Manufacturing is one massive ball of different production methods. Among them, batch production is what industries like food, pharmaceuticals, and textiles select mainly due to its ability to blend efficiency with adaptability. However, it is not as easy as it seems to be. That is because not every manufacturing system can handle the demands of moderate volumes, variety, and quick changeovers. Manufacturers worldwide struggle to find the perfect match and end up sacrificing quality for speed or flexibility. Then, which system can handle batch production more successfully?
In this article, we discover the main types of manufacturing systems that are suitable for batch production.
What is Batch Production in Manufacturing?
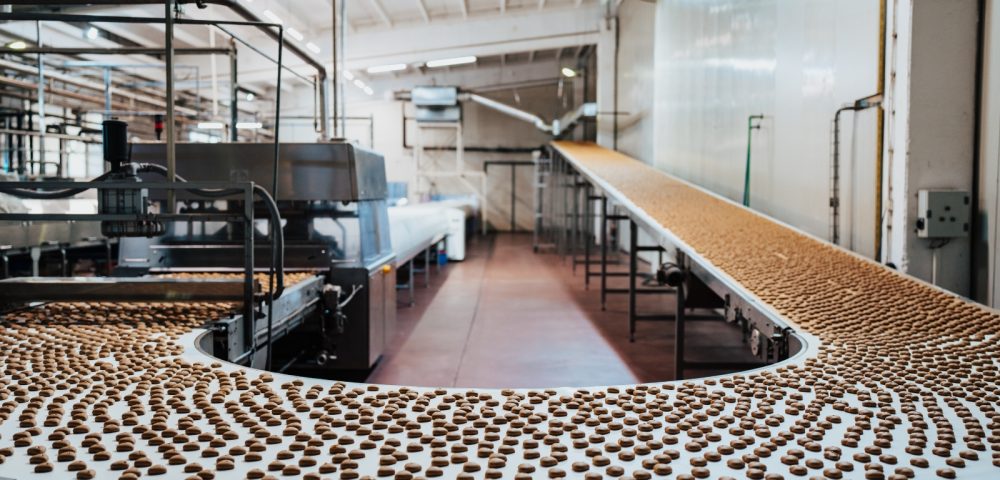
- Batch production in manufacturing means producing goods in specific, fixed quantities called batches instead of making them one by one or in a continuous flow.
- Manufacturers produce a set amount of identical products before switching the machines and processes to create a different batch. This method works best when companies need to balance efficiency with variety because it allows them to create moderate quantities while still offering different designs, flavours, or sizes.
- Many industries depend on batch production because it lets them meet customer demands without wasting resources.
- With its balance of variety and efficiency, batch production remains a smart choice for many industries.
Top Manufacturing Systems that are Suitable for Batch Production
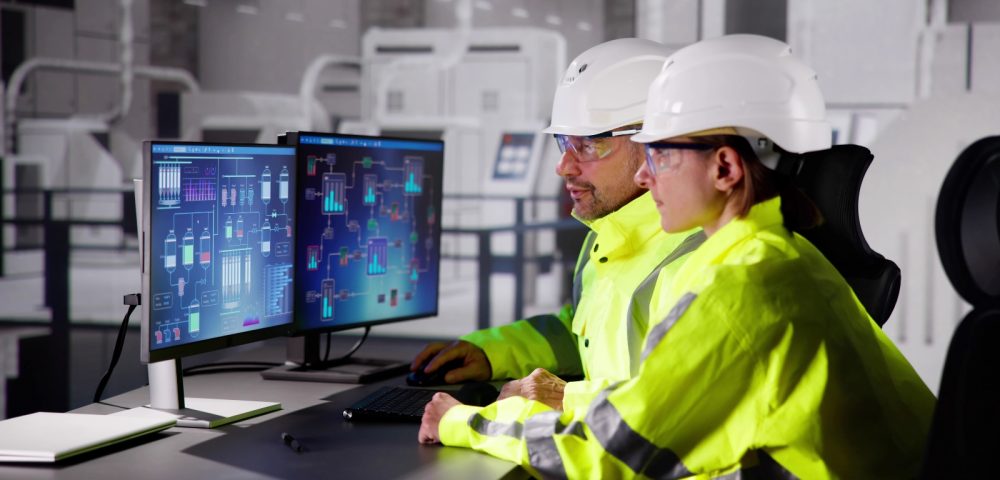
Flexible Manufacturing System (FMS)
If you look into Google, you can see this pops up as the number one choice for batch production.
