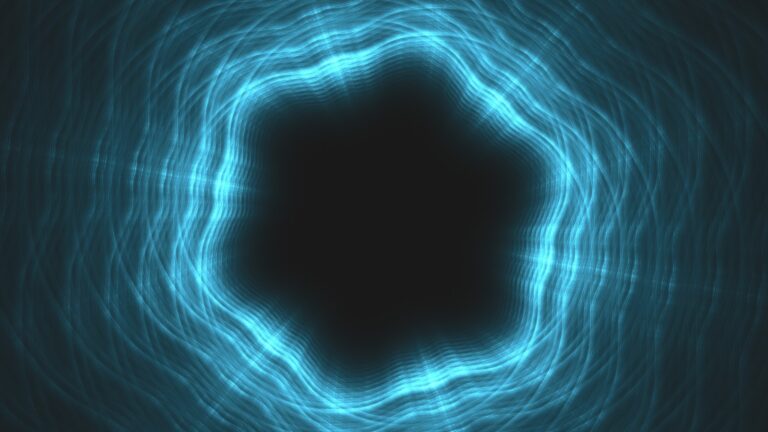
Vibrational analysis refers to a method used to monitor the equipment’s condition. As indicated by its term, it specifically studies the different vibrational patterns of machines, allowing managers to discover potential issues where the vibrations are abnormal. Since almost every asset vibrates in operation, it is a useful form of data to identify changes in a machine’s behaviour. Hence, a typical maintenance solution adopts vibrational analysis to identify and predict future anomalies and breakdowns in advance, allowing managers to take preventive measures. This blog will explain the relationship between vibrational analysis and predictive maintenance.
Why is Vibrational Analysis Integral to Predictive Maintenance?
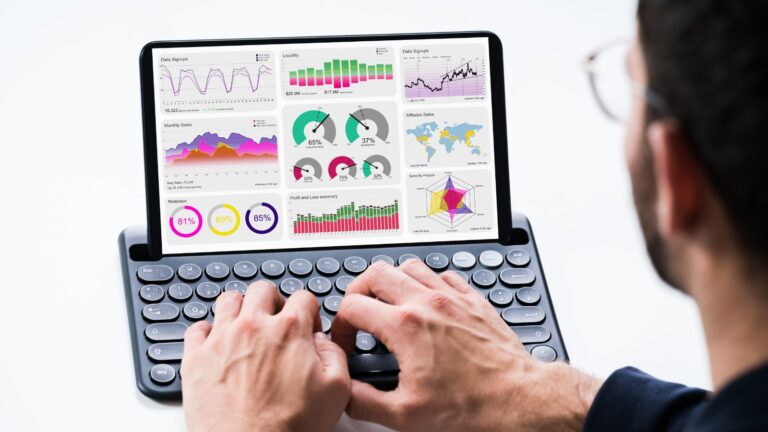
Assets with discrete rotating parts make it hard for manufacturers in a traditional setting to detect anomalies. Hence, under manual processes, the manager will only understand that something is wrong when the issue becomes more serious and obvious. Having vibrational analysis, however, can help detect problems as fast as possible. Instead of identifying a specific asset to have an anomaly when vibrations are audible to the human ear, assessing vibrational changes allows managers to detect even the most slight changes. As a result, whenever the rotating equipment and its components begin to wear, the vibrational analysis tool will be able to identify that something is wrong. Failure to take practical steps only means the products using such assets lack quality and accuracy. Thus, detecting vibrational changes much later could produce enormous waste, unnecessarily having to bear losses and even extending deadlines of a manufacturing project. All of this heightens the need to ensure an effective system is in place to monitor the vibrations of assets.
How Does Vibrational Analysis Work?
