In a world full of emerging technologies and new advancements, the manufacturing industry is moving forward day by day. Gone are the days when manufacturers relied on manual work and labour in order to proceed with production. Now, the times have changed, and advanced and modern tools and technologies have made everything from production and packaging to warehousing and supply chain super smooth. Industry 4.0 is another realm that has revolutionised the industrial world, especially lean manufacturing.
In this article, we explore the application of Industry 4.0 digital strengths in lean manufacturing in order to extract the best essence of the procedures.
We will discover
What is Industry 4.0?
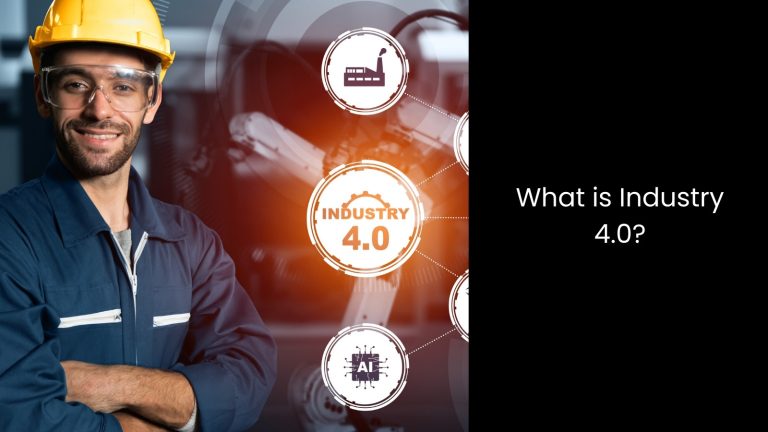
- This is a term that describes the ongoing digital transformation of the manufacturing industry.
- The mechanism of the latter starts with the integration of advanced technologies like artificial intelligence, the Internet of Things (IoT), robotics, and big data analytics into the production process.
- In today’s world, this technological framework is receiving very good reviews. Do you know why? Industry 4.0 is crucial for manufacturing as it enhances efficiency, flexibility, and productivity on a similar scale. If they can employ smart technologies, manufacturers can optimise production processes, reduce waste, and improve product quality to an extent where it can’t be done through traditional technologies.
- However, the main reason behind its demand is that Industry 4.0 enables real-time monitoring of machines and supply chains. This leads to proactive maintenance and better decision-making from the manufacturer’s end.
- The time is over when manufacturers have to encounter challenges such as high production costs, quality control issues, and supply chain disruptions. With Industry 4.0, they can successfully address them, ensuring competitiveness in the global market.
- If the truth is spoken, Industry 4.0 clearly revolutionises manufacturing by making it smarter, more connected, and better equipped to meet the demands of the modern world.
What is Lean Manufacturing?
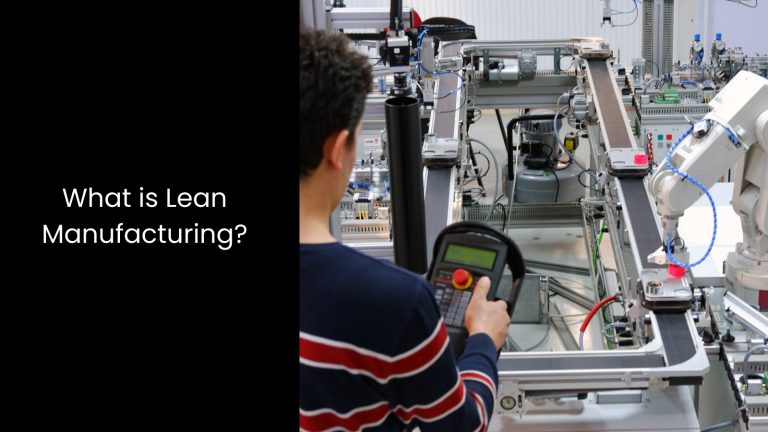
- Lean manufacturing is a production philosophy focused on minimising waste and maximising efficiency throughout the manufacturing process.
- Unlike traditional manufacturing methods that prioritise mass production and large inventories, lean manufacturing emphasises continuous improvement, just-in-time production, and value stream mapping.
- It aims to eliminate activities that do not add value to the product, such as overproduction, waiting times, unnecessary transportation, excess inventory, overprocessing, and defects.