FMS lets manufacturers handle batch production with remarkable ease because it combines automation, adaptability, and speed. This system uses advanced computer controls, robots, and CNC machines to switch between different products quickly without wasting much time or materials.
Manufacturers who deal with moderate volumes and frequent product changes find FMS very helpful since it balances efficiency with variety. For example, an FMS can produce a batch of engine parts, then reconfigure itself within minutes to start making a different component. This flexibility saves labour costs and reduces downtime between batches, which makes it much more efficient than older methods.
The system also helps maintain high quality because machines follow precise, programmed instructions without errors caused by manual intervention.
Although it requires a higher initial investment, companies recover the cost through better productivity and lower waste.
Cellular Manufacturing
The latter organises machines and workers into small groups, or ‘cells,’ that focus on producing similar products in batches. Each cell handles a family of parts that share similar shapes, processes, or materials, which cuts down on unnecessary movement and saves time during production.
Unlike a traditional assembly line that spreads operations out, cellular manufacturing keeps everything close together, which makes it easier for workers to communicate and solve problems quickly. When manufacturers choose this system for batch production, they can reduce setup times and improve quality because the same team focuses on related products over and over.
Although cellular manufacturing works well for batches, it struggles when product designs change too drastically because cells need to be reconfigured. Still, it offers a good balance for manufacturers who want some flexibility but do not need the full automation of an FMS. When used effectively, this system creates faster flow and higher productivity in batch-oriented operations.
Job Shop Manufacturing
Job shop manufacturing suits batch production when products require a high level of customisation and the volumes stay relatively low to moderate. This system uses a wide variety of machines arranged by function, not sequence, which gives workers the freedom to handle different tasks as needed.
Manufacturers use job shops when no two batches look exactly alike, such as in custom furniture, speciality tools, or medical devices.
In a job shop, skilled workers move materials between stations where each machine performs a specific operation, allowing flexibility to produce unique designs. This system also works well when customers ask for specific modifications that a standard line cannot handle.
However, job shops tend to move more slowly and cost more to operate than systems designed for higher volumes. They also create longer lead times because switching between tasks takes time and planning.
Manual Batch Production Line
This particular system relies on workers and basic machines to produce batches step by step in a straightforward process.
This system works best in smaller factories or businesses that do not have the resources to invest in high-tech equipment but still need to meet batch demands. Workers set up machines, complete each step, and then move the batch to the next station until finished. This method allows manufacturers to produce moderate quantities with a level of variety that automated systems might find difficult to accommodate.
However, it demands more labour and takes longer than automated methods, making it less efficient when demand grows. Despite this, manual batch production remains an important choice for industries where craftsmanship or detail matters more than speed.
Lean Manufacturing with Batch Scheduling
It combines the efficiency of lean principles with the flexibility needed for batch production. This system aims to eliminate waste, such as excess inventory, waiting time, and overproduction, while still producing goods in batches that meet customer needs.
Manufacturers plan and schedule batches carefully so that each batch uses resources wisely without causing bottlenecks. For example, a furniture company might schedule just enough wooden parts for a batch of chairs while ensuring the next batch of tables starts as soon as possible.
Lean techniques, like just-in-time production and continuous improvement, help streamline workflows and keep the focus on delivering value to customers. While traditional lean manufacturing favours one-piece flow, many industries adapt it to batch settings because it allows them to balance efficiency with variety.
This system works well when volumes are moderate and designs change often enough to prevent full automation.
Hybrid Manufacturing Systems
Hybrid manufacturing systems blend elements of job shop and flow line methods to suit the unique needs of batch production. This system gives manufacturers the flexibility of a job shop and the efficiency of a flow system, making it a good middle ground when neither extreme works alone.
In a hybrid setup, machines and workers perform specific tasks in a semi-organised sequence while still allowing enough freedom to switch between batches of different products.
Manufacturers tend to choose this approach when their products have some standardisation but still require customisation between batches. For example, an electronics factory might produce batches of circuit boards using standard processes while allowing adjustments in design or components for each batch. Hybrid systems help reduce setup times compared to a full job shop while avoiding the rigidity of a flow line.
However, this method demands careful planning and skilled workers who can adapt to changes quickly.
