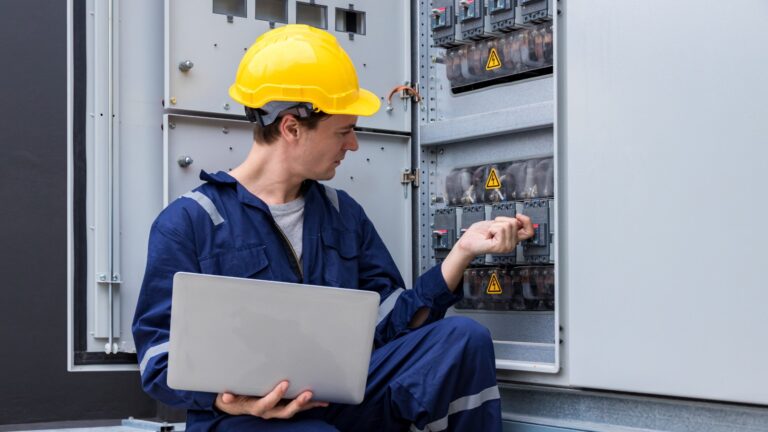
Supervisory Control and Data Acquisition (SCADA) and Manufacturing Execution System (MES) are two well-known software systems in the manufacturing industry. Many consider each to be similar or mutually exclusive. Hence, where a company have already adopted a SCADA, there could be a tendency to believe that an MES has nothing new to offer. However, in reality, not only are the two different from each other, but they are also complementary. They optimise a manufacturer’s operations more efficiently and put a company a step ahead of its competition. This blog will describe how an MES can improve a company that already has a SCADA integrated.
What is SCADA?
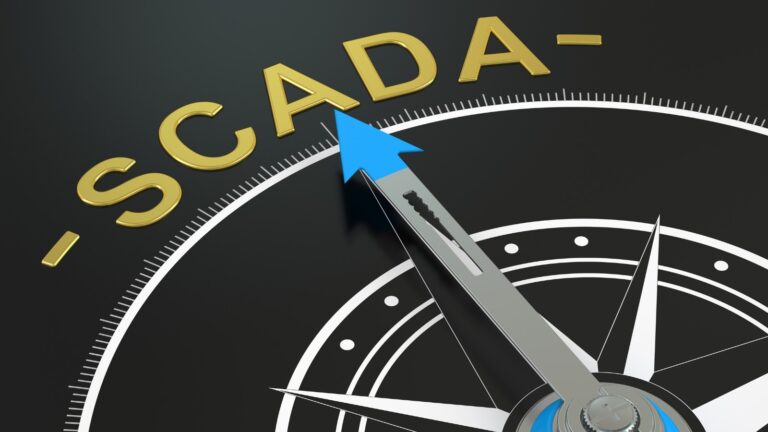
Simply put, SCADA handles automating the plant floor. It is a great application that can be used for any industrial process and includes software and hardware components. It uses sensors to gather real-time information on assets, allowing manufacturers to control assets remotely and notify managers of any dangers immediately. It primarily has a programmable logic controller (PLC) or remote terminal unit (RTU), which integrates all assets in a factory into one platform. While SCADA allows managers to acquire information on product quality and the effectiveness of the company operations, one drawback is that it does not track the detailed transformation of raw materials to finished goods. SCADA is primarily known, however, to be the best real-time visualisation tool to monitor processors.
Where Does MES Come into the Picture?
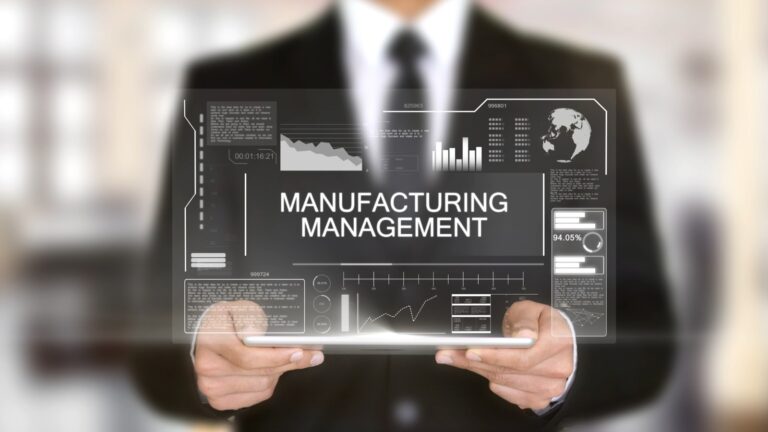
MES specialises in tracking and collecting information about each product in real-time. Unlike SCADA, which only stores, records and processes limited data in the production process, MES monitors all processes in all of their stages with excruciating detail. It is sometimes also considered as an intermediary between an ERP and SCADA. It focuses on streamlining functions related to production order, calculating the OEE and identifying the reasons for efficiency loss, measures actual production costs and has the predictive capability to detect anomalies and other events. It focuses on presenting aggregate data, which includes daily reports and is designed to work with data repositories such as historians and databases. Hence, an MES is far more important in handling big data in a manufacturing company.