- This approach results in reduced lead times, lower costs, improved quality, and increased customer satisfaction. Plus, lean manufacturing is popular because it enables companies to respond quickly to changing customer demands, adapt to market fluctuations, and stay competitive in a dynamic business environment.
- It is commonly applied in industries producing standardised products with high volume and low variability, such as automotive, electronics, and consumer goods.
- However, just like any other business model, lean manufacturing has challenges. This includes resistance to change, employee training, maintaining supplier relationships, balancing cost reduction with quality improvement, etc. This is where lean manufacturing is desperately in need of an innovative concept like Industry 4.0.
Key Ways Industry 4.0 Impacts Lean Manufacturing in Singapore
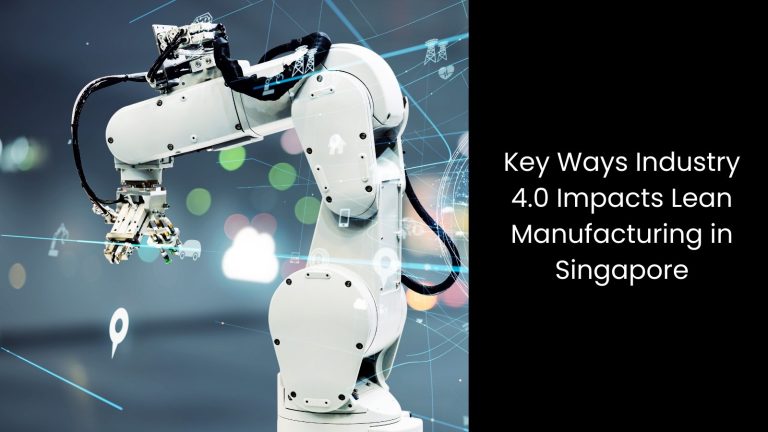
Predictive Maintenance
Manufacturing is a realm that gives a high-scale value to predictions and foreseeing capacity. This is where they should opt for Industry 4.0.
With IoT sensors embedded in manufacturing equipment, companies can closely monitor the health and performance of their machines in real-time. This means that by analysing data using predictive analytics algorithms, manufacturers can foresee potential equipment failures before they even happen.
You can call this a proactive strategy. Yes, it allows them to schedule maintenance in advance, preventing unplanned downtime and disruptions to production. As a result, overall equipment effectiveness (OEE) is greatly enhanced, leading to increased productivity and reduced waste.
More and more manufacturing organisations in Singapore tend to go with the flow of Industry 4.0 due to the same reason. This combination of Industry 4.0 and lean manufacturing principles enables Singaporean companies to maintain high levels of efficiency and competitiveness in the global market.
Smart Manufacturing Systems
In the realm of lean manufacturing, Industry 4.0 brings forth transformative impacts through the implementation of smart manufacturing systems. Let us elaborate on this.
When they have Industry 4.0 implemented, different production systems like machines, robots, and software applications can seamlessly integrate into interconnected smart manufacturing systems. These systems have the capability to autonomously adapt production processes in response to real-time changes in demand, quality concerns, and resource availability.
With this capacity in hand, production can swiftly adjust to fluctuations in demand. They can ensure that resources are utilised efficiently and production goals are met effectively.
The interconnected nature of these smart systems encourages enhanced agility, responsiveness, and overall production efficiency within lean manufacturing environments.
It is evident that by utilising the power of Industry 4.0 technologies, lean manufacturers can optimise their operations, minimise waste, and remain competitive in the ever-evolving global market landscape, which is their sole desire. The best thing about this integration is that it not only streamlines production processes but also creates a dynamic environment where continuous improvement and innovation occur.
Digital Twin Technology
Every manufacturer’s dream is to see new developments in their products. Lean manufacturers are no exception in this case. However, the research and development process does not come inexpensively in today’s world. This is why lean manufacturers increasingly narrow down towards Industry 4.0 digital capabilities.
Industry 4.0 offers Digital Twin technology, where there are virtual copies of real-world assets, processes, or systems, facilitating real-time monitoring, analysis, and optimisation. If they have the ability to craft digital replicas of manufacturing processes and equipment, lean manufacturers easily gain the ability to simulate diverse scenarios, experiment with process enhancements, and fine-tune production parameters without interrupting ongoing operations.
