Is your manufacturing yield as high as it could be, or is there room to improve? Predictive maintenance could be the missing link to reaching your production goals. What do you think? With technology that identifies potential machine failures before they occur, manufacturers can reduce downtime, extend the lifespan of equipment, and maintain peak efficiency.
This article will explore how predictive maintenance empowers factories to not only meet but exceed expectations, resulting in higher manufacturing yield at the end of the day.
This article will explore how predictive maintenance empowers factories to not only meet but exceed expectations, resulting in higher manufacturing yield at the end of the day.
What is Predictive Maintenance?
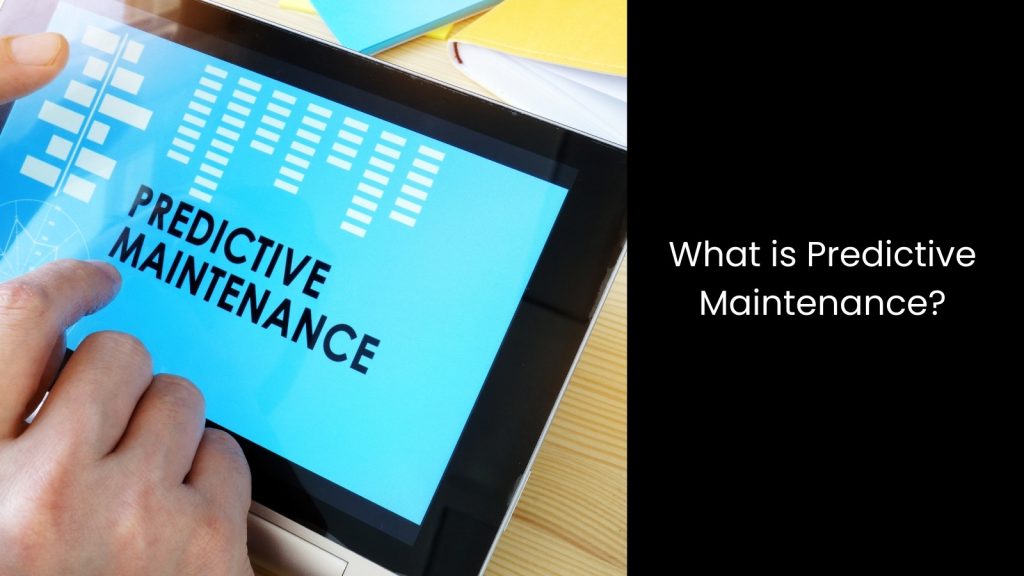
- Predictive maintenance is a process of checking machines regularly using smart tools like sensors, AI, and data analytics to catch problems before they cause breakdowns. It works like a health tracker for equipment, where real-time monitoring and performance tracking help manufacturers fix issues before they turn into bigger troubles.
- Instead of waiting for something to break or just guessing when to do maintenance, maintenance teams now use machine data, vibration checks, temperature readings, and usage patterns to figure out the best time for repairs.
- This helps stop sudden downtime, save money, and keep production lines running smoothly.
- Manufacturers need predictive maintenance since modern machines cost a lot to fix, and every minute of machine failure means lost time and wasted materials. It supports better equipment reliability, longer machine life, and smarter decision-making.
- Plus, predictive maintenance software connects easily with other factory systems, making it easier to control everything from one place. This makes daily operations smoother, more efficient, and more predictable without wasting time on guesswork or emergency fixes.
