In this article, we will explore how chemical production companies can employ the power of AI to meet industry demands in today’s Singaporean landscape.
What is AI Technology?
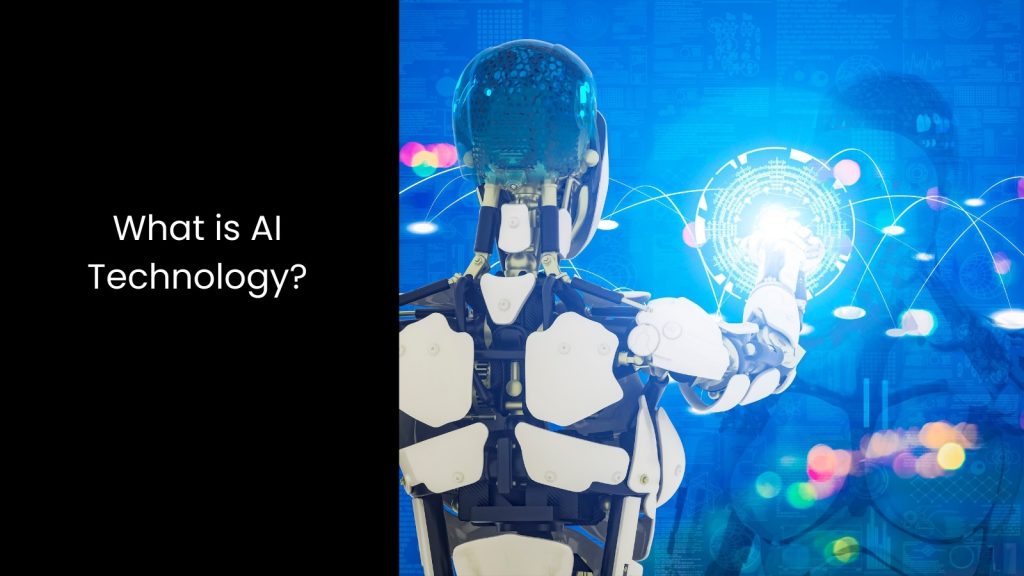
These intelligent systems analyse vast amounts of data collected from sensors and machines in real time, helping companies monitor production lines, predict equipment failures, and ensure consistent product quality when it comes to manufacturing.
AI algorithms optimise complex processes, saving energy and resources by fine-tuning production conditions. No matter what domain is concerned, AI aids in tracking everything, forecasting demand, and minimising waste, which leads to improved sustainability.
As this particular technology or capability can be easily integrated into other systems, its powers can be doubled. One of its main strengths is predictive maintenance, for sure. With this in hand, any industry can analyse the data they keep receiving from various ends under a single screen.
What are the Challenges Chemical Production Companies Encounter?
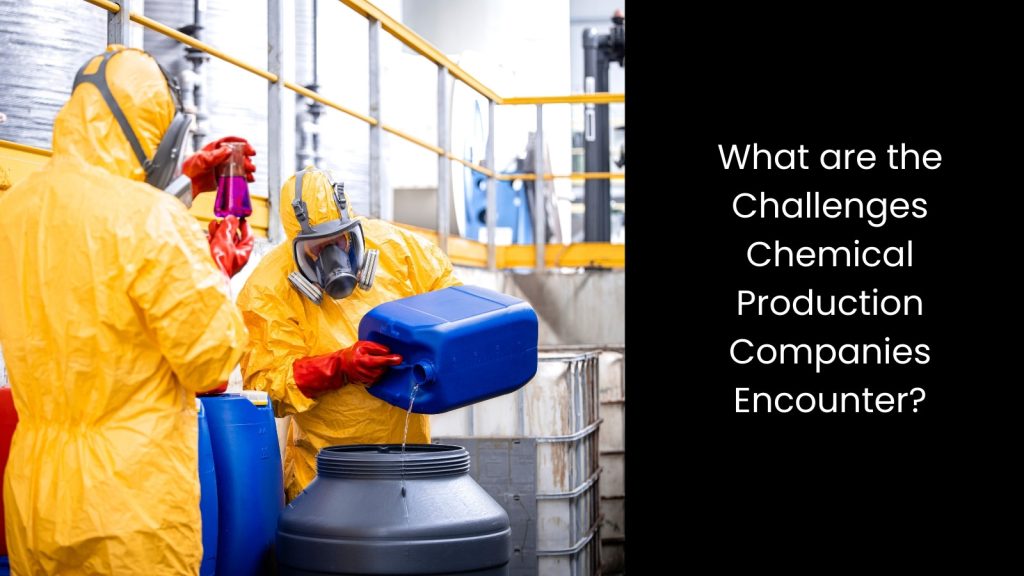
- Adapting to strict safety and environmental regulations, which vary across regions.
