In this article, we dive deep into the benefits of employing wearable technology in manufacturing operations.
What is Wearable Technology?
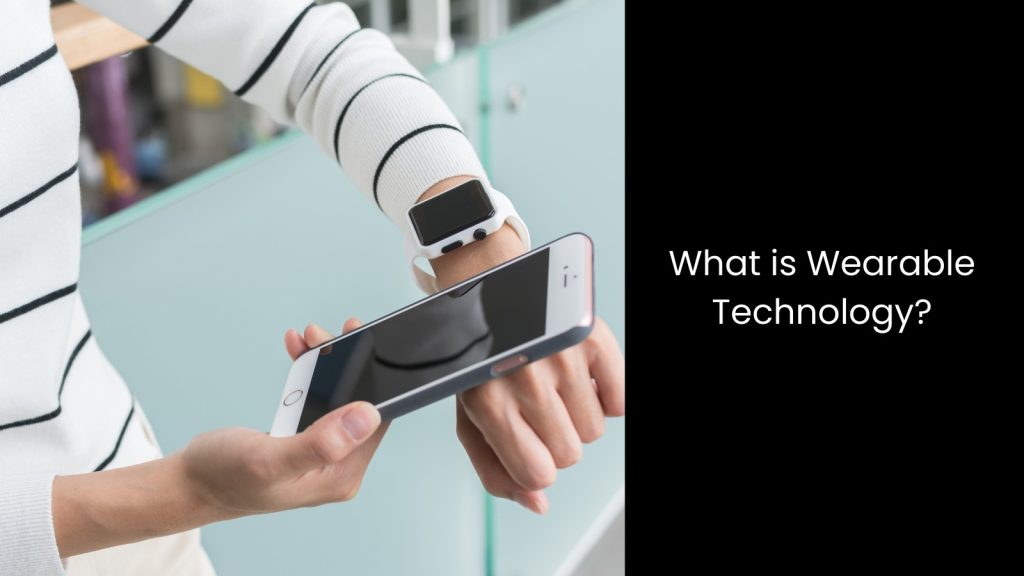
- Wearable technology simply includes smart devices designed to be worn on the body, offering users real-time data tracking, connectivity, and interactive features. These gadgets, like smartwatches, fitness trackers, smart glasses, and wearable medical devices, use built-in sensors, wireless communication, and AI-powered analytics to collect and process information.
- In today’s world, people use them to monitor health, track workouts, and enhance daily tasks. In healthcare, wearable health monitors help doctors keep an eye on patients remotely, while biometric wearables measure heart rate, oxygen levels, and sleep patterns.
- However, this is a hot topic in the industrial world. Do you know why? Many industries rely on wearable sensors for safety and productivity, such as industrial wearables that assist factory workers in preventing injuries. The manufacturing employees use augmented reality wearables and virtual reality headsets, which create immersive digital experiences.
- Businesses use enterprise wearables to boost workplace efficiency, keeping employees connected with instant notifications. With this much enthusiasm going on for the latter, wearable tech continues to evolve, making life more convenient while pushing the limits of human-device interaction.
What are the Benefits of Wearable Technology in Manufacturing?
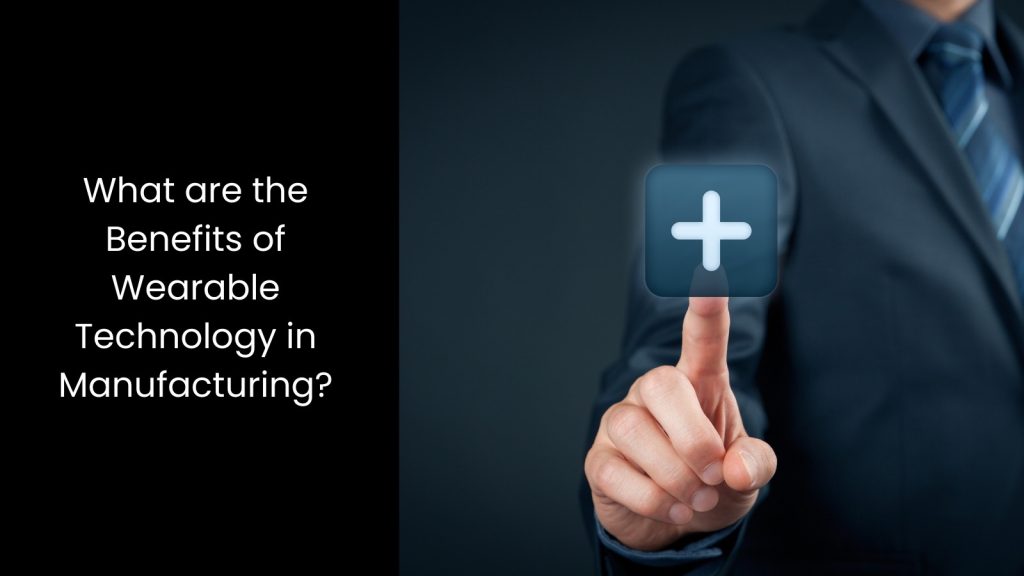
Enhanced Worker Safety
Wearable technology plays a massive role in keeping them out of harm’s way by tracking posture, fatigue levels, and dangerous surroundings in real-time.
