Manufacturing starts with planning and blooms with planning. This indicates how important planning is for a manufacturing company. When it comes to planning everything out, from inventory and processes to warehousing and packing, production planning requires a lot of attention. In one way, production planning acts as a strategy to receive the maximum yield; in another, it is a transparent grid for the production to be made.
In this article, we reveal how to do production planning for manufacturing in this dynamic business landscape.
We will know
What Is Production Planning & Why Is It Important?
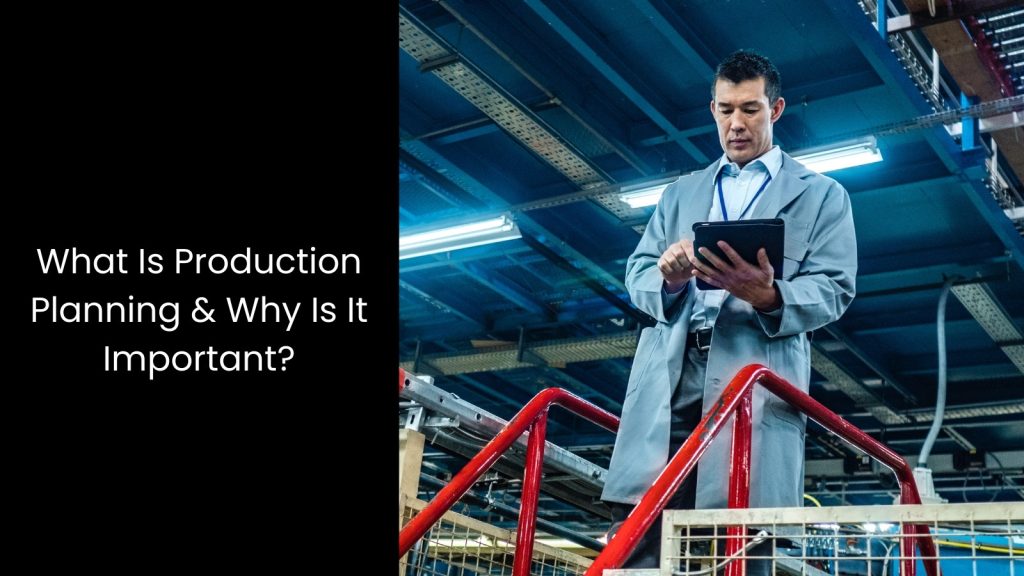
- First of all, production planning is the strategic process of organising and coordinating every step required for efficient manufacturing.
- What is included in a manufacturing plan? This is a complex mechanism, and it involves determining what products to create, establishing timelines, deciding on manufacturing methods, and identifying the resources needed. When a manufacturer develops a solid production plan, the company basically aims to streamline processes, align supply with demand, and reduce delays and inefficiencies. This process is crucial for optimising resource use and eliminating bottlenecks by ensuring human and material resources are available when needed.
- If there is effective planning, it can reduce production costs by minimising waste and avoiding overproduction, which helps maintain lean operations. It also plays a critical role in enhancing product quality, as it emphasises precision, quality control, and consistency across manufacturing processes.
- When manufacturers prioritise proper planning, they can better forecast demand and meet customer expectations, ensuring timely product delivery. This approach improves productivity, strengthens operational control, and supports higher customer satisfaction.
- This is why today’s manufacturing, as a realm, entirely concentrates on production planning in the first place.
How to make a manufacturing plan?-Top 5 Ways
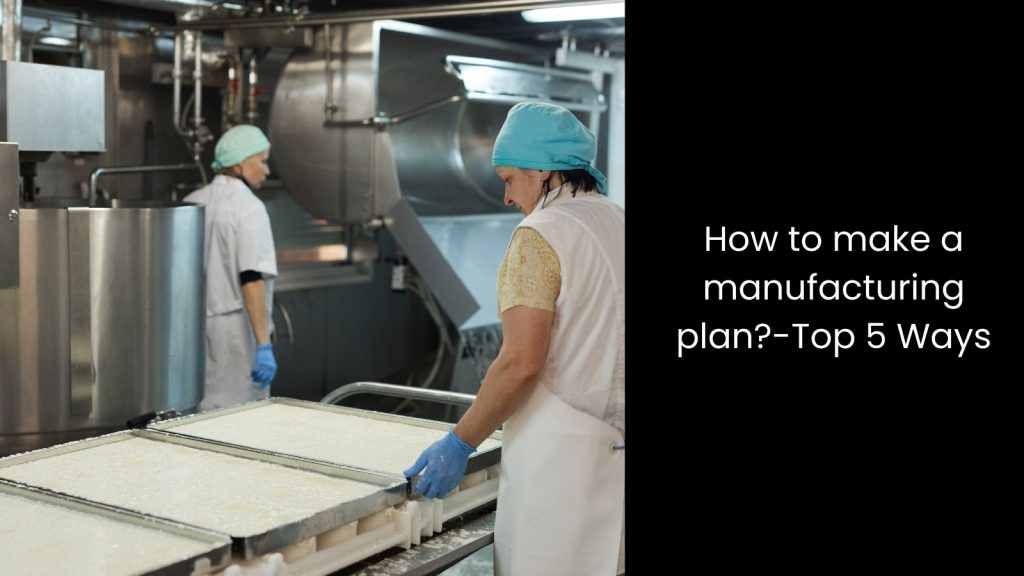
Designing a Master Production Schedule (MPS)
Master Production Schedule, or MPS, as many know, involves crafting a comprehensive schedule that clearly specifies what products need to be made, the exact quantities required, and the precise timelines for production. This ensures that the manufacturing process stays aligned with demand forecasts, enabling businesses to meet customer expectations efficiently.
