This article explores how manufacturers apply smart materials in real-world production scenarios.
What are Smart Materials in Manufacturing?
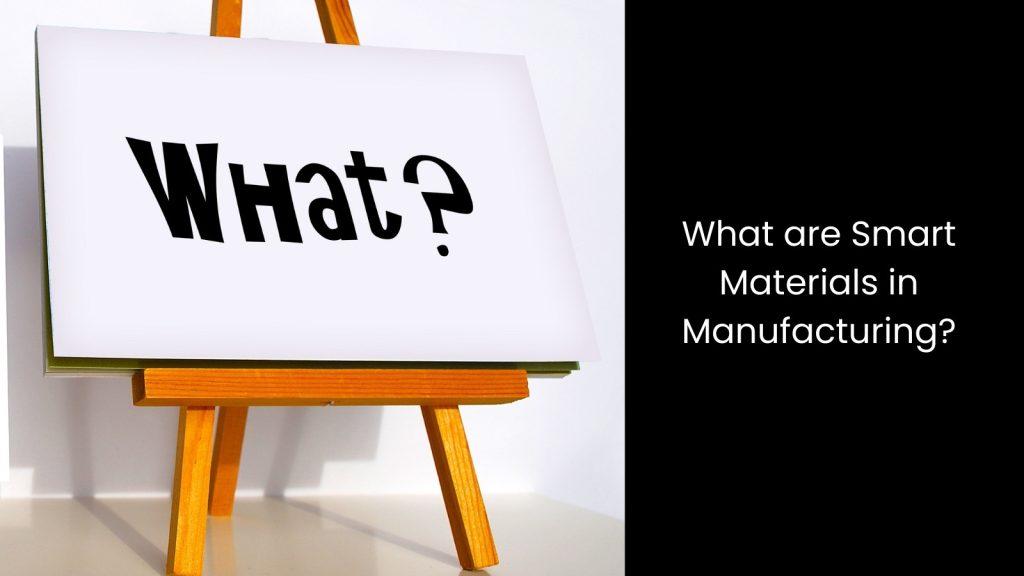
- Smart materials is the process of using materials that can sense and respond to changes in their environment without the need for external control. These materials have unique properties that allow them to adapt to things like temperature, pressure, moisture, and even light.
- For example, shape-memory alloys can return to their original shape after being deformed when exposed to heat. This responsiveness makes smart materials ideal for a range of manufacturing applications.
- In manufacturing, smart materials work by automatically adjusting their properties to improve performance or efficiency. For instance, in smart packaging, materials can change their structure to protect products, maintain freshness, or even display information. This ability to adapt improves not only the functionality of products but also saves energy and reduces waste.
- When it comes to some industries like electronics, smart materials help create devices that are more durable and efficient, as they can self-heal or change their shape to prevent damage. The use of smart materials in manufacturing can lead to products that last longer, require less maintenance, and are more environmentally friendly.
- As industries continue to explore new ways to incorporate smart materials, the innovation potential grows. This makes them an exciting area of development for the future.
Top 4 Advantages of Smart Materials in Manufacturing
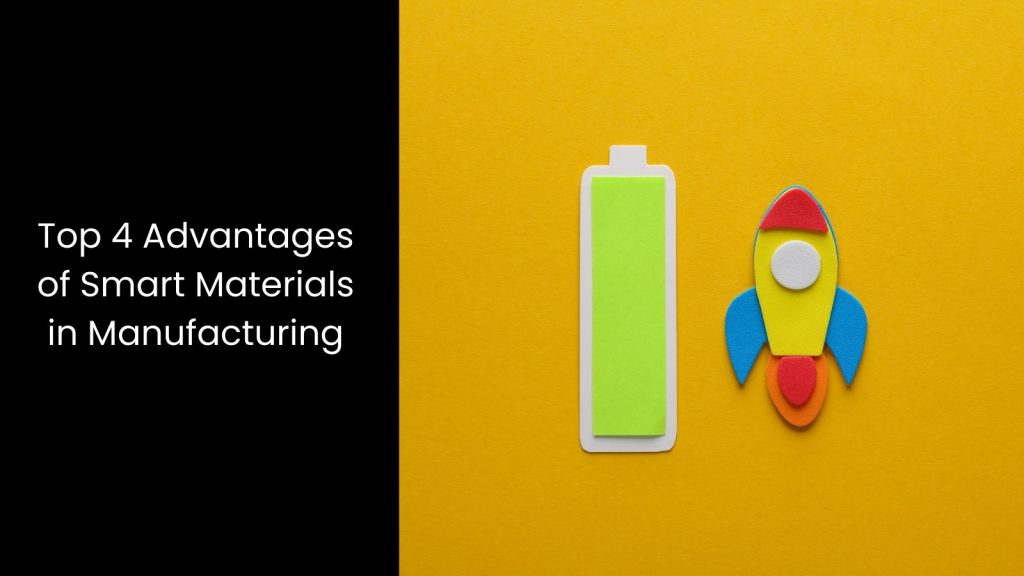
Improved Durability
Some advanced coatings, for example, can regenerate their surface when scratched, preventing further deterioration. In industries like automotive and aerospace, manufacturers use self-healing polymers and alloys to extend the lifespan of components that experience constant stress. Smart materials also adapt to external conditions. This helps them withstand harsh environments.
