The manufacturing sector has long been experiencing a labour shortage, even before the pandemic. For instance, a 2018 study predicted that globally more than 8 million jobs in manufacturing will be unfilled by 2030. This fear was worsened by COVID-19, growing the number of jobs that will remain to be unfulfilled in the impending future. To address many concerns, manufacturers and warehouses have turned to digitalisation.
The digitalisation of factories has made manufacturing and warehouse operations much safer and more accessible. Companies are now able to finish their tasks faster and without errors. For some manufacturers adopting labour utilisation technology is no longer a choice. With the lack of labourers to do the work, manufacturers worldwide require a robot or software program to handle tasks and responsibilities. Additionally, such solutions are known to offer better value for money in terms of maximising labour productivity. This article will explain how labour utilisation technology responds to the skill gap.
Why is There a Skill Gap?
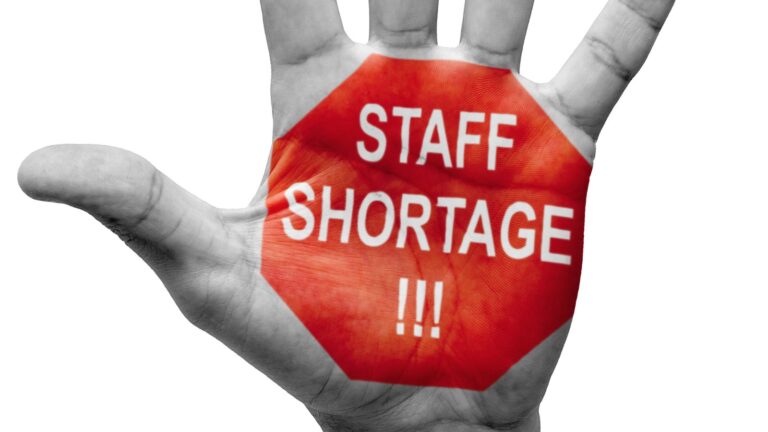
According to HBK, a financial service firm, 22 per cent of skilled manufacturing workers in the world belonging to the baby boomer generation will be retiring by the end of 2025. As a result, with approximately 2 to 3.5 million job opportunities available in 2025, manufacturing companies are at risk of going out of business. One reason for this is the lack of interest among the youth.
Young people are not incentivised to work in the manufacturing sector due to the misconceptions held by the public. For instance, society believes that manufacturing is a low-skilled job that offers very little pay. In reality, however, the industry works with a wide range of advanced technologies that require a unique set of skills and offers competitive remuneration rates with additional benefits. Singapore specifically has introduced an Overseas Networks & Expertise (ONE) pass, launched in January 2023, hoping to attract top talent worldwide to work in local firms.
The after-effects of COVID-19 have also greatly affected the decrease in the skills gap. For instance, the pandemic opened the public’s eyes to choose workplaces that offer more stability. The disruption in the semiconductor supply chains affected auto and electronic manufacturers whose number of goods produced significantly decreased. As profits were reduced, the number of workers laid off also increased, resorting to people finding more secure jobs in the future. Other external world events, such as the Ukraine war, have also affected the sector, leading to the manufacturing industry gaining a less attractive position in the job market.
One last important factor for the labour shortage is the skills gap. With the number of technological advancements made throughout the years, it has removed the need to hire people for certain roles and responsibilities while opening new job opportunities. Unlike traditional manufacturing tasks, which were repetitive and mundane, these functions require new skills. According to one report, this skills gap has resulted in 10 million manufacturing jobs in the world being filled. While manufacturing companies can provide training opportunities, encouraging more people to join the sector has been challenging.
