The integration of automation in lean manufacturing has proven to be one of the best strategies ever. Do you wonder why? Automation simply enables companies to eliminate waste, reduce costs, and improve overall efficiency. From reducing cycle times to improving safety, automation is transforming the way manufacturers approach production. With these advancements, businesses can meet growing demand without sacrificing quality or efficiency.
This article is about the role that automation plays in lean manufacturing.
We will know
This is How Automation Works in Lean Manufacturing
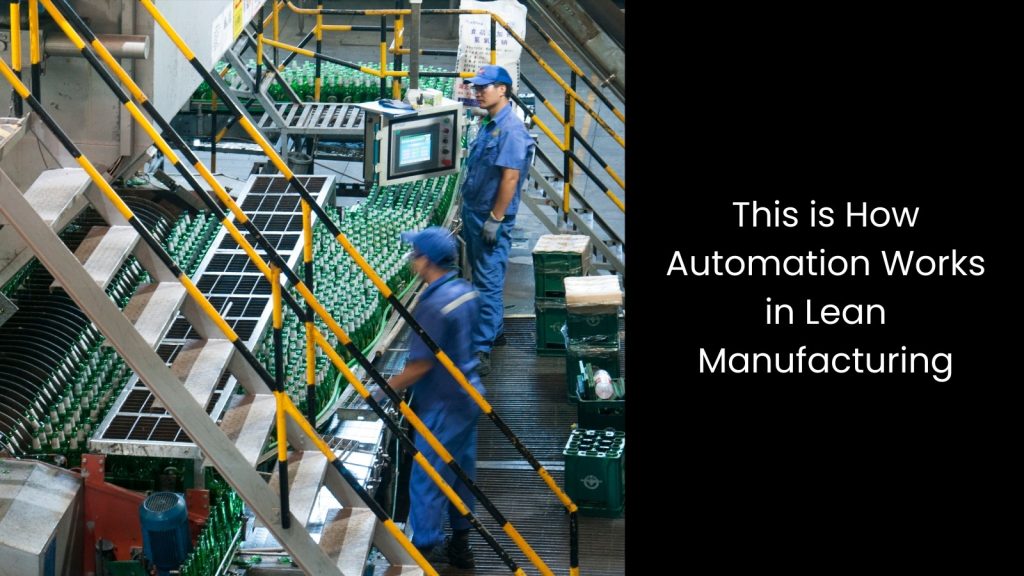
It Reduces Waste
Automation backs up waste reduction in lean manufacturing by streamlining processes and eliminating inefficiencies. In lean manufacturing, the focus is on minimising non-value-added activities, and automation helps achieve this by taking over repetitive tasks that are prone to errors or inefficiencies when done manually.
With automation, machines can work continuously, maintaining high precision and consistency, which reduces the likelihood of defects and scrap. These systems can also track materials in real-time. It will ensure that only the necessary amount is used in production, which prevents overproduction, a common form of waste.
Instead of relying on human intervention, which can sometimes result in delays or miscalculations, automated systems ensure that the right quantities are produced at the right time, cutting down on excess inventory. Moreover, automation enables faster detection of faults, allowing for quicker corrective actions that minimise downtime and reduce the waste associated with rework.
The result is a more efficient production process with fewer mistakes, reduced costs, and higher-quality products.
Automation Improves Efficiency
Regarding lean manufacturing, reducing waste and optimising production are the most important fact. This is where automation helps in both these areas.
Machines handle repetitive tasks much faster than humans, which cuts down on production time and increases the number of items produced within a given period. Automation also ensures that tasks are performed consistently without the slowdowns or errors that human workers might face due to fatigue or distractions. This consistency helps eliminate delays that typically occur during manual setups, as automated systems can quickly adjust to new tasks or product types.
In addition, automation reduces the time workers spend on non-productive activities like waiting for materials or troubleshooting problems, freeing them up to focus on higher-value tasks. Automation can also help improve coordination between different stages of production, ensuring that materials move smoothly from one step to the next without unnecessary hold-ups.
As a result, manufacturers see a more streamlined operation, where work flows without interruption and production stays on track.
