Are you aware that most sheet metal manufacturers still rely on outdated methods? However, this journey has faced challenges as age-old methods lead to inefficiencies, high error rates, and wasted materials. It is hard to say that approach cannot match the competition out there. Luckily, technology has stepped in to turn the tide. From CNC machining to laser cutting and automation, innovative tools redefine how manufacturers approach production. As the sheet metal manufacturing industry continues to grow, embracing these tools is not just another approach; it is the best path they can walk on.
In this article, we cover everything about the advantages of utilising technology in sheet metal manufacturing.
We will discover
- What is Sheet Metal Manufacturing?
- Challenges Faced in the Process of Sheet Metal Manufacturing
- Top 5 Advantages of Utilising Technology in Sheet Metal Manufacturing
- Cerexio Industry 4.0 Powered MES for Sheet Metal Manufacturing Industry
- Keeping Sheet Metal Manufacturing Process on Point Utilising Roust Tech
What is Sheet Metal Manufacturing?
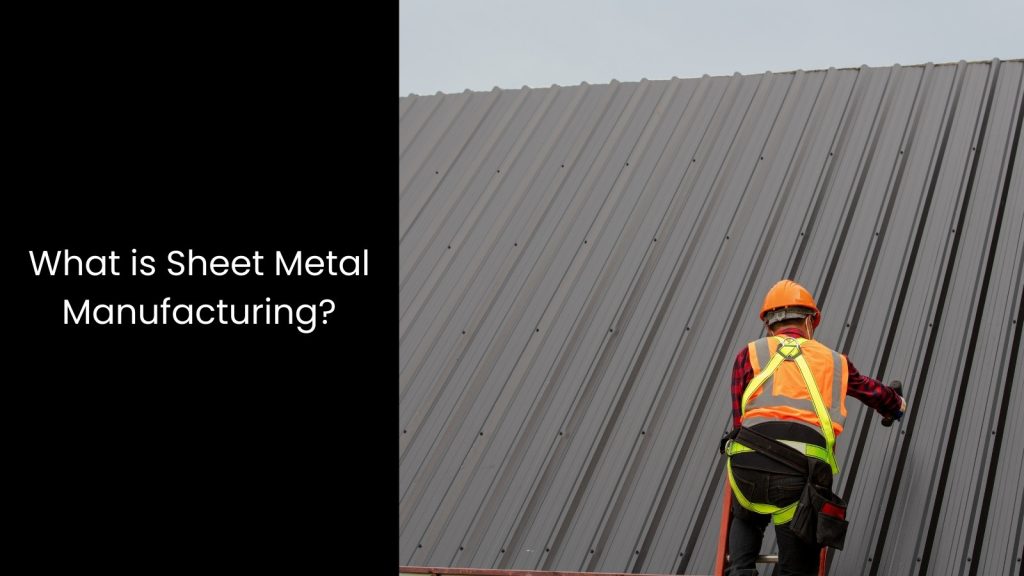
- Sheet metal manufacturing is a domain where the process transforms flat sheet metal into various shapes and products through cutting, bending, and forming processes.
- This indicates that it involves the creation of metal products by shaping thin, flat pieces of metal into various forms and sizes. These sheets are typically made from materials like steel, aluminium, or copper, which are processed through techniques such as cutting, bending, and stamping.
- The process starts with large metal coils, which are then transformed into sheets by rolling them.
- In today’s world, manufacturers prefer to use advanced equipment, including CNC machines and laser cutting tools, to precisely shape and form these sheets into components for various industries, from automotive to aerospace.
- This specific industry focuses on creating high-quality, durable products with minimal waste, ensuring efficiency and precision in production.
