Singapore holds a global manufacturing hub status making it one of the leading players in the manufacturing world. But did you know that according to statistics in 2021, the manufacturing industry is responsible for producing 46 per cent of primary emissions and 14 per cent of secondary emissions? Amidst threats of climate change and the Singapore government’s goal to reduce carbon emissions, the manufacturing industry is one of the sectors at the forefront that needs to be more sustainable. One feasible solution for this is to transition to lean manufacturing, which refers to a production process that strives to maximise productivity in parallel to minimising waste. This blog will explain everything you need to know about lean manufacturing.
What is Lean Manufacturing?
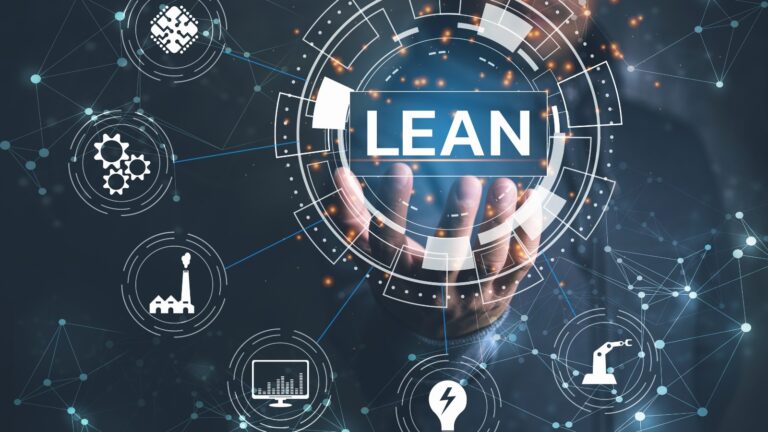
Lean manufacturing is a form of philosophy integrated into manufacturing processes. Although the term ‘lean manufacturing’ originated in 1998 by John Krafcik, it has been a concept for a long time. It was Benjamin Franklin that formally conceptualised lean manufacturing in his essay ‘The Way to Wealth’, after which Fedrick Winslow Taylor expanded it by presenting it as a scientific management process in his book, the ‘Principles of Scientific Management’. Accordingly, lean manufacturing was seen as a process whereby, whenever a workman proposed an improvement, the management as a policy would analyse it and conduct experiments (where needed) to compare it with the old standard. If the new suggested standard is found to be better, Taylor notes that it would be in the company’s best interest to adopt it as the new standard for the establishment. While the history demonstrates the theoretical aspect of lean manufacturing, it was first implemented most successfully by Toyota Motor Corporation in Japan. The primary motivation behind this was that Japan did not have the financial means to produce waste after the second world war.
The Three Types of Waste
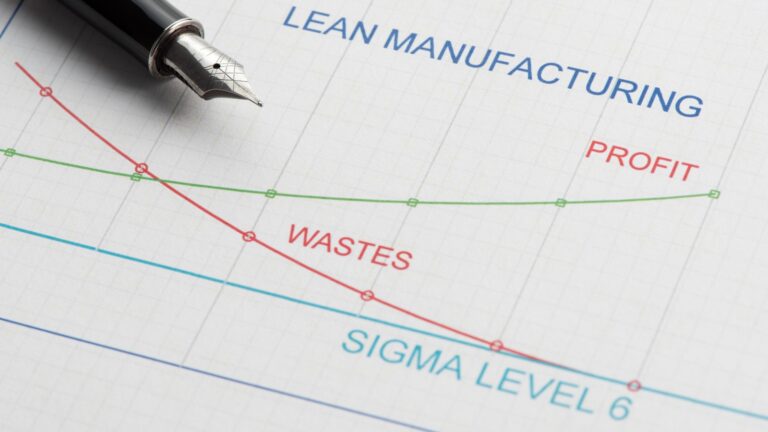
Toyota identified three broad types of waste, including Mura, Muri and Muda. It is helpful to understand what they are to assess the multiple layers of waste typically present in a company.
- Mura: This is waste that results from increased demand for new products or services.
- Muri: Refers to waste generated due to a company’s stubborn attempt to do too much. Hence, when employees have to work overtime, handle multiple roles and are overburdened with work, resources and valuable time is wasted.
