Programmable Logic Controllers (PLCs) and Distributed Control Systems (DCSs) are often regarded to be the same by many as they both contribute to automating processes. While it is similar in some respects, both are different, especially regarding origin. PLCs were originally the replacement for hardwired relay logic panels, which were included in older control systems. As such control systems required teams to spend enormous time to find even the slightest issue, a PLC helped streamline the process. A DCS, in contrast, a DCS was a tool used to integrate two or more machines in the plant or a factory. Some people consider DCS a type of control system meant to subsequently replace PLCs. However, DCS is a control system ideally used with a PLC system. Certain software vendors today have been able to make one compact solution with both PLC and DCS features. However, to understand the unique nature of such a system, it is helpful to learn what makes a PLC different to a DCS. This article will help you comprehensively understand the differences between these two controlling systems.
Five Ways PLCs and Different from DCSs
Many things make PLCs and DCS different from one another. While these differences may seem subtle, the overall contribution towards the feasibility and sustainability of investing in a solution is essential. Here are five things that make a traditional PLC different from a DCS.
The Complexity of The Operating System
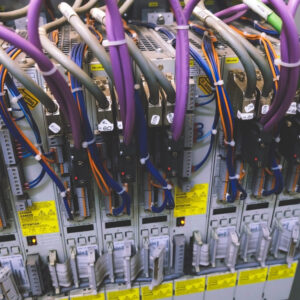
PLCs only have one controller to handle processes. Hence, it has a relatively simple operating system that focuses on scanning inputs and updating outputs. This makes it easy for managers to carry out programs quickly. At the same time, PLCs are limited in the number of processes they can handle. In other words, a PLC is most suitable for a smaller business with fewer operations. A DCS, on the other hand, can handle multiple processes due to the complex nature of its operating system. Rather than a single unit, a DCS is a complete system. Taken in another way, a DCS is a network of processes which does not have a central point. Moreover, DCS can integrate with various electronic devices such as sensors, transmitters and other intelligent technologies located in different parts of the factory.
Ability to Customise
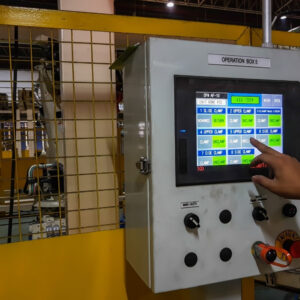
PLCs have a dedicated process. It includes various functions like logical operations, sequencing, timing and counting. As a result, because they are typically used for a restricted role, there is barely the possibility to customise them. It should be noted, however, that each PLC is industry specific. Hence, if a company is purely carrying out the traditional processes, a PLC is much sufficient. DCS comparatively offers more flexibility. If a company wants to increase scalability, a PLC would not, in that sense, be the ideal solution. For instance, a typical PLC can only integrate to 1000 I/O ports, whereas a DCS has several thousand I/Os.
Which One Responds Faster?
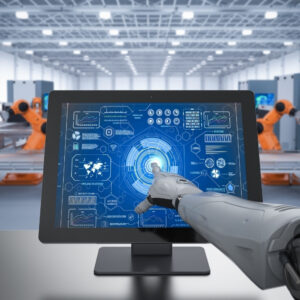
Due to the simple nature of the PLCs, programs can be carried out faster. One reason contributing to the faster speeds is the need for PLCs to be placed close to the devices. A critical point that is kept in mind when producing a PLC is, after all, to perform high-speed functions. As stated previously, PLCs are restricted to one device, whereas DCS provides the flexibility of connecting to many devices simultaneously. Consequently, since DCS handles multiple processes with various control points, it can be relatively slow to execute programs. It, however, does have a high-speed network connection which helps managers carry out at a manageable speed. A reason why DCS are not as fast may be because the focal point of a DCS is to perform bulk processes. Therefore while a PLC takes approximately a decisecond to respond, a DCS takes around 30 milliseconds.
Which Is Better For Repetitive Tasks
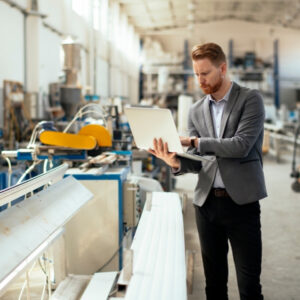
The majority of processes carried out are very monotonous. This has been one of the main reasons for transitioning to automation and why PLCs have been the first choice. Since PLCs can focus on specific processes, they can execute repetitive processes more accurately and consistently. While the flexibility DCS offers allows managers to perform multiple performances in bulk and parallelly, this also puts a traditional DCS at risk. The DCS could be open for attack by unwanted interferences originating from any one of the devices or processes connected to it. As a result, there is a tendency for DCS not to carry out repetitive tasks as efficiently and face downtime more occasionally.
Does It Need Human Interaction?
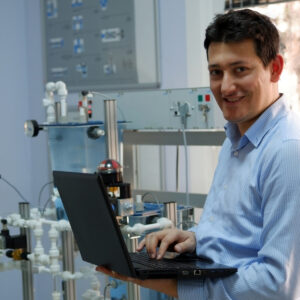
PLC does not require humans to take action. As it precisely controls repetitive tasks, humans can simply let the PLC have control of automating mundane processes and rely on them to be consistent in quality. A DCS, on the other hand, requires more human interference. Human interaction can also be assessed by the nature of the architecture of a PLC and DCS. A PLC consists of controllers, IO modules, HMIs and engineering software, making it a relatively simple and flexible architecture. A DCS, on the other hand, includes controllers, IO systems, database servers, and engineering and operating servers which is quite complicated. To ensure the smooth functioning of the architecture, humans will have to monitor its progress constantly, and where the process is complex, it will require greater attention.
Cerexio PLC and Instrumentation Setup: A Compact Solution that Infuses Both PLC and DCS Features
Connect with us to learn more about how Cerexio offers an upgraded version of a PLC.
Why You Should Opt For Either A Solution That Combines A PLC and DCS
You can gain unique advantages and, at the same time, face disadvantages when adopting a traditional PLC and DCS system. While a broken PLC could halt the entire process, a DCS can continue to function independently of any errors in a specific process. If you hold a large factory, you may think that DCS is a better option based on its flexibility. However, remember that DCS are slower processing speeds and do not always guarantee reliability. To merge the advantages PLC and DCS offer and cross out each disadvantage, you should consider a software vendor that integrates both. You will then have a compact solution that is perfect for small or large enterprises and will be a financially feasible investment in the long term. Cerexio, one of the leading software vendors in Asia and the world, offers a one-of-a-kind solution that should not be missed.