Did you know that manufacturers are haunted by workforce challenges in Australia? It is a well-known fact that the Australian government attracts labourers with lucrative grants and encourages skilled labour growth in the manufacturing sector. This is because labour productivity growth defines the potential of the country’s economic performance and narrates the high living standards of its citizens. However, this is a different story for industrial leaders like factory owners and manufacturing specialists; they have landed in a soup due to hiked up expenses in managing local and international workforces.
The manufacturing industry is highly competitive and dynamic. Therefore, utilising labour in a suboptimal manner can make a manufacturing company unsure of future success. Many manufacturers who fail to meet the desired levels of labour productivity can mean that the quality of labour is poor and is handicapping them from making the best out of technological capabilities and skilled or unskilled workers. Addressing these workforce challenges of manufacturing companies can help them start cutting down otiose labour costs, eliminate nugatory overtime and employ experienced and determined talent confidently.
This article addresses the main challenges of manufacturers in managing and attracting labour and explains how employing innovative, industry 4.0-defined methods to enhance the quality of labour utilisation can help manufacturers thrive in the 21st century.
The 3 Main Labour Conundrums of the Australian Manufacturing Domain
Substandard Employment Quality and Inadequate Working Environments of Offshore Labour Management
The Gen Z Perspective; Millennial Reluctance in Industrial Work
Governments Attract Workers, but Manufacturing Companies Cannot Afford Hiked Up Prices
Though state and federal governments provide attractive grants and opportunities for determining manufacturing labour to build their lives, it is hard to attract quality labour forces due to higher demand from labourers. Also, manufacturing companies cannot afford the demand due to extra expenses in ensuring safe working environments and good labour wages in limited premises.
The cost of labour in Australia since January 2019 is illustrated in the graph below as said by tradingeconomics.com. It shows a gradual increment in the labour charges from January 2021 to January 2022, which explains the hiked up cost of labour management that was inflicted on Australian manufacturers.
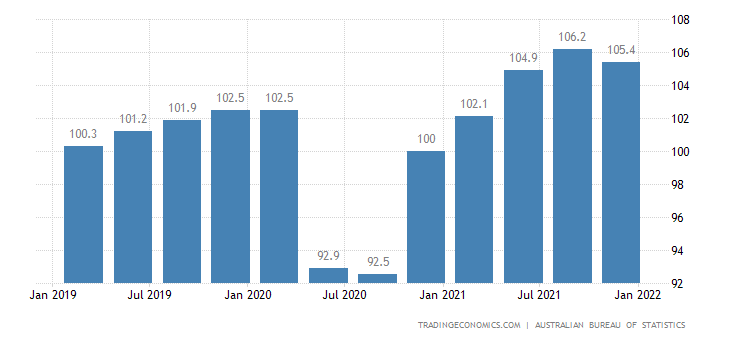
How Can Cerexio Help in Overcoming Labour Challenges?
So, How Does This Work?
Cerexio MES is a process and data-oriented AI-based system to improve your manufacturing premise’s administrative, managerial and operational excellence, starting from the executive office up to your factory floor. In essence, the Cerexio MES solution is unrivalled in guiding manufacturers towards optimal labour utilisations. The conventional ERP and analytics systems use data-oriented analytics and AI tools to enhance labour performances, but Cerexio AI models are powered by data and process-oriented data. This solution uses a multi-dimensional matrix of each manufacturing process and automatically builds an AI model on top of the model. It will automatically represent the actual quality of labour against the potential and desired quality of labour. This makes quintessential labour utilisation, not a forced effort but an intrinsic motivation for labourers to do their best.
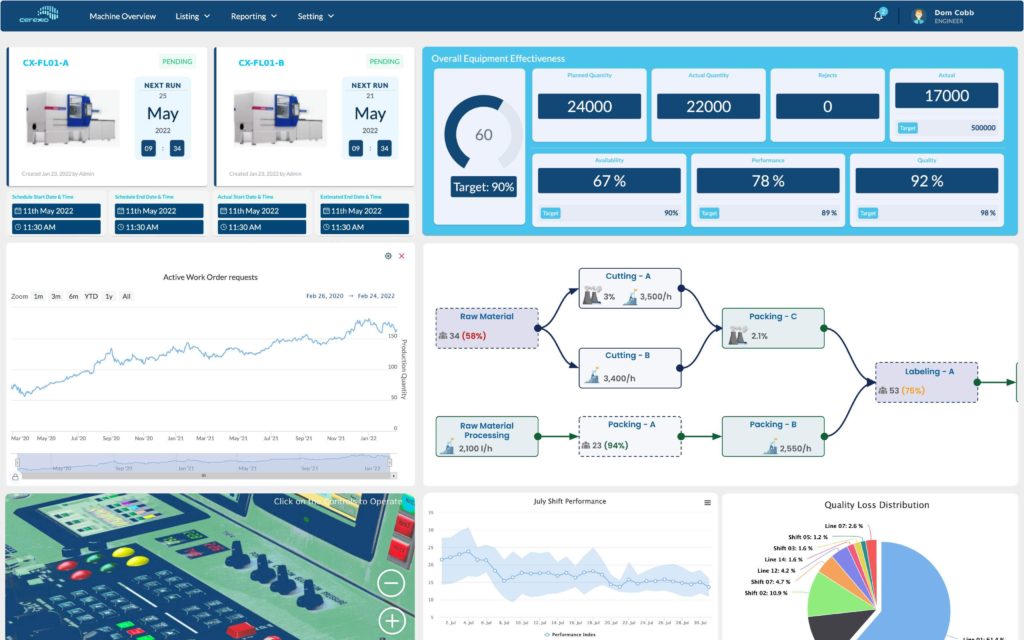
Secondly, we master IoT sensors and cyber security services related to the manufacturing ecosystem to optimise your asset performance by reducing downtime and automated root cause analysis of quality losses and wastages. The machines can be automated to augment routes based on the dynamic process priorities so that all operations are streamlining seamlessly. This technology gives your labour more time to work on tasks that need human intervention with lesser idle time.
Still curious about how we can help your factory make the best out of existing labour potential and capacity? Connect with Cerexio to learn more about how we can facilitate your company in meeting the best labour productivity levels with ‘The Industry 4.0 Way of Labour Utilisation’.