Every industrial operation relies on compressed air, but not all compressors perform equally. Are you still unsure which type of air compressor best suits your heavy-duty needs? The scariest part is that making the wrong choice can drain resources and stall progress. How can you select the suitable air compressor type, and what factors should you consider when choosing one?
This article breaks down the top four industrial air compressors, highlighting their unique strengths and areas of excellence.
We will explore
- Understanding Air Compressor Mechanisms
- The Top 4 Industrial Air Compressor Types
- How to Choose the Right Industrial Air Compressor
- Cerexio Machine Health Monitoring System for Maintaining Compressors
- Fulfilling the Industrial Purpose: Selecting the Right Air Compressors
- FAQ about Industrial Air Compressor Types
Understanding Air Compressor Mechanisms
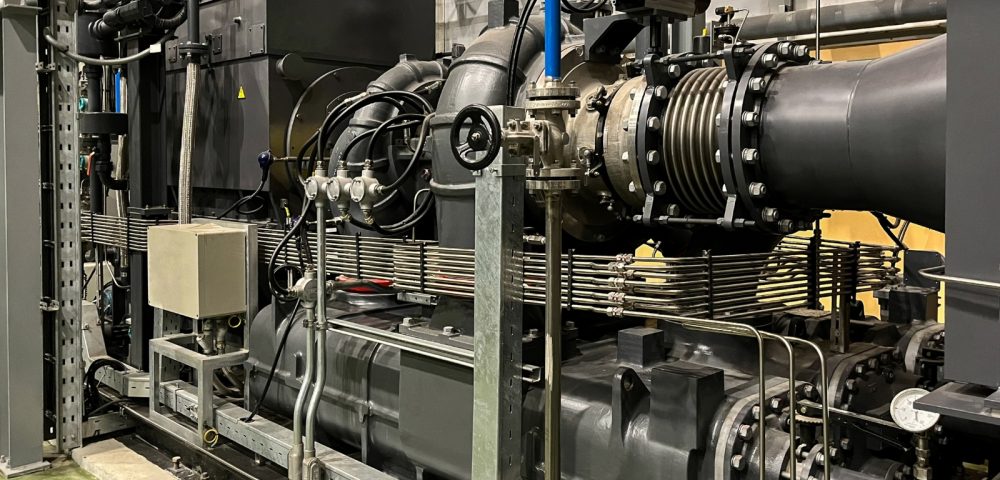
- Air compressors work through two main mechanisms: positive displacement and dynamic displacement, and each performs differently depending on the task.
- Let us walk you through the first one, or the positive displacement compressors. It simply traps air in a chamber, then reduces the chamber’s size to squeeze the air and raise its pressure. This method produces steady airflow and suits projects that need consistent pressure at lower volumes.
- On the other hand, dynamic displacement compressors use fast-spinning impellers to accelerate air, then convert that speed into pressure with diffusers. This approach creates high-pressure air efficiently at higher volumes, making it useful for heavy-duty industries.
- Positive displacement usually delivers reliable power at moderate energy costs but requires more upkeep due to moving parts. Meanwhile, dynamic displacement generates stronger pressure with fewer mechanical parts, reducing maintenance needs but consuming more energy in some cases.
The Top 4 Industrial Air Compressor Types
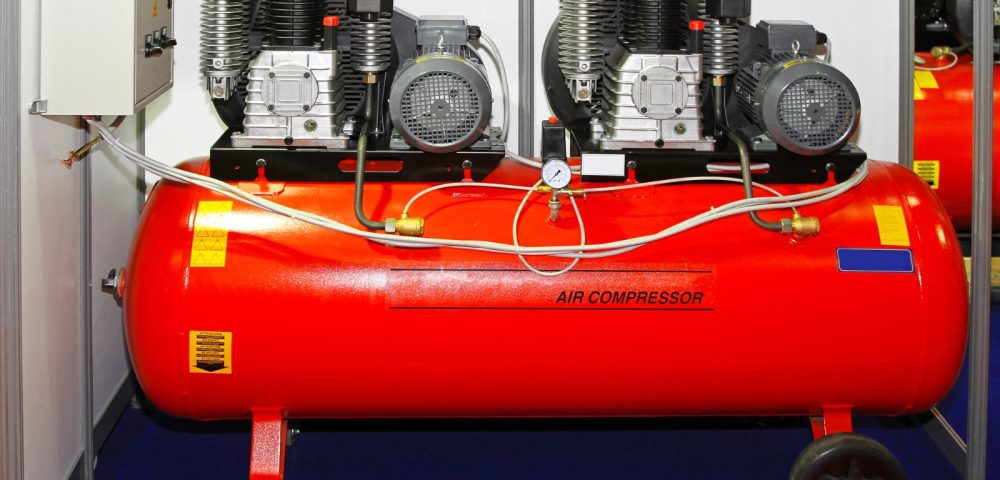
Rotary Screw Compressors
These types of compressors use two helical rotors that spin toward each other, trapping air between them and pushing it into a smaller space to build pressure. This mechanism keeps the airflow smooth and constant, which makes it perfect for heavy-duty and continuous work.