It Facilitates Cost Savings
Cost is one of the burdens that lean manufacturing aims to reduce, and automation plays a key role in achieving this goal.
Automation helps lower costs in various ways by minimising the need for manual labour, which leads to significant savings in wages and benefits. Machines work faster and more accurately than humans, reducing errors that often result in costly rework or scrap. With automation, the production process runs smoothly and consistently. This will eliminate downtime and delays caused by human factors such as fatigue or mistakes.
Automation also helps optimise the use of materials, preventing waste and ensuring that only the required amount is used, which reduces material costs. Furthermore, automation can improve energy efficiency by managing power consumption more effectively, leading to lower utility bills.
Manufacturers can also save on training and supervision costs because automated systems require less oversight compared to a workforce of human workers. Likewise, automation supports a more efficient workflow, cutting down on unnecessary steps and allowing resources to be used more effectively.
It Increases Throughput
Automated systems operate continuously without the breaks or slowdowns that human workers need, which means they can produce goods around the clock. This constant operation allows manufacturers to increase the volume of products without additional labour costs or downtime.
Automation also reduces cycle times because machines can perform tasks faster and more consistently than humans, speeding up the entire production process. As machines handle repetitive tasks more efficiently, workers can focus on tasks that require more skill, further improving productivity.
Automation also helps streamline workflows by coordinating different production steps more effectively, eliminating delays and bottlenecks that often occur when tasks depend on human interaction. When production processes flow more smoothly, throughput rises because goods move from one stage to the next without interruption.
This improvement in efficiency and speed allows businesses to meet demand more effectively and improve their competitive edge in the market.
Automation Improves Accuracy
You know, in lean manufacturing, errors in production lead to wasted time, materials, and resources. Automation helps solve this by executing tasks with high precision every time, making sure each product meets the required specifications.
Machines do not suffer from fatigue, distractions, or varying skill levels, which are factors that can affect human performance. As a result, automated systems produce products with less variation, maintaining uniformity in each batch. This consistency reduces the need for rework or corrections, directly saving time and resources.
Automation also ensures that measurements and adjustments are made accurately in real time, preventing mistakes that might go unnoticed in manual operations. Plus, automated systems can be calibrated to make fine adjustments based on immediate feedback, which helps maintain high standards.
In lean manufacturing, this accuracy translates to fewer defects, less waste, and better quality control. With accurate processes in place, manufacturers can produce goods faster and with less effort, aligning with lean principles to optimise resources and minimise unnecessary steps.
Automation Enhances Safety
Automation helps minimise accidents by taking over dangerous or physically demanding tasks.
For example, robots can handle heavy lifting, high-temperature processes, or work in environments with toxic materials, removing the need for workers to be exposed to these risks. This reduces the chances of workplace injuries and illnesses, creating a safer space for employees.
Automation also helps prevent human error, which is a leading cause of accidents. Machines can work with precision and follow strict protocols, reducing the likelihood of mistakes that can result in injury or damage to equipment.
Additionally, automated systems can be equipped with sensors that detect irregularities or dangerous situations, instantly shutting down operations to prevent harm. This real-time monitoring enhances safety and allows for quick responses in emergencies.
With automation taking over the riskier tasks, workers can focus on more strategic activities in safer conditions. In lean manufacturing, this not only improves safety but also increases productivity, as fewer injuries mean fewer disruptions in the workflow.