Three Ways MES Can Help Your Factory Perform Better
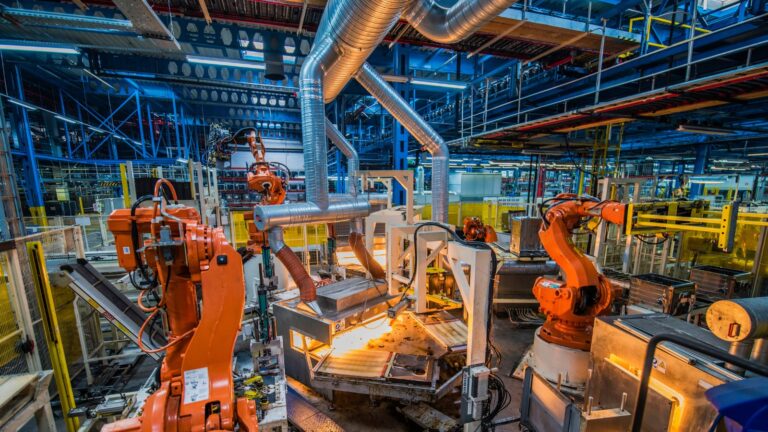
While SCADA can sometimes be very similar to MES, here are five ways MES uniquely contribute to a manufacturing plant floor.
Communication Speeds
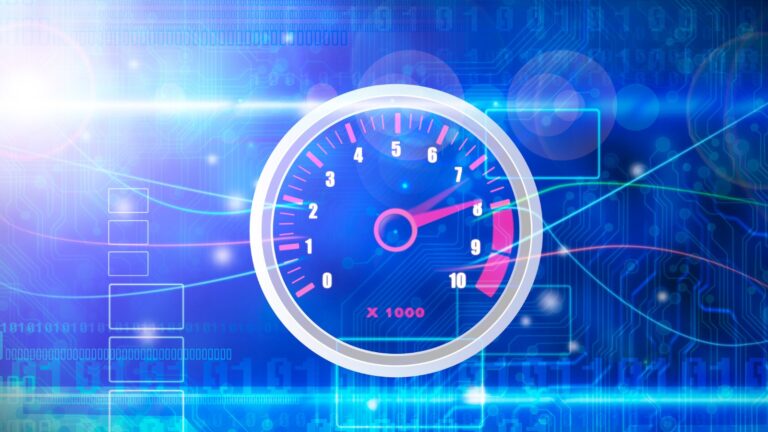
In a SCADA system, communication relies on daily and monthly transactions. In a MEs solution, however, the hourly and minute time frames are considered. Hence, while SCADA does a good job of assessing communication between processes, the MES solution does an even better job of focusing on every detail. Hence, even minute time frame events become important, making quality control, production scheduling and maintenance operations much more accurate and better. Considering that a manufacturing floor includes multiple transactions within an hour, with some estimating there to be a transaction every 4.5 seconds, around 300 to 800 transitions within 60 minutes are effectively monitored. This ensures that the functions within a factory are constantly updated, addressing the changes or updates required according to the different transactions that take place.
Offers Analytical Capabilities
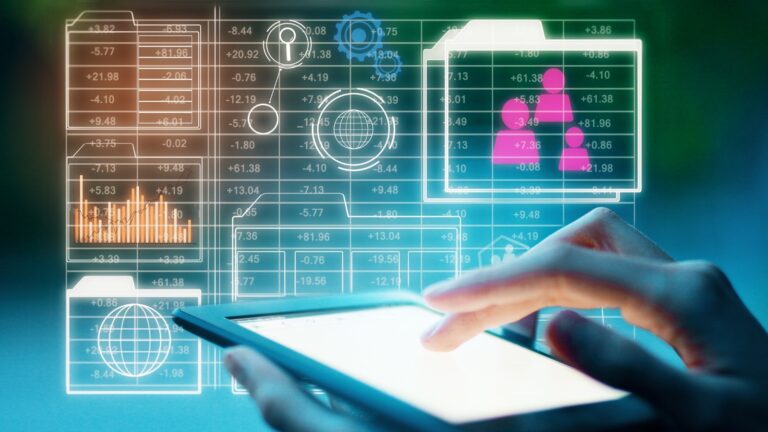
MES provides analytical capabilities into manufacturing operations allowing you to make smarter decisions. It does this by having real-time performing metrics such as OEE, which accurately carries out product and materials traceability to ensure strict regulatory requirements and quality standards are constantly in place. This guarantees power protocols are implemented to ensure quality assurance within the manufacturing factory premises. Since an MES ensures there all production plant processes are thoroughly connected, the data processed is analysed to offer the most reliable insights. It is also these capabilities that provide reliable futuristic insights into potential failures, breakdowns and errors which previously could not be made with a SCADA system as it failed to consider all the data accumulated across the entire manufacturing process.
