Quality Management Systems, also known in its abbreviated form as QMS, refers to a process implemented in a factory that demonstrates and confirms how the company has assessed whether the product manufactured meets the required standards in the industry. Quality standards generally differ from industry to industry. As manufacturing is an aspect related to almost any sector, be it in automotive, aerospace or something else, there will be specific quality requirements manufacturers are required to meet. As a general rule, however, one of the essential quality standards manufacturers must meet is ISO 9001. Failing to do so generally indicates that the product built lacks safety and durability measures, all of which lead to a reduction in customer satisfaction and may, at times, even lead to the permanent closure of the factory. Due to these reasons, it is crucial to have a QMS in place. This article will summarise everything manufacturers need to know about QMS.
How Does A QMS Help in Maintaining Golden Standards?
The ISO standards are worldwide recognised premium targets for asset-centric organisations, allowing a uniform quality management framework regardless of the peculiarity of your organisation. Following an asset quality framework can help to simplify the process and reduce uncertainty regarding asset cost, risk and performance expectations. A framework may also enable your firm to expand by increasing efficiency and encouraging growth from the bottom line. These constant improvements may instil trust in your consumers and your board of directors, and other stakeholders whose decisions and engagement are critical in bolstering your manufacturing efforts.
Since asset managers are dealing with a common set of approved practices by complying with ISO standards, doing business with companies in different nations is much easier and more straightforward. This is why manufacturers must equip failure-proof QMS solutions that will help the company to seamlessly comply with asset management standards such as ISO 9001: 2015.
So how exactly does a QMS allow asset managers to achieve ISO 9001 standards? Adhering to quality management principles can result in higher-quality products and more delighted consumers, greatly boosting your company processes. Plus, in order to do so efficiently, a QMS must be implemented. It will help save your company from the danger of human mistakes, decrease quality costs, and guarantee you satisfy your industry’s quality requirements. The QMS continuously improves all your manufacturing quality processes using AI technology that tracks KPIs to keep optimising quality processes to get better with every passing minute. Also, employing a QMS is the easiest, fastest and most innovative way of conforming to and meeting compliance standards. Still curious? Here are 3 main ways how QMS can optimise your company’s adherence to ISO 9001 standards.
Features to Cut-down Quality Costs: Using a variety of capabilities, QMS may actually decrease your company’s quality costs while keeping you in compliance with ISO 9001 requirements. It prepares live reports that illustrate real-time metrics that visually pinpoint inefficient areas of your quality and production processes. The periodic review cycles can also routine evaluation of documentation automatically, ameliorating audit and conformance evaluation of your processes. It reduces wasteful production and otiose processes using Predictive and Prescriptive analytics tools that will drop poor quality production instances.
Tools to Downsize Human Error to Net-zero Levels: A quality management system reduces the need for paper data input and simplifies a two-step procedure into a single step. Workers may gather data in real-time on a simple electronic device, reducing the danger of typical transfer mistakes. Using the following capabilities, a QMS can minimise the frequency and severity of human errors: approving, drafting and counselling documents, using NCR forms to deal with potential non-conformances and having instant access to the complete document histories of all documents to track down inconveniences or mishaps in the documentation. Each employee in a quality management system works toward quantifiable goals. Human mistakes are reduced, and employees have a clear understanding of their quality objectives, ensuring that the organisation complies with this provision of ISO 9001:2015.
Modules that Verify Steadfast Consistency: Delivering a quality product that satisfies your consumers’ expectations is an important aspect of satisfying ISO standards. This implies you must consistently produce items that fulfil all of your company’s quality objectives. The key to accomplishing this is to ensure uniformity throughout your supply chain procedures. When you adopt a QMS, you must design particular standard operating procedures (SOPs) to reduce the risk of nonconformance while increasing productivity.
Furthermore, because a QMS is a centralised database that your team can access from anywhere at any time, your employees can align their efforts across the supply chain and work toward common quality goals, making it simple to meet customer expectations and consistently deliver a high-quality product.
Why Do You Need A QMS?
Manufacturers Are Legally Required to Comply With Corporate and Industry Regulations

Specific statutory requirements must be met to prove that the company upholds quality in its processes and finished goods. These requirements are set out by the “International Organisation for Standardisation”, which manufacturers, even in Singapore, must satisfy to claim the 1900 certification. There are two main statutory and regulatory requirements when implementing a QMS. This includes conditions that apply to company products or services and requirements for company processes and procedures. It denotes what specifications a company product or service needs to meet to be legally available for sale. These regulations, moreover, require companies to document every detail, ranging from design specifications to mandated tests. Each manufacturing company’s responsibility is to ensure such essential information and records are maintained and included in the QMS.
