Are you seeking new and innovative ways to provide answers for the challenges you encounter in different levels of manufacturing business? This is a complex set of processes that vary from production and packaging to supply chain, delivery, etc. How can you handle those various interwoven chains without compromising much time and money? The answer lies in the hands of ‘Event-Driven Architecture’ technology.
What exactly is this software solution? How can it offer the answers to certain obstacles through its robust features and functionalities? Let us explain everything in our latest blog article.
Introducing 'Event-Driven Architecture' Technology
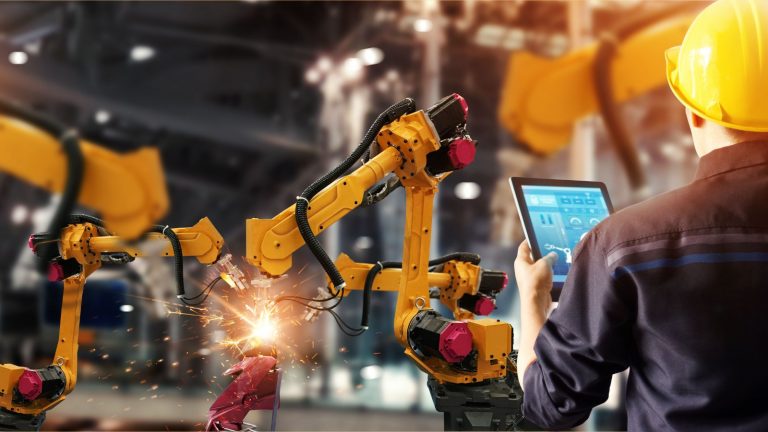
Event-driven architecture, in short, EDA, is a software design pattern that helps a company identify situations or crucial business moments and respond to them in real time or almost immediately. This pattern replaces the traditional request or response architecture in which services were required to wait for a response before moving on to the following activity. Events control how an event-driven architecture works, and the architecture is built to react to those events or take some other action in response to them.
On the other hand, This is a method of developing enterprise IT systems that allow real-time information exchange across apps, microservices, and connected devices as events take place across the company. Event-driven architecture has three key components. Those are event producers, event routers, and event consumers. A producer initially publishes an event to the router, which filters and distributes the events to consumers. This is exactly how the process works. The ability to grow, update, and deploy producer services and consumer services separately is the result of this basic independence.
Top 8 Perks of Event-Driven Architecture
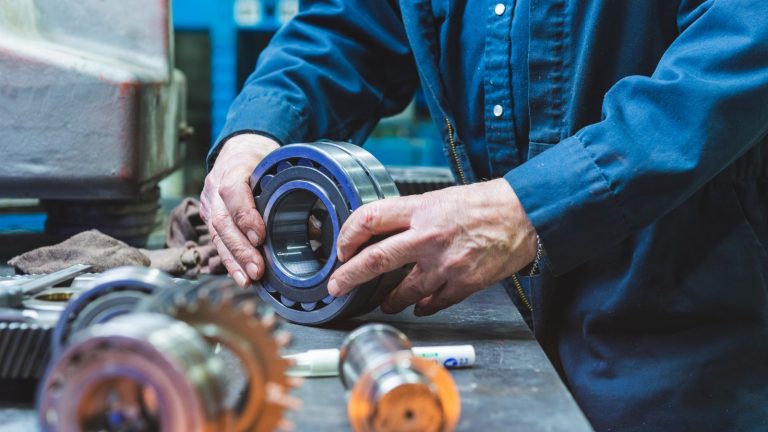
Real-Time Monitoring and Control
EDA technology seems to be revolutionising the manufacturing industry due to its ability to monitor and take control in real-time. If further explained, it empowers manufacturers to gain instant insights into their operations, ensuring seamless production. EDA systems are used to detect and respond to events in real-time while allowing for proactive intervention when issues arise.