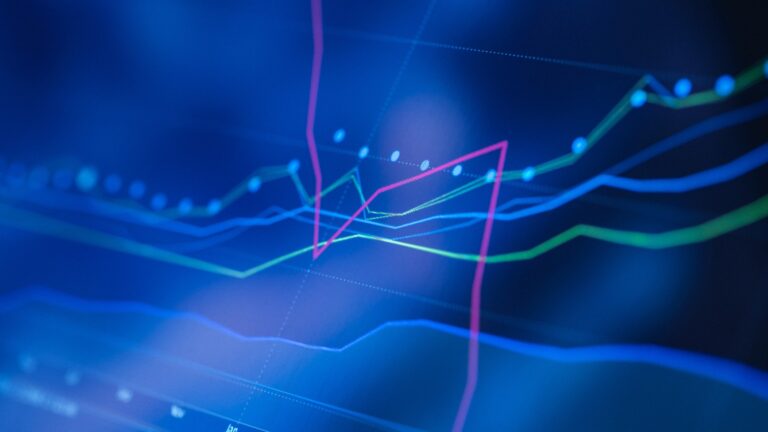
Vibrational analysis monitors the vibrational frequencies by studying the displacement, velocity and acceleration of rotating equipment. This includes fans, rotors, bearings, belts, shafts, and others. While Displacement studies the interval of vibration peaks, recording them in a wave part or frequency measure, Velocity considers the time taken for the component to move. Acceleration takes into account the former two vectors to assess other forms of analysis, including dynamic fault analysis. Hence, the combined effect of the three levels has the capacity to find fault in assets at every level.
There are four steps in a typical predictive maintenance system that have incorporated vibrational analysis. This includes the data collection phase whereby industrial Internet of Thing sensors specialising in monitoring vibrations are implemented to collect vibrational data remotely. Next, the data collected establishes a baseline to compare data from other machines. In other words, the system can identify what vibrations are ‘normal’ for each machine since vibrations differ from asset to asset. The third step is to store the vibration data to compare the historical data with future data. Lastly, in the analysis stage, each new piece of data collected is compared with the baseline to identify vibration levels, anomalies and defects. Where a fault is detected, no matter how small it is, it is communicated to the manager, who will schedule maintenance. This demonstrates how vibrational analysis allows managers to find issues and understand assets in their starting stages.
Advantages of Using Vibrational Analysis as a Predictive Technological Tool
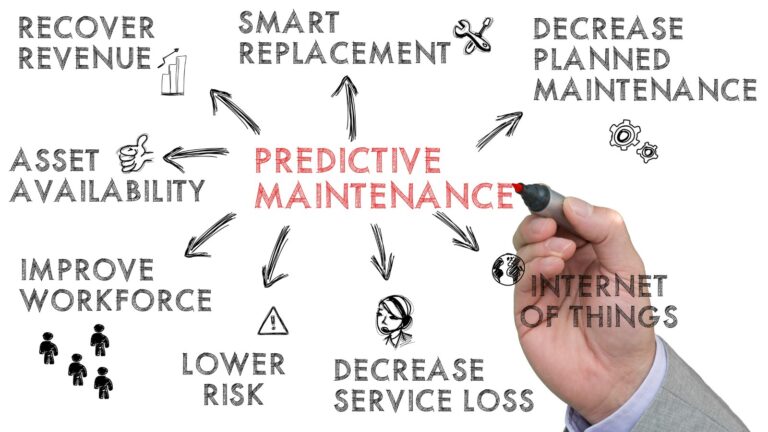
While the most obvious advantage is the ability for the manufacturer to detect anomalies in advance, there are multiple other benefits a company can enjoy with this cost-effective tool:
- Remote Accessibility: Sensors used for vibrational analysis are small and are a one-time instalment in manufacturing factories. They automate collecting data on asset health and allow managers to monitor them from anywhere, even when not they are not physically present on the production floor. When an anomaly is detected, it instantly dispatches a warning notification to the managers through a virtual screen without the manager having to keep an eye out constantly.
- Increase the Lifecycle of Assets: Every time a vibrational change is detected, manufacturers can rectify the issue by doing minor corrective maintenance at minimal costs. Hence, whenever an anomaly is addressed at the very start, it completely allows the asset to function as if no anomaly was ever present, thus, strengthening the asset’s lifecycle.
- Implements a Safe Working Environment: Certain machines that undergo issues make the factory hazardous for humans. Hence, by detecting anomalies at the very start, the system can assess how worse it would be and address it accordingly. Sometimes a predictive maintenance system could automatically restrict people from entering a specific area in the factory. This ensures that the human staff does accidentally enter or is put at risk in the factory.
- Guarantee Quality End-Products: An end product have a high probability of not having defects whenever all the assets in a manufacturing factory are working in optimal condition. Hence, as managers receive detailed insights into the performance of each asset, it ensures the machine remains consistent in producing materials, thereby eliminating situations where quality is hindered.
- Offers Targeted Maintenance: With vibrational analysis, manufacturers do not have to go in blind. Instead, the system will highlight and demarcate which component within the asset, for instance, is experiencing a different vibrational pattern. Hence, maintenance teams can instantly address the root cause of the problem and provide targeted maintenance instead of wasting time figuring out which aspect of the asset requires repairs.
