Manufacturing is a fine balance between meeting deadlines and maintaining product excellence. While the race to keep up with demand is pretty constant, there is one factor that determines whether a company sinks or swims. That is ‘quality management’. But what does quality management really mean, and what keeps it running smoothly? It is not just about checking boxes or running a few tests. The process involves several key elements working together to ensure products not only meet expectations but exceed them. Want to know what truly drives quality in manufacturing?
Let this blog article explore the four core components that bring quality management to life in manufacturing.
Let this blog article explore the four core components that bring quality management to life in manufacturing.
Why is Quality Management Important in Manufacturing?
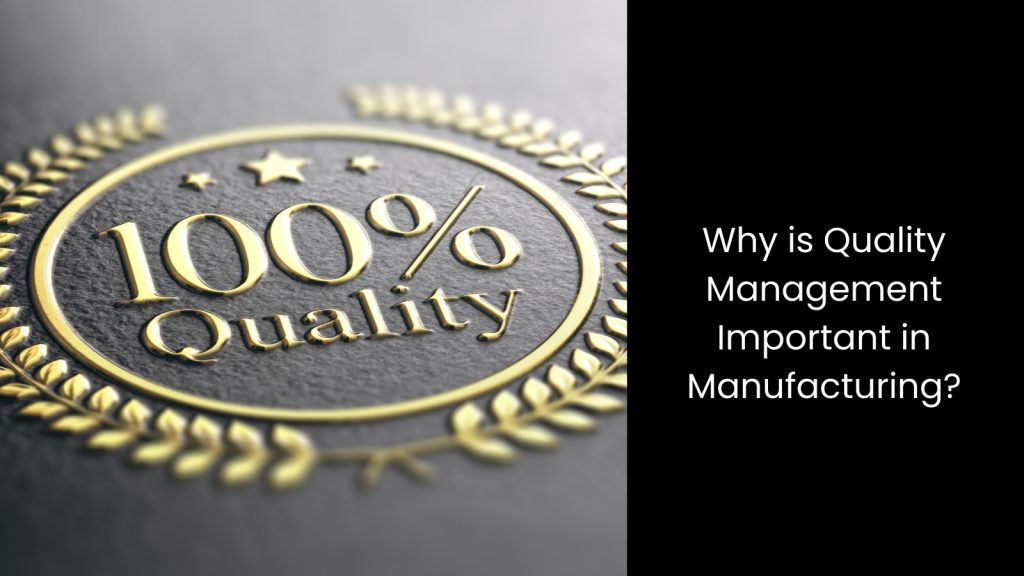
- As much as we put pressure on production, we need to make sure every product meets high standards, or the entire process falls apart.
- The problem with traditional manufacturing quality management is that it relies on manual inspections, routine sampling, and set guidelines, but this old-school method comes with plenty of headaches. Human error, inconsistent checks, and delays in identifying defects cause massive waste, rework, and financial losses.
- Many factories also rush production, and they think speed matters more than precision. However, skipping proper inspections unknowingly leads to defects slipping through. When factories do not check quality properly, faulty products reach customers, damaging trust and leading to complaints, recalls, and revenue loss.
- Workers in traditional settings usually miss hidden issues, and companies relying too much on fixed procedures struggle to adapt when production scales or new materials come in. Some even focus only on end-product testing and ignore process monitoring. This means defects pile up unnoticed.
- Without strong quality control, supply chains suffer, and faulty parts create expensive breakdowns.
- As you can see, quality management is not just a factory task. It literally decides whether a manufacturing business succeeds or crashes.
4 Components of Quality Management in Manufacturing

Quality Control Planning
The first step starts with quality control planning, where manufacturers set the rules to keep production on track and prevent defects before they happen.
Every factory needs a clear plan that decides what to check, how to measure quality, and which standards to follow. Engineers and managers can work together to map out inspection points, testing methods, and acceptable limits for defects.
Without a solid plan, workers guess their way through quality checks. This will lead to inconsistent results and wasted materials. This is why many factories set up control charts, sampling methods, and standard operating procedures to catch mistakes early, but a weak plan leaves gaps that allow poor-quality products to slip through.
Plus, some companies focus too much on end-product testing, forgetting that real control starts during the production process. If a machine runs slightly off or raw materials contain flaws, unchecked defects multiply down the line, causing costly rework and delays.
Further, quality control planning also helps teams prepare for unexpected problems, such as sudden material shortages or equipment malfunctions, which can throw off production.
Experts have found that factories that skip this step tend to deal with production bottlenecks, customer complaints, and wasted resources.
Every factory needs a clear plan that decides what to check, how to measure quality, and which standards to follow. Engineers and managers can work together to map out inspection points, testing methods, and acceptable limits for defects.
Without a solid plan, workers guess their way through quality checks. This will lead to inconsistent results and wasted materials. This is why many factories set up control charts, sampling methods, and standard operating procedures to catch mistakes early, but a weak plan leaves gaps that allow poor-quality products to slip through.
Plus, some companies focus too much on end-product testing, forgetting that real control starts during the production process. If a machine runs slightly off or raw materials contain flaws, unchecked defects multiply down the line, causing costly rework and delays.