For example, in electronics, flexible smart materials prevent devices from breaking when they are bent. It improves durability without sacrificing performance. In smart packaging, these materials protect products by adjusting to temperature or humidity, keeping goods in perfect condition during transport.
The ability to resist damage and repair itself gives smart materials a huge advantage over traditional materials, which usually weaken over time.
As technology keeps improving, manufacturers continue to explore new ways to use smart materials. So, it creates products that are not only stronger but also more reliable and cost-effective. This shift towards smarter manufacturing means consumers get better-quality products that last longer while companies reduce waste and maintenance expenses.
Enhanced Efficiency
This means that manufacturers can use shape-memory alloys that return to their original form when heated. This eliminates the need for complex mechanical systems. Some coatings change their properties based on the environment, preventing unnecessary wear and reducing maintenance.
Another example is that when it comes to smart materials in robotics, they help machines work with better precision by adapting to force and motion, cutting down on errors and improving productivity. In energy management, phase-changing materials store and release heat efficiently, reducing the need for excessive heating or cooling. Even in smart packaging, materials react to humidity or oxygen levels to keep products fresh, reducing spoilage and ensuring better supply chain efficiency.
Since smart materials optimise how resources are used, companies have the capacity to lower their production costs while creating higher-quality goods. Unlike traditional materials that need frequent adjustments, smart materials improve performance without extra effort. That quality makes manufacturing more reliable.
As industries push towards smarter, more sustainable production methods, smart materials continue to play a huge role in transforming how factories operate.
Innovation Potential
You already know that these advanced materials change their properties based on temperature, pressure, or electrical signals, and it allows manufacturers to create products that were impossible with traditional materials.
Shape-memory alloys make it easier to design flexible structures that can shift back to their original form, while self-healing polymers help create products that repair minor damage without human intervention. Engineers experiment with smart textiles that adjust to body temperature, making clothing more comfortable and functional.
Plus, manufacturers can develop bendable displays and ultra-thin sensors using smart materials, and it will lead to futuristic gadgets that perform better and last longer. In one way, smart packaging benefits from materials that react to environmental conditions, extending shelf life and reducing waste. In another way, factories use adaptive coatings that improve durability and efficiency, cutting down maintenance costs while improving product quality.
Unlike regular materials, smart materials offer endless room for creative applications and help industries develop cutting-edge solutions. As research continues, manufacturers keep discovering new ways to integrate smart materials into different sectors. This makes everyday products more responsive, durable, and sustainable.
It is noticeable that this shift towards smarter production methods pushes industries to think beyond limitations. The result would be making manufacturing more advanced, adaptable, and exciting for the future.
Higher Precision and Accuracy
These advanced materials sense factors like temperature, pressure, and stress. It allows manufacturers to fine-tune production without relying on constant human adjustments. Shape-memory alloys help create precise components that return to their original form after deformation, making them useful in industries like aerospace and medical devices.
Further, piezoelectric materials convert mechanical energy into electrical signals and improve sensor accuracy in high-tech equipment. Also, smart materials enable machines to adjust grip strength based on object sensitivity, reducing damage and improving efficiency.
Factories use self-adjusting coatings that change their properties under different conditions, ensuring consistent performance without extra effort. Smart packaging benefits from intelligent sensors that monitor freshness and provide real-time feedback, reducing errors in supply chains.