- Muda: Any steps within the process that had not amounted to Muda waste. For it to be regarded as necessary, the step needs to either have value on its own or support a step that does have value.
Principles of Lean Manufacturing

Many lean manufacturing principles exist, especially considering that Toyota introduced fourteen. Today they are known as Toyota Production System, which gained prominence after the publication of James Womack and Daniel Jones’s book, ‘Lean Solutions’. According to the book, the principles can broadly be categorised into the following five:
Value
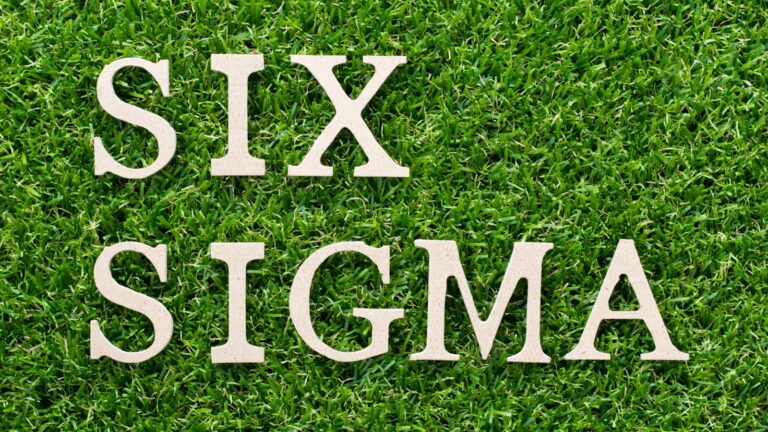
What a company values may vastly differ from what a customer values. Therefore, In the context of lean manufacturing, manufacturers should only consider value from the customer’s point of view. This requires manufacturers to find out what their consumers feel is valuable in their products, specifically in terms of what drives them to purchase them. Understanding this is crucial to increasing an organisation’s sales as it is based on this, for instance, that the target price would be set. This is the starting step to designing and constructing a plan to adopt lean manufacturing within an organisation. A helpful framework to identify value includes the Design for Six Sigma (DFSS).
Value Streams
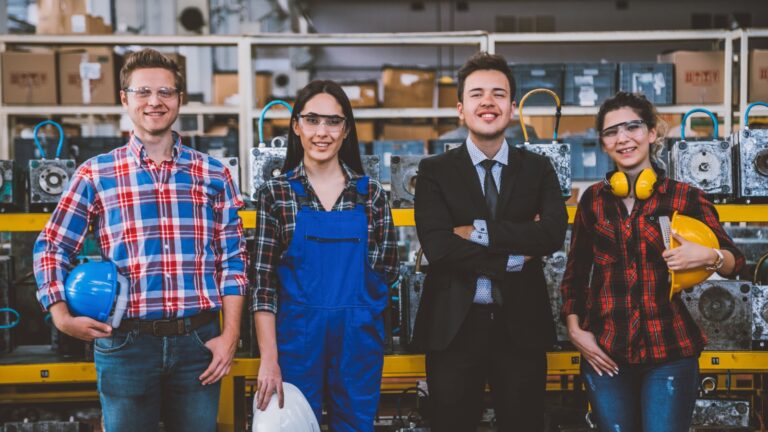
A value stream refers to the end-to-end lifecycle of a complete product or service. From the product’s inception to when it is sent to the supply chain, the production process and afterwards delivered to the consumer, the product’s lifecycle also requires the disposal of the item to be considered. By comprehensively detailing all value streams, managers need to first identify where waste could potentially generate. Consequently, teams can discuss, formulate, adopt and evaluate whether certain steps within the entire process can be eliminated based on whether they generate waste. An easy way to do this is by adopting a Value Stream Mapping (VSM) framework, which refers to visually mapping out the entire product flow as a flowchart.
