Can you limit the manufacturing operational process to one aspect? The answer is an obvious ‘no’! It is common knowledge that the manufacturing business consists of various stages where the materials float through, and the final output comes in at the expected quality. Can you guess how much information we are gathering throughout this whole process? The truth is the data collection is uncountable. This is where the manufacturing industry is in need of the ‘Big Data Management’ concept.
In this article, we explore the technology of ‘Big Data’ and look into the importance of having this cutting-edge technology in the manufacturing business realm.
What is Big Data Management?
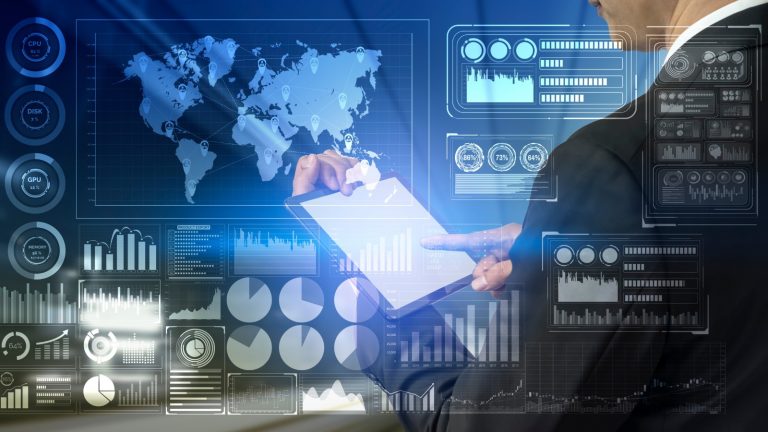
This refers to the process of collecting, storing, organising, and analysing large volumes of complex and diverse data sets.
It encompasses strategies and technologies aimed at handling the immense volume, velocity, and variety of data generated from various sources within an organisation. This includes structured and unstructured data from machines, sensors, transactions, social media, and more.
The goal is to derive meaningful insights and actionable information from this data, enabling informed decision-making, enhancing operational efficiency, and driving innovation. Big Data Management involves robust infrastructure, data governance, integration tools, analytics, and visualisation techniques to process and interpret data, ultimately extracting valuable insights to gain a competitive edge, improve processes, and better understand customer behaviours and market trends.
In the business world, Big Data Management drives informed decisions by analysing vast data sets. It enhances operations, customer insights, and innovation. By optimising processes, predicting trends, and improving efficiencies, it fosters competitiveness and strategic growth in dynamic markets.
Top 6 Benefits of Big Data Management in Manufacturing
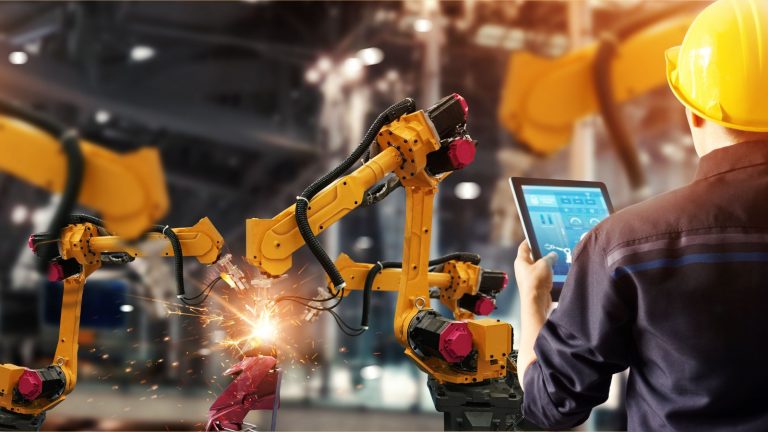
Quality Control
Big Data Management empowers manufacturers to control production quality by integrating data from various sources like sensors, machines, and production lines. Through real-time analysis, it identifies patterns and anomalies, enabling swift corrective actions to maintain stringent quality standards.