How to Employ Predictive Maintenance to Achieve Higher Manufacturing Yield
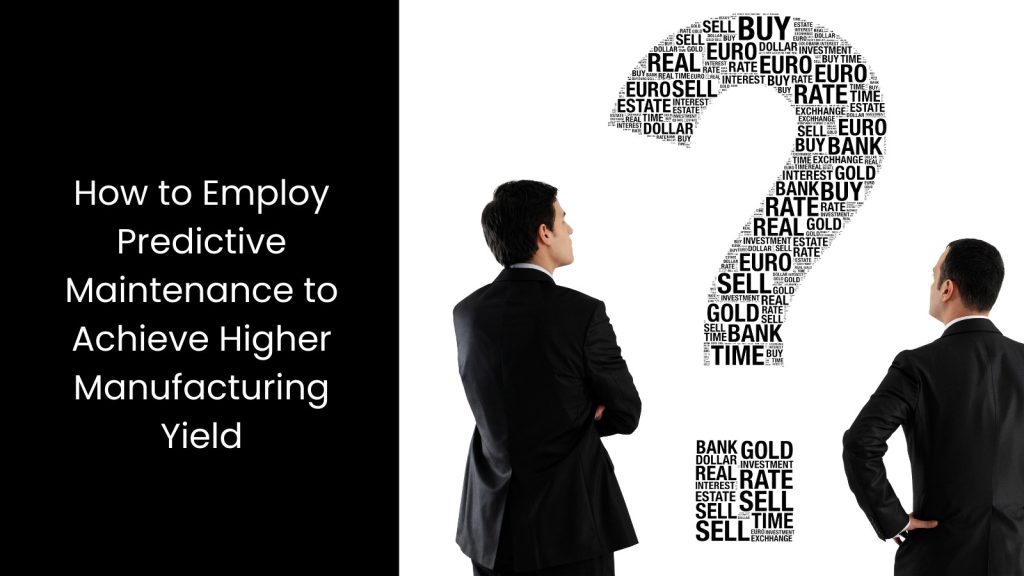
Install IoT Sensors on Equipment
This gives businesses a smart and hands-on way to increase yield through predictive maintenance.
These small yet powerful devices track real-time data like temperature, pressure, vibration, noise, and machine speed directly from the machines without interrupting production. As these sensors collect continuous updates, they help operators spot unusual activity before it turns into equipment failure or production loss.
Instead of relying on guesswork or waiting for something to break, manufacturers can use these insights to plan maintenance when it truly matters. This means less downtime, fewer surprises, and more time spent actually making products.
Also, IoT sensors feed data into predictive maintenance systems, which helps detect wear-and-tear patterns and hidden issues that humans might miss. When machines start acting strangely, maybe heating up too fast or shaking more than usual, these sensors send alerts right away so engineers can respond fast.
This keeps operations steady, improves machine health, and supports higher output with fewer wasted materials.
These small yet powerful devices track real-time data like temperature, pressure, vibration, noise, and machine speed directly from the machines without interrupting production. As these sensors collect continuous updates, they help operators spot unusual activity before it turns into equipment failure or production loss.
Instead of relying on guesswork or waiting for something to break, manufacturers can use these insights to plan maintenance when it truly matters. This means less downtime, fewer surprises, and more time spent actually making products.
Also, IoT sensors feed data into predictive maintenance systems, which helps detect wear-and-tear patterns and hidden issues that humans might miss. When machines start acting strangely, maybe heating up too fast or shaking more than usual, these sensors send alerts right away so engineers can respond fast.
This keeps operations steady, improves machine health, and supports higher output with fewer wasted materials.
Conduct Vibration Analysis
Every machine creates a normal vibration pattern when it runs smoothly, but when something inside starts going wrong, like loose parts, misalignment, or worn-out bearings, the vibration changes. Vibration sensors pick up these small shifts and send that data to predictive maintenance software, which then alerts technicians to take a closer look.
This means teams do not have to wait for weird noises or total breakdowns to know something’s wrong.
Instead, they can step in early and fix the issue while it is still small. This keeps machines running longer and more efficiently, which means less wasted time, fewer defective products, and more units coming off the line.
Plus, vibration analysis does not slow things down since sensors can monitor machines while they run. Manufacturers also save money because they avoid major repairs and unplanned stops. On the other hand, this method helps with tracking how machines wear out over time, so planners can decide exactly when to schedule repairs or replacements.
The data from vibration analysis works well with other predictive maintenance tools, creating a full picture of machine health. Manufacturers that use this approach often notice fewer surprise failures, smoother workflows, and higher output over time.
This means teams do not have to wait for weird noises or total breakdowns to know something’s wrong.
Instead, they can step in early and fix the issue while it is still small. This keeps machines running longer and more efficiently, which means less wasted time, fewer defective products, and more units coming off the line.
Plus, vibration analysis does not slow things down since sensors can monitor machines while they run. Manufacturers also save money because they avoid major repairs and unplanned stops. On the other hand, this method helps with tracking how machines wear out over time, so planners can decide exactly when to schedule repairs or replacements.
