Yield is one concept that has been introduced to the production world to save a vital range of resources and conserve them for future usage. While yield helps the manufacturers execute production performance improvements, saving money and resource allocations, The outcome of yield optimisation cannot be limited to one or a few aspects, as it is a wide and collaborative ecosystem. ‘Digital Twin’ is one technology that the manufacturing domain relies on when carrying out yield initiatives for their production lines.
In this article, we will discover the employment of Digital Twin in manufacturing yield optimisation and the ways it can be done perfectly.
What is Digital Twin?
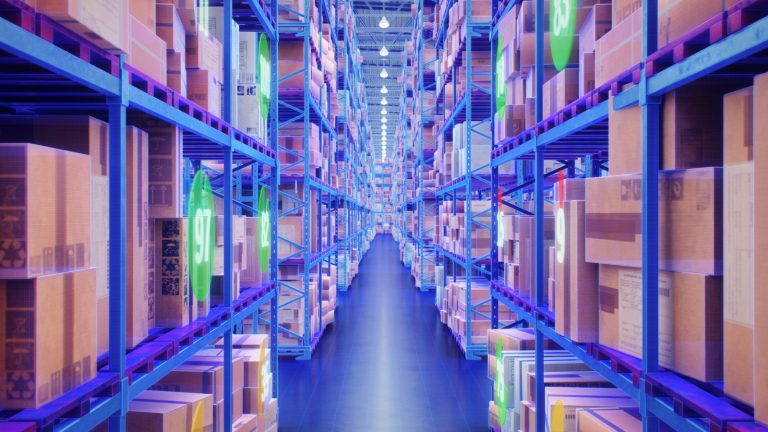
Before going further, let us start by introducing Digital Twin technology.
You might already know that it is a digital representation of a physical object, process, or system. This technology offers full-scale real-time monitoring, analysis, and simulation to understand the hidden essence of the above-said components.
It is actually a mirror! The latter reflects the behaviour and characteristics of its physical counterpart through the virtual collaboration of an immersive ecosystem. In the end, it offers you predictive insights and optimisation ideas.
When it comes to manufacturing specifically, Digital Twin is utilised across various stages, from design and prototyping to production and maintenance. Manufacturers create virtual replicas of equipment, production lines, and even entire factories nowadays. This strength supports them in monitoring performance, simulating scenarios, optimising processes, and predicting maintenance needs.
Since Digital Twin technology has an outstanding ability to integrate with other technologies such as Industrial Internet-of-Things (IIoT), Predictive Analytics, GIS, etc., it covers all the aspects that come under its digital thread to encourage everything from process optimisation to non-linear supply chain networks to collaborative decision-making.
What is Yield Optimisation?
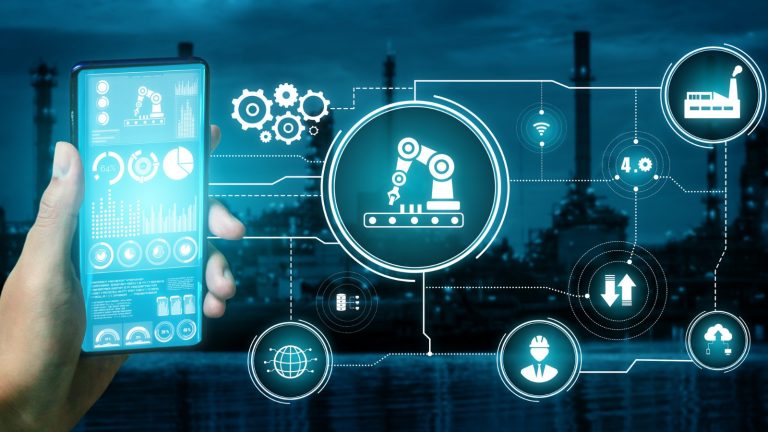
In the manufacturing world, this refers to maximising the output of high-quality products while minimising waste and defects. It involves improving processes, materials, and resource utilisation to achieve the highest possible yield rate.
