We know that your manufacturing establishment has unique requirements and faces specific challenges. The lack of fundamental understanding of the latest industrial technologies can misguide you from opportunities of deploying appropriate technologies to overcome your unique organisational battles. Keep your understanding of newly fangled industrial technologies up-to-date with this article and explore which technologies can you use to stay ahead of the curve in the manufacturing world.
What are You Missing By Not Being Updated on Modern Manufacturing Technologies?
Forward-thinking Manufacturers are Ready to Face Disruption
Not Being Part of The Digital Revolution is A Risk You Cannot Afford to Take.
The digital revolution started with IoT (Internet of Things) systems where data threads are amalgamated from disparate data sources like sensors, machines, production lines, data warehouses, ERP, MES, EAM, databases, data lakes, applications and more. It offers unprecedented strengths and opportunities that boost the effectiveness and efficiency of manufacturing operations. Missing out on the fact-based, success-guaranteed insights derived by this new data puts the neo manufacturers at a great disadvantage. On the other hand, manufacturers that manoeuvre intelligent factories use technologies to overcome operational, managerial and administrative inefficiencies plus risks and threats.
New-age Technologies are Indispensable
Guide for Manufacturers in Understanding The Latest Industrial Technologies Comprehensively
Disruptions Prone by Additive Manufacturing
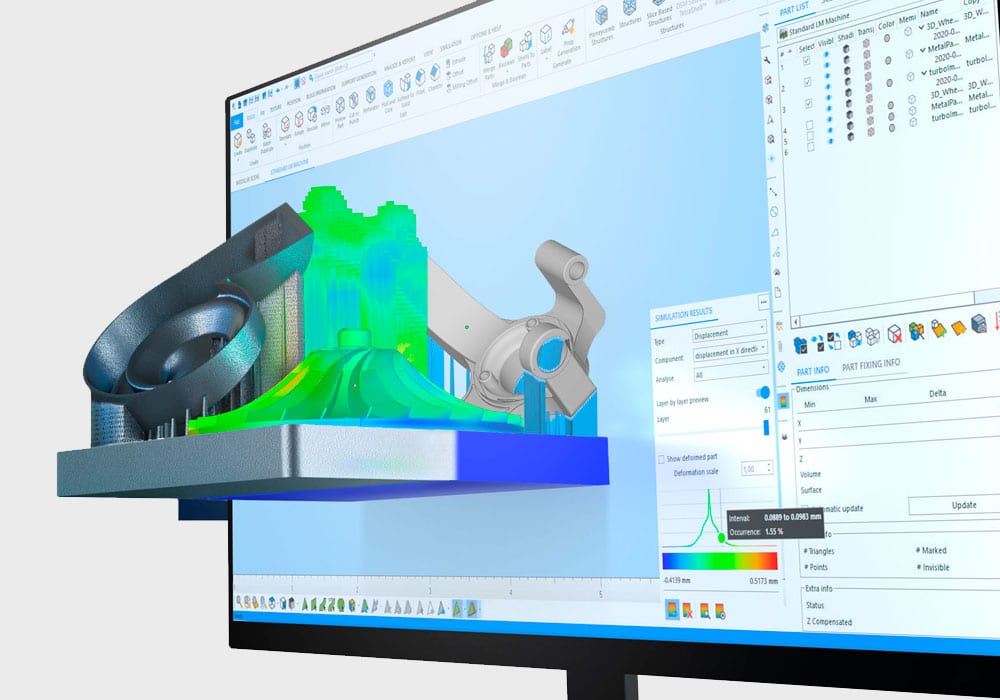
This technology is a CAD (Computer-Aided Design) software linked to 3D Object scanners and hardware that deposits materials layer by layer to create objects. This technology overlooks all the challenging steps of manufacturing objects in the traditional way, including milling, carving, shaping or any other means of creating an object.
One of the most famous industrial examples that explain this technology’s benefits is the Metal AM Printer. Metal additive manufacturing allows quality control and integrated calibration to build a model via in-situ metrology sensors to offer image manufacturing capabilities. This technology offers precise and optimised throughput that leads to an unlimited number of innovative designs despite the intricate manufacturing demands of any industrial player.
