This article explores how centralising data empowers manufacturers to improve performance, reduce costs, and drive innovation at scale.
We will look at
- The Hidden Cost of Fragmented Data
- What is Centralised Data Management in Manufacturing?
- Key Benefits of Centralised Data in Manufacturing
- Implementation: How to Transition Smoothly
- Overcoming Common Challenges
- Why the Time to Act Is Now with Cerexio
- Driving Your Manufacturing Business with Centralised Data
The Hidden Cost of Fragmented Data
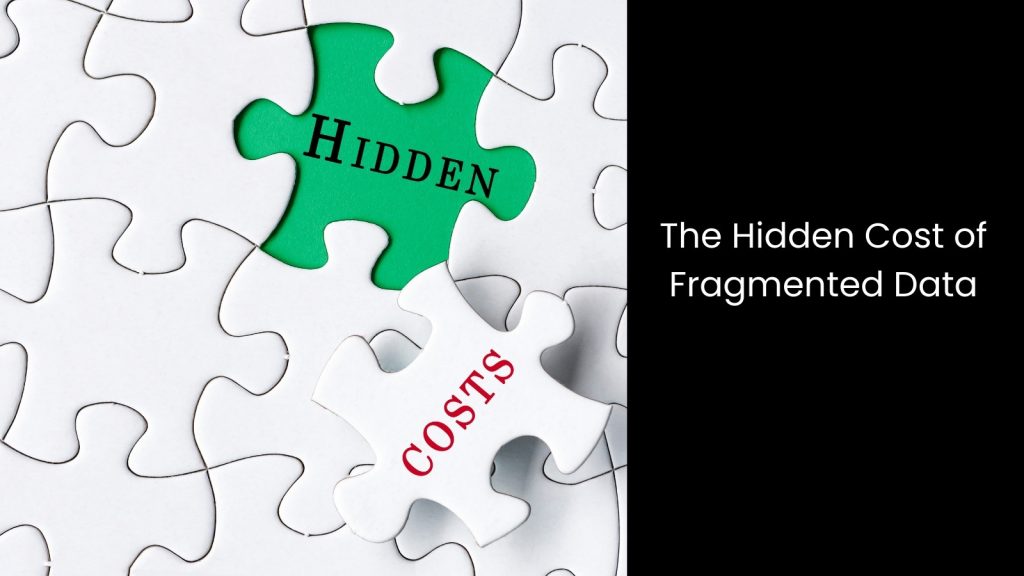
- Fragmented data systems are more than just a nuisance; they are a major barrier to growth. This is not a new thing in this industry, but every day, every manufacturer goes through it.
- When information is scattered across departments, stored in incompatible formats, or manually extracted for analysis, errors become inevitable. According to reports like Gartner, poor data quality costs businesses an average of $12.9 million annually.
- In one high-profile case, one company attributed a $110 million revenue loss and a $5 billion drop in market value to bad data from a major customer. Yes, it is that serious!
- For manufacturers, disjointed data systems result in slow reporting, misinformed decisions, production delays, and missed opportunities.
- These inefficiencies can quickly compound across large-scale operations, making it clear that a centralised data strategy is not something manufacturers can take lightly, but a necessity.
What is Centralised Data Management in Manufacturing?
