The rising concept of ‘Digital Twin’ is being used more in a multitude of production processes in the industrial world. Being a technology utilised for expert visualisation, digital twin is powered by IoT-based sensors that companies employ to collect crucial data on manufacturing industry operations. Did you know that in 2021, the global market for digital twin technology is estimated to be worth $6.5 billion? By 2030, it is anticipated to reach $125.7 billion. The more manufacturing companies embark on the race of business growth, the more technologies like digital twintechnology come into play every day!
In this article, we are going to share knowledge about ‘Digital Twin Technology’ and how its implementation happens in the fast-paced manufacturing industry. Plus, we will discover the benefits of utilising digital twin technology in manufacturing operations in this article today.
What is Digital Twin in Manufacturing?
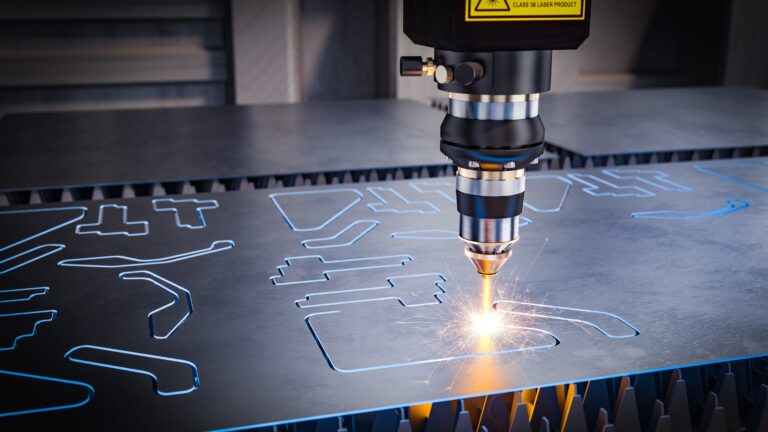
A digital twin is a full digital representation of an environment, a product, or a system that can be used for testing, integration, and simulations without affecting the counterpart in the real world. A twin can execute many simulations at once, whereas a simulation normally only duplicates one scenario or process, allowing for the large-scale study of numerous processes and results. If put simply, in manufacturing, a digital twin is a virtual counterpart of a facility, factory, piece of equipment, system, or product.
This is Why Manufacturing Industry Should Opt for Digital Twin
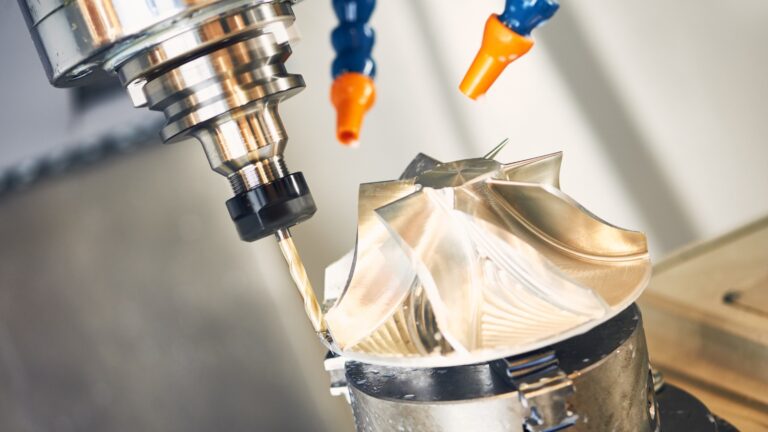
The way that manufacturing processes are optimised has been profoundly changed by the rise of digital twin technology. Through enhanced product design, development, predictive maintenance, and real-time simulations, digital twin technology has the ability to radically revolutionise the industrial environment and help businesses thrive in the era of Industry 4.0. In the section below, we will be discussing the benefits of implementing digital twin technology for the manufacturing industry.
Decrease Product Time to Market
The revolutionary digital twin technology has drastically changed the industrial sector over the years. Utilising it has a substantial advantage in reducing product time to market. By building a virtual version of tangible assets, manufacturers can carry out real-time simulations and testing. This allows for quicker design and development iterations. With this capacity, the entire product development process could be sped up and the need for several physical prototypes can be removed.
Using the application of digital twin technologies, manufacturers can acquire rapid insights into how their physical assets behave and operate. The collaborative component of adopting digital twin technology reduces time to market drastically. Teams and stakeholders located in diverse regions can readily communicate and collaborate thanks to the virtual replica.
Improve the Efficiency of Processes and Products
Digital twin technology has become a game-changing technology in the industrial sector, enabling organisations to improve the efficiency of both processes and products. Digital twin technology enables real-time insights and data analytics, enabling manufacturers to make well-informed decisions and changes by building virtual versions of actual assets and processes.
Manufacturers can maximise and improve their operations without spending money on expensive physical iterations by using digital twin technology to simulate and test their products in a virtual setting. This skill encourages improved production, less waste, and higher efficiency.
Digital twin technology is also essential for improving the performance of products. The behaviour and performance of the products they produce can be continually observed and examined by manufacturers in real-time. Early issue diagnosis makes proactive maintenance possible, increasing product dependability and reducing downtime.
