Are you seeking new ways to automate your manufacturing production process and multiply your efficiency? Then the answer lies in the new technology. The manufacturing environment is being transformed by the digitalisation of plant processes employing programmable logic controllers or PLC and instrumentation sets over the years. Factory automation can unleash new levels of efficiency, accuracy, and flexibility by seamlessly integrating sophisticated technologies and intelligent systems. This transformation enables enterprises to streamline operations, improve product quality, and respond to market needs more quickly.
In this article, we will explore how factories can achieve digitization utilising PLC and instrumentation setup in the manufacturing business context.
What is PLC and Instrumentation Set Up?
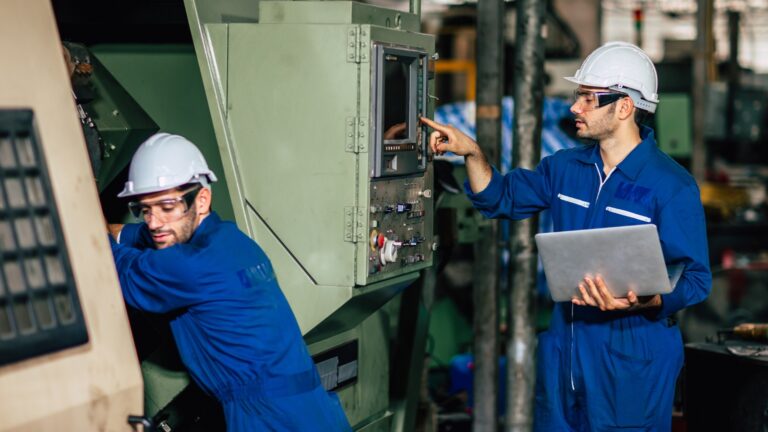
All control devices in a standard industrial control system are linked directly to each other based on how the system is designed to work. However, with a PLC system, it replaces the wire connecting the devices. They’re strong enough to adapt to a variety of contexts and activities, yet sufficiently straightforward that even technicians with no prior programming or scripting experience can grasp them fast. PLCs have unique characteristics that make them the favoured choice for sectors that rely on these systems.
In the factories of the manufacturing industry, this technology is used to monitor and automate their manufacturing operations. These are industrial computers that are built to endure the harsh conditions of an industrial setting. With more businesses wanting to automate their manufacturing processes, the increase of data-driven decision-making, and growing IIoT and machine learning applications, the importance of PLCs in Manufacturing is becoming more significant.
Key Ways to Optimise Digitisation in Manufacturing with PLC
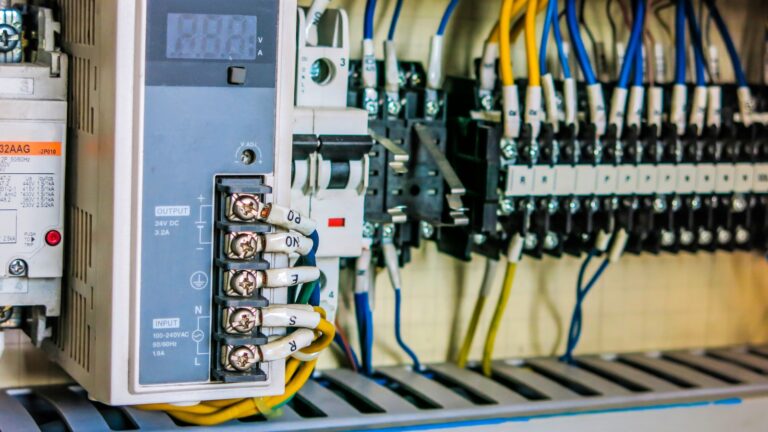
Process Mapping in Depth
Comprehensive process mapping, or mapping out your production processes in depth, is an effective technique for improving digitalization with PLCs. This strategy entails drawing a detailed depiction of how your manufacturing steps run. This allows you to determine exactly where and how the technology can be utilised successfully.