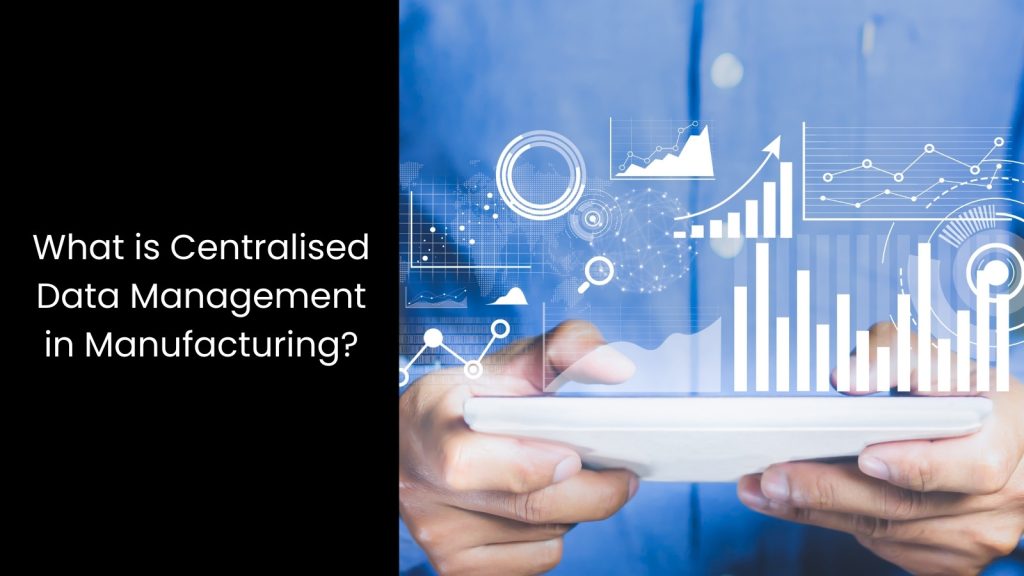
- Centralised data management refers to the consolidation of all operational, production, supply chain, and business data into a single, unified platform.
- It is like this: instead of juggling multiple spreadsheets, software, or databases, manufacturers rely on one integrated system that ensures data accuracy, consistency, and accessibility. This centralised hub enables real-time monitoring, standardised workflows, and streamlined communication across departments.
- This means that it acts as the single source of truth for the entire organisation. It simply allows decision-makers to respond quickly to issues, align goals, and optimise performance.
Key Benefits of Centralised Data in Manufacturing
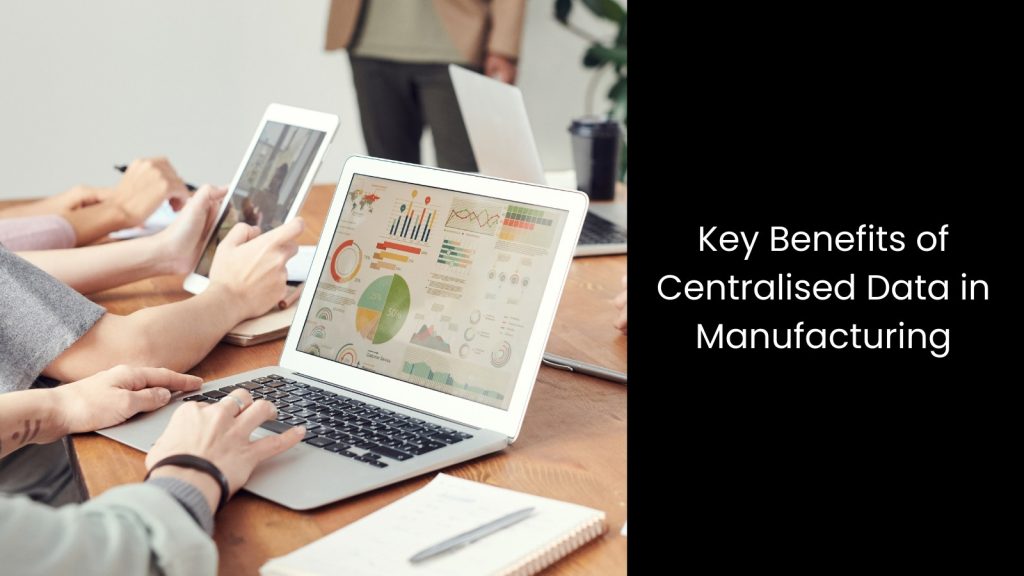
Improved Operational Efficiency
Real-time access to accurate data allows manufacturers to make faster, more informed decisions, reduce production bottlenecks, and increase throughput. When eliminating the time employees spend searching for or reconciling data, manufacturers can focus on core tasks and strategic initiatives.