This capability minimises downtime, enhances production efficiency, and ensures quality control. Manufacturers can track inventory levels, monitor equipment health, maintain ideal settings, and quickly adjust to changing conditions via sensors and automatic mechanisms. The manufacturing industry can stay competitive flexible, and reliably produce excellent products through EDA’s real-time capabilities.
Improved Efficiency
With EDA in action, manufacturers are given the best way to simplify their processes and operations in production. The technology helps in automating tasks and responses based on real-time manufacturing events. This automation lowers the need for manual labour, reduces room for human mistakes, and maximises resource use, which improves overall effectiveness. Whether refilling inventory, altering machine settings, or reacting to quality violations, EDA systems make sure that manufacturers perform their responsibilities precisely when required.
As you can see, EDA easily connects with other technologies. EDA’s ability to effortlessly interface with existing systems and equipment ensures a smooth flow of information, helping manufacturers to make data-driven choices quickly. The result is a leaner, more flexible production process that increases overall output. Obviously, It helps in reducing waste, making an important contribution to the whole operational excellence.
Spotting Changes in Process
This has the ability to constantly track data streams and react quickly to any breaches from accepted standards. With the use of this ability, it is possible to spot manufacturing process modifications that would be difficult to observe using standard techniques. EDA empowers manufacturers to proactively fix issues before they get out of hand, lowering the risk of production disruptions and quality difficulties. It does this by identifying abnormalities and sending out notifications in real-time.
Through its powerful capacity, EDA makes it possible to quickly modify procedures, equipment, and resources targeting the shifting circumstances. This act is important to ensure that production will stay flexible and highly adaptive to the changing requirements and unexpected challenges. As you can witness, the manufacturing industry benefits from improved operational resilience and quality control all because of this proactive approach.
Establishing Scalability
As we witness, manufacturers often face dynamic and evolving demands that require the ability to adjust production capacity quickly. EDA systems develop in this area by providing a framework that is adaptable and scalable. It easily supports increasing data flow, more sensors, or the integration of new equipment as production demands change or develop without the need for costly system involvements.
The best part is that this scalability ensures that manufacturers can efficiently achieve production goals, optimise resources, and respond to changing market conditions on time. A key benefit of this solution is its ability to grow smoothly, allowing manufacturers to remain responsive, adaptable, and competitive in today’s market.
Enhanced Fault Tolerance
With the help of this software, the industrial sector now has fault tolerance that ensures ongoing operations even in the middle of some unplanned disturbances. EDA systems come with a built-in resilience that allows them to keep processing inputs and initiating actions even when specific parts or services stop working. The capability to fault tolerance is pretty essential, specifically in the manufacturing arena where downtime can result in significant financial losses.
With EDA in use, the system can automatically redirect data and operations if a sensor malfunctions or a component breaks, minimising production bottlenecks and sustaining productivity. This fault tolerance aspect helps manufacturers maintain consistent product quality in the first place. Then it reduces the effect of failures and protects against data loss, which ultimately improves overall production.
Flexible Integration
It is a common functionality of EDA technology that empowers the manufacturing industry with flexible integration capabilities. As a result of this, it can seamlessly merge various technologies and systems into a comprehensive ecosystem. This solution readily integrates with many other technologies, including IoT(Internet-of-Things) sensors, robotics, SCADA systems, MES (Manufacturing Execution Systems), and legacy equipment. Those who are looking to update their processes while protecting previous investments will find this adaptability to be quite helpful.
If put in other words, EDA acts as a unified platform that allows efficient data exchange and communication among these diverse technologies. It enables real-time data flow, helping manufacturers to accomplish various responsibilities varying from maximising production processes, and quality control to predictive maintenance etc.
Providing Predictions for Maintenance
These technical systems always gather information from equipment and sensors and then analyse it in real-time to spot trends and abnormalities. When the system is in their hands, Manufacturers can forecast equipment breakdowns and maintenance requirements incredibly well due to this data-driven strategy. Manufacturers can now schedule maintenance operations based on these projections.