Predictive analytics forecast potential quality issues, allowing preemptive measures to avoid defects. Historical data analysis helps in continuous improvement by understanding past flaws and refining processes. Additionally, it facilitates predictive maintenance, ensuring equipment functions optimally and reducing breakdowns that might affect product quality.
By harnessing these insights, manufacturers can streamline operations, enhance product consistency, minimise defects, and uphold quality, ultimately fostering customer trust and loyalty while staying competitive in the market.
Customisation and Personalisation
It helps manufacturers offer customisation and personalisation by analysing vast datasets encompassing customer preferences, market trends, and production capabilities. Through predictive analytics, it identifies individual preferences and market demands, allowing for tailored production runs. Customer data analysis facilitates understanding specific needs, aiding in product customisation.
Real-time data monitoring during production enables agile adjustments to meet personalised requirements without compromising efficiency. This approach enhances customer satisfaction by fostering brand loyalty and market competitiveness. Moreover, by leveraging insights from customer feedback and purchasing behaviour, manufacturers refine their offerings, launching targeted products that resonate with diverse consumer segments.
Ultimately, Big Data Management empowers manufacturers to deliver personalised experiences, meeting the dynamic demands of consumers while optimising production processes for greater flexibility and responsiveness.
Cost Reduction
Big Data Management contributes significantly to cost reduction in manufacturing by optimising operations and resource allocation. Through data analytics, it identifies inefficiencies, streamlines processes, and minimises waste. Predictive maintenance prevents unexpected breakdowns, reducing downtime and associated repair costs.
Real-time monitoring of equipment and supply chain data allows for efficient inventory management, avoiding overstocking or shortages. Analysis of energy usage patterns helps in optimising consumption and cutting utility expenses. Additionally, data-driven insights aid in sourcing decisions, negotiating better deals with suppliers, and identifying areas for process improvement, which collectively reduce unnecessary expenditures.
By harnessing these insights, manufacturers can enhance operational efficiency, optimise spending, and make informed decisions, ultimately trimming costs across various facets of their operations while maintaining or improving product quality.
Supply Chain Optimisation
This revolutionises supply chain optimisation for manufacturers by providing comprehensive insights into every aspect of the supply network. It integrates data from multiple sources, offering real-time visibility into inventory levels, supplier performance, transportation routes, and market demand. Predictive analytics anticipate fluctuations, enabling proactive adjustments in inventory levels and production schedules to meet demand while minimising excess stock.
Through data-driven insights, it identifies bottlenecks or inefficiencies, facilitating smoother logistics and timely deliveries. Moreover, historical data analysis aids in risk mitigation by foreseeing potential disruptions, allowing for contingency planning.
Collaborative data sharing among stakeholders fosters transparency and coordination, optimising the entire supply chain. Ultimately, Big Data Management empowers manufacturers to enhance agility, responsiveness, and efficiency in their supply chain operations, reducing costs and improving customer satisfaction.
Optimised Production
This optimises overall production for manufacturers by leveraging data-driven insights across the production lifecycle. It integrates data from machines, processes, and quality control to identify inefficiencies, bottlenecks, and areas for improvement.
Predictive analytics forecast demand patterns, enabling precise production planning and resource allocation. Real-time monitoring of equipment performance allows for preventive maintenance, reducing downtime, and enhancing operational efficiency. Continuous analysis of production data facilitates fine-tuning of processes, improving yield rates, and minimising waste. Additionally, it enables adaptive manufacturing, swiftly adjusting production in response to market changes or customer demands.
Collaborative data sharing among departments fosters a cohesive production ecosystem, enhancing coordination and agility. Ultimately, Big Data Management optimises production by refining processes, ensuring resource efficiency, and enabling responsiveness to dynamic market conditions, fostering a competitive edge for manufacturers.
Risk Management
The latter equips manufacturers with robust risk management capabilities by analysing diverse data sets to identify, assess, and mitigate risks across their operations. Through predictive analytics, it forecasts potential risks in supply chains, market demands, or operational disruptions.