Making System Designs Better
The industrial sector gains a lot from digital twin technology because they enable better system designs. Manufacturers can simulate and test various system designs in a risk-free environment by building virtual duplicates of actual assets and processes. Engineers and designers can gain immediate insights into the behaviour and performance of various system configurations thanks to digital twin technology . As a result, they are more equipped to foresee future problems, improve designs, and reach data-driven judgments before making changes to the physical world.
Digital twin technology allows iterative design, which improves system effectiveness, decreases downtime, and boosts productivity. Manufacturers have the ability to optimise their designs, reducing inefficiencies and boosting overall performance.
Increase Production Efficiency
A digital twin is a powerful tool that manufacturers can employ to verify that their systems and processes are working properly. By continuously monitoring these systems, operators can quickly recognise any potential problem areas and choose the best course of action to fix them. This is especially useful for industry because production flow routinely falls short of expectations.
Companies that employ digital twin technology could acquire a deeper knowledge of their production line, allowing them to identify areas for improvement and take the necessary steps to attain optimum efficiency.
Testing New Products
Previously, testing new or updated products inside of running production processes required manufacturing teams to go through a time-consuming process of trial and error. Digital twin technology has drastically changed this approach, allowing manufacturers to test updated setups fast and effectively while reducing the possibility of expensive errors.
Companies are able to make informed decisions and carry out changes with more certainty and precision thanks to digital twin technology, which makes it simpler and faster than traditional physical testing to replicate several scenarios.
Enable Predictive Maintenance
In smart manufacturing, unplanned downtime can cost hundreds or thousands of dollars per hour, which can lead to large financial losses. Digital twin, on the other hand, provides a workable solution by enabling operators to anticipate future issues under various environmental pressures and conditions by integrating with AI-driven predictive models.
By employing digital twin technology to get insights into the inner workings of complex systems, manufacturers can effortlessly predict the start of problems and proactively address maintenance difficulties.
Make It Practical for Virtual Commissioning
Through the use of virtual commissioning, which is an essential tool for smart manufacturing, engineers can accurately test system designs. Potential problems with integrating equipment and processes can be predicted and fixed by modelling the entire system rather than just isolated components using digital twin technology. Engineers will be able to identify issues before they develop, leading to a smoother and faster implementation process.
Digital twin technology can be utilised as well to assess the overall performance of the manufacturing floor, ensuring that the system is as effective and efficient as possible.
Cerexio Digital Twin Technology
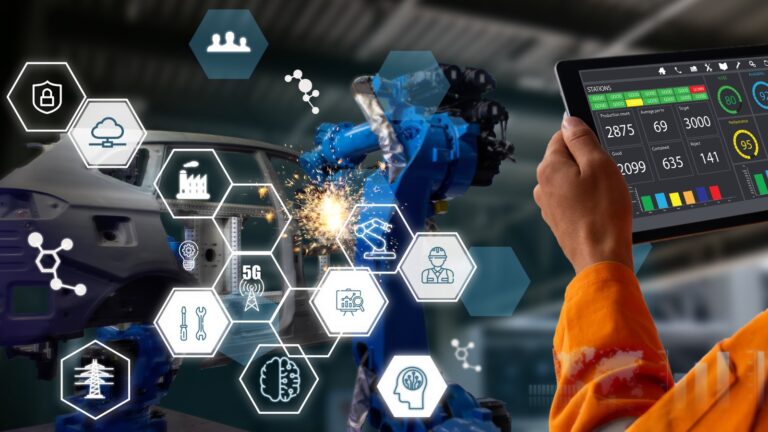
Cerexio presents our latest Digital Twin technology for your manufacturing business with cutting-edge 3D and 4D advancements. From utilising AR and VR technologies to smart planning and optimization our digital twin system is well-designed to serve all your industry matters. With Cerexio digital twin software, your business is about to see new horizons.
Step into the New World Technology with Digital Twin
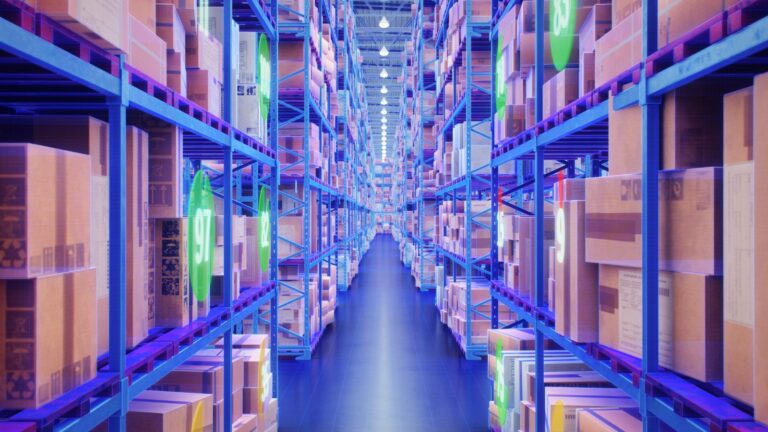
As we have come to the end of our analysis of cutting-edge manufacturing technology, it is clearly evident that digital twin technology represents a revolutionary innovation that holds the key to attaining previously unheard-of levels of productivity, efficiency, and competitiveness.