Flow
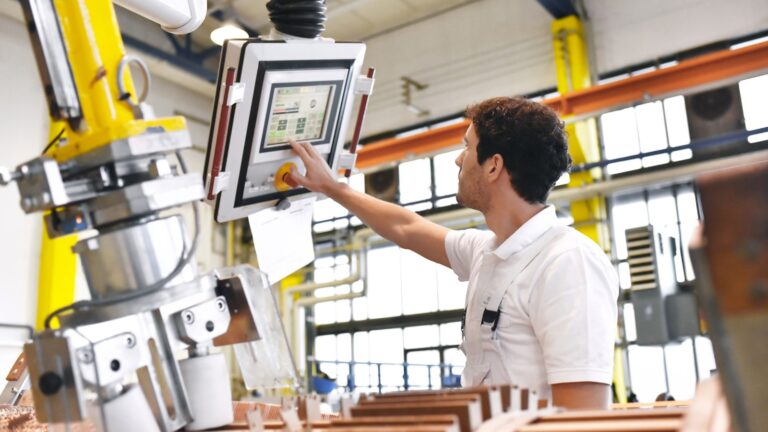
Flow refers to the constant movement within the value stream. In other words, manufacturers must assess whether items move from one stage to another without interruption. Every time the flow is halted, waste is created as time is lost, or any extra movement is followed by wasted energy or storage space. This affects the overall lifecycle of value streams as the customer’s value is disrupted and efficiency is decreased. One way to address this is by focusing on ‘levelized production’, which specifically ensures energy is used in an eco-friendly manner. As a result, moving away from practices that centre on batch or siloed production, which require more energy, will help manufacturers be more efficient and reduce energy waste.
Pull
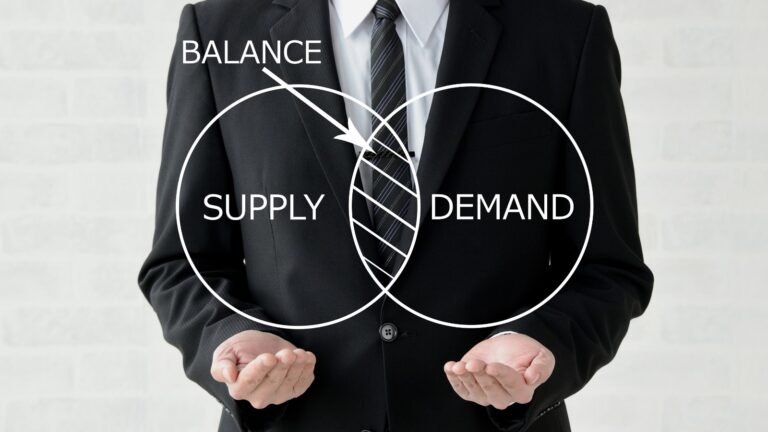
Traditionally, manufacturers rely on forecasts when producing items. Hence based on the estimated number of sales, manufacturers would purchase raw materials and keep their inventories stocked. However, in reality, companies may experience either fewer or higher number of sales than expected. Both scenarios, unfortunately, generate waste. Where sales are low, the number of goods made go to waste, whereas when it is high, the added costs incurred for last-moment purchases required to keep up with production could result in other forms of waste being created. In a pull system, manufacturers avoid making decisions on predictions. Instead, orders are readied based on their quantified demand from consumers. This may not be the easiest to adopt if the factory lacks flexibility.
Perfection
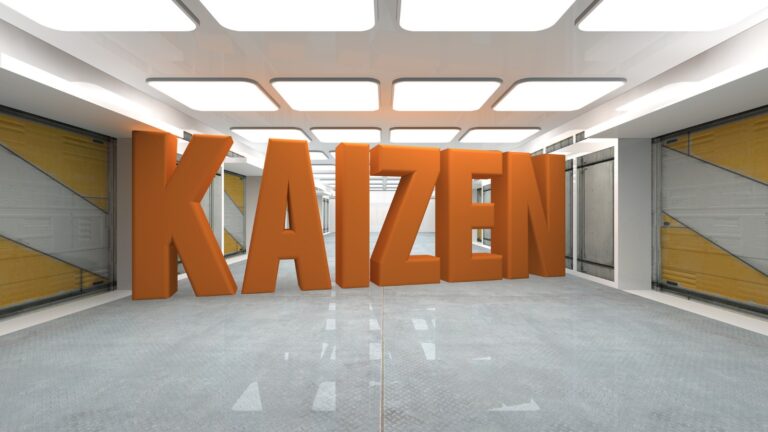
Although this may seem like an abstract principle, perfection refers to a manufacturing company’s drive to consistently improve by following an upward spiral of efficiency, profitability and customer satisfaction. This highlights the need to follow through with the previous four principles and demonstrates how employees in the manufacturing company themselves need to change. In terms of the latter, perfection can be achieved if there is a shift in the workplace culture and mindset. As perfection never comes easy, this is often regarded as the hardest principle to apply in a manufacturing organisation. Drawing from the Japanese principle of Kaizen, however, perfection can be achieved if all employees, from the CEO to assembly line workers, strive to make small improvements in each stage of the manufacturing process.