Since it focuses on the details, an MPS helps manufacturers coordinate resources, avoid bottlenecks, and maintain a steady workflow. It bridges the gap between demand and supply, offering a clear roadmap that keeps production organised and adaptable to market changes.
It truly has numerous benefits. As you can see, creating a well-structured MPS reduces waste, enhances resource utilisation, and eliminates the risks of overproduction or stock shortages. It also boosts productivity by providing clarity for teams, establishing better communication, and minimising last-minute adjustments that disrupt efficiency.
Designing an MPS does not just streamline operations; it empowers manufacturers to operate smarter, respond faster to changes, and achieve sustainable growth by balancing operational efficiency with market demands.
Optimising Inventory Management
This is one way that stands as a crucial pillar for effective production planning in manufacturing.
It revolves around maintaining the right balance of raw materials and finished goods to prevent overstocking and avoid the disruptions caused by stockouts. When you carefully manage inventory levels, you can create a smooth and uninterrupted production flow that aligns with operational goals. This approach not only ensures that production runs efficiently but also minimises unnecessary costs associated with excess storage or emergency procurement.
When businesses optimise their inventory, they can allocate resources more effectively, reduce waste, and enhance overall productivity. It empowers manufacturers to respond promptly to fluctuations in demand without compromising delivery timelines or product quality.
Furthermore, well-managed inventory systems pave the way for better coordination across supply chains. Plus, it ensures that every component required for production arrives on time and in optimal quantities. This sort of precision prevents delays, avoids costly errors, and strengthens customer satisfaction by enabling consistent order fulfilment.
Accurate Demand Forecast
When it comes to production planning for manufacturing, this certain strategy drives efficiency and ensures success.
If we look into this process, we can see it involves analysing market trends, historical data, and customer behaviour to predict the exact demand for products. If they can understand what customers need and when they need it, manufacturers can perfectly align production schedules, resource allocation, and inventory levels to match these demands. This is a kind of precision that eliminates the risks of overproduction or shortages, enabling a smoother production flow.
When the manufacturers have the capability to forecast accurately, this means that they can easily prevent wasted materials and excessive storage costs. Most importantly, the latter ensures the timely delivery of finished goods, which strengthens customer satisfaction. It gives manufacturers the ability to adapt to shifting market conditions, allowing them to make informed decisions that support agility and resilience.
What is more, demand forecasting contributes to better financial planning by providing insights into future sales and production requirements, helping businesses allocate resources effectively. This wise approach also reduces the strain of last-minute adjustments, minimises operational disruptions, and fosters a culture of consistency and reliability.
Focusing on Lean Manufacturing Principles
Lean manufacturing principles transform production planning into a highly efficient and effective process.
Since it eliminates waste and prioritises activities that add value, manufacturers can streamline operations and ensure that resources are used wisely. Lean manufacturing helps identify inefficiencies in production, such as overproduction, excessive inventory, or unnecessary delays and works to eliminate them, creating a more focused and productive workflow. This approach not only reduces costs but also improves the overall quality of products by maintaining attention to detail at every stage of manufacturing.
On the other hand, lean principles encourage businesses to continuously evaluate and refine their processes, creating a culture of innovation and adaptability. As it allows aligning production with real-time demand, lean manufacturing helps manufacturers respond quickly to market changes and customer needs without sacrificing efficiency. It also promotes better team collaboration, as clear goals and streamlined processes ensure everyone stays aligned.
So, obviously, the benefits extend to customers, as they are the ones who receive high-quality products delivered on time, building trust and satisfaction. Therefore, it is noteworthy that lean manufacturing does not just improve operational performance; it empowers businesses to stay competitive, reduce their environmental footprint, and achieve long-term sustainability.
Employing Technology for Optimisation
This is where the manufacturers can add greater value to their production framework as the technology makes processes smarter, faster, and more efficient.
Let us walk you through a perfect example of this. When there are AI-powered systems, they can analyse massive datasets to provide real-time insights and accurate demand forecasts, helping manufacturers make data-driven decisions. Also, Digital twin technology takes this a step further by creating virtual replicas of physical assets and processes, enabling businesses to simulate scenarios, identify inefficiencies, and refine strategies without disrupting operations.