For example, smart helmets detect gas leaks, overheating, or falling objects and instantly alert workers, allowing them to react before a small issue turns into a big accident. Exoskeletons reduce strain on muscles and joints, making physically demanding tasks easier and lowering the chances of injuries caused by repetitive motion or heavy lifting. In addition, sensors inside these devices track body movement, ensuring workers maintain safe postures while operating machinery or carrying loads.
Plus, connected wearables sync with plant-wide systems, ensuring managers receive instant updates if a worker falls, suffers from extreme fatigue, or faces exposure to toxic environments. Real-time monitoring creates a proactive safety net that prevents accidents rather than reacting to them after they happen. It is evident that wearable technology transforms the way safety works in manufacturing plants, making every shift less risky and every worker more protected without disrupting productivity.
Improved Productivity
Wearable technology changes the battleground by making real-time data access easier, keeping downtime low, and helping workers complete tasks faster without cutting corners.
As you can see, augmented reality (AR) glasses display step-by-step instructions, equipment diagnostics, and live updates right in front of the worker’s eyes, removing the need to stop and check manuals or computers. This hands-free access to information means they can fix machines, assemble components, or troubleshoot issues while staying focused. Smart gloves take efficiency to another level by allowing workers to scan barcodes, interact with digital interfaces, and record inventory movements with just a simple hand gesture.
These wearables eliminate the hassle of juggling tools, tablets, or paperwork, which speeds up production lines and reduces mistakes. Wearable technology also connects employees with supervisors instantly, making sure they receive guidance without wasting time searching for answers. When teams communicate faster, errors get solved quicker, and machines stay up and running longer.
Faster Training and Skill Development
New employees step into complex environments where they must learn procedures quickly without slowing down production. AR-based training modules turn that learning curve into a smooth ride by providing hands-free, interactive guidance that eliminates the need for bulky manuals or lengthy classroom sessions.
AR glasses project step-by-step instructions, 3D models, and real-time visual overlays directly into the worker’s field of view. This allows them to understand machine operations, assembly techniques, and safety protocols while actively performing tasks. This approach removes the stress of information overload and lets employees absorb knowledge in a way that sticks.
Wearable technology also ensures that trainers do not have to hover over every new hire, as smart wearables track progress and provide automated feedback on task execution. Smart gloves enhance learning by allowing workers to interact with virtual components, scan items, or trigger guided workflows with simple hand gestures.
As a result, manufacturing plants run on efficiency, and wearable technology makes sure that employees reach full productivity faster without the usual back-and-forth that traditional training requires.
With this tech-driven approach, companies can up-skill their workforce in record time, and they can keep operations smooth and adapt to new challenges with ease.
Hands-Free Operation
Stopping every few minutes to check reports, instructions, or system data slows down workflow and causes unnecessary delays. With hands-free operation, workers stay fully engaged without breaking their rhythm. Smart glasses project real-time instructions, diagrams, or equipment diagnostics right into their field of vision. Therefore, they do not need to leave their workstations or shuffle through paper manuals.
Further, wearable technology eliminates the hassle of carrying around tablets, radios, or handheld scanners, streamlining tasks and reducing distractions. On the other hand, voice-activated controls allow workers to request data, check reports, or receive real-time alerts without lifting a finger. This level of instant access improves accuracy since employees do not rely on memory or outdated printouts when performing complex tasks.
Less time wasted on back-and-forth means machines stay up and running longer, reducing downtime and increasing efficiency. Seamless integration with factory systems ensures that workers always stay connected, whether they need to adjust production settings, check quality parameters, or receive urgent notifications.
So, there is no doubt that wearable technology keeps everything within reach without slowing anyone down.