Real-time monitoring of data detects anomalies, allowing for immediate responses to mitigate emerging risks. Historical data analysis aids in understanding past failures and refining strategies to avoid similar risks in the future. By integrating data from various sources, it provides a holistic view of potential vulnerabilities, enabling proactive risk mitigation strategies.
Additionally, Big Data Management facilitates compliance monitoring, ensuring adherence to regulations, thereby reducing legal and regulatory risks. Overall, it enables manufacturers to anticipate, assess, and respond to risks effectively, fostering resilience and adaptability in an ever-evolving business landscape.
Cerexio Big Data Technology
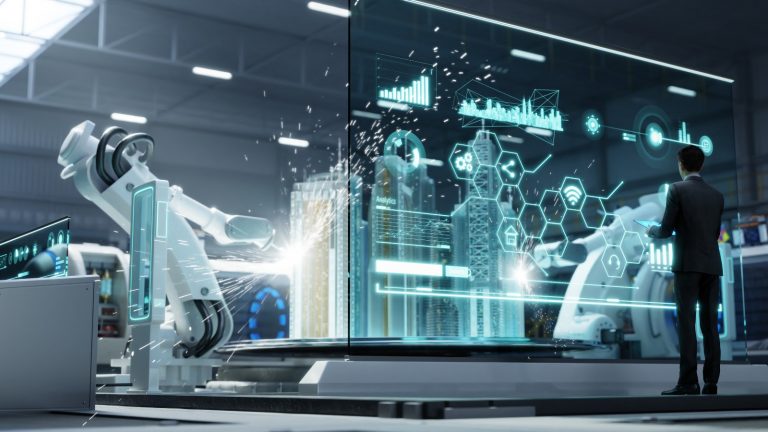
Understanding how important it is for you to establish a data-driven culture inside your business, Cerexio is presenting our Industry 4.0-powered ‘Big Data Technology’, where we offer smart Big Data solutions specifically tailored to user-defined needs. Our tools filter complex data structures, making them accessible for modern technology. These solutions assist in capturing actionable insights as well. Cerexio emphasises data handling, cleansing, and security features. If you are interested in gaining more knowledge about this, you can connect with our team to explore how these innovations enhance your manufacturing business operations.
Embracing an Unlimited Vision with Big Data Management
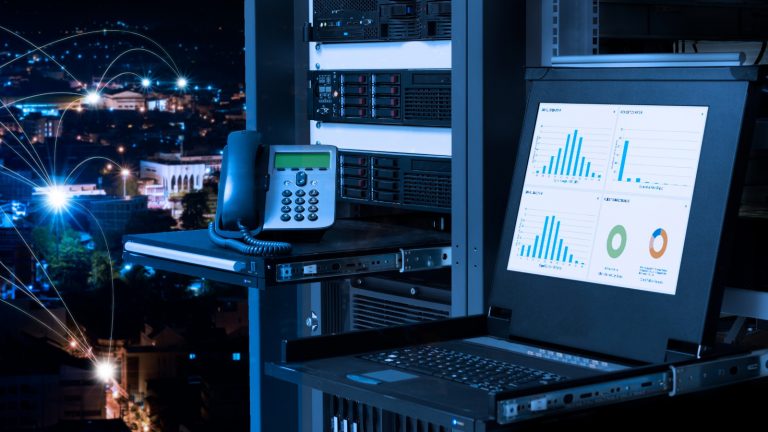
It is common for a manufacturing business to encounter various obstacles when collecting and analysing large sets of data due to the complex nature of the business. However, it is highly important to have a unified view of these data sets without missing any tiny detail that will affect the quality of the final decision. The ‘Big Data Technology’ comes to the rescue of manufacturing businesses with its cutting-edge functionalities, simplifying decision-making at the end. However, when you purchase a software solution like ‘Big Data’, you should take its features into account before making the final judgement. Collaboration with a reputed supplier will be the most convenient path you can choose.