Did you know that manufacturing as a whole entity carries various sub-components, commonly known as manufacturing types? One of the main manufacturing types is repetitive manufacturing. This seems to be used in the production of automotive elements, construction components, etc. When you walk down the path of business with this repetitive manufacturing, technology is something you cannot stay away from. Why? That is because the implementation of the right technologies will help you expedite your production on a large scale. Digital Twin is one such innovation that most of the industrial companies in Singapore that depend on repetitive manufacturing rely on.
In this article, we concentrate on the employment of Digital Twin technology in repetitive manufacturing in Singapore.
What is Digital Twin?
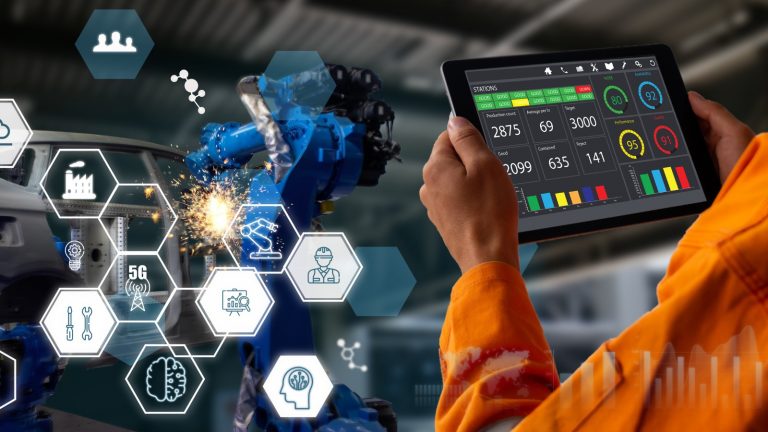
As an initial step, let us unlock the beauty of this technological pinnacle: Digital Twin. This is the way to create ‘virtual replicas or representations’ of physical systems, products, or processes through its power to combine real-time data with advanced modelling and simulation tools.
Yes, you can say this tool copies the physical objectives or processes. However, those are not the only parts it can copy. These digital copies allow for thorough analysis, prediction, and optimisation via imitating the characteristics, behaviours, and functions of their physical versions.
They provide a dynamic, real-time visualisation of the physical object, letting experimentation, performance analysis, and ongoing monitoring occur without having a negative impact on the system itself.
It is more like bridging the physical and digital worlds with just one tool. In Singapore, Digital Twin mainly empowers the manufacturing industry to improve efficiency, predict maintenance needs, and simulate scenarios for innovation. However, it is not limited to manufacturing.
With a robust technology like Digital Twin in place, the goals of the manufacturing world cannot be limited, as this gives a twin energy to everything from planning and processing to decision-making.
What is Repetitive Manufacturing?
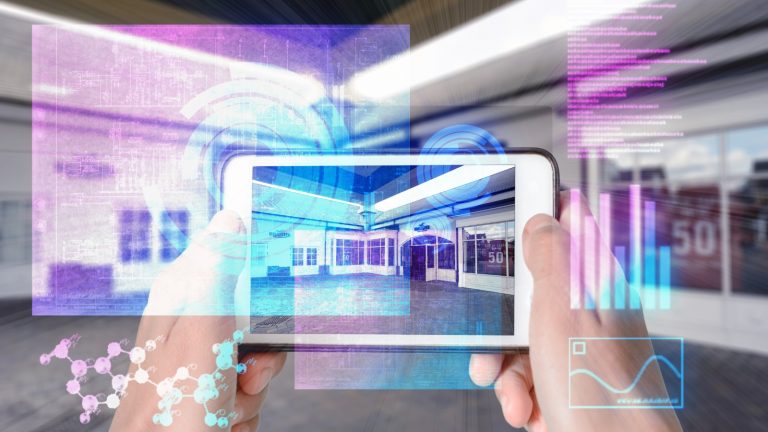
Now let us move on to identifying repetitive manufacturing. What exactly is it? This is a manufacturing process that usually follows a particular chain of activities and is illustrated by the constant and continuous production of vast volumes of identical or very similar items.
If you want to create things quickly and reliably, this strategy places a strong focus on standard operating procedures and makes use of assembly lines or automated machinery. This means it uses standard processes and machinery configurations to mass-produce things with little to no modification from the product design, and it requires very little change in the manufacturing process.