Further, quality control planning also helps teams prepare for unexpected problems, such as sudden material shortages or equipment malfunctions, which can throw off production.
Experts have found that factories that skip this step tend to deal with production bottlenecks, customer complaints, and wasted resources.
Quality Control
The second phase is quality control, where manufacturers put their quality plan into action and make sure every step of production stays on track.
Inspectors and engineers check raw materials, monitor machines, and test finished products to catch defects before they cause bigger problems. Skipping proper checks at this stage leads to faulty parts stacking up, which means costly rework and wasted time.
Some manufacturers rely too much on manual inspections, but human eyes miss small flaws that automated systems can easily detect. Others only test final products, ignoring issues that start during production, which allows defects to spread undetected. However, if they work with quality control teams, they can set up checkpoints, use measurement tools, and analyse samples to compare against industry standards. If something goes wrong, they adjust machines, change materials, or modify production steps to prevent more defects.
Factories that rush this process might end up dealing with rejected shipments, customer complaints, and supply chain disruptions. Some businesses even ignore small defects, thinking they will not matter. Did you know that those small mistakes are what usually lead to big failures later?
Inspectors and engineers check raw materials, monitor machines, and test finished products to catch defects before they cause bigger problems. Skipping proper checks at this stage leads to faulty parts stacking up, which means costly rework and wasted time.
Some manufacturers rely too much on manual inspections, but human eyes miss small flaws that automated systems can easily detect. Others only test final products, ignoring issues that start during production, which allows defects to spread undetected. However, if they work with quality control teams, they can set up checkpoints, use measurement tools, and analyse samples to compare against industry standards. If something goes wrong, they adjust machines, change materials, or modify production steps to prevent more defects.
Factories that rush this process might end up dealing with rejected shipments, customer complaints, and supply chain disruptions. Some businesses even ignore small defects, thinking they will not matter. Did you know that those small mistakes are what usually lead to big failures later?
Quality Assurance
When it comes to manufacturing quality management, assurance takes a front seat in making sure production runs smoothly without defects sneaking through.
Instead of just fixing problems after they happen, quality assurance focuses on building a system where mistakes rarely occur in the first place. Engineers, supervisors, and production teams work together to design processes, set standards, and create guidelines that keep everything in check.
What would happen if a manufacturing company ran without a proper assurance system? They will end up gambling with product consistency, which may lead to unexpected failures and customer complaints.
Some companies think occasional spot checks are enough, but that outdated approach allows hidden defects to spread unnoticed. This is where quality assurance includes training workers, testing raw materials, calibrating machines, and reviewing production methods to catch risks before they turn into disasters. Ignoring these steps leads to unstable production, where one faulty batch can ruin an entire shipment.
Factories that rush to meet deadlines without checking their processes end up spending more time fixing issues than actually producing.
Assurance does not just focus on finished products, but it looks at every stage, from sourcing materials to final inspections, to make sure everything stays within standard limits. Without this foundation, production turns unpredictable, wasting resources and damaging a company’s reputation.
Instead of just fixing problems after they happen, quality assurance focuses on building a system where mistakes rarely occur in the first place. Engineers, supervisors, and production teams work together to design processes, set standards, and create guidelines that keep everything in check.
What would happen if a manufacturing company ran without a proper assurance system? They will end up gambling with product consistency, which may lead to unexpected failures and customer complaints.
Some companies think occasional spot checks are enough, but that outdated approach allows hidden defects to spread unnoticed. This is where quality assurance includes training workers, testing raw materials, calibrating machines, and reviewing production methods to catch risks before they turn into disasters. Ignoring these steps leads to unstable production, where one faulty batch can ruin an entire shipment.
Factories that rush to meet deadlines without checking their processes end up spending more time fixing issues than actually producing.
Assurance does not just focus on finished products, but it looks at every stage, from sourcing materials to final inspections, to make sure everything stays within standard limits. Without this foundation, production turns unpredictable, wasting resources and damaging a company’s reputation.
Quality Improvement
The last step, or maybe the most essential step, in manufacturing quality management goes to quality improvement. This is when the companies fine-tune their processes to eliminate flaws, boost efficiency, and keep up with evolving standards.
Even the best production lines make mistakes, and ignoring small defects today turns into bigger headaches down the road. Engineers, supervisors, and quality teams dive into performance data, customer feedback, and production reports to spot weak points that need fixing. Factories that resist change get stuck with outdated methods, leading to waste, slow production, and frustrated customers.
Quality improvement focuses on upgrading machinery, refining workflows, training workers, and introducing new technologies that prevent defects instead of just catching them. Ignoring continuous improvement turns production into a guessing game where inconsistencies pile up, increasing costs and damaging reliability.
Without a structured improvement process, companies risk falling behind competitors who constantly refine their operations. A strong quality improvement strategy makes manufacturing smarter, reduces material waste, and ensures products meet the highest standards every time.
Even the best production lines make mistakes, and ignoring small defects today turns into bigger headaches down the road. Engineers, supervisors, and quality teams dive into performance data, customer feedback, and production reports to spot weak points that need fixing. Factories that resist change get stuck with outdated methods, leading to waste, slow production, and frustrated customers.