The data from vibration analysis works well with other predictive maintenance tools, creating a full picture of machine health. Manufacturers that use this approach often notice fewer surprise failures, smoother workflows, and higher output over time.
Integrate Predictive Tools with ERP Systems
The latter brings machine health data and business operations together in one place. When factories run machines nonstop, they need clear updates on when those machines might fail or slow down.
Predictive maintenance tools track all that using sensor data, and when teams connect those tools with ERP systems, they create a smooth path for smart decision-making. For example, if a machine shows signs of wear, the predictive system can alert the ERP right away, which then triggers an automatic maintenance schedule, spare part request, or team assignment, all without delay.
This keeps machines running longer and stops problems from growing into costly breakdowns. It also helps managers see the bigger picture, like how equipment performance affects delivery times, inventory levels, or worker shifts.
Instead of using separate systems that do not talk to each other, teams get to work from one connected dashboard, which saves time and cuts down on confusion. Manufacturers who use this method gain better control over production timelines, reduce waste, and increase output because they catch problems before they mess things up.
Predictive maintenance tools track all that using sensor data, and when teams connect those tools with ERP systems, they create a smooth path for smart decision-making. For example, if a machine shows signs of wear, the predictive system can alert the ERP right away, which then triggers an automatic maintenance schedule, spare part request, or team assignment, all without delay.
This keeps machines running longer and stops problems from growing into costly breakdowns. It also helps managers see the bigger picture, like how equipment performance affects delivery times, inventory levels, or worker shifts.
Instead of using separate systems that do not talk to each other, teams get to work from one connected dashboard, which saves time and cuts down on confusion. Manufacturers who use this method gain better control over production timelines, reduce waste, and increase output because they catch problems before they mess things up.
Establish Failure Mode and Effects Analysis (FMEA)
FMEA works like a deep inspection checklist where teams look at every part of a process or machine and ask, ‘What could go wrong here, how would it happen, and what damage would it cause?’ They then rank each possible issue based on how often it could happen, how serious it would be, and how easy it would be to catch early.
This helps teams find the riskiest problems and fix them before they mess with production.
When used with predictive maintenance tools, FMEA becomes even more powerful.
Sensors and machine data give real-time warnings, while FMEA tells workers where to look first and what to do next. That combo helps factories avoid breakdowns, cut waste, and keep machines running longer.
This helps teams find the riskiest problems and fix them before they mess with production.
When used with predictive maintenance tools, FMEA becomes even more powerful.
Sensors and machine data give real-time warnings, while FMEA tells workers where to look first and what to do next. That combo helps factories avoid breakdowns, cut waste, and keep machines running longer.
Automate Maintenance Alerts and Workflows
Instead of waiting for something to go wrong or manually checking equipment, manufacturers can set up smart systems that watch machine health and instantly send alerts when something looks off. These alerts go straight to the right people, like technicians, managers, or inventory teams.
So they can jump into action without delays.
This is when predictive maintenance tools track real-time data like temperature, noise, or vibration, and when they spot strange patterns, the system creates a task, sends reminders, and updates the maintenance schedule automatically.
This keeps everyone on the same page and avoids last-minute chaos. It also helps teams fix small issues before they become big disasters, which keeps production lines moving smoothly and avoids waste.
Plus, automated workflows mean no one forgets a step or skips a part of the repair process, which improves machine care and reduces human error. Over time, this smart system learns from past alerts and gets better at predicting future problems, which boosts accuracy and saves time.
So they can jump into action without delays.
This is when predictive maintenance tools track real-time data like temperature, noise, or vibration, and when they spot strange patterns, the system creates a task, sends reminders, and updates the maintenance schedule automatically.
This keeps everyone on the same page and avoids last-minute chaos. It also helps teams fix small issues before they become big disasters, which keeps production lines moving smoothly and avoids waste.
Plus, automated workflows mean no one forgets a step or skips a part of the repair process, which improves machine care and reduces human error. Over time, this smart system learns from past alerts and gets better at predicting future problems, which boosts accuracy and saves time.