This type of manufacturing is not utilised everywhere. Repetitive manufacturing is commonly found in industries such as automotive, electronics, and consumer goods. But why? When you carry out these manufacturing tasks, high-volume output, consistency, and efficiency are top priorities for meeting market demands and achieving economies of scale.
The Top 5 Ways to Employ Digital Twin Technology in Repetitive Manufacturing
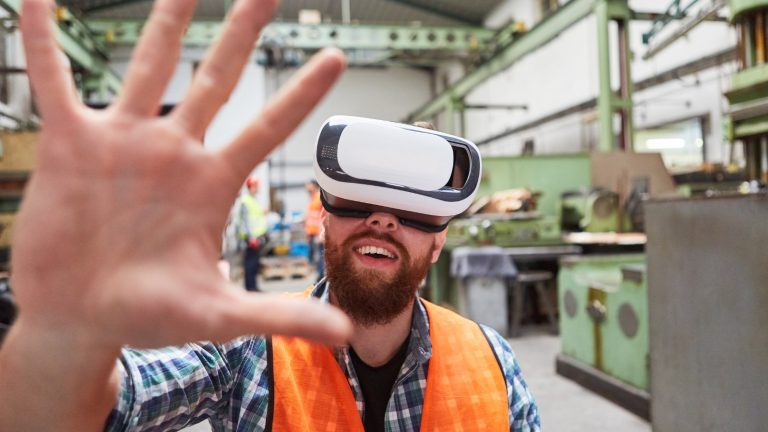
Customisation and Personalisation
This is one of the major expectations of the manufacturing industry, as the power to produce customised items will make you achieve a good position in the Singaporean market. This is the reason behind most of the manufacturing companies started using Digital Twin in the first place.
These capabilities truly empower repetitive manufacturing with its capacity for tailored adaptations within standardised production frameworks. You already know that it creates virtual replicas of products and processes. Therefore, manufacturers can simulate variations and customise individual units without disrupting the efficiency of mass production.
These virtual versions offer immediate modifications to parameters, features, or settings, allowing customised changes while preserving the overall efficiency of the production process.
This empowers companies to respond swiftly to unique customer demands or market trends without compromising the benefits of repetitive manufacturing. Plus, this ensures flexibility within a high-volume production environment.
Now you know that Digital Twin is able to provide a platform to optimise product variations and fine-tune specifications without compromising quality. On the other hand, it incorporates customised elements, enhancing customer satisfaction and market competitiveness without sacrificing operational efficiency.
Simulation for New Product Development
Singapore is a country where they always encourage new product developments through research. However, as a manufacturing company, can you really bear these expenses for physical developments? The truth is ‘NO’. These capabilities lie within the Digital Twin system and profoundly impact repetitive manufacturing by expediting and refining new product development processes.
As this helps to create virtual models of products and production environments, manufacturers can simulate various design iterations, test new concepts, and evaluate manufacturing processes without physical prototyping. This makes it easier to experiment quickly, resulting in the early detection and resolution of possible problems throughout the development stage.
On one hand, these simulations back up fine-tuning production lines and optimising workflows without any hesitation. On the other hand, this ensures that new product introductions seamlessly integrate into existing manufacturing systems.
Therefore, the obvious result is that manufacturing companies can minimise the time and resources typically required for new product development, ensuring smoother transitions from design to mass production.
Supply Chain Visibility
This offers a comprehensive, real-time view of the entire supply chain ecosystem. No more errors in the supply chain with Digital Twin!
It will look into the movement of raw materials, components, and finished products through simulations. With this technology in hand, manufacturers gain some outstanding insights into logistics, inventory levels, and production schedules.
As another way to optimise the entire supply chain, these digital representations encourage predictive analysis, allowing for the proactive identification of potential bottlenecks or delays. As a result, businesses can boost supplier coordination, reduce production schedules, and maximise inventory management by 200%.
Be in repetitive manufacturing or any other form of production, Digital Twin will take care of everything in your supply chain from A to Z.
Resource Optimisation
Unlike other types of manufacturing, repetitive manufacturing requires a heavy force of resource allocation. The Digital Twin plays an important role in enhancing this repetitive manufacturing by providing a dynamic and data-driven approach to managing and optimising resources within the whole production environment.