What Kind of Solutions Amount to Labour Shortage
The lack of employees in the manufacturing industry has led to workplace injuries, led numerous instances of product liability and a surge in finances. This is why labour utilisation technology is a mandatory tool for manufacturers. Here are three labour utilisation technologies that factories should consider adopting:
Cobots
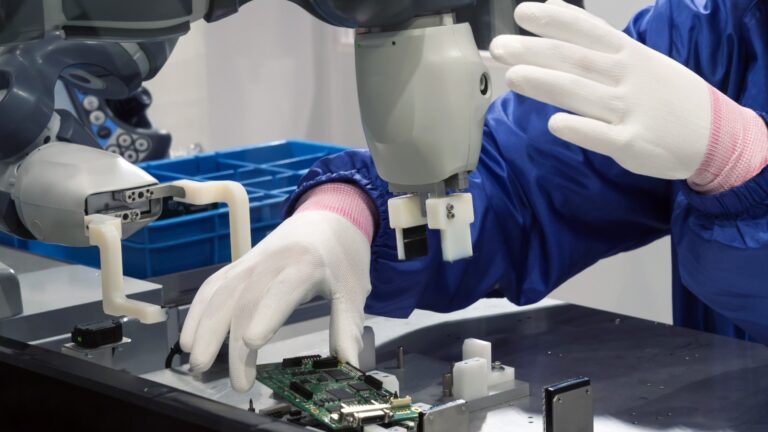
Also known as collaborative robots, cobots work alongside existing staff members. They help create a safer work environment for human workers and assist them in the packaging, pick-ups, palletising, monitoring, welding, deburring and more. Unlike other robots trained to carry out tasks through whatever means, thereby leading to anyone possibly injured, cobots sense when a human is close by and will switch on to a safe mode. This is a cost-effective robot that can easily be integrated into any type of manufacturing company. It significantly helps in quality control and in optimising production processors.
Digital Workers
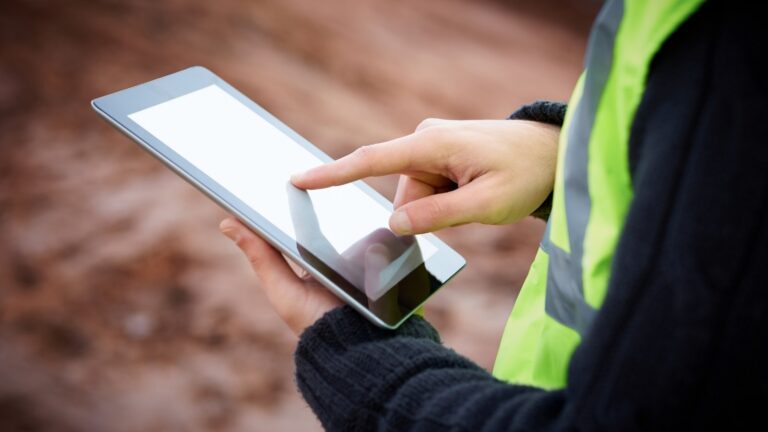
Digital workers is a semantic automation tool that integrates robotic process automation (RPA) with conversational AI. Digital workers communicate with humans using a social platform, such as Slack or Microsoft Teams, and similar to any other employee, they will execute its functions when requested. This makes it an interactive form of automation. For example, you can ask a digital worker to schedule an event or draft and send an email by simply sending a message. Unlike traditional RPA, digital workers can automate a wider range of tasks. They have the capability to learn from past experiences and improve their communication skills with the help of AI.
Industry-Specific Software Programmes
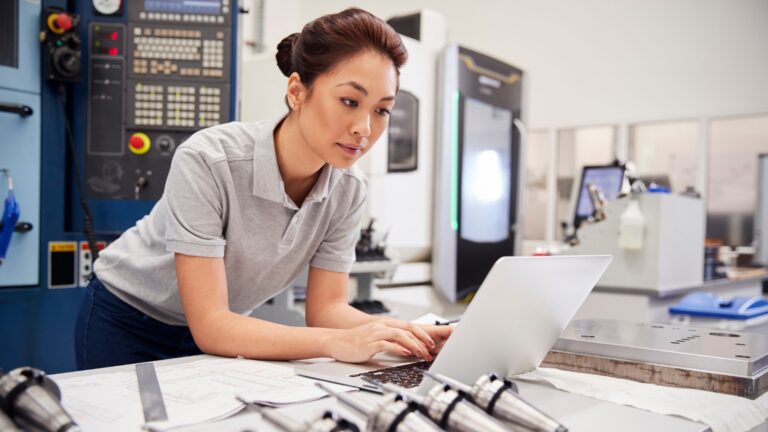
Today, advanced software vendors develop solutions that can monitor the health of assets in factories, warn managers of any anomalies, provide valuable insights with the help of AI-infused data analytical capabilities, and schedule maintenance based on criticality. Such software solutions act as a way to manage and overlook the multitude of processors occurring on the production floor. They can detect whether any change in the supply chain has affected product quality and help companies build a trustworthy reputation among their customers, who would be able to trace any goods sent by the manufacturing or warehouse factory. This eliminates the need for teams to carry out daily checks and hire data scientists.