This empowers them to iteratively refine their processes, identify inefficiencies, and ultimately reduce waste.
Not to mention that Digital Twin technology offers a safe and controlled environment for testing improvements. The latter ensures that any changes implemented in the actual production line are thoroughly optimised for maximum efficiency.
With Industry 4.0 and Digital Twin technology, lean manufacturers smoothly drive towards their goals of operational excellence and waste minimisation in this dynamic business world.
Supply Chain Visibility and Collaboration
This is certainly another way Industry 4.0 brings significant advancements through enhanced supply chain visibility and collaboration. Let’s see how this occurs.
With technologies like blockchain, RFID, and cloud-based platforms, the entire supply chain becomes more transparent and interconnected. In such a scenario, lean manufacturers can monitor the movement of materials, components, and finished products in real-time. This allows them to make informed decisions and respond swiftly to changes in demand or supply.
Further, these technologies encourage a smoother interchange of resources and information by permitting tighter collaboration between suppliers and customers.
Since they can optimise inventory levels, lead times, and order fulfilment processes, lean manufacturers can also minimise waste and improve overall supply chain efficiency. This heightened visibility and collaboration streamline operations in one way, and in another way, it enhances the agility and resilience of the supply chain.
Cerexio-Dominated Industry 4.0 Power for Manufacturing Excellence
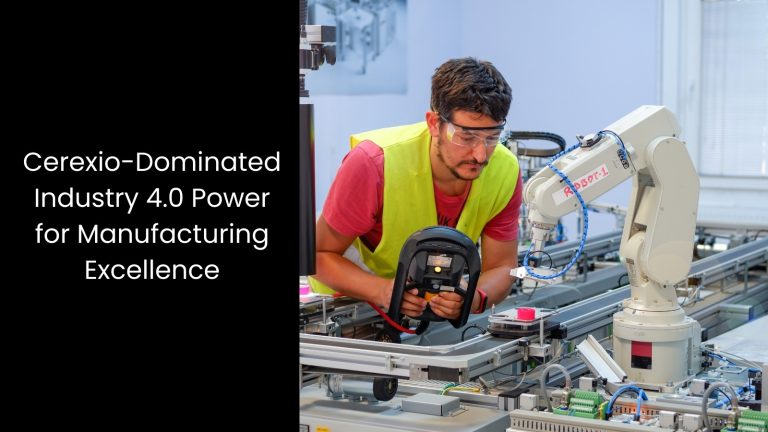
Cerexio offers solutions that are specifically tailored to meet the needs of the Singaporean manufacturing sector, ensuring seamless integration with existing infrastructure and compliance with local regulations. Cerexio empowers Singaporean manufacturers to embrace the future of Industry 4.0. With our industry-leading solutions and commitment to excellence, Cerexio is the ideal partner to propel your manufacturing operations to new heights.
Optimised Lean Manufacturing Culture via Industry 4.0 Strengths
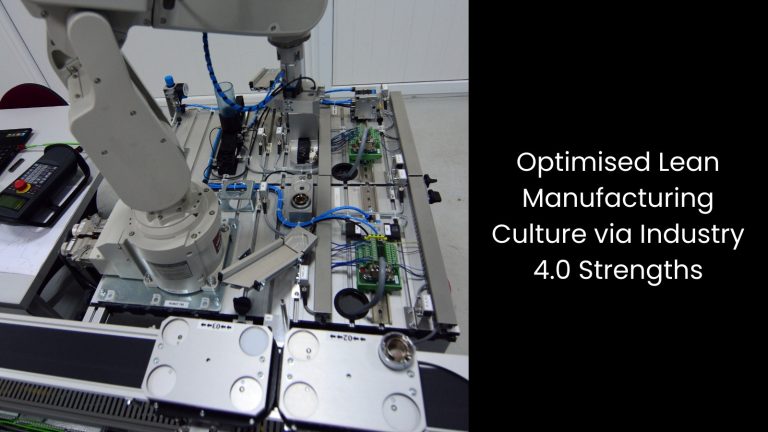
It is not a secret that profitability is the dream of every lean manufacturer. However, balancing efficiency, product quality, and productivity with this aspect is the challenge here. If you opt for the Industry 4.0 framework, there will be no turning back on this competitive business landscape for sure.