It aids in the identification of potential areas for automation, data collecting, and process control. This mapping directs the strategic placement of PLCs, ensuring that they are integrated precisely where they will have the greatest impact. Factories create a solid basis for employing this to simplify operations, decrease mistakes, and maximise efficiency across the manufacturing journey with a well-mapped strategy.
Strategic Asset Integration
This is a critical approach for increasing digitalization in PLC-based production. It entails intelligently integrating the technology into the factory’s architecture. By properly positioning and connecting the latter, which to critical equipment and machinery, factories can create a strong network capable of controlling and monitoring these assets. This interface enables the gathering of real-time data, remote monitoring, and automatic modifications.
This becomes the brain that controls manufacturing production operations. This method converts the factory into a more responsive, agile, and optimised manufacturing environment.
Data Collection in Real Time
This entails gathering real-time data from sensors and devices strategically positioned throughout the manufacturing process. It captures and sends data in real-time, giving authorities a clear picture of what’s going on at every stage. With this real-time data, administrators can spot faults fast, monitor performance, and make swift choices.
By incorporating real-time data capture via PLCs, it is possible to enable the factory to respond quickly to changes, improve operations, and assure high-quality output. It’s like keeping a continual eye on the production activities to ensure efficiency and performance.
Data Analytics for Better Insights
The latter involves the use of data acquired by sensors and equipment and processed and evaluated by PLCs. Factory managers can discover important patterns, trends, and performance measures by analysing this data. These insights provide a more in-depth understanding of the manufacturing processes, helping them to find areas for improvement, streamline workflows, and make more educated decisions.
Data analytics gives them the ability to fix inefficiencies, minimise waste, and increase overall production. They can turn raw data into actionable knowledge by leveraging the analytical power of this technology, directing their production toward smarter, more efficient, and higher-quality manufacturing outputs.
Predictive Maintenance Techniques
Sensors and instruments are used in these solutions to monitor equipment characteristics and performance in real-time via this technology. Patterns of wear and possible difficulties can be recognized early by examining this data, allowing for preventative maintenance before failures occur. This lowers unnecessary downtime, and production interruptions, and increases the longevity of machines.
Predictive maintenance improves efficiency by eliminating needless maintenance and increasing operational uptime. It also improves resource allocation by concentrating efforts on equipment that genuinely need care.
Remote Monitoring and Control
Using these modern controllers, industrial workers and managers could remotely monitor and supervise production operations. It allows for real-time data collecting that can be viewed remotely, allowing decision-makers to monitor operations, discover problems, and make modifications without having to physically be present on the factory floor.
This remote capacity boosts efficiency, shortens problem reaction times, and improves overall production management. It also allows for quicker interventions, which reduces downtime and ensures smooth operations.
Quality Assurance Enhancement
Quality assurance enhancement is critical in maximising factory digitalisation with the usage of this system. Manufacturers can guarantee constant and excellent product quality by including these controls in the manufacturing process. The latter allows for real-time monitoring of numerous factors during manufacturing, such as measurements and tolerances.
This data is evaluated, and if any abnormalities are identified, rapid changes or alarms can be issued to prevent faulty items from proceeding further. This strategy lowers mistakes, and waste, and improves overall product reliability.
Increasing Energy Efficiency
The technology aids in energy conservation by accurately managing equipment operations and resource utilisation. These controllers provide automatic process modifications based on real-time data, ensuring that machinery functions effectively and without wasting energy. It makes smart choices to reduce energy waste by monitoring elements such as power use, temperature, and manufacturing demand.
The resulting optimization not only lowers operational expenses but also helps to ensure environmental sustainability by cutting carbon emissions. Manufacturers can accomplish significant energy savings, integrate with eco-friendly practices, and contribute to a better future while maintaining effective production levels using Energy Efficiency Optimization via PLCs. It’s an effective way to boost profits while being mindful of the environment.