But why is this such a popular concept? The latter is crucial in the production process to enhance efficiency, reduce costs, and maintain competitiveness to enhance brand resilience, all while keeping efficiency and sustainability promises alive.
Manufacturers benefit from yield optimisation by increasing profitability through higher production output, reducing material and resource waste, and improving product quality and consistency. It helps them to meet customer demand effectively and stay competitive in the market.
The ultimate outcome of the latter is that manufacturers achieve the highest possible return on investment by maximising the output of valuable products. With the highest possible yield optimisation, there will be no waste and no inefficiencies.
Top Ways to Employ Digital Twin for Yield Optimisation
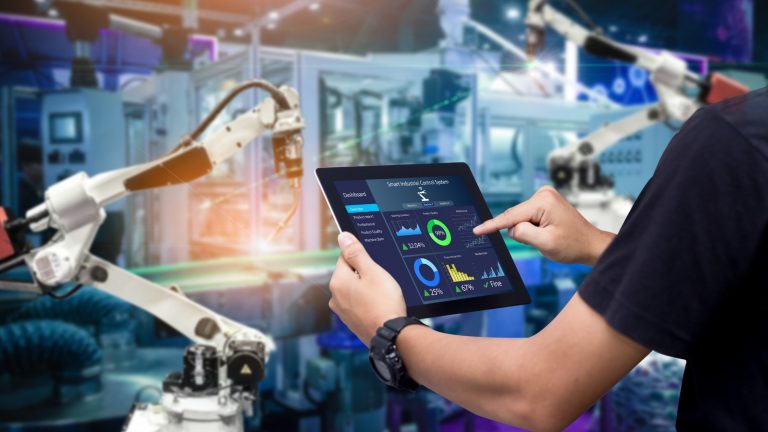
Real-time Monitoring and Simulation
One of the best ways to implement the latter is for the monitoring aspect of the processes. As the technology can keep up with continuous monitoring of production processes, it provides valuable insights into equipment performance, material utilisation, and product quality adherence within the manufacturing operations framework.
When you can analyse data in real-time, you can identify inefficiencies, bottlenecks, and potential issues that may impact yield adversely from root cause analysis until supply chain disruptions. Furthermore, digital twins facilitate the simulation of various production scenarios. This allows manufacturers to predict the outcomes of process modifications or parameter adjustments without disrupting actual manufacturing operations.
Due to the real-time monitoring and simulation capabilities provided by Digital Twin, manufacturers can fine-tune their operations as per the expected standards. Plus, they can reduce waste, improve efficiency, and ultimately enhance yield optimisation in manufacturing processes, which leads to maximised ROI.
Identifying Gaps in Yield
This benefit is interwoven with the above-mentioned point. When you can look into the production processes more closely, you can identify the gaps hidden inside them. It would be beneficial for the manufacturers to comprehend the holes in existing yield operations through comprehensive data analysis and simulation capabilities before going for new developments.
This is exactly what Digital Twin does! The procedure starts with creating virtual replicas of production processes. Then it enables manufacturers to compare real-time data with ideal performance metrics, revealing discrepancies and areas for improvement.
These virtual models support the simulation of different scenarios, allowing manufacturers to pinpoint inefficiencies, bottlenecks, and the root causes of yield losses. Through advanced analytics, Digital Twin can analyse historical data to detect patterns and trends, highlighting recurring issues that have the potential to lower yield optimisation.
This capability doubles when it is incorporated with predictive analytics. With predictive modelling in hand, manufacturers have the capacity to predict the impact of process changes or interventions on yield outcomes.
Process Optimisation through Research and Development
Generally, yield initiatives are designed and developed during production processes. However, it will be an unbearable cost for this research and development from the manufacturer’s end. The other thing is that these try-out sessions have two possibilities: they can touch the right point, or they can go wrong. It is a 50-50 chance.
Digital Twin is the ideal technology for yield optimisation development as it allows you to create virtual replicas of new implementations. Since this is not implemented in the real world, the development cost is very low. The latter helps manufacturers experiment with innovations and process improvements in a risk-free virtual environment.