It will be easier to understand each point of resource allocation as the latter creates digital versions of manufacturing systems, equipment, and processes. With this ability in place, companies can simulate and analyse resource utilisation, energy consumption, and production efficiency in real-time. The benefit is that this encourages fine-tuning of operational parameters, identifying inefficiencies, and optimising resource allocation to maximise output while minimising waste.
Through continuous monitoring and analysis powered by this technological pinnacle, it makes sure that resources are optimally utilised to meet production demands within a repetitive manufacturing framework.
Process Optimisation
When it comes to this type of manufacturing, the stakeholders should put more focus on the process. The latter helps in the analysis, improvement, and refining of constant manufacturing operations in real-time. Digital Twin provides continuous monitoring and simulation by modelling physical production systems, which makes it possible to identify inefficiencies, bottlenecks, or areas for development.
Why do the manufacturers need it? This empowers manufacturers to experiment with different process configurations and adjust parameters. Also, it will simulate complex scenarios to optimise production efficiency, minimise downtime, while boosting efficiency by 100%.
If you feel like the process flow within your manufacturing business is getting slower day by day, Digital Twin is the best solution you can think of!
Cerexio-Powered Digital Twin Technology
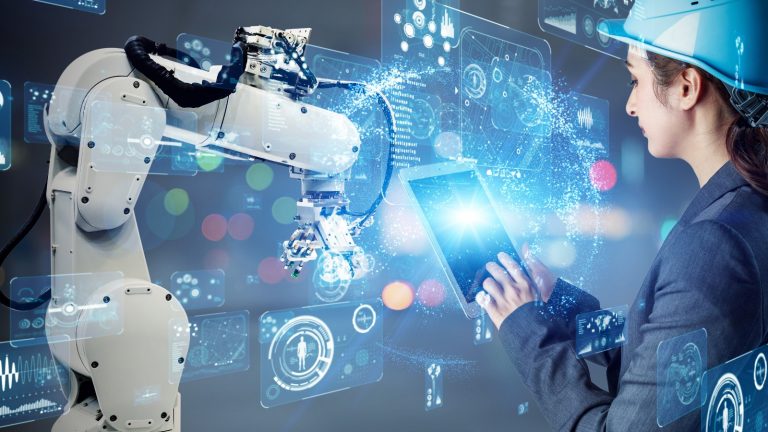
As one of the main technological capabilities that have been revolutionising the manufacturing industry, Cerexio-powered Digital Twin technology optimises the overall operations in a manufacturing environment with its ability to provide visualisation dashboards, create virtual models of everything from machines and systems to people, and provide seamless integration with the existing system to provide cutting-edge replicas of physical objects or processes. With Cerexio Digital Twin exposure, your manufacturing business is error-proof.
Making Way for Unchallenged Supply with Digital Twin
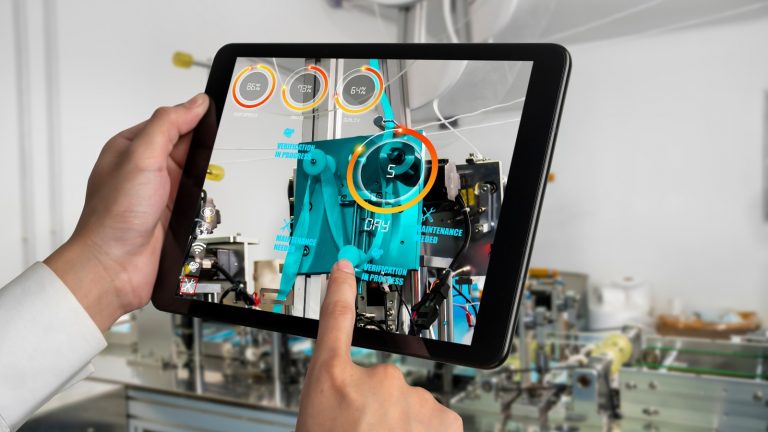
Repetitive manufacturing is where you need to put in 100% attention and effort to operate smoothly without errors. Digital Twin Technology is extending its arm for you to employ its capabilities to conduct an unchallenged supply to the market in Singapore.