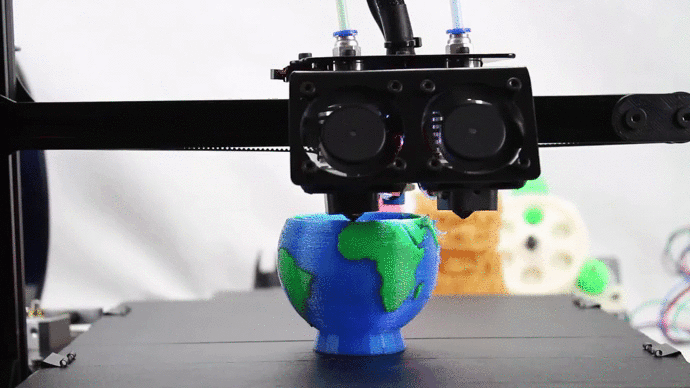
This technology offers a cutting-edge trifecta of simplified fabrications, enhanced performance and the ability to craft complex geometries. The manufacturing industry is therefore at a great advantage if they use this technology to manufacture objects because it saves time, mitigates material wastage and labour costs and offers precise end-products that rapidly drops the damaged goods rates. The future shows a broad consensus for additive manufacturing trends because this technology brings the automation, collaboration and sustainability of manufacturing processes to a whole new level.
FUN FACT: The latest trend of Additive Manufacturing is ‘4D Printing’. This technology uses 3D printing to print an object that can change its properties when it is exposed to certain environments (like changing the light, water, temperature, or passing an electric current). It is the same as 3D printing, but it has an energy source and time dimension- which allows the object to be created using precise geometric codes.
Digital Twins for End-to-end Manufacturing Vicinity
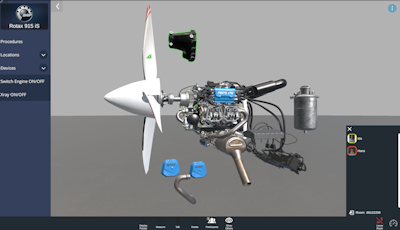
Having constant access to a near-real-time virtual representation of a process or a physical component is a great advantage for manufacturing specialists to make success-guaranteed decisions, and that is exactly the advantage offered by a digital twin. The new-age manufacturer’s success in implementing smart manufacturing depends on how updated and predictive they are of the operations and other business processes of their manufacturing facilities. This is why the digital twin technology is used by many around the world- especially manufacturing conglomerates to monitor, predict and optimise fixed assets, products and systems to make smarter decisions.
There are many advantages of using this technology of the modern manufacturer, like:
- A gateway to understand and update necessary security and risk detection protocols
- Amazing training tools for better visibility of employees to understand their responsibilities with hands-on virtual inspection opportunities
- Minimised production time due to predictive advantages
- Predictive maintenance technologies that represent life cycle models of assets
- Remote monitoring tools via interactive digital models
- Superfast manufacturing process risk assessment
- Unlock the surest financial decision-making processes based on fact-based predictions and visibilities
When empowered by simulation, AI and advanced analytical technologies, digital twins soothsayer of the manufacturing team. Data collected from various data points can be fed to well-trained AI-driven predictive and prescriptive technologies to understand what is going to happen and what needs to be done to dodge negative futures. The insights extracted by these advanced analytical technologies can then be fed to simulated digital twins to showcase the future of manufacturing objects, processes and systems. Therefore, digital twins not only represent the real-time statuses, performance metrics and resources allocation and usage of your manufacturing centres, but it will also say how they will behave in future. Thus, digital twins are advanced in the digital era to be ‘even more cognitive’.
New-age digital twins are advanced with cognitive technologies that possess executable knowledge to guide manufacturers by guiding them with data-driven intelligence by correlating manufacturing events to the external environment for more realistic insights. This technology bridges the human intuition and machines and prescribes executable knowledge that would take days or months for analytical experts to suggest. Thus, the adoption of digital twins seems to be one of the most important monitoring and analytical windows for manufacturers to make data-guided decisions to meet their objectives faster than ever.