It will lead to minimising costly unexpected downtime, increasing the lifespan of equipment, and allocating maintenance resources more efficiently. This Predictive maintenance model has the ability to decrease repair expenses while simultaneously maximising equipment efficiency and minimising operational interruptions.
Supply Chain Optimisation
Error-free supply chain operational success is every manufacturer’s dream for sure. If they implement EDA systems, it can provide real-time visibility into various aspects of the supply chain. The overview they provide ranges from raw material procurement to final distribution. EDA helps manufacturers quickly make accurate data-driven choices by gathering and analysing events relating to inventory levels, manufacturing schedules, transportation status, and demand variations.
Another good thing is this real-time information offers improved inventory management, lowering carrying costs while maintaining timely material availability. EDA also makes it easier to coordinate with partners and suppliers more effectively, increasing the effectiveness of the overall supply chain network.
Cerexio Event-Driven Architecture
The Cerexio-powered event-driven architecture is a versatile software framework facilitating event-driven processes and enabling modern applications to function efficiently. It supports any programming language and supports networked digital architecture, making it simple to develop creative and useful applications. From easily integrated with IoT, AI, and ML technologies to handling various business levels Cerexio EDA is a highly flexible application.
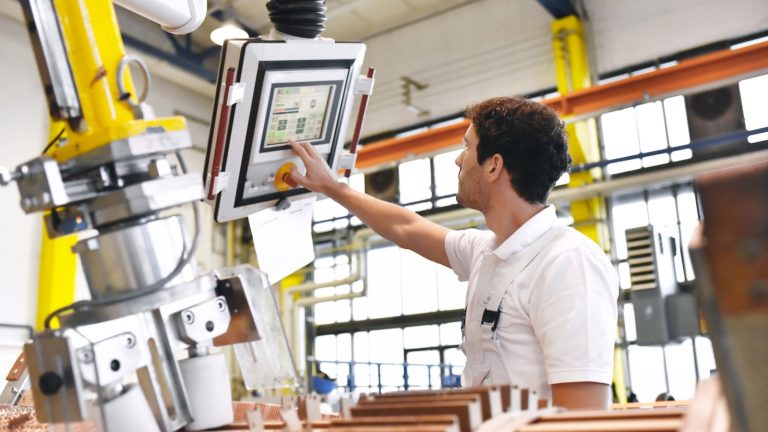
Scaling Up Your Business with Modernity
It is a wise movement if you choose to walk on a path that leads to your expectations and business desires. Technology is what can help you to accomplish those dreams and narrow down the long path with its powerful features. However, not every tool in the market can benefit you greatly as you expect. That is why you need to collaborate with the industry supplier, as it will keep your worries at bay.
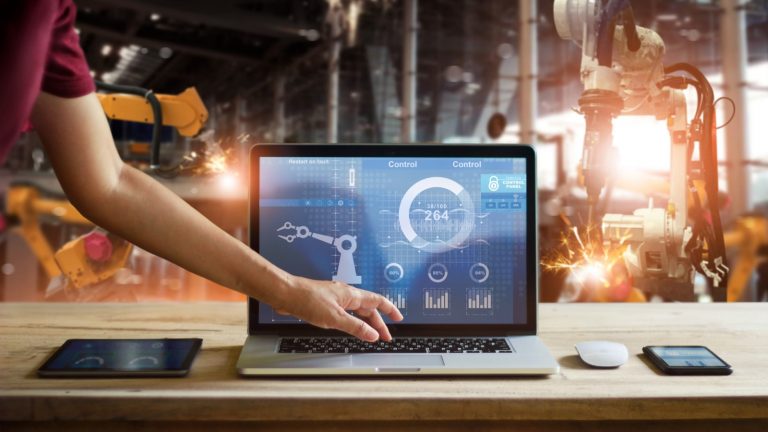