To Build a Reputation as a Trusted Manufacturer
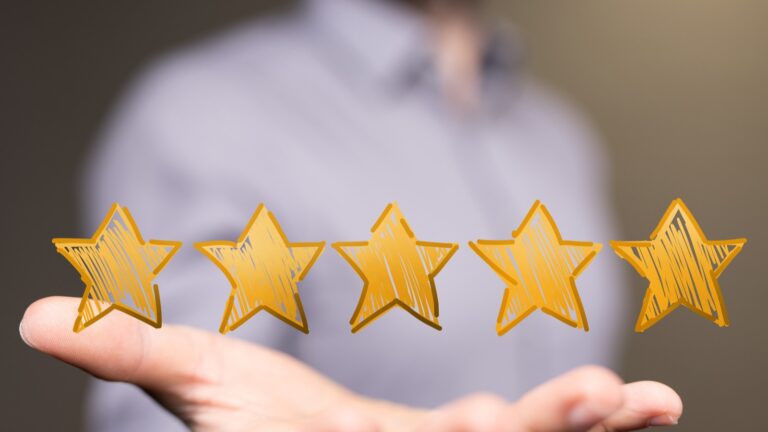
It should be noted that while some people may claim to have a standardised QMS, only a few have, in reality, done so. The difference can be spotted by checking whether the certification has been received. This would generally be featured on their website as the awarding body that provides the ISO certificate officially endorses and agrees that the manufacturing company’s quality standards are met. In a world where many industrial players strive to gain an edge over others, displaying the ISO certification that proves the QMS incorporated in the factory is an important tool in convincing the public and building a reputation of a trusted manufacturer. Manufacturers will have to undergo an internal audit, management audit, and corrective actions to make changes where gaps are identified.
To Have More Control
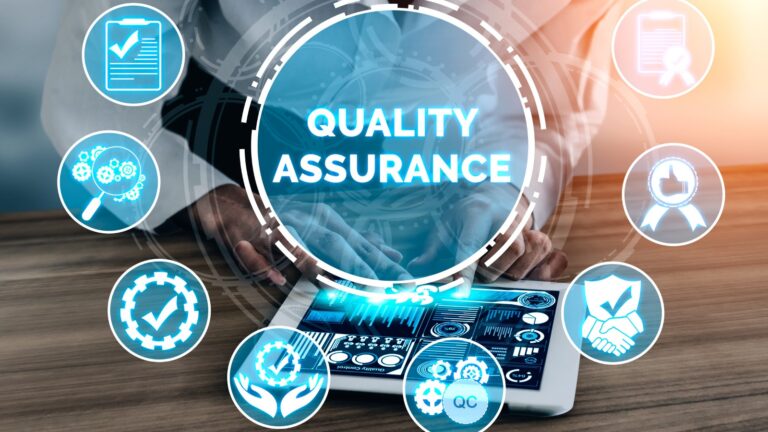
There are numerous ways a manufacturing factory can face downtime or increase waste. However, where a QMS is fully implemented, it introduces feasible process controls and workflows to ensure a quality end product is manufactured. As a result, there is a higher consistency rate, ensuring quality is maintained throughout time. It also leads to clear communication within the team regarding what needs to be met to consider an end product ready for sale. Generally, a factory with a QMS system also provides more control regarding the quality of raw materials. In other words, quality checks are not limited to production but extend to all phases from beginning to end.
To Eliminate Risks
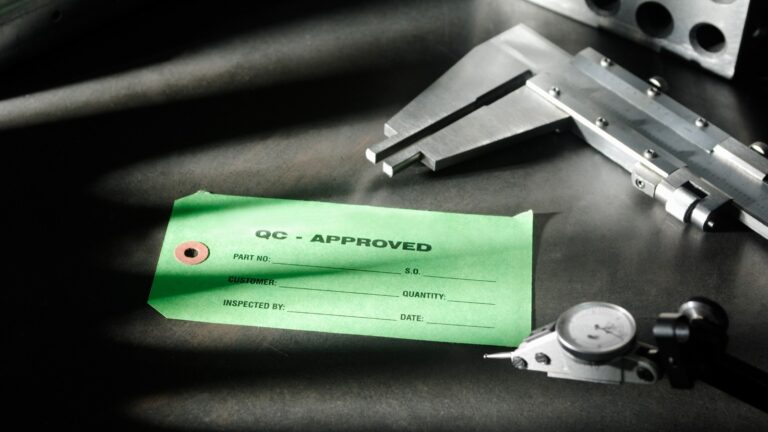
QMS offers a proactive step to prevent quality issues from occurring. In other words, a closed-loop QMS takes a risk-based approach to prevent waste from generating. It can foresee instances where a defect in quality cannot be seen until it has reached the last stages of manufacturing. With QMS, manufacturers can find the root cause of a quality-related issue and resolve it immediately instead of brainstorming why such a problem occurs in the first place. This risk-based approach also extends to the designing stage of a product so that no space is left for errors that could have been prevented.
Can You Integrate an MES with QMS?