Cerexio: Providing Solutions That Solve The Labour Shortage
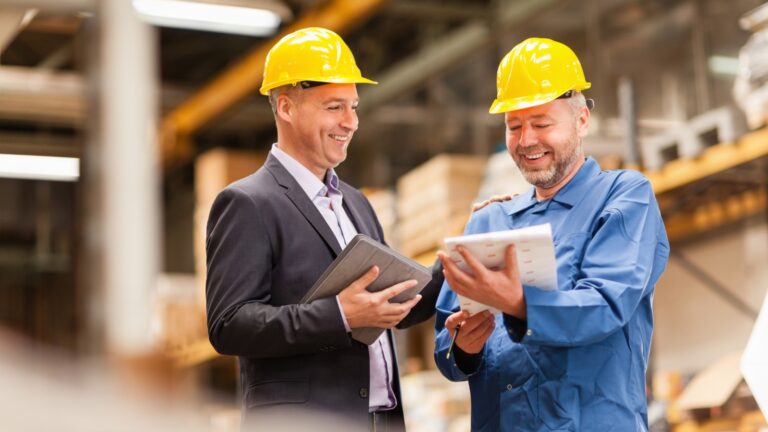
Cerexio specialises in engineering a range of industry 4.0-powered digital solutions that automate various processes to ensure perfection in every respect. Two of its solutions include Cerexio MES, a recognised software specifically made for the manufacturing sector and Cerexio Smart WMS, an all-in-one warehouse management suite that optimises all operations. These solutions monitor each asset, warn you of impending risks and anomalies, strengthen the assets’ lifecycle of assets and help you to make feasible financial budgets. Most importantly, these well-rounded solution suites include the right features to maximise labour utilisation. It automates mundane and repetitive processes, can easily make reliable progress reports in seconds and give you hidden insights on changing market and consumer changes.
Connect with Cerexio to see how you can keep reaping success in industries facing labour shortages due to the increased skills gap.
From A Human Workforce to an Augmented Workforce
While an augmented workforce will help companies improve their productivity significantly, it does not mean that all human employees should or would be replaced soon. No matter how efficient digital technologies can make a manufacturing company, a human workforce will still be important. For instance, while a system may recommend what needs to be done, the workforce will have to implement them to monitor its progress. Innovation is also driven by human creativity, and an augmented workforce is simply present to assist such teams in reaching their business goals. In other words, Industries like manufacturing need to work alongside technology to succeed in this competitive world. As manufacturing companies worldwide are struggling to fill vacancies and the skill gap is only growing daily, labour utilisation technologies are a must.
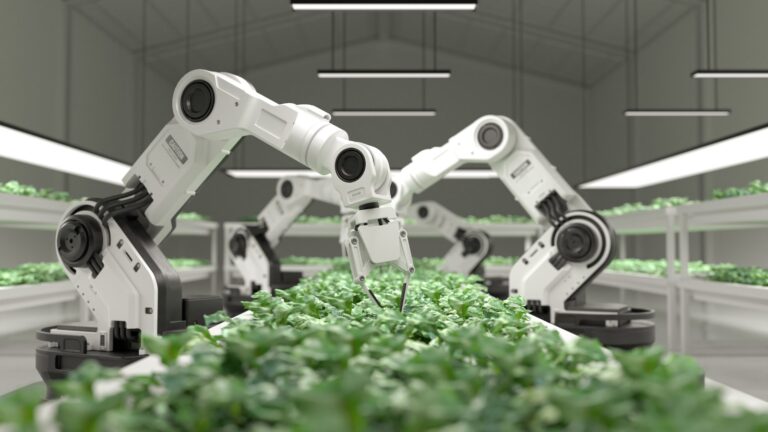
This article is prepared by Cerexio, a leading technology vendor that offers specialised solutions in the Advanced Manufacturing Technology Sector. The company is headquartered in Singapore and has offices even in Australia. Cerexio consists of a team of experts that have years of experience and hold detailed knowledge on a range of subject matters centric to the latest technologies offered in manufacturing and warehouse operations, as well as in predictive maintenance, digital twin, PLC & instrumentation setup, enterprise integrator, data analytics and total investment system.