Challenges Faced in the Process of Sheet Metal Manufacturing
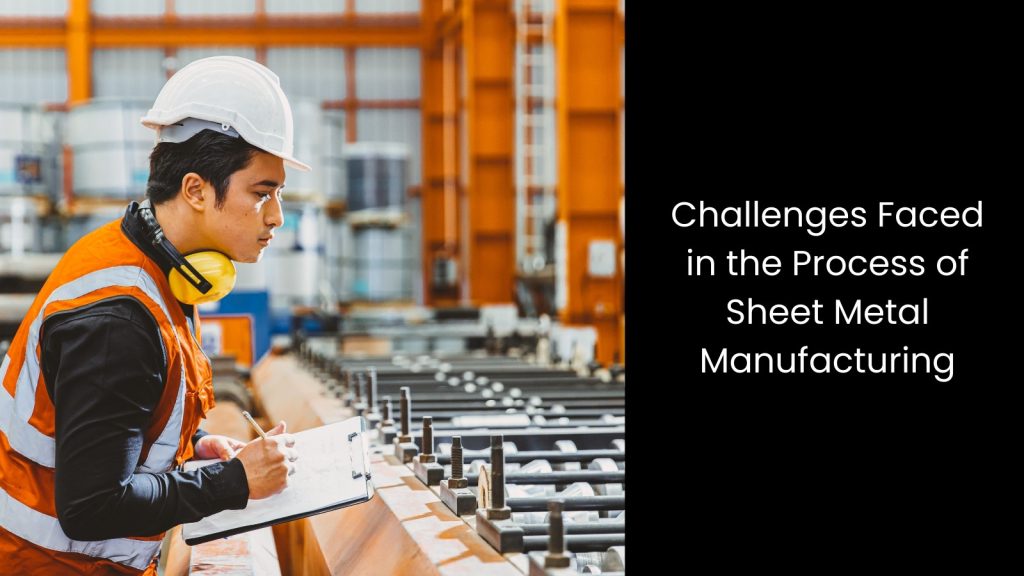
- Differences in sheet metal thickness, hardness, and composition affect consistency and precision in manufacturing.
- It is difficult to achieve accurate angles as, during bending, the material tends to revert to its original shape.
- Continuous use of tools like dies and cutters leads to wear, reducing their effectiveness and precision.
- Processes like laser cutting and welding generate heat, which can cause warping or distortion in the sheet metal.
- Scratches, dents, or oxidation during handling and storage impact the final product’s quality.
- Forming intricate shapes or tight tolerances requires advanced machinery and careful planning.
- Misalignment during cutting or bending leads to inaccurate parts, increasing wastage.
- Incorporating automated systems requires precise calibration and can face compatibility issues with existing setups.
Top 5 Advantages of Utilising Technology in Sheet Metal Manufacturing
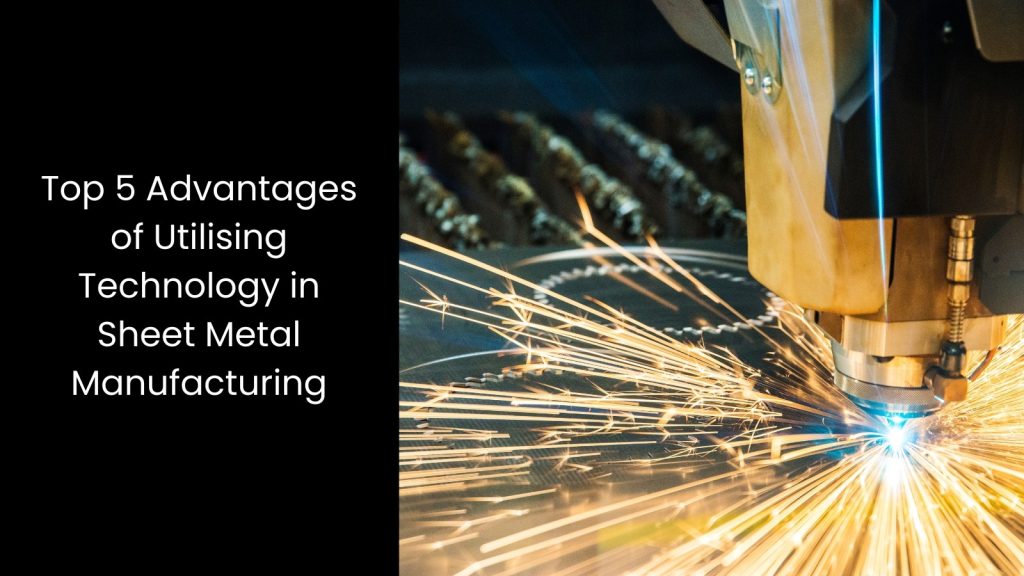
High Levels of Design Flexibility
Technology gives the sheet metal manufacturing industry an unmatched ability to achieve high levels of design flexibility. This makes it easier to meet unique customer demands.
For example, CAD software and 3D modelling tools allow manufacturers to create complex designs, offering more customisation options easily. When we look back at traditional setups, we can see they lacked this precision, as manual draughting and basic machinery limited possibilities, leading to errors and wasted materials.
