The term digital twins is not a new one. Since recent years, the benefits of infusing digital twins have been a popular topic, especially in the manufacturing, construction and utility sectors. They have helped companies to significantly lower their expenses, streamline their processes and give the capacity of businesses to take their innovation to the next level. There are a handful of companies, however, that are currently testing how further they can use digital twins. This is where cognitive digital twins come into play. They offer more agile and robust opportunities to manipulate physical objects and have more control of big data. The common consensus in the business world is that real-world elements such as assets, processes and systems have different types and levels of cognitive capabilities. This article will break down the characteristics of cognitive digital twins.
What Are Cognitive Digital Twins
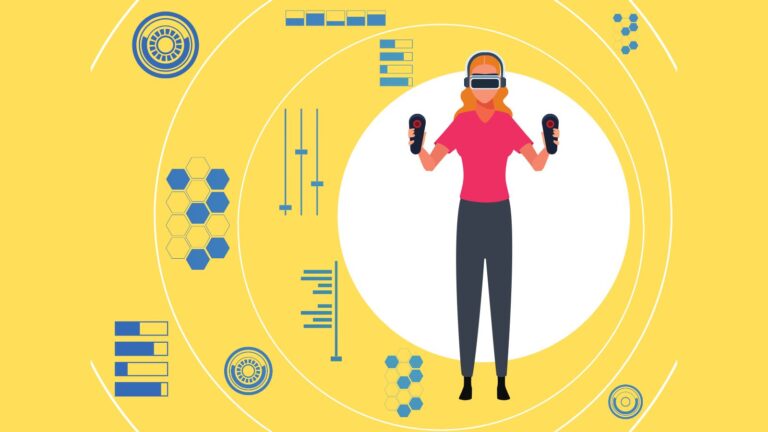
Various institutes have attempted to cognitive digital twins by breaking down the meaning of the two words. Hence, while digital twins can be explained as a digital replica of real-world assets, systems and processes, cognition is a form of computation that views the mind as a machine infusing capabilities with attention, perception, reasoning, memory, problem-solving and learning skills. Hence, when put together, cognitive digital twins are the algorithms that AI makes in real time to provide self-learning capabilities. The most prominent feature of cognitive digital twins, besides their self-learning capabilities, is their ability to predict the future and suggest solutions based on such models. Even where companies struggle to find enough data to make such predictions, a cognitive digital twin creates synthetic data based on high-fidelity models that reflect the actual system.
How Different Are They From Just Digital Twins?
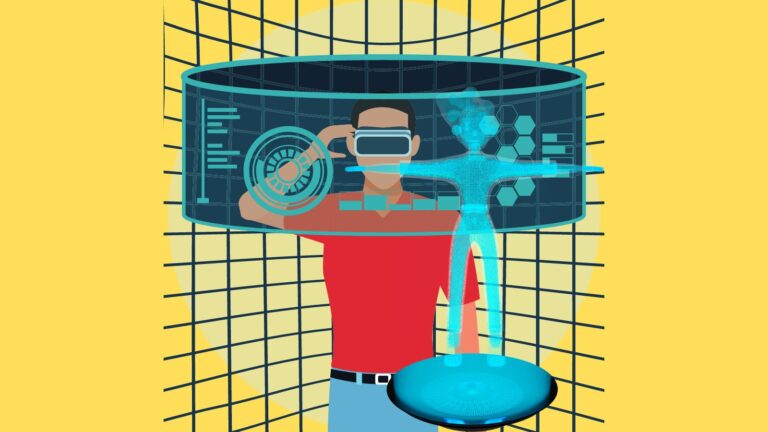
In its usual sense, a digital twin is an advanced industry 4.0 solution predominantly used for three aspects. This includes status monitoring, simulation and visualisation. Such processes are made possible by integrating Internet of Things sensors, real-time visualisation dashboards and alert systems. In short, digital twins are regarded as an identical digital copy of the physical asset, which converts it into autonomous intelligent agents and offers possibilities that cannot be executed on physical assets without wasting resources.
Cognitive digital twins carry out the same functions. However, the most significant difference lies in that it adds more capabilities for assets, systems and processes to communicate and enhances analytical and intelligence capabilities in three ways. This is assessed by regarding them as three different layers. The first is the access layer which handles the communication between machines and accesses data on the physical asset’s condition to update the status of the digital twin. The second is the analytics layers which enhance the edge analytics capabilities of the devices. Consequently, in addition to collecting real-time data, it converts it to actionable knowledge to help make the decision process of managers much smarter. The third and final layer includes the cognitive layer, simplifying complex decision-making using domain expertise, edge analytics and global knowledge bases. This plays a significant role in the communication between digital twins, thereby allowing them to make their own network and carry out decisions on their own. In other words, cognitive digital twins lessen the number of work humans has ever to do. Previously, digital twins merely provided information which humans had to determine what they needed to do. In cognitive digital twins, the traditional digital twins are converted to smarter agents that can “access, analyse, understand and react to their current status”.