Cerexio MES: A Start to Your Sustainable Manufacturing Journey
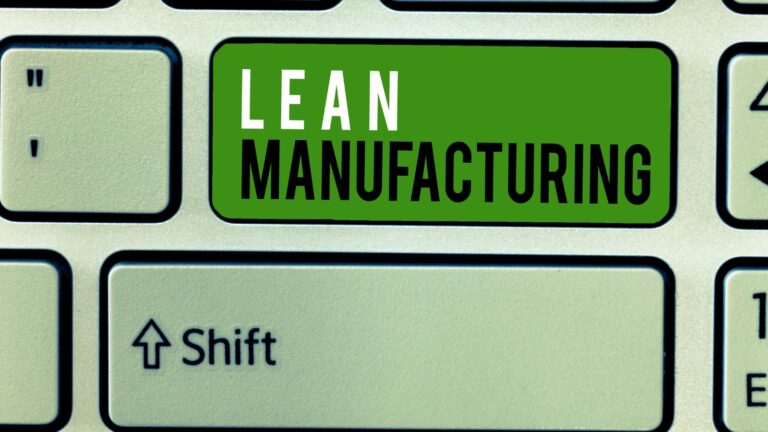
Cerexio MES is the perfect solution for those who want to easily adopt lean manufacturing principles in their factory. It is embedded with advanced technologies such as Artificial Intelligence, Machine Learning, predictive and prescriptive analytics, digital twin and more.
Connect with Cerexio to learn how else our robust solution suite can help you conduct manufacturing processes sustainably.
Lean Manufacturing: A Philosophy for Sustainability and Success
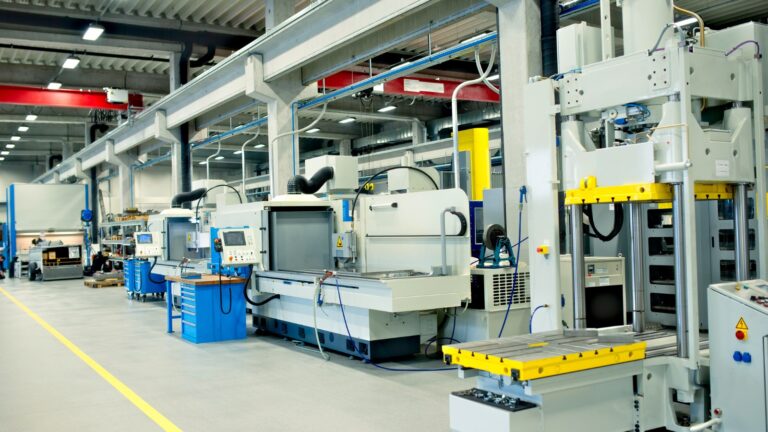
At the essence of lean manufacturing is the idea that waste does not add value to what a customer is willing to pay. Hence, those who embrace this form of manufacturing attempt to eliminate waste completely. This is done by removing processes, services, products and activities that incur high expenses and require a lot of time. Waste also includes underused talent and excess inventory. Therefore, the core aim of a company adopting lean manufacturing is to consider how they can do more with less human effort, equipment, time and space, thereby providing customers exclusively what they want. Thus, not only can lean manufacturing be regarded as a philosophy that rids waste to benefit the environment, but it also significantly contributes to a company’s success as profits are maximised, and the quality of products is improved.