Quality improvement focuses on upgrading machinery, refining workflows, training workers, and introducing new technologies that prevent defects instead of just catching them. Ignoring continuous improvement turns production into a guessing game where inconsistencies pile up, increasing costs and damaging reliability.
Without a structured improvement process, companies risk falling behind competitors who constantly refine their operations. A strong quality improvement strategy makes manufacturing smarter, reduces material waste, and ensures products meet the highest standards every time.
Cerexio Track & Trace System for Enhanced Manufacturing Quality Management
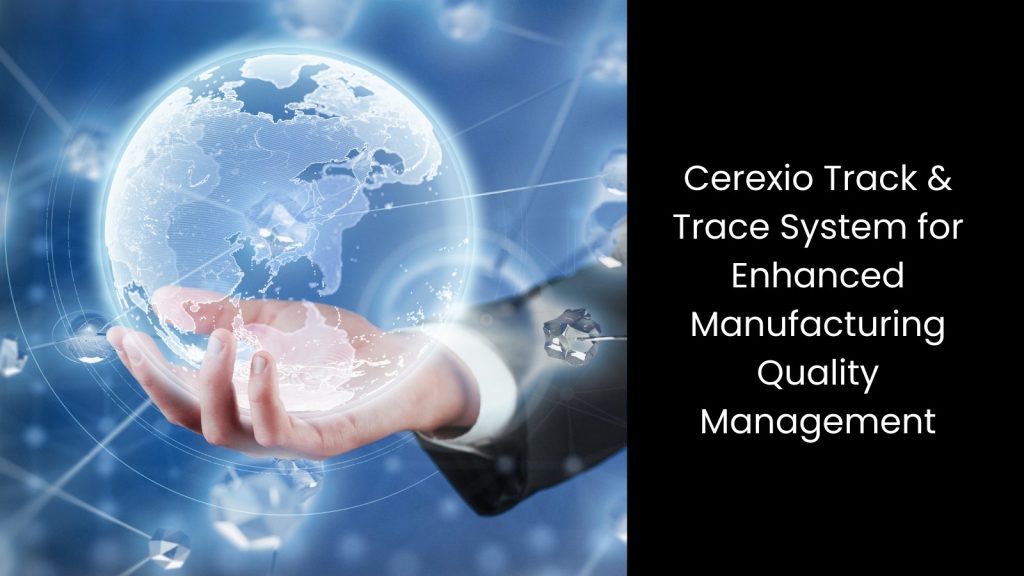
Cerexio introduced our Industry 4.0-powered Track & Trace system for the manufacturing industry to strengthen their quality management initiatives smartly. Our system can monitor materials, track production stages, and ensure product authenticity, all under one roof. With this solution in place, you can reduce defects, prevent recalls, and improve compliance by providing real-time data on every unit.
Ensuring Highest Product Quality in Manufacturing via Right Tools
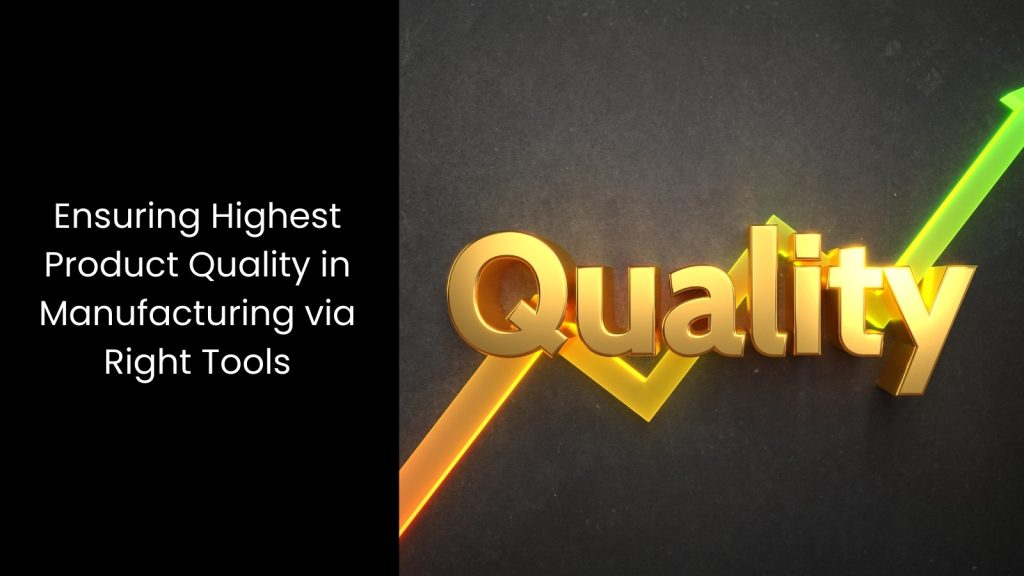
Quality is not a gamble; it equips your manufacturing with the right tools and ensures every product meets the highest standards! With the right tools in hand, you can detect defects early, refine processes, and deliver excellence with precision-driven solutions. Why are you still hesitant? Stay ahead of the competition with flawless quality.