Gone are the days when the manufacturing world relied on manual work and tended to make more mistakes unintentionally. As the best solution to this matter, they have developed a technological concept known as ‘Industrial Automation’ where everything is automated and follows predefined workflows. However, the most challenging part of opting for industrial automation is deciding the most suitable type of automation for certain companies. Not everyone produces the same products or follows the same processes. Aligning with the production instructions and industry requirements is the number one concern when implementing automation. This is not as easy as it seems to be, as there are different types of industrial automation.
In this article, we explore the various types of industrial automation, expressing their uniqueness.
We will know
- Industrial Automation; What is It?
- Why are There Different Types of Industrial Automation?
- Key 4 Types of Industrial Automation
- Fixed Automation System
- Flexible Automation System
- Integrated Automation System
- Programmable Automation System
- Cerexio Solutions for Smooth Automation
- Automating the Production Floor for Better Results
Industrial Automation; What is It?
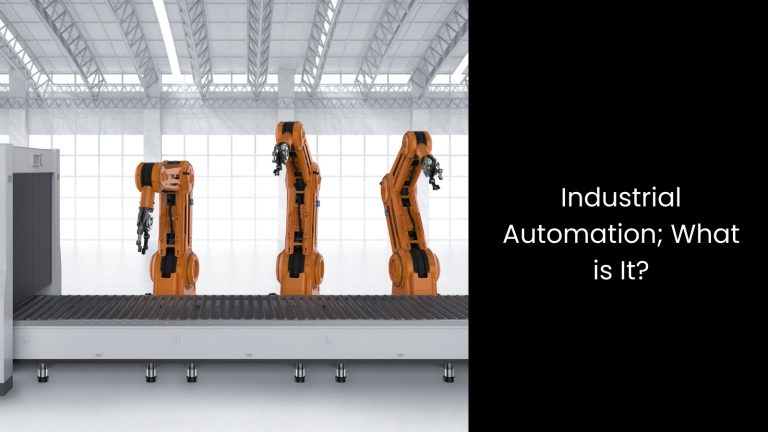
- This concept in manufacturing refers to the use of technology and machinery to perform tasks without human intervention.
- It is not as simple as it may seem. The latter is a whole network of processes, machinery, and technologies. If we elaborate on this a bit, it involves the integration of computers, sensors, and control systems to operate machinery and processes in factories.
- These automated systems can handle various tasks, such as assembly, packaging, and quality control, with precision and efficiency. As it is designed and developed to automate repetitive and labour-intensive tasks, industrial automation helps increase productivity on a larger scale. Not to mention that the latter improves product quality and reduces production costs without any human involvement.
- For instance, most organisations nowadays employ robots for automation. They can be programmed to perform tasks like welding or painting with consistency and accuracy, while automated conveyor belts can efficiently move materials between different stages of production.
- So, this whole network is all about streamlining processes, enhancing efficiency, and ensuring consistent output automatically.
Why are There Different Types of Industrial Automation?
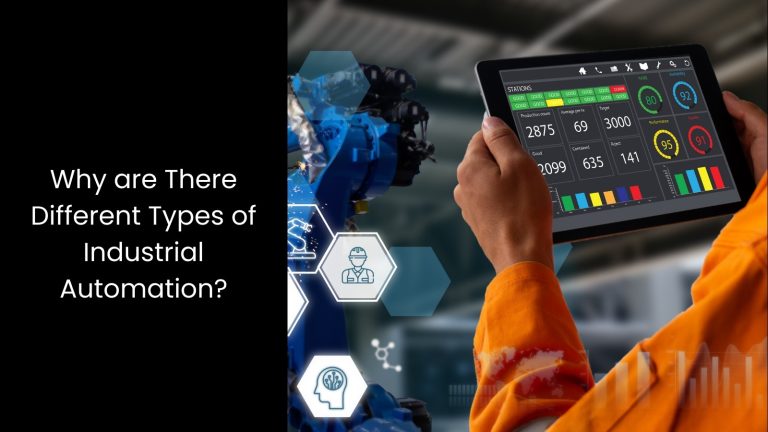
- Different types of industrial automation exist to cater to diverse manufacturing needs and requirements.