Advanced tools now let designers visualise and modify intricate shapes in real time, ensuring perfect alignment with project specifications. Machines like CNC equipment take these digital designs and produce them with exceptional accuracy, removing the guesswork.
This shift also reduces lead times, helping manufacturers deliver products faster while maintaining quality. The best part is complex components for industries like aerospace, automotive, and electronics benefit from these innovations.
High Precision
Precision and accuracy are the number one requirements in any manufacturing process, let alone sheet metal manufacturing, where even minor errors can lead to defects and material waste.
Advanced technologies like CNC machining and laser cutting provide high levels of accuracy, ensuring precise dimensions and reduced material wastage.
You know that those traditional methods relied heavily on manual operations, which resulted in inconsistent results and human errors. Workers faced challenges maintaining uniformity, especially for intricate designs or tight tolerances.
But when it comes to modern tools, they eliminate these issues by automating cutting, shaping, and bending with unmatched precision. Laser cutting offers clean edges, while CNC machines execute detailed designs consistently. These advancements also optimise material usage, minimising scrap and decreasing production costs.
Manufacturers in the aerospace, automotive, and construction industries rely on these technologies to produce high-quality components that meet stringent standards.
Fewer Environmental Impacts
It is sort of a tough responsibility that sheet metal manufacturers have to balance production efficiency with environmental care. Traditional methods usually waste materials and consume excessive energy, making it hard to stay eco-friendly.
This is where modern manufacturing technologies came into the spotlight, and they are now tackling these issues effectively. These efficient technologies lower energy consumption, reduce waste, and promote sustainable manufacturing practices. Not to forget that machines like automated cutters and advanced stamping systems use precise measurements to minimise scrap, while energy-efficient equipment reduces power usage during production.
These innovations in recycling allow manufacturers to repurpose leftover materials into new products, further cutting waste. It is not a secret that those traditional setups lacked this ability, with manual operations often generating inconsistent cuts and excessive material loss. However, such new approaches prioritise sustainability without compromising on quality.
Manufacturers using advanced sheet metal processing tools help protect resources and support cleaner production. These innovations make the sheet metal industry smarter, greener, and better prepared for the future.
Safety Enhancement
Gone are the days when sheet metal manufacturing relied on manual labour for risky tasks like cutting, welding, and shaping heavy materials.
Do you remember the era when traditional setups exposed workers to sharp edges, extreme heat, and mechanical hazards? It clearly leads to frequent injuries.
Automation changes this landscape entirely. It reduces the need for human involvement in hazardous operations, minimising workplace injuries and improving safety conditions. In another way, robots and programmable machines now handle tasks with high precision, eliminating direct contact with dangerous equipment.
Similarly, technologies like motion sensors and safety interlocks add another layer of protection, shutting down operations when anomalies occur. Sheet metal fabrication systems equipped with smart controls monitor processes in real time, ensuring smooth and safe operations.
Training workers to manage these advanced systems shifts their roles to supervision rather than direct engagement, reducing risks significantly. This transformation allows the sheet metal production industry to enhance safety while maintaining efficiency, benefiting both employees and manufacturers.
Cost Reduction
Cost was the most uncertain thing in sheet metal manufacturing, as traditional methods usually involved material waste, high labour expenses, and frequent production errors.
The truth is manual processes lacked precision, leading to costly rework and inefficient resource usage. This is when technology completely changes this scenario.
It minimises errors, optimises material usage, and reduces labour costs, contributing to overall cost savings in manufacturing. Advanced tools like automated cutting machines ensure materials are used efficiently, leaving minimal scrap. As mentioned above, robotics and programmable systems take over repetitive tasks, cutting down on labour-intensive operations and freeing up skilled workers for more strategic roles.
On the other hand, real-time monitoring systems improve efficiency and detect issues early, reducing downtime and repair costs. Digital solutions in sheet metal fabrication also streamline inventory management, preventing overstocking or underutilisation.
As you can see, these are just a few ways this domain can cut costs.