It is a widely known fact that companies without a clear inventory of accessible data waste 30-40% of employee time just locating information.
Centralised systems solve this by providing dashboards, alerts, and analytics that enable agile responses to changing conditions. In addition, these systems improve coordination between departments, reduce duplicative tasks, and allow for better planning and scheduling, all of which contribute to overall productivity.
Significant Cost Savings
This visibility empowers managers to optimise scheduling, inventory, and energy consumption.
Some reports suggest that companies moving from fragmented to integrated data environments save between 5% and 10% in the first six months and 10-30% over three years. These savings not only improve the bottom line but also free up capital for innovation and growth.
For example, predictive maintenance powered by centralised data can help avoid costly equipment breakdowns and reduce the need for emergency repairs, resulting in further financial savings.
Enhanced Sustainability
The latter enables precise tracking of energy use, emissions, material waste, and water consumption across facilities. With this level of insight, manufacturers can identify inefficiencies, implement green initiatives, and measure the impact of sustainability programmes.
As this mechanism optimises resource usage and reduces waste, companies can protect the environment and also enhance brand reputation and reduce operational costs. Real-time data also supports compliance reporting, helping businesses meet environmental standards and avoid regulatory penalties.
Better Demand Prediction and Agility
Centralised data gives manufacturers the tools to forecast demand more accurately, identify risks like downtime or inventory shortages, and respond in real-time. Instead of reacting to problems after they occur, manufacturers can proactively adjust production, procurement, and distribution plans.
This sort of agility minimises losses, maximises customer satisfaction, and strengthens supply chain resilience. Furthermore, integrating market trends, customer feedback, and historical data into a unified system allows for smarter forecasting and timely interventions, ensuring a competitive edge in rapidly changing markets.
Improved Product Quality and Compliance
Further, automated alerts can notify teams of deviations in real-time, allowing immediate corrective actions. Over time, this leads to improved product reliability, reduced warranty claims, and stronger customer loyalty.
Plus, centralised documentation also supports traceability, making it easier to conduct audits and track materials or components throughout the production cycle.
Faster Innovation and Time-to-Market
When eliminating information silos, collaboration across departments improves, enabling faster prototyping, testing, and scaling of new solutions.
This speed to market is critical in competitive sectors where being first can mean a significant market advantage.
Implementation: How to Transition Smoothly
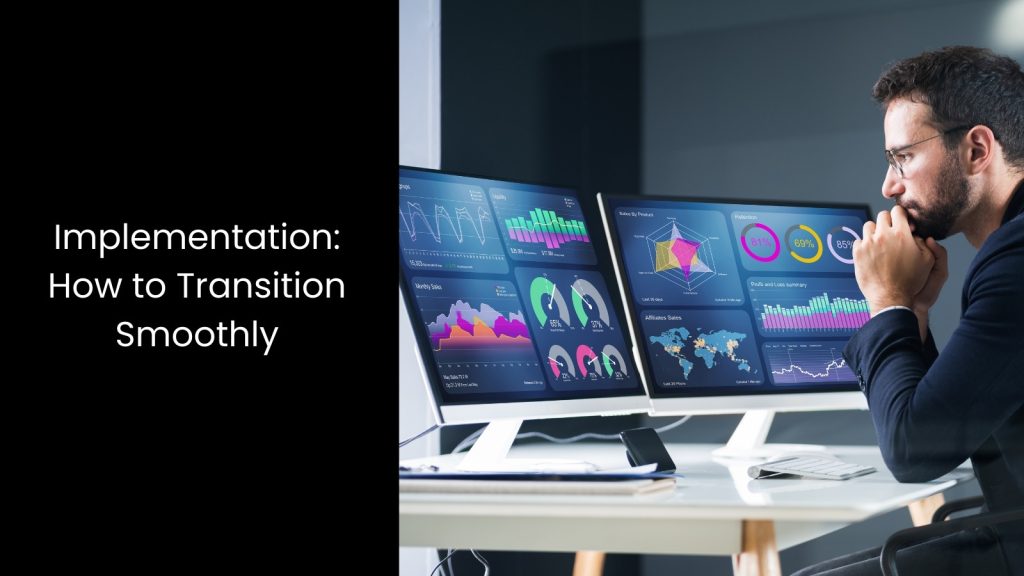
- Successfully adopting centralised data management requires careful planning and execution.