Cerexio Solution to Boost Manufacturing Yield
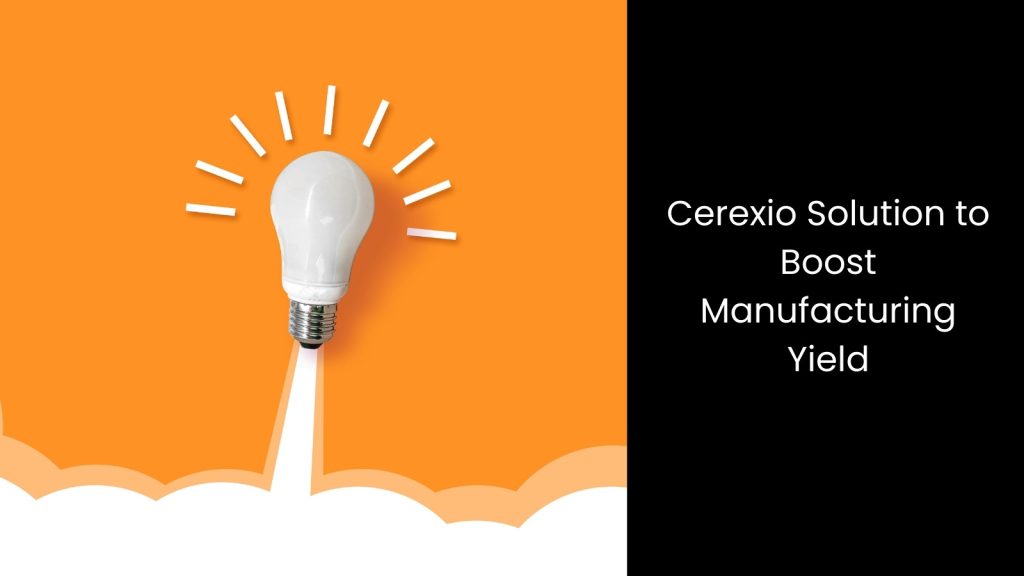
Cerexio offers an Industry 4.0-powered manufacturing yield-optimising software that boosts output by using real-time data, predictive maintenance, and smart automation. Our product spots issues early, reduces downtime, and improves machine efficiency. With its connected system and accurate insights, manufacturers can fix problems fast, fine-tune processes, and keep production running at its best.
Collaborating High-End Tech to Maximise Manufacturing Yield Easily
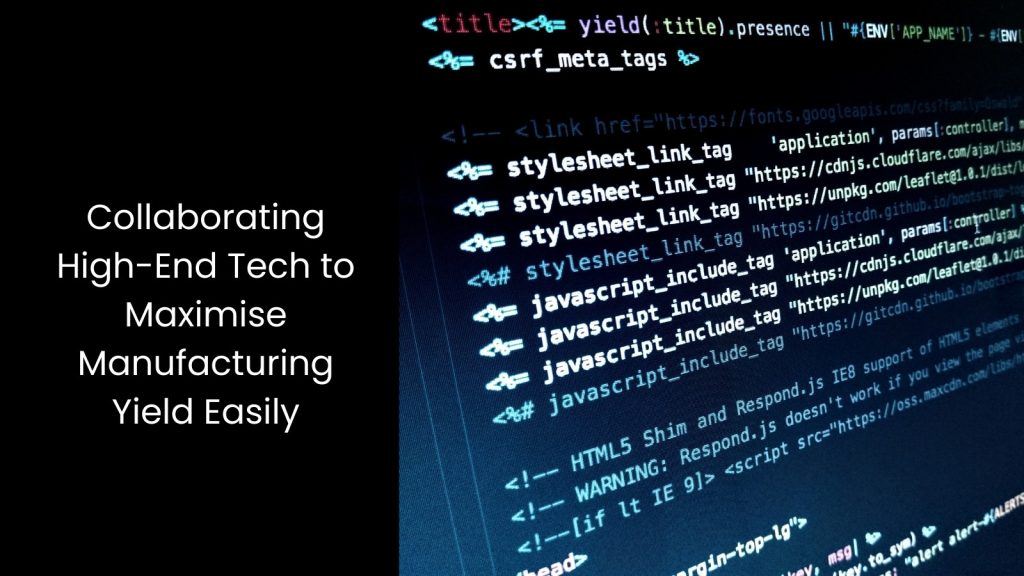
Teaming up high-end technology with smart processes gives manufacturers a strong way to boost yield without adding stress. When systems communicate, data flows smoothly, and predictive tools stay active, teams avoid downtime and waste. The future of easy, efficient production starts with the right tech working together.