Also, these compressors shine because they last long, stay cool thanks to built-in cooling systems, and need little maintenance compared to other types. You can find them in factories, plants, construction sites, and oil and gas operations where uninterrupted power is essential.
Many industrialists opt for them because they come in oil-lubricated and oil-free designs, making them versatile for different air quality needs. While they take up more space and cost more upfront, they save time and hassle over the years with their durability.
Reciprocating (Piston) Compressors
Reciprocating compressors rely on a piston moving up and down inside a cylinder to compress air, creating high pressure in bursts rather than a constant stream. This makes them great for tasks that do not need continuous air but still demand powerful bursts, like inflating tires, painting, or powering tools.
Their biggest advantage lies in their affordability and portability; they pack a lot of strength into a small, mobile frame. Workshops, garages, and smaller construction sites use them daily because they are easy to move and quick to set up. Single-stage versions handle light to medium tasks, while multi-stage models work better for higher-pressure jobs like car assembly.
On the downside, they make more noise, wear out faster, and require frequent oiling.
Centrifugal Compressors
Centrifugal compressors work by spinning air quickly with impellers to add speed, then guiding it through a diffuser where that speed turns into pressure. This process delivers high volumes of air without needing a huge machine, and this is what makes it an efficient choice for industries needing lots of power.
One clear advantage is that these compressors fit a lot of energy into a compact frame, and some even produce oil-free air, which keeps the air cleaner for sensitive environments. They require less maintenance since they do not have as many moving parts, and they handle continuous, heavy workloads beautifully.
We can find them in chemical plants, steel mills, oil refineries, and large manufacturing facilities where both strength and reliability matter. However, it comes with higher initial costs and the need for skilled operators.
Axial Compressors
Axial compressors compress air through multiple rows of rotating and stationary blades that guide and squeeze the air as it flows through the machine.
This staged process produces extremely high airflow and impressive efficiency, especially at higher speeds. You will notice that many industrialists admire these compressors for their ability to move massive amounts of air while staying surprisingly compact for their output.
They also work well in environments that demand high horsepower without wasting energy. We can find them powering jet engines, naval ships, and large power plants because they handle extreme performance requirements with precision. They also have downsides due to the high cost, complex maintenance, and the fact that they are usually custom-designed for specific uses.
How to Choose the Right Industrial Air Compressor
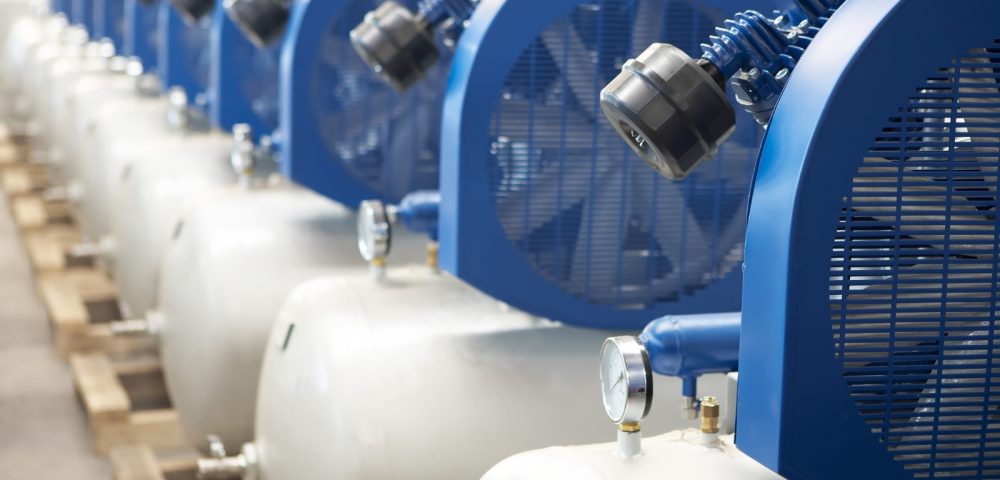
Air Quality Requirements—If you work in a clean environment like food, pharma, or electronics, you should pick an oil-free compressor to keep the air pure and avoid messing up sensitive products.
Energy Efficiency—When you care about cutting energy bills and wasting less power, you can choose a variable speed drive or natural gas-powered compressor to match your exact demand and save money over time.
Portability and Footprint—If you move between different sites a lot, go for a portable compressor, but if you have a permanent workshop with plenty of space, a stationary one makes more sense and stays more stable.
Maintenance Requirements—Since compressors need regular checkups to stay reliable, you should think about how easy it is to service, who will handle repairs, and whether you can keep up with its maintenance schedule.