A practical example demonstrating the difference between digital and cognitive twins is identifying risks in assets. When an asset faces an anomaly, a digital system simply alerts the manager, who is responsible for finding a solution. In cognitive digital twins, it interacts with the operating environment and digital twin products to run processes to analyse more constructively and intelligently understand the anomalies much better. It takes more advanced efforts to understand local anomalies better, which it shares with others. As a result, a social and interactive network is created instead of simply an intelligent system. It improves communication between tacit human knowledge with the power of a digital twin model to utilise synergies and help provide better reactions, which neither a human nor a digital twin alone could do without interacting with one another. It self-heals, self-configures and self-orchestrates systems. It will, in essence, create an ecosystem whereby a network of automated machine-to-machine interaction and decision-making is created among themselves.
How Cognitive Digital Twins Works
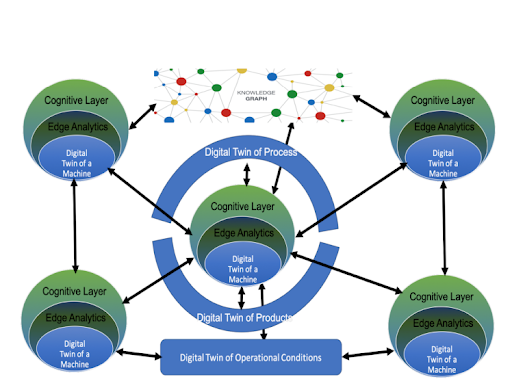
There are four stages in cognitive digital twins. They include the following:
- First Stage: If the manager requires an industrial machine to have a cognitive digital twin, the first step is integrating it with edge analytics. This will monitor the condition of the equipment in real-time around the clock every day. The system saves a predefined threshold, whereby a value below it indicates it is in good condition. An alert is sent when this is expected to increase or does increase.
- Second Stage: At this stage, the cognitive digital twins try to find the root cause of the problem, assessing why such a failure is about to happen. This is sometimes referred to as the ‘sense-making’ process, which collects contextual information, configurations of the processes applied by the machine and operational conditions. The cognitive digital twins correlate all the data accumulated to find the most accurate cause. Every time a new anomaly is made, the information is saved in the system so that where similar features are seen, it is flagged in advance.
- Third Stage: Where the system is finding it hard to find the correct source of failure, cognitive digital twins take advanced steps to gain further assistance from social networks. It does this by communicating with the other machines connected in a factory, and reaching out to social networks of peers with similar machines and similar operational conditions. Hence, the digital twin automatically adjusts itself to the configuration of machines running without any problem. Since this results in a multitude of assets being connected, where all such machines are at risk, a network-wide alert is sent, requesting urgent remedial action.
- Fourth Stage: The role played in this stage significantly eliminates the need for a human expert. All the events, interactions, analytics and sensemaking processes are processed in a central place like an enterprise-level knowledge graph. This knowledge graph will act as a library of information that allows the machine to make future predictions regarding assets and other ever-changing trends in the industry.
Will the Demand for Cognitive Digital Twins Increase in the Future?
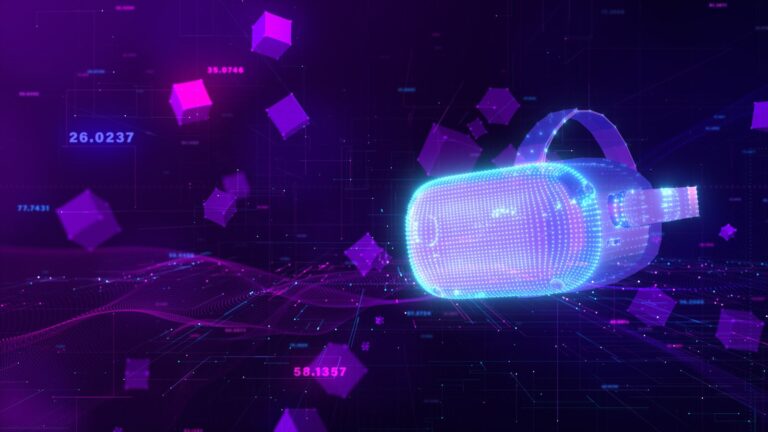
At present, cognitive digital twins are not a concept that is fully utilised in industrial operations. While a few companies are testing it out, research is still being conducted on its implementation. A question that has been consistently asked is how many cognitive capabilities we want machines to hold. It will be interesting to see how this debate will proceed and whether there will be a surge in companies that will implement such technologies into their operations. Cerexio, a leading vendor that holds the latest industry 4.0 technologies, has a powerful digital twin for the time being to help companies assess whether a much more powerful tool is required. Connect with our team to get more answers.