Cerexio IoT Integration System for Smooth Implementation of Wearable Technology
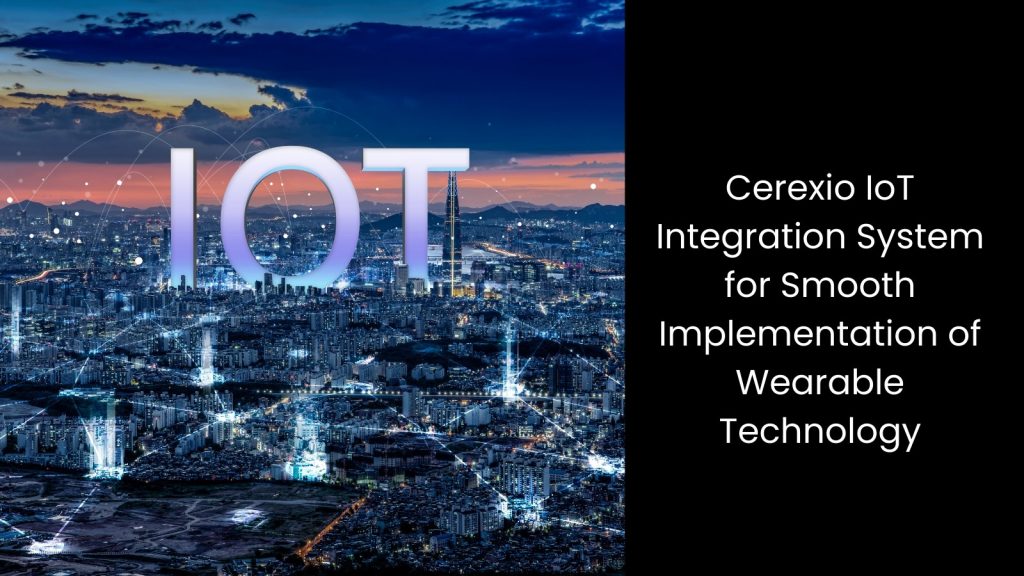
Cerexio IoT Integration System makes wearable technology work flawlessly in modern manufacturing plants, and it ensures smooth connectivity, real-time data exchange, and hands-free efficiency. With Cerexio-initiated intelligent automation, predictive insights, and seamless device syncing, this system transforms wearables into a powerhouse for productivity, safety, and precision. Our solution simply helps manufacturers stay ahead in the fast-moving industrial landscape without disruptions or delays.
Utilising Wearable Technology in Manufacturing to Ensure a Safe Worker Environment
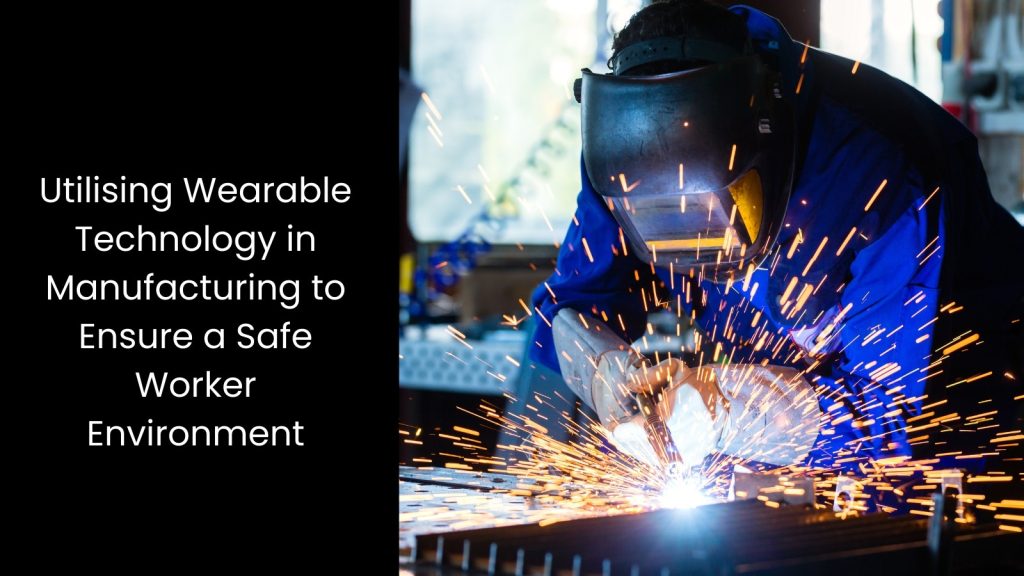
Manufacturers no longer need to choose between productivity and safety since wearable technology delivers both. It minimises risks, prevents fatigue, and creates a workplace where injuries become a thing of the past. The industries that adopt these innovations today will set the standard for a future where every worker feels secure on the job.