- Managing complex chemical reactions and intricate production processes that require precise control.
- Avoiding quality issues or production downtime.
- Securing a steady supply of raw materials is quite challenging due to market fluctuations, transportation delays, and supplier inconsistencies.
- High energy usage in chemical production.
- Operational costs and environmental impact.
- Handling hazardous materials and equipment.
- High risks for workers necessitate rigorous safety protocols and advanced monitoring systems.
- Maintaining consistent product quality across batches.
Top Ways AI Aids Chemical Production Companies
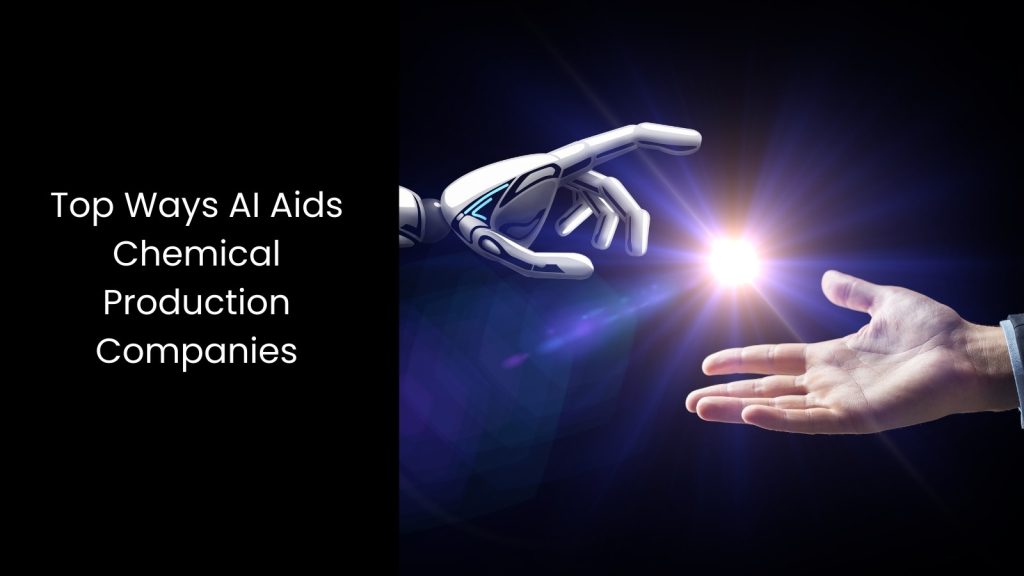
Real-Time Monitoring and Control
AI-enabled sensors and systems provide real-time monitoring of plant operations, allowing for rapid adjustments to maintain safe and efficient conditions. These sensors capture vast amounts of data from equipment, raw materials, temperature, and chemical reactions, which AI algorithms analyse instantly. This constant data analysis helps production teams detect anomalies or potential issues before they escalate, such as equipment malfunctions or unsafe temperature rises, enabling preventive action that minimises downtime and costly repairs.
Since it is possible to track real-time conditions, AI supports optimal reaction controls. This will ensure that all processes maintain quality standards and avoid deviations that could impact product consistency.