- You know that industries vary in terms of their products, production processes, and operational priorities. This will lead to the development of specialised automation solutions.
- Let us explain this a bit further. Some automotive manufacturing frameworks might require robotic arms for precise assembly, while food processing sectors need conveyor belts designed for hygiene and sanitation. Likewise, it is all about diversity in the industrial world.
- We should not forget that other factors like budget constraints, facility layout, and technological advancements also have some influence on the choice of automation systems.
- This is why industrial automation has a variety of types, substructures, shapes, and natures. It is up to the organisation to decide which type of industrial automation they will opt for.
Key 4 Types of Industrial Automation
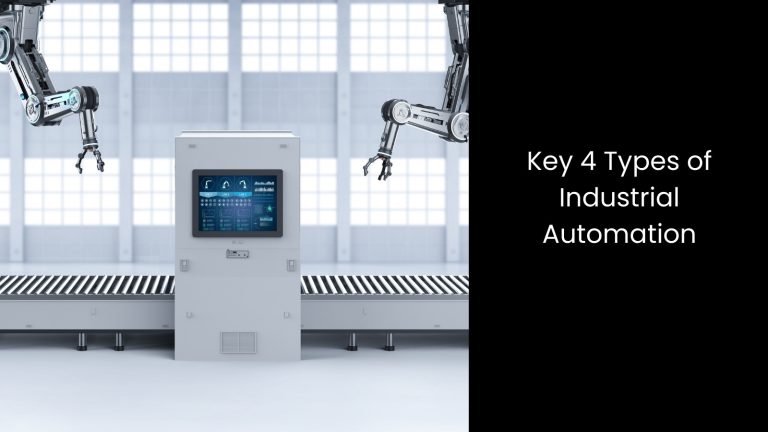
Fixed Automation System
This particular type of automation stands out as the most straightforward form of industrial automation.
If we take a look at its mechanism, it includes machines dedicated to specific tasks, set up permanently. Once a task is done, the machine resets itself, ready for the next one. That is the basic theory.
Which companies find this suitable? Industries that rely on repetitive tasks find fixed automation systems indispensable. If we take, for example, mass production factories where items like food move along conveyor belts, they undergo standardised processes.
The mechanism is clear-cut, as you can also see. Those machines carry out precise tasks repeatedly. They do not have to adapt to different tasks, staying locked into their designated functions.
It is also true that fixed automation lacks flexibility. However, it excels in high-volume production settings, ensuring consistent output. Its straightforward nature and reliability make it ideal for scenarios demanding repetitive tasks.
If a manufacturing company puts more weight on the requirement of minimising human intervention and streamlining processes, then fixed automation is the best fit.
Flexible Automation System
Flexible automation is full of capacity, as it is known as the pinnacle of industrial automation complexity.
Unlike fixed automation, where machines are locked into specific tasks, flexible automation systems offer versatility. These machines can not only perform a variety of tasks but also adapt to changing requirements.
Then what else can they fulfil? The best thing about them is that they are programmable and adjustable. This quality allows factories to swiftly alter their production lines and cater to a broader range of products.
You know that those industries dealing with diverse product lines are desperately in need of such flexible automation. Take, for example, manufacturing plants where products vary significantly from one to the next. Here, machines need the ability to quickly switch tasks and configurations to accommodate different product specifications.
The mechanism behind flexible automation ranges from sophisticated programming to control systems that allow machines to seamlessly transition between tasks to adjust their operations as needed. Despite their complexity, flexible automation systems empower factories to respond rapidly to market demands and so on.
Integrated Automation System
This specific type stands as the epitome of industrial automation sophistication. Do you know why?
Unlike other types, where machines operate independently, They operate in an integrated automation system; all machines are linked to a central computer.
In a way, it is a centralised control that allows factories to oversee every aspect of production from one location. However, this is particularly suited for industries with small batch production and frequent line changes.
The integrated automation enables swift and effortless modifications to the manufacturing process. Its core mechanism involves the seamless connection of various components like CAD, CAM, computers, machinery, operators, robots, and cranes through a single interface.