Cerexio Solutions for Tracking the Quality of Smart Materials in Manufacturing
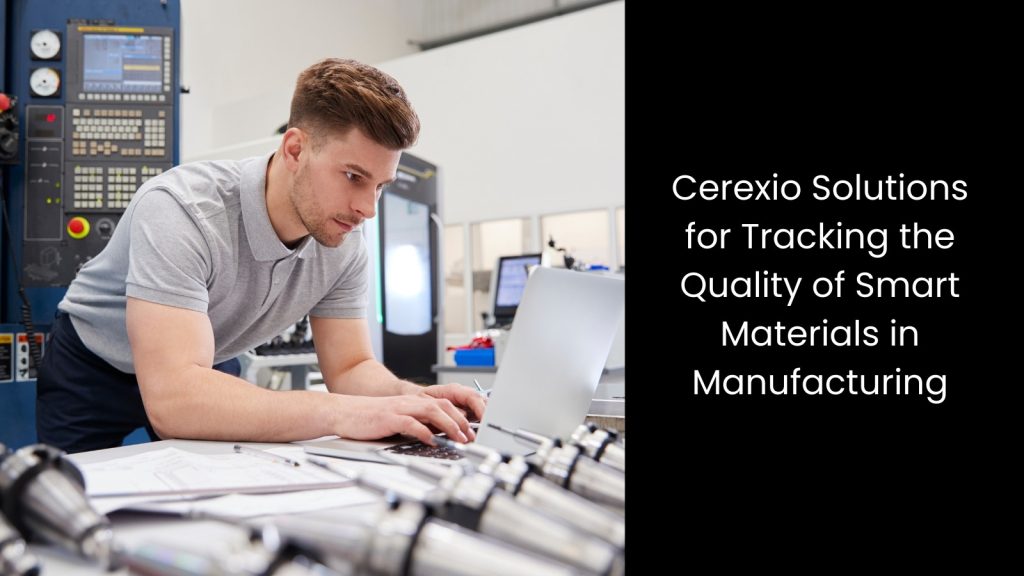
Cerexio has introduced Industry 4.0-powered software tracking systems to help monitor the quality of smart materials in manufacturing by using real-time data, AI-driven analytics, and IoT sensors. Our cutting-edge systems detect defects, analyse performance, and ensure consistency, reducing waste and improving efficiency. We are proud that Cerexio’s automated tracking capacity enhances precision, ensuring smart materials meet industry standards and product requirements.
Significantly Reducing the Costs via Using Smart Materials in Manufacturing
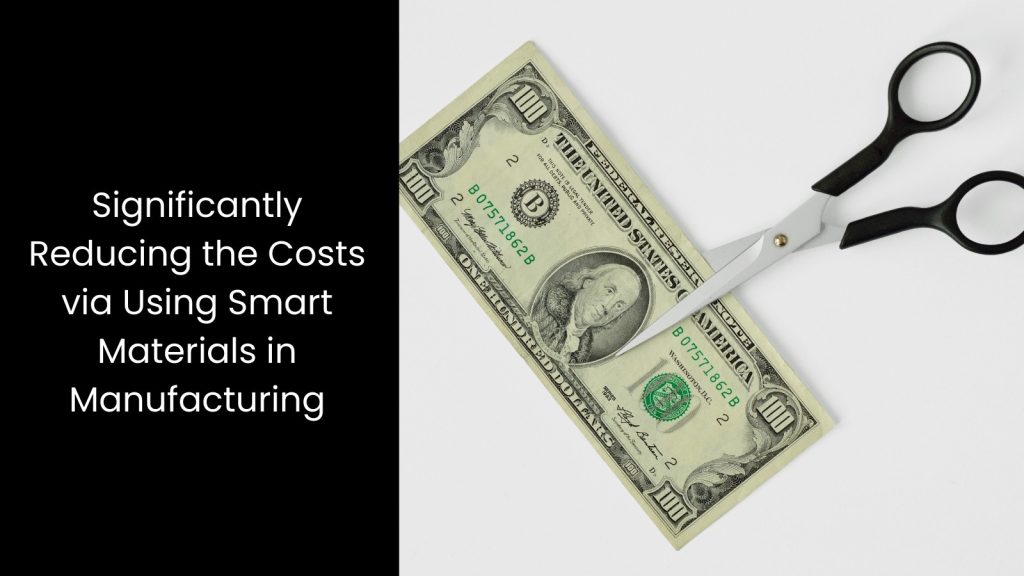
You cannot deny the fact that embracing smart materials in manufacturing leads to significant cost reductions by minimising waste, lowering energy consumption, and enhancing product lifespan. These innovative materials enable manufacturers to optimise resources, streamline production, and maintain competitive pricing while meeting sustainability goals. As it seems, the future of manufacturing lies in smarter, more efficient material choices. Do you agree?