Integration with ERP Systems
PLCs are able to interact with ERP software in real-time, enabling real-time data interchange between the factory floor and business operations. This connection allows for improved production planning, more precise inventory management, and more efficient communication across departments. Production rates, material use, and quality data can all be sent into the ERP system automatically, improving decision-making and resource allocation.
Manufacturers receive a comprehensive perspective of their whole operation by merging this with ERP systems, resulting in better productivity, decreased bottlenecks, and informed strategic decisions.
Cerexio PLC and Instrumentation Set Up
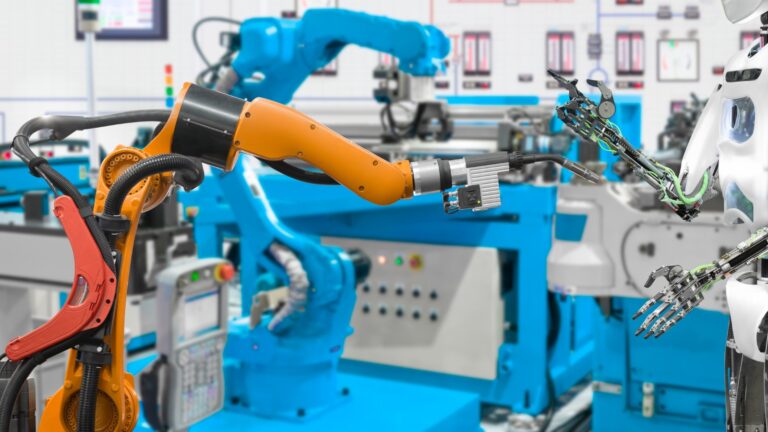
Is it a struggle for you to overcome manufacturing challenges? Automation and hyperconnectivity platforms are the ideal answer for this. Cerexio’s professional Instrumentation & PLCs ability is ready to help you with planning, setting up, and commissioning your full automation system depending on your company’s particular production needs. Cerexio can configure devices from a variety of instrument manufacturers, and we offer the finest guidance and support for designing your PLC and instrumentation connections with the best technology and the smartest devices. Also, our technology provides a plethora of software systems with numerous modules that fit your company’s current production demands.
Business Growth is Just One Step Away Once You Hold Hands with Technology
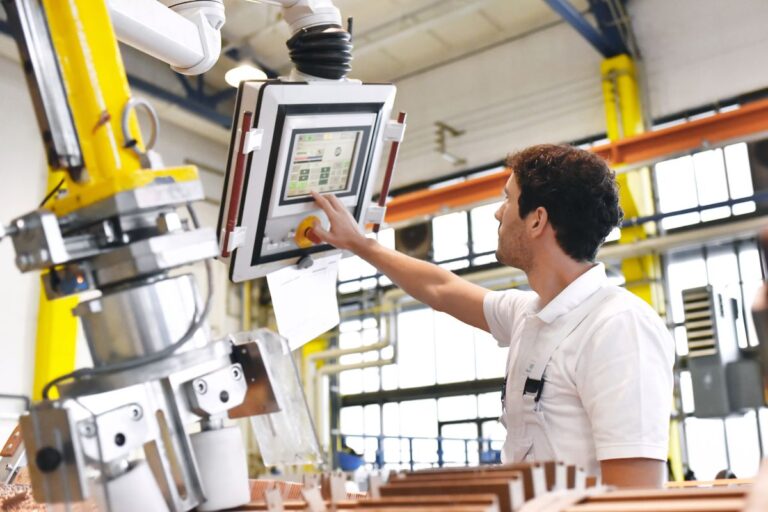
If you are thinking of new ways to step away from traditional methods and move on to opting for new technology for your factory operations, it is high time to get into action. With the implementation of modern technology, your businesses will see new horizons within a short time for sure. So, don’t hesitate to go for the best partner when purchasing the ideal software solutions.