Budget and Lifespan Considerations—You must weigh how much you are willing to invest now against how long it will last and how much you will spend on upkeep in the future.
Cerexio Machine Health Monitoring System for Maintaining Compressors
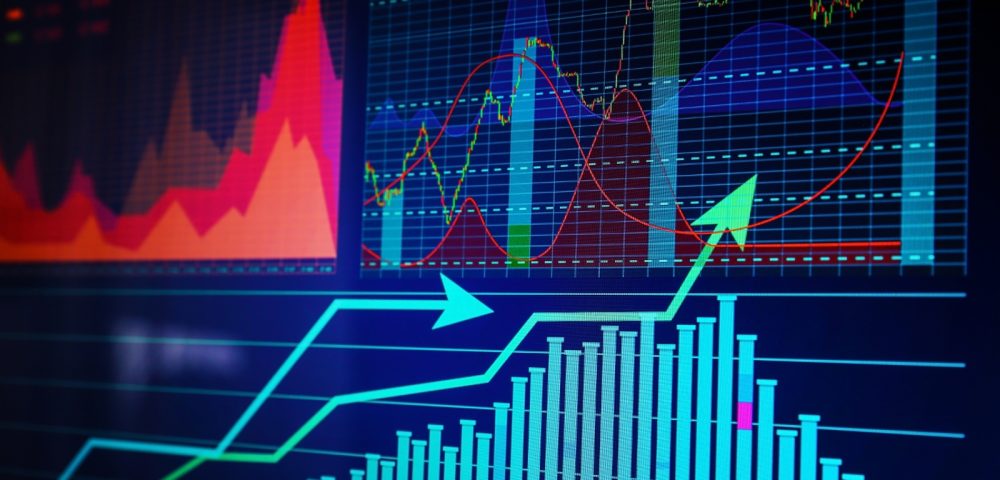
Cerexio offers an Industry 4.0-powered Machine Health Monitoring System that has the ability to track every vibration, temperature shift, and pressure fluctuation in real-time, keeping air compressors efficient and reliable. With its embedded predictive analytics power, it alerts you before issues escalate, minimising downtime, reducing costs, and ensuring your compressors deliver peak performance without unnecessary wear or surprise breakdowns.
Fulfilling the Industrial Purpose: Selecting the Right Air Compressors
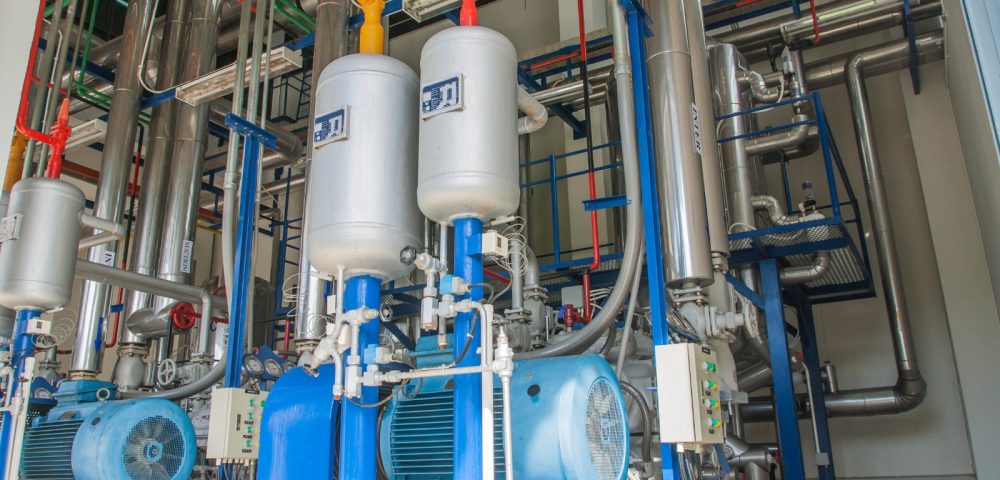
Your air compressor choice fuels your entire operation. The wrong pick drains efficiency, while the right one supercharges performance and reliability. When purchasing air compressors, you must think about your goals, your workspace, and your tools. Ready to uncover what really sets the best compressors apart? Connect with our specialists and make your investment count.
FAQ about Industrial Air Compressor Types
The most common industrial air compressor is the rotary screw compressor. It offers continuous airflow, high efficiency, and low maintenance, making it ideal for large-scale manufacturing, construction, and industrial applications requiring reliable, steady compressed air.
You can calculate CFM by measuring the volume of air delivered per minute at a specific pressure. Use this formula: CFM = (Volume of tank × pressure drop) ÷ (time in seconds) × 60. This ensures you select the right compressor capacity for your needs.
Choose compressor size by assessing your tool’s total CFM requirements and operating pressure. Add a 25% safety margin, consider duty cycle, and match the compressor’s output to your application to ensure efficient, uninterrupted air supply without overloading the system.