Immersive Technologies
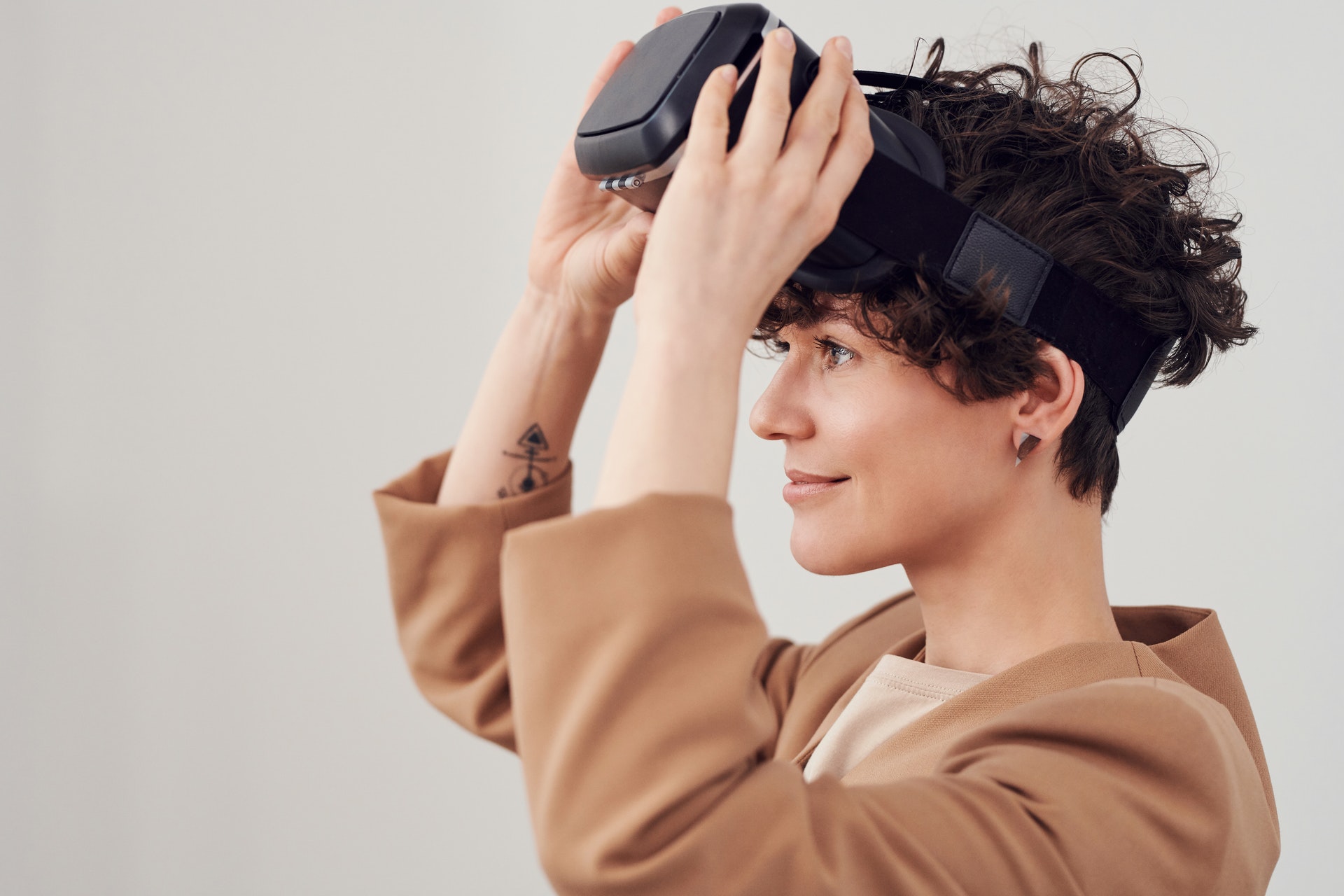
In a manufacturing context, VR, AR and MR can be majorly used in improving the visibility of manufacturing floors. When advanced with computer vision (CV) technologies, AI and data tools, data technologies can facilitate a range of manufacturing activities. Here are some of the manufacturing activities that can be enhanced with immersive technologies.