Cerexio's Automation Powered Manufacturing Software Solutions Strengthen Lean Manufacturing
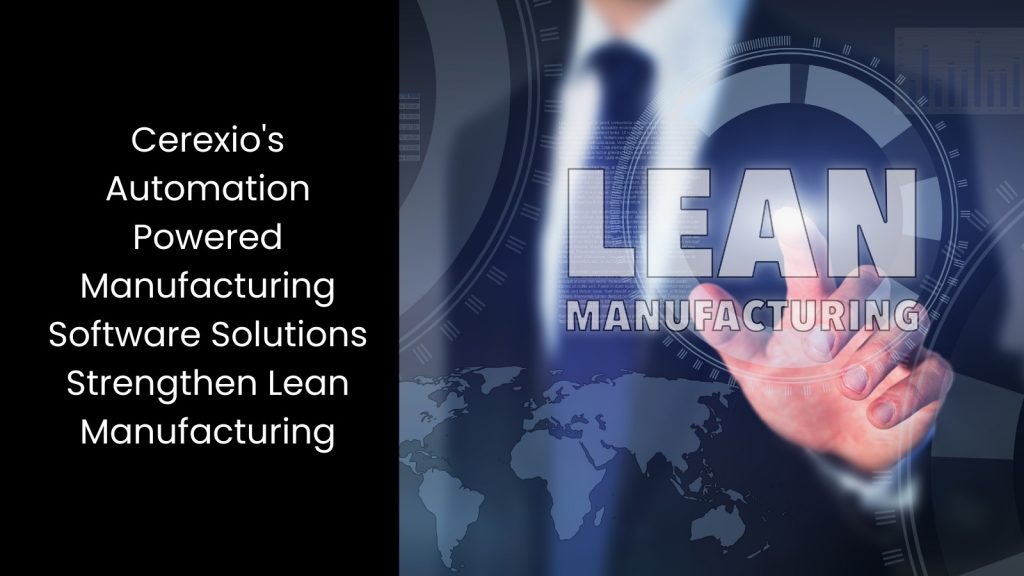
Cerexio’s Automation Powered Manufacturing Software Solutions strengthen lean manufacturing by streamlining processes, reducing waste, and enhancing efficiency. Our solutions automate repetitive tasks, minimise errors, and optimise workflows, allowing manufacturers to increase throughput while maintaining high quality. With real-time monitoring and data-driven insights, Cerexio’s software suites support continuous improvement, ensuring faster production cycles and cost savings in lean manufacturing environments.
Streamlining Lean Manufacturing with Automated Tools
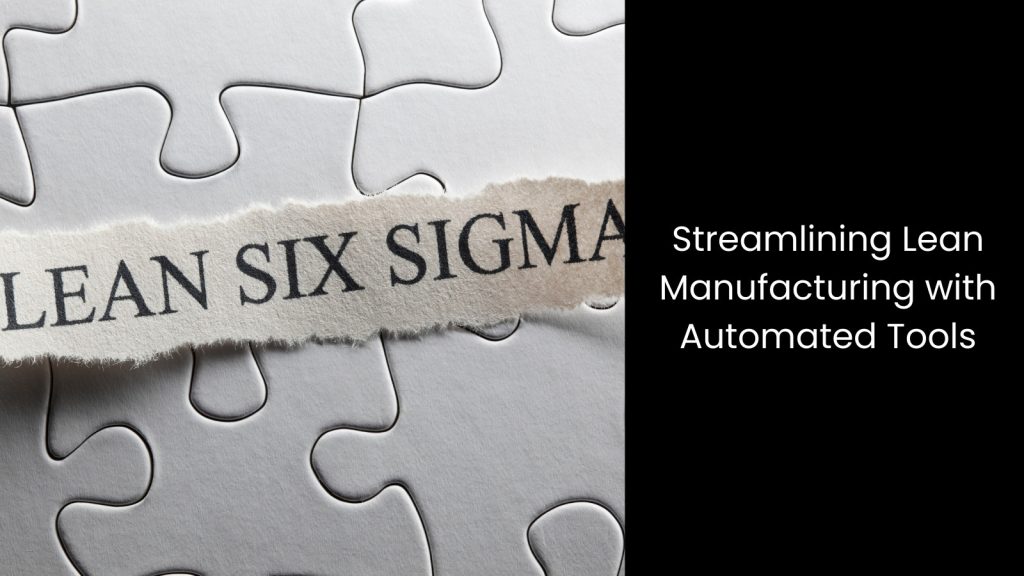
As automation continues to evolve, lean manufacturing stands to benefit from smarter, faster production methods. Incorporating such advanced automated tools allows your manufacturing company to enhance efficiency, cut waste, and streamline operations under one platform. Manufacturers that embrace these advancements will be better positioned to meet market demands and maintain a competitive edge in the industry.