- Manufacturers should start by selecting a platform that is scalable, user-friendly, and easily integrates with existing ERP, MES, and CRM systems.
- Equally important is staff training. Employees at all levels must understand how to use the system and why it matters. Leadership plays a key role in driving adoption, setting clear goals, and allocating resources for implementation.
- Before migration, organisations must also clean and standardise their existing data to avoid importing errors into the new system.
- A phased rollout, beginning with high-impact areas like production or quality control, can help test workflows and refine strategies.
- Continuous feedback and performance monitoring ensure the system evolves with the organisation’s needs.
Overcoming Common Challenges
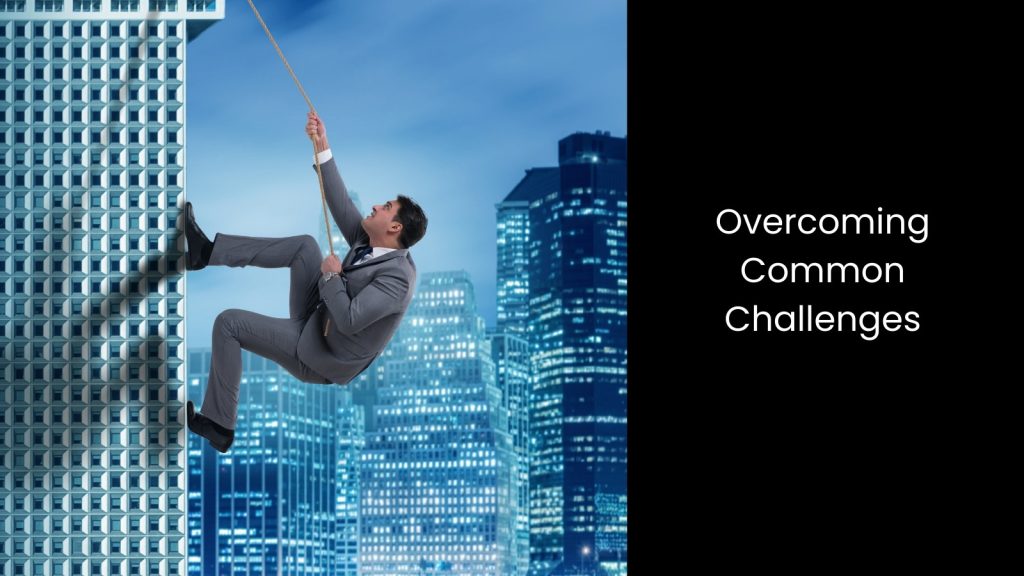
- One common mistake is choosing software with too many features that add complexity without delivering real value. Manufacturers should focus on core functionalities that support their goals and scale over time.
- Another risk is creating new data silos by allowing certain departments to maintain separate tools. Ensuring complete integration and cross-functional collaboration is key to long-term success.
- Finally, some organisations underestimate the cultural shift required. Without clear communication and change management, even the best systems can fail to gain traction.