Cerexio Industry 4.0 Powered MES for Sheet Metal Manufacturing Industry
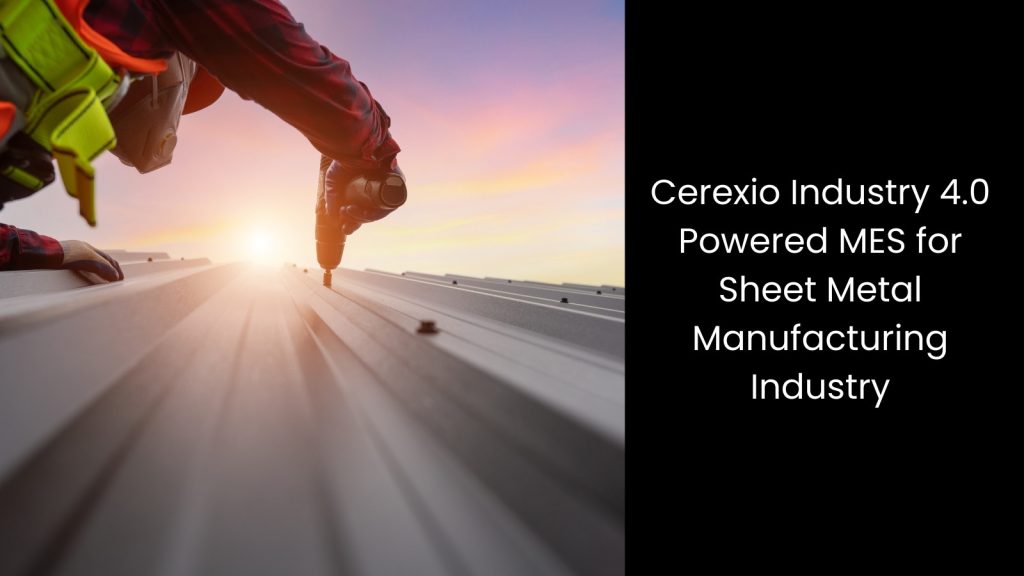
Cerexio Industry 4.0-Powered MES transforms the sheet metal manufacturing industry as it can enable real-time monitoring, predictive maintenance, and workflow automation. This solution is the best way to enhance production efficiency, minimise material waste, and ensure consistent quality in the long run. Its embossed strengths, such as advanced analytics and IoT integrations, empower sheet metal manufacturers to optimise operations smoothly.
Keeping Sheet Metal Manufacturing Process on Point Utilising Robust Tech
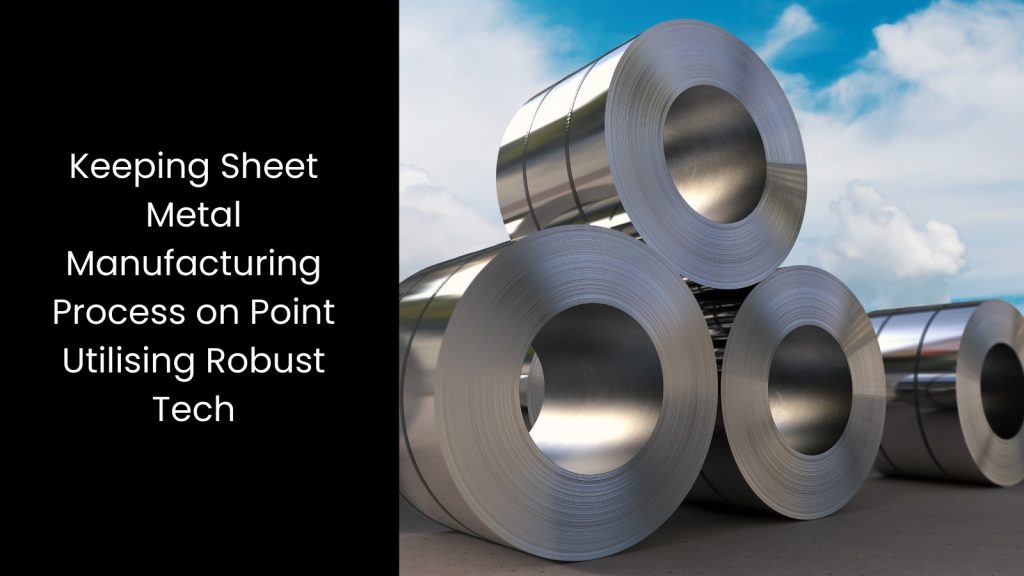
You must agree with the fact that the power of technology in sheet metal manufacturing is undeniable! From automation to real-time tracking, the tech advancements available today ensure smoother processes and superior results. As the whole sheet metal manufacturing domain continues advancing, there is no limit to the efficiency and quality it can achieve via robust technology.