Cerexio EBR System for Batch Production Excellence
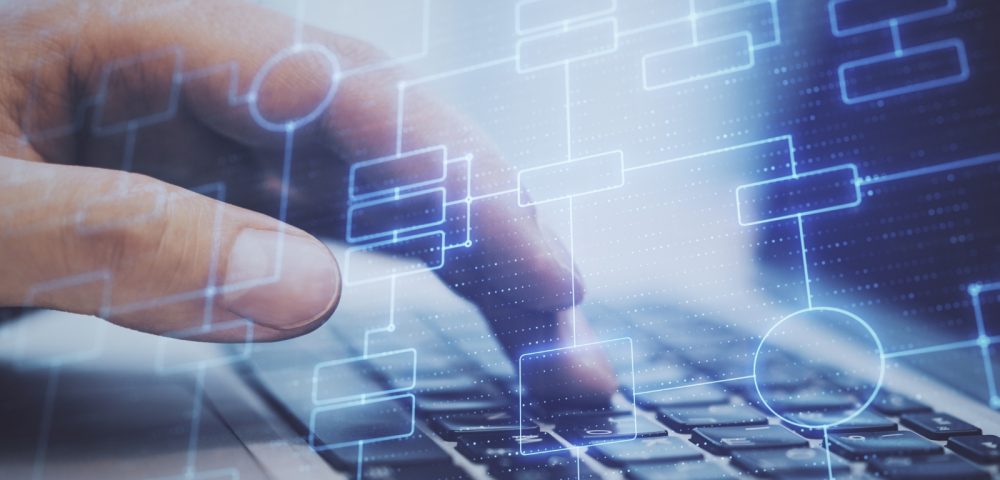
Cerexio offers an Industry 4.0-enabled Electronic Batch Record System that transforms batch production by connecting machines, data, and analytics. Every process step is tracked automatically, minimising human error. With our Cerexio solution, quality control happens in real-time, making it easier to maintain standards.
Guaranteeing Every Batch of Your Produce is of Top Quality
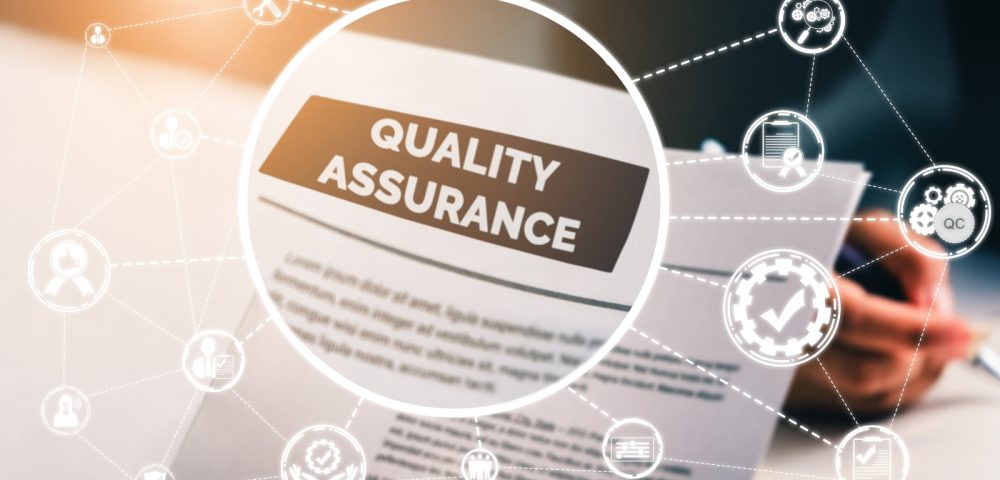
Batch production skyrockets when you master both change and consistency, and that is exactly where the technology shines. The demand for speed and quality grows louder daily. Discover how you can make every batch unforgettable today. Connect with Cerexio to unleash the top quality for all your batches.
FAQ about Batch Production
Batch production is best suited for manufacturing moderate quantities of products with some variety. Industries like food, pharmaceuticals, and clothing use it to produce goods in fixed batches, allowing flexibility, efficient changeovers, and consistent quality while meeting varied customer demands.
Batch production needs machines such as CNC machines, mixers, ovens, conveyors, and flexible manufacturing systems. Automated robots, packaging machines, and assembly tools also help streamline processes, enabling efficient, high-quality production of batches while handling moderate volumes and frequent product changes.
The main disadvantage of batch processing is downtime between batches during changeovers, which reduces efficiency. It also requires careful planning to avoid delays, and inconsistent batch sizes can lead to higher costs compared to continuous production methods in high-demand situations.