Again, when it comes to warehousing, AI-driven monitoring manages storage conditions like temperature and humidity, which are critical for chemical stability, reducing the risks of product degradation. AI also helps chemical companies meet strict regulatory requirements by constantly monitoring environmental compliance factors, such as emissions and waste levels, and alerting teams if levels approach limits.
Enhancing Worker Safety
These risks not only threaten worker safety but also disrupt operations and lead to costly damages.
This is when AI technology helps enhance safety within these plants by actively monitoring for these dangers and providing timely alerts. AI-powered safety systems monitor hazardous conditions and provide early warnings, reducing risks and ensuring a safer environment for employees in chemical plants. These systems use AI-enabled sensors to track environmental factors like air quality, temperature, and gas levels in real-time.
When conditions indicate a potential threat, such as a gas leak or sudden temperature rise, the AI system immediately alerts staff to take protective measures. AI also detects subtle patterns that might lead to equipment failure, like unusual vibrations or pressure changes, allowing workers to perform maintenance before accidents occur.
In addition to early warnings, AI integrates with automated shutdown procedures, instantly halting processes if critical thresholds are met, which prevents escalation of dangerous situations. Beyond hazard detection, AI-powered safety tools provide intelligent insights into worker behaviour, alerting management if somebody enters restricted zones or forgets protective gear.
Process Optimisation
Manual data analysis usually falls short because it is time-consuming and lacks the precision to capture subtle changes in real-time, leading to inefficiencies and inconsistencies in product quality. Additionally, achieving a balance between high output and low energy usage becomes difficult without advanced tools, as small adjustments in one area can significantly impact overall production costs.
This is no longer an issue when you have AI technology. It has the capacity to address these challenges by introducing real-time data analysis and advanced algorithms that streamline every aspect of the production process. AI algorithms analyse data from production processes to identify inefficiencies and optimise reaction conditions, temperatures, and other variables, boosting output quality and energy efficiency.
With AI, companies monitor thousands of data points simultaneously, gaining precise insights into each step of the production chain. So, with AI, every aspect is fully covered and optimised.
Quality Control
That is because even small variations in ingredients, temperature, or reaction time can impact the final product’s performance. Maintaining consistent product quality across batches requires meticulous monitoring and can lead to waste if standards are not met.
Traditional quality control usually involves manual checks and sample testing, which only cover a fraction of each batch and can miss subtle changes, leading to inconsistencies and wastage. However, since now they have AI technology, it can revolutionise quality control by providing real-time monitoring, rapid analysis, and precise adjustments to maintain high standards without excessive waste.
AI systems use advanced sensors to collect data on critical factors like chemical composition, temperature, and pressure at every stage of production. With this continuous monitoring, AI quickly detects any slight deviation from set quality parameters and sends alerts for immediate corrective actions. Through predictive analysis, AI anticipates potential quality issues by analysing patterns and trends from past production data, allowing companies to address problems before they arise.