Why the Time to Act Is Now with Cerexio
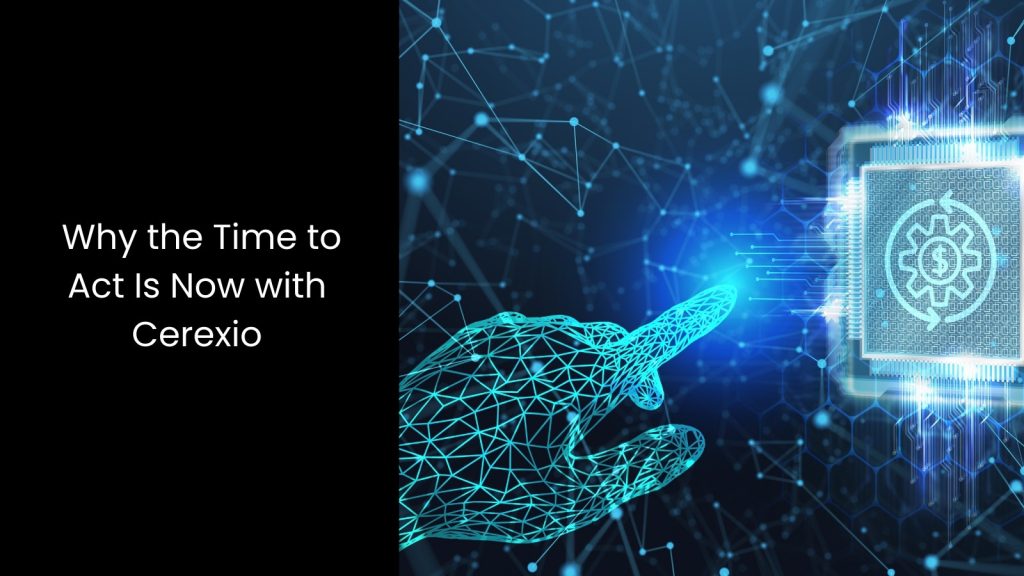
With Cerexio’s Industry 4.0 capabilities, manufacturers can centralise and visualise data from diverse systems across facilities. This unified data ecosystem enhances traceability, predictive analytics, and operational control, empowering stakeholders to make informed decisions quickly and drive productivity, sustainability, and efficiency across the entire manufacturing process.
Driving Your Manufacturing Business with Centralised Data
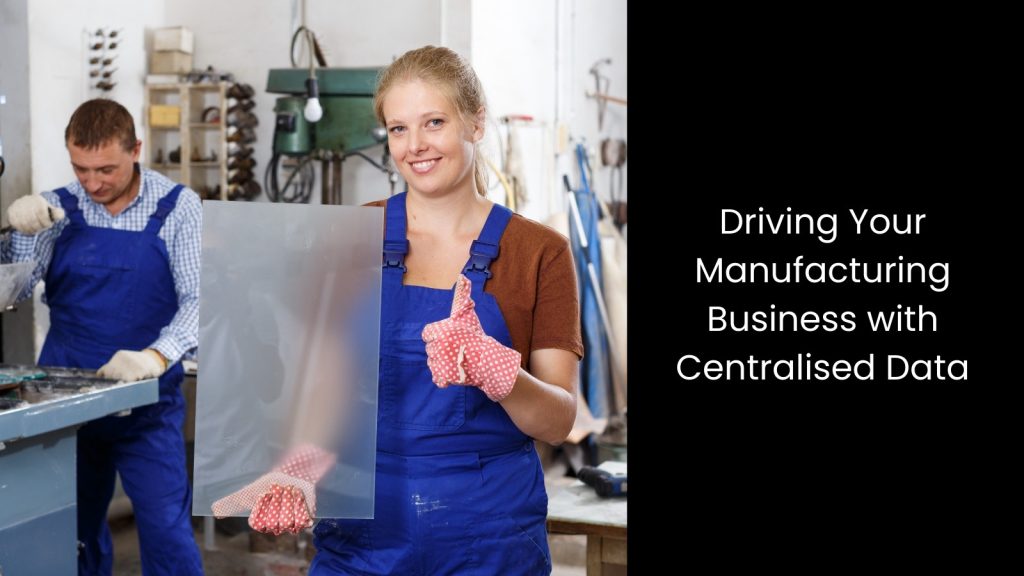
Manufacturers must embrace centralised data management to navigate the complexities of today’s industrial landscape. With the right strategy, tools, and commitment, they can transform their operations, reduce costs, meet sustainability goals, and respond dynamically to market demands. Centralised data is not just a technology upgrade; it is a catalyst for innovation, resilience, and long-term growth. For forward-thinking manufacturers, the time to centralise is now.