Manufacturers are able to assess the possible effects of new methods, technologies, and techniques on yield optimisation by using simulation and analysis. This makes it possible to investigate other manufacturing techniques, materials, and setups without interfering with current business processes.
Digital Twin also gives companies the ability to carry out in-depth analysis and experimentation in order to determine the best approaches for raising yield, cutting waste, and boosting productivity.
Quality Control and Defect Detection
Quality receives the utmost importance in the manufacturing domain. Digital Twin technology helps manufacturers keep these quality standards to the maximum level. How is that possible?
It occurs when the latter gives manufacturers the power to compare expected quality standards with actual performance metrics within its data analysis framework. Through continuous monitoring of production data, anomalies and deviations from quality specifications can be detected in real-time.
Digital twins facilitate root-cause analysis by correlating quality control errors with specific process parameters or equipment conditions. Additionally, by simulating various scenarios, digital twins can predict potential quality control issues before they occur, allowing for proactive interventions to prevent yield losses. This capability enables manufacturers to implement corrective actions promptly, minimise defects, and maintain consistent product quality.
On the other hand, since this easily couples with Predictive maintenance, it backs up initiatives for machine setup time reduction, downtime reduction, etc., which leads to overall equipment effectiveness (OEE) improvement.
Cerexio-Powered Digital Twin Technology
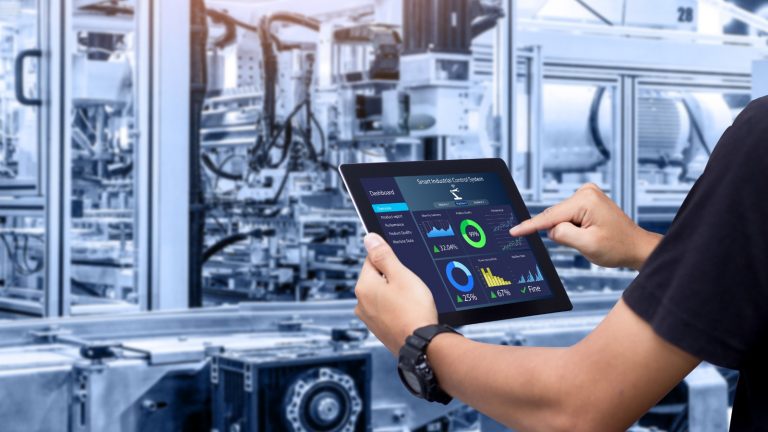
Cerexio Digital Twin technology is the ideal solution for the manufacturing domain in their quest for optimal yield levels. Since our solution is dominated by Industry 4.0 capabilities, it gives manufacturers an extra hand to foresee the facts that limit their full potential in production. Cerexio Digital Twin helps you achieve the maximum yield of materials, chemicals, and extruders as it drags everything under a singular dashboard.
Extract the Best with Digital Twin
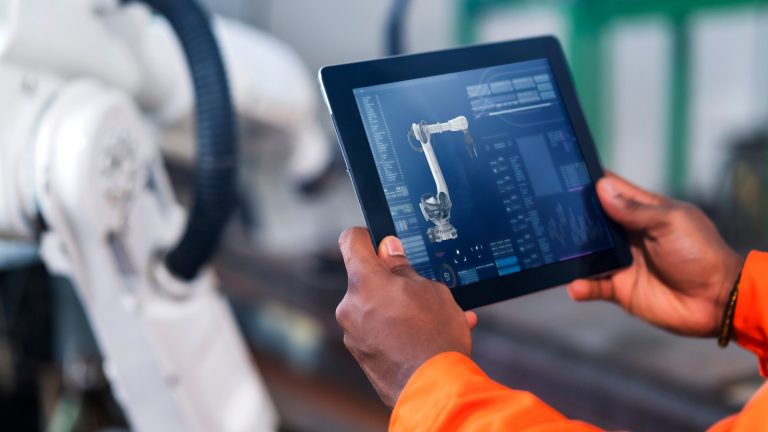
It is an outstanding trend that manufacturers are moving towards sustainability and conserving limited resources, thinking about future generations. The Digital Twin is the technological arm you receive to magnify this capacity by ten more times.