Cerexio Predictive Maintenance: Goes Beyond Vibrational Analysis
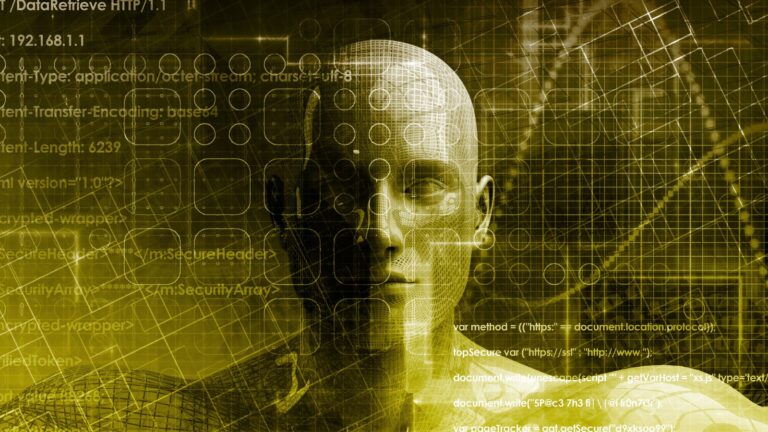
Cerexio Predictive Maintenance is a future-proof solution suite that embraces vibrational analysis and other advanced technologies. As a specialised digital vendor in the manufacturing industry, Cerexio understands the intricate components of industrial assets, making it hard for manufacturers to maintain their assets and ensure their life cycle is not greatly depreciated. It, therefore, infuses industry 4.0 technologies such as AI, ML, digital twin, IIoT and others, all of which significantly contribute to creating a robust predictive maintenance system. As a result, Cerexio considers not only vibrational patterns but other useful information, such as asset temperatures and other variables, in detecting asset anomalies. It has proven to reduce maintenance costs, improve asset network reliability and accurately break down future asset failures. It can, moreover, selectively implement analytical comparisons of your organisation to assess the company’s profit by considering the performability, reliability and functional metrics of assets.
Connect with Cerexio to comprehensively understand how it can ensure your assets remain in brand-new conditions for years ahead.
Vibrational Analysis is a Much Needed Companant in Predictive Maintenance
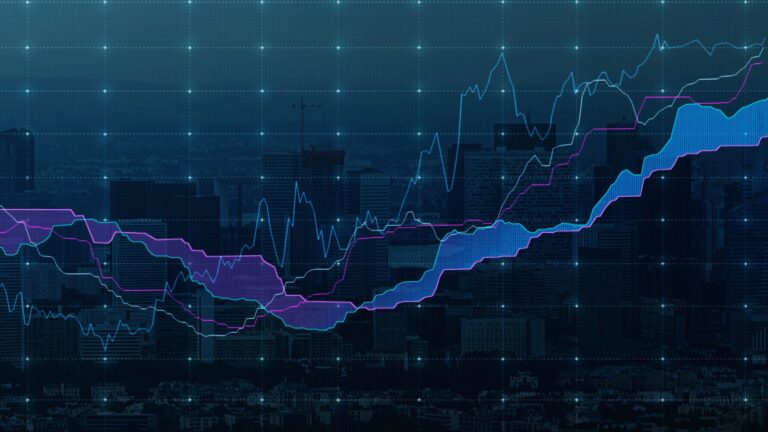
Vibrational analysis monitors and detects a range of problems, including when a component in an asset is misaligned, has operational issues, has gear defects, bent shafts, loose bolts and more. Manufacturers can easily avoid serious equipment failure by detecting such issues the moment they occur. Hence, when investing in a predictive maintenance system, considering whether vibrational analytics is a key feature is a good way to ascertain if you can effectively eliminate anomalies in the long term and guarantee that the lifecycle of your assets is strengthened. In this respect, ensuring your predictive maintenance system is not limited to vibrational analysis is important if you are looking to stay ahead of any kind of potential threats that your manufacturing company can face in the foreseeable future.
This article is prepared by Cerexio, a leading technology vendor that offers specialised solutions in the Advanced Manufacturing Technology Sector. The company is headquartered in Singapore and has offices even in Australia. Cerexio consists of a team of experts that have years of experience and holds detailed knowledge on a range of subject matters centric to the latest technologies offered in manufacturing and warehouse operations, as well as in predictive maintenance, digital twin, PLC & instrumentation setup, enterprise integrator, data analytics and total investment system.