Similarly, IoT devices play a central role in connecting machinery and systems, providing seamless communication and live updates that keep the production flow smooth. Likewise, Data analytics turns raw information into actionable insights, clarifying resource allocation, workflow bottlenecks, and performance metrics.
Together, these technologies not only optimise production schedules but also enhance flexibility, allowing manufacturers to adapt quickly to market changes.
Cerexio Solutions for Enhanced Production Planning in Manufacturing
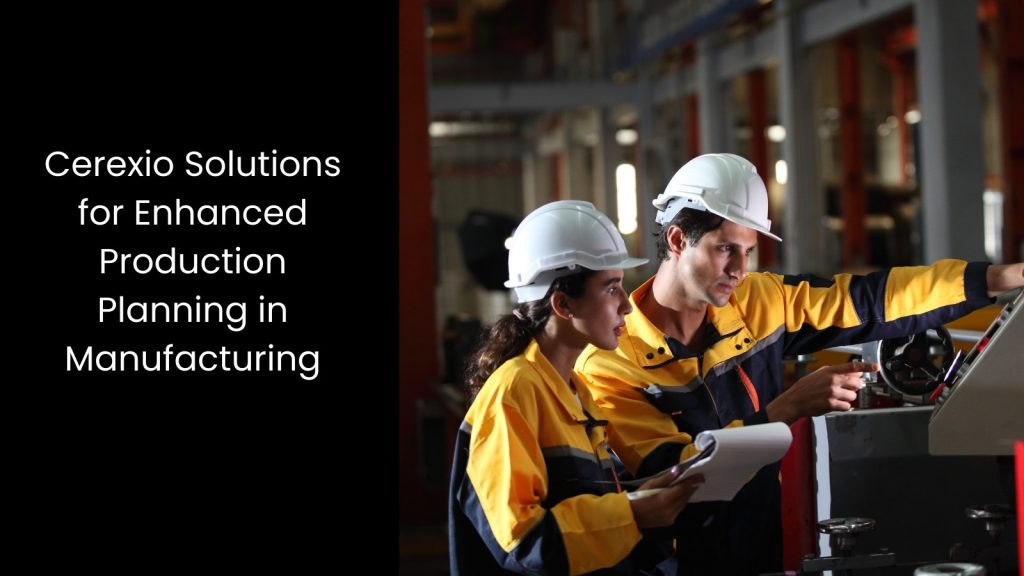
Cerexio presents a wide range of software solutions that can help manufacturing production planning, such as MES, Digital Twin System, etc., powered by Industry 4.0 capabilities. With our solutions, you can simplify your production mechanism, receive the best out of processes, and decrease the production time to a greater extent.
Simplifying Production Planning with Modern Tools
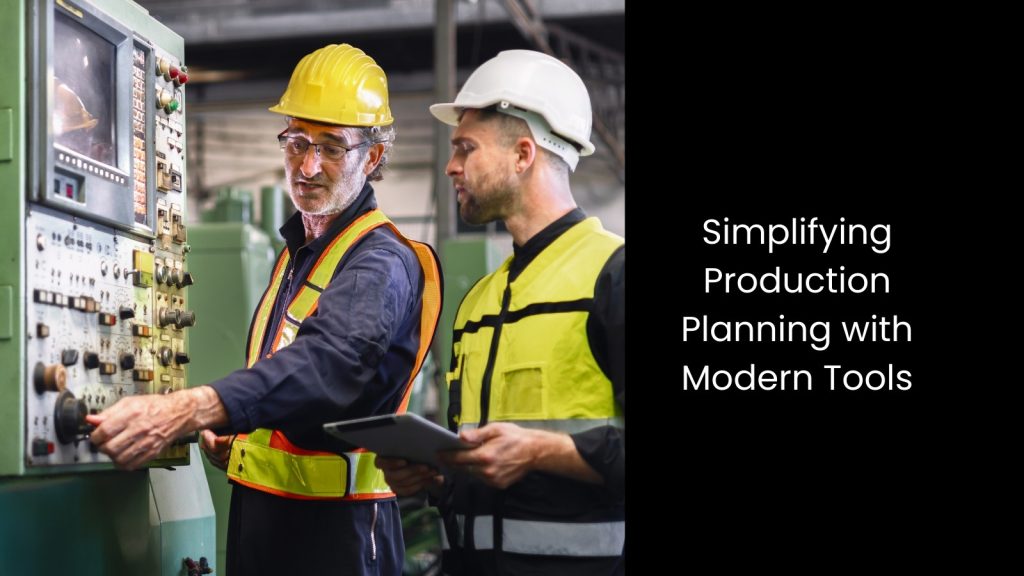
As production planning is a central aspect of the entire order fulfilment cycle, you must avoid production inefficiencies and complexities as much as possible. The best strategy to accomplish this is to implement modern tools that help you navigate challenges and simplify the planning process.