Cerexio AI-Powered Solutions for Manufacturing Optimisation
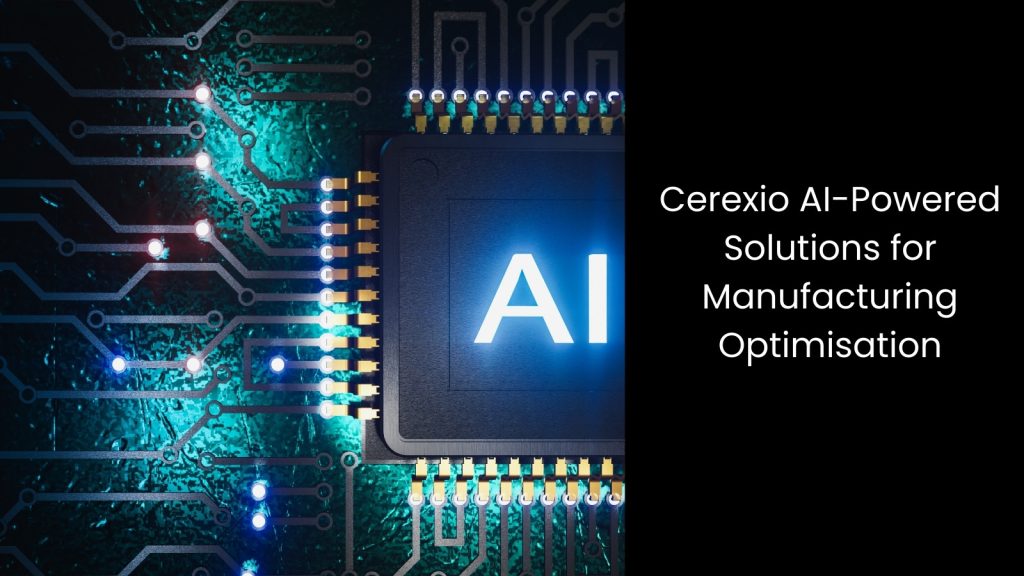
Cerexio has a variety of AI-powered solutions that drive manufacturing optimisation. Our advanced tools, like Cerexio MES and the Manufacturing Control Tower, are specifically developed using the powers of AI technology, combining other capabilities of Industry 4.0. Cerexio MES streamlines production workflows, boosts machine efficiency, and reduces downtime, while the Manufacturing Control Tower provides real-time visibility, enabling predictive insights and adaptive control. Together, these solutions enhance productivity, quality, and resource management across manufacturing operations.
Making Chemical Production Errorless with the Use of AI-Driven Solutions
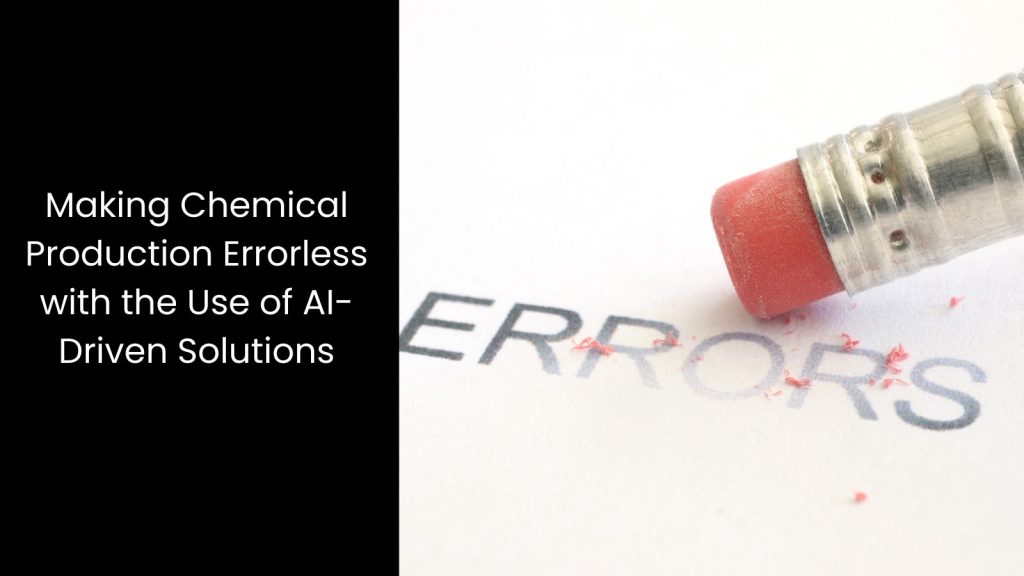
Can you see the transformation AI brings to chemical production? With AI-driven solutions, chemical production companies can perfect their processes, boost worker safety, and meet high-quality standards effortlessly. It is not that tough to create a world where errors and risks are less and innovation flourishes through the power of AI.