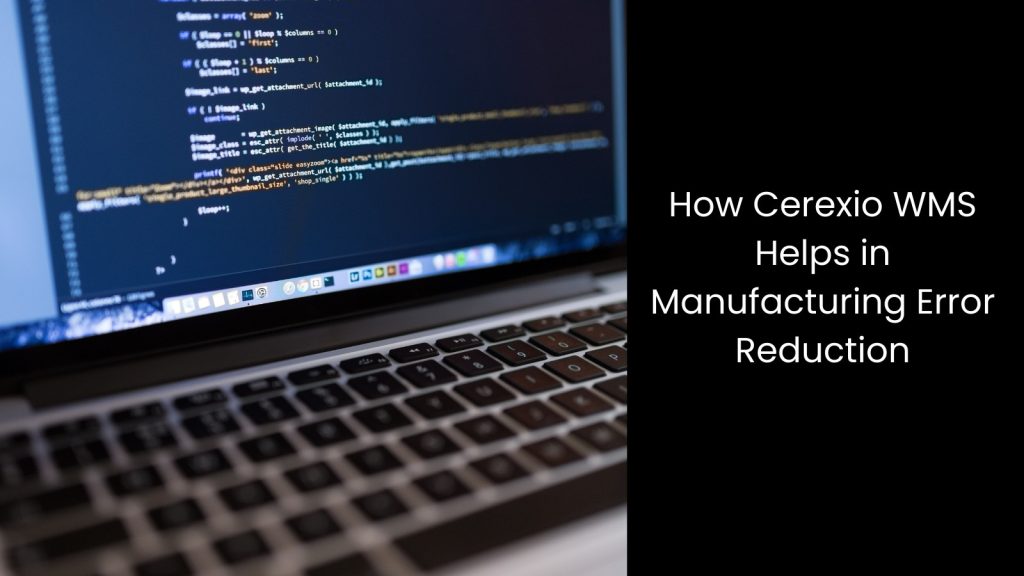
Integrated with RFID, Cerexio WMS automates inventory control and part verification, eliminating human errors in stock management. This integration ensures accurate material tracking, prevents mis-shipments, and improves workflow efficiency, ultimately supporting error-free manufacturing operations.
Skyrocketing towards Manufacturing Success with Fewer Errors
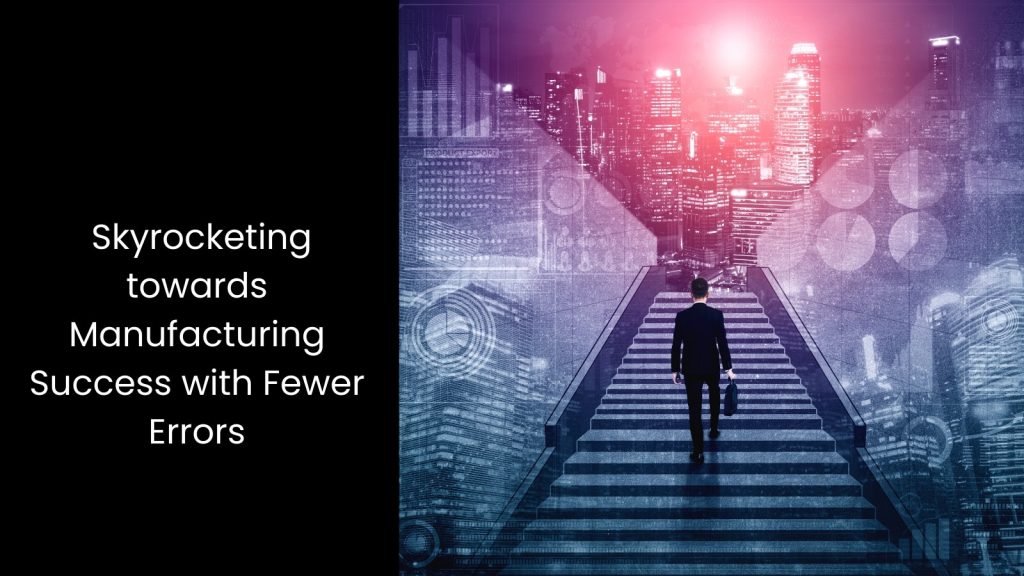
Since we have stepped into a competitive and high-stakes manufacturing environment, reducing human error is essential for profitability, compliance, and customer trust. If you can adopt RFID technology, manufacturers can eliminate many of the risks associated with manual processes. As RFID in manufacturing continues to evolve, its ability to support human error reduction, boost productivity, and enable smart decision-making will become indispensable. Companies that embrace RFID today will be better prepared for the digital future of manufacturing success.