This unified control interface paves the way for manufacturers to schedule and manage production. It is evident that it streamlines operations and enhances efficiency to a notable extent.
Since the latter has the ability to integrate diverse processes under one system, factories can achieve greater coordination, faster response times, and improved productivity. This comprehensive approach to automation empowers manufacturers to adapt quickly to market demands and optimise resource utilisation to the maximum level.
Programmable Automation System
This is another main type of industrial automation. Programmable automation serves as a step up in complexity from fixed automation, offering enhanced versatility.
The uniqueness of this framework lies in its powers. Within a programmable automation system, machines are not restricted to singular tasks. Did you know this?
Instead, they can be programmed to execute a range of functions. This adaptability is what allows factories to diversify their product lines, as the sequence of operations and machine functions can be adjusted as needed.
Not every production line can rely on this. There are certain industries where production requirements fluctuate from batch to batch, and programmable automation is the right choice for sure. The mechanism behind this system involves programming machines to follow specific instructions, allowing for flexibility in task execution.
As you can see, by enabling rapid reconfiguration of operations, programmable automation systems facilitate the efficient production of varied products. This flexibility in task execution empowers manufacturers to bridge the gap between fixed automation’s rigidity and flexible automation’s adaptability, offering a balanced approach to industrial automation suited for industries with diverse production needs.
Cerexio Solutions for Smooth Automation
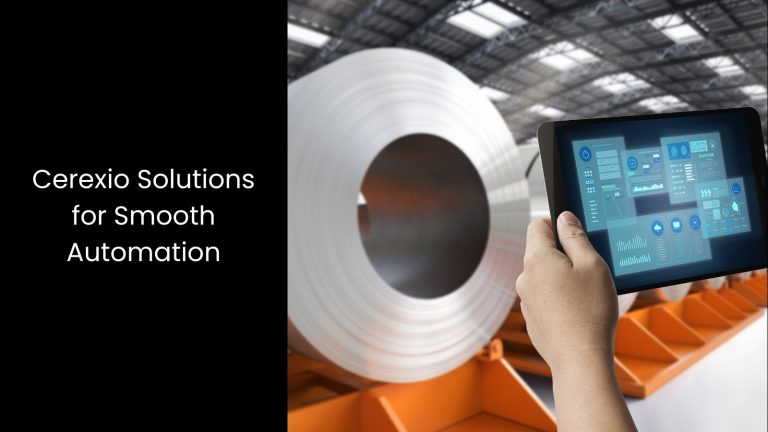
In a complex industrial world, Cerexio offers a diverse range of sophisticated software solutions to fill the gaps in traditional processes with a focus on profitability, sustainability, and efficiency. From its MES, Energy Management Platform, and Air Management System to its Track & Trace System, etc., Cerexio technologies are being consolidated to offer manufacturing excellence with ease via industrial automation.
Automating the Production Floor for Better Results
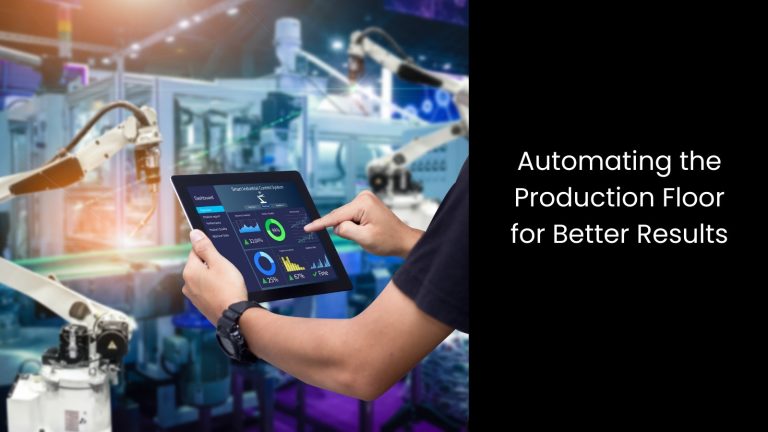
It is not necessary in this dynamic industrial world to completely rely on human labour. If a major portion of manufacturing work can be transferred to machines, there will be a significant increase in productivity and efficiency. With the right strategies in place, the production floor can be a smart world.