- 3D content authoring to automate UV unwrapping, unity shading and texturing, modelling, rendering, baking and lighting and more
- AI and CV technologies for conversational interaction and precise detection of objects, models edges and even faces
- Allowing manufacturing managers to have VR tours on the shop floor to get near-real-time updates of the shop floor
- AR-based user manuals
- AR technology for capturing and advanced processing of camera scenes of the shop floor to detect risks and augment maintenance protocols
- AR to track positions and orientation activities and display rendering effects
- For enabling Augmented marking advertisement using sharp AR-based selling tactics
- Simulated training environment powered by blended immersive technologies
- Using MR for tailoring hyper-personalised products demanded by unique customer requirements
Integrated Manufacturing Solutions that Maneuver Robot Fleets
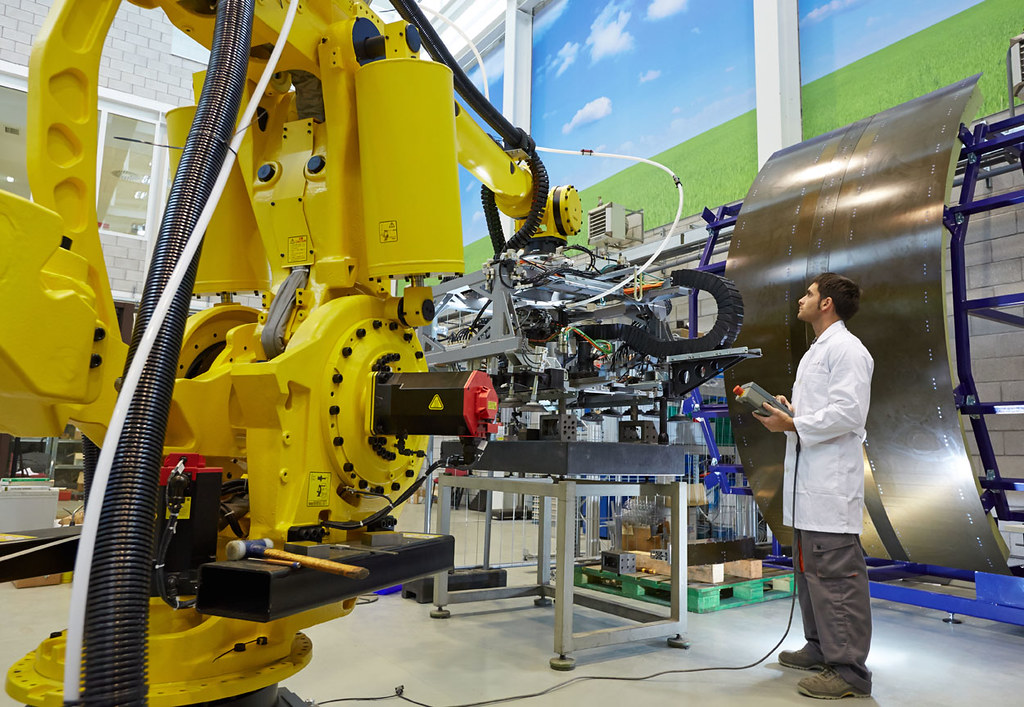
The advanced technologies of industry 4.0-defined technologies -Predictive Analytics, Prescriptive Analytics, Robot Automation, AI, IIoT- led to the integration of all software suites, smart machines, stakeholders, cloud platforms and other elements of complex IT infrastructure of manufacturing organisations. These advances have led to the adoption of robot fleets easier and ameliorated the past few years.
The technological integrations offer universal viability for manufacturers to extract data at every data centre and take control of AGVs, IGVs, RGVs, AMRs, UAVs, NFCs and other robotic fleets. Such technological power can be adopted by any type of manufacturing practitioner to overcome limitations in manufacturing processes, warehouse, supply and logistics and other functions. Advanced software suites and precise robotic automation is mainly used by manufacturers who make textiles, food and beverages, metal, gadgets, computers, plastics, chemicals and more.
Cerexio Offers Advanced Manufacturing Technologies That Makes You Resilient to The Future of The Manufacturing Realm
Cerexio offers a range of technologies and services that optimises manufacturing efforts, decisions and business models with industry 4.0-defined tools and technologies. We are a team of manufacturing specialists, technology experts and innovation enthusiasts ready to help you create a road map and navigate through it to meet the next best level of your manufacturing centre. We were recognised as the best MES provider in Asia in 2020 by professional research associations for executing solutions that are empowered with technologies that meet industry 4.0 demands.
Cerexio offers end-to-end technologies that are defined by the latest technology world’s front-page news. Starting from digital twin, AR, VR, simulation tools, predictive and prescriptive analytics, self-reliant analytics, smart robotic employment, IIoT, AI and ML algorithms deployment and engineering tools and more. We also offer services like PLC and Instrumentation for Smart Factory and Smart Warehouse Installation and professional manufacturing training and consultancy services. Visit Cerexio to learn more about our exclusive manufacturing technology products and platforms that can boost your factory yield by 10% after initial deployment and how your asset reliability rates can skyrocket starting from the first day.
Are You Ready To Meet The Futurity of Modern Manufacturing
This is why your organisation must make future-oriented decisions in relaying the potential and performability rate that you can reach by adopting better, more innovative and smarter technologies. Smart technology deployment can help you focus on participating global value chains, improve all the departments of your manufacturing centres through seamless collaborators and make organisation-specific decisions to meet your goals in a timely and profitable manner.