Provides Higher Level Management
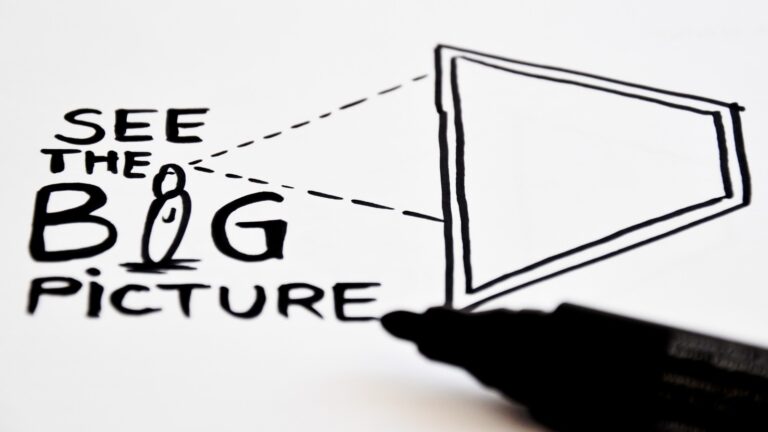
A SCADA only focuses on the end product. For example, if a person was to go on a trip, SCADA focuses on getting the person to their destination by offering vital safety information that is needed to drive there with no problem. However, being able to travel from one place to another is not enough. An MES solution will consider the overall picture: where you need to go, how you will get there, plan and schedule the stops you will take, schedule when your will be driving and ensure all the resources are available. It, therefore, plans, schedules, and optimises the production process, reducing production downtime and increasing the factory’s efficiency.
Cerexio MES: The Best MES to Integrate with Your SCADA System
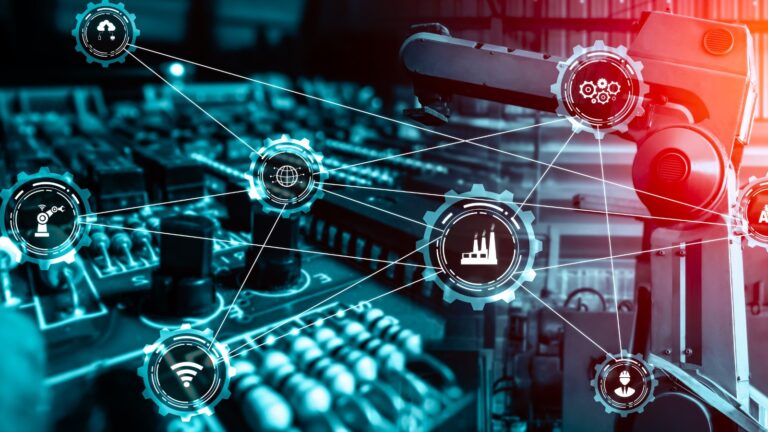
Cerexio MES is a globally recognised solution ranked the best in the Asian region. It is powered by a range of industry 4.0 technologies, including artificial intelligence, machine learning, predictive and prescriptive analytics, digital twin, and more. It offers end-to-end control of all of your manufacturing operations by interconnecting, advancing and automating factory processes using one digital platform. It offers reliable ways to track and trace everything, can seamlessly connect to other systems like ERP, can intelligently schedule maintenance, and is embedded with the best analytical tools that can accurately calculate your OEE rates.
Connect with Cerexio to learn how itS MES solution can enhance the visibility, performance and success of your manufacturing company when it is already integrated with SCADA.
Unlock Your True Potential With MES and SCADA Together
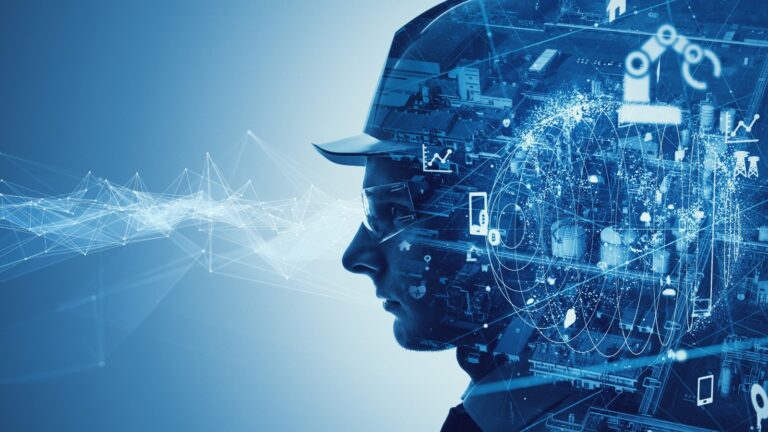
Two complementary systems can offer companies to gain a competitive edge in the manufacturing world when they are merged together. They enhance operational visibility by providing a comprehensive overview of the entire manufacturing process, influence managers to take better and more informed decisions, optimise manufacturing operations with little to no intervention by humans, and allow you to flexibly meet the changing needs of the market without wasting finances and resources.
This article is prepared by Cerexio, a leading technology vendor that offers specialised solutions in the Advanced Manufacturing Technology Sector. The company is headquartered in Singapore and has offices even in Australia. Cerexio consists of a team of experts that have years of experience and holds detailed knowledge on a range of subject matters centric to the latest technologies offered in manufacturing and warehouse operations, as well as in predictive maintenance, digital twin, PLC & instrumentation setup, enterprise integrator, data analytics and total investment system.