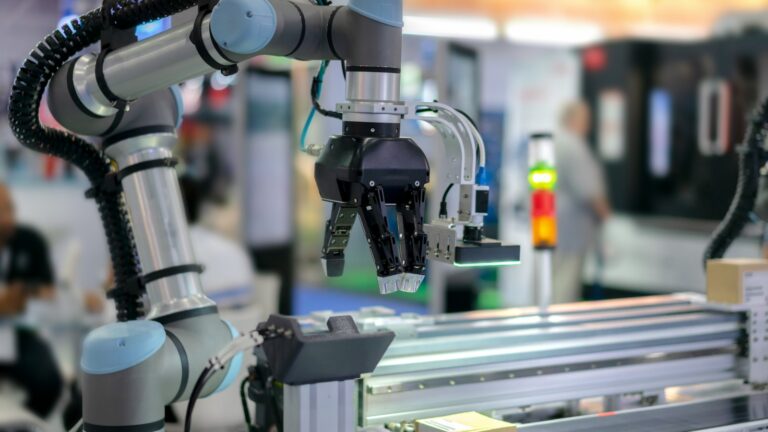
Manufacturers today are more familiar with manufacturing execution systems (MES). It has been a digital trending tool in the 21st century for anyone that wants to increase their profit margins. This is because an MES implements sustainable practices in the factory, eliminates waste and downtime, reduces carbon emission, increases the lifecycle of manufacturing assets and more. While this tool provides a range of advantages, not all MES solutions will have a QMS-like feature embedded in them. Hence, manufacturers may find it beneficial to integrate their QMS with MES. Such integration explicitly helps them improve the production stage by ensuring the item manufactured at the end is perfect. Manufacturers that have incorporated a QMS have been reported to have better mechanisms in place for real-time product risk evaluation and become trusted manufacturers for their clients.
Cerexio is Equipped With Reliable QMS Tools To Ensure You Meet Manufacturing Standards
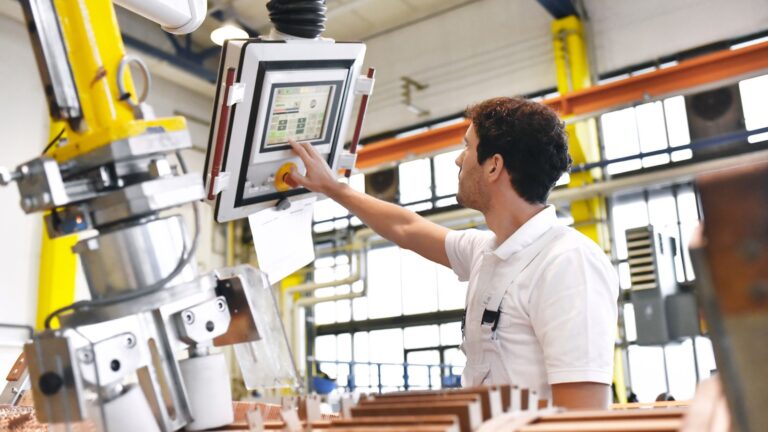
Cerexio MES integrated with Cerexio QMS features to ensure better quality standards. It is a powerful manufacturing tool that integrates and is compatible with other manufacturing systems such as ERP systems, PLCs, databases (Netsuite, SAP HANA), SAP systems, Warehouse Management Systems, and more. It is, therefore, a multi-faceted MES solution that takes all core manufacturing functions to the next level.
It smartly schedules production, enables data-rich relationships and automates mundane processes that prevent factories from maximising their productivity. As one of the few technology vendors that provide modern manufacturing solutions, Cerexio is equipped with state-of-the-art industry 4.0 technology. This includes digital twins, AI, ML, predictive analytics, and more. Using such technologies, Cerexio can meet quality standards by ensuring manufacturing assets are in their best condition. The solution automatically rules the root cause of the losses out of data tags to prevent plant-wide failures and inefficiencies from happening. It, moreover, accurately yields results in terms of quality standards, significantly helping manufacturers create long-lasting end products.
Connect with Cerexio to learn all the advantages its world-class MES solution provides.
Quality As The Ultimate Trump Card
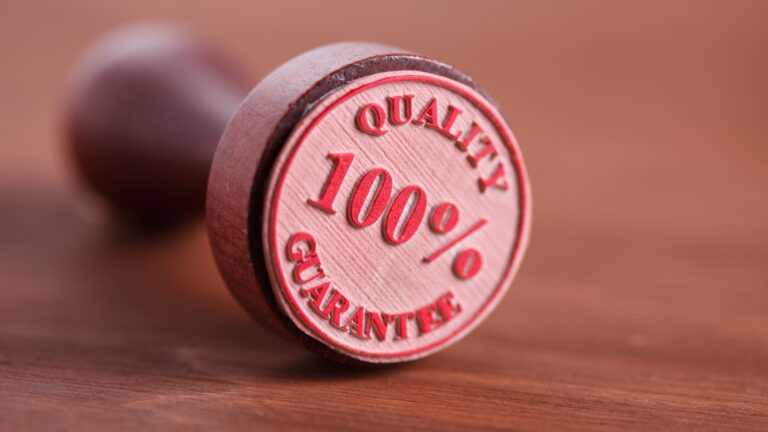
You can always have ample clients or sales, but ultimately, quality becomes the trump card when judging who the best manufacturing companies are. Holding an ISO certificate is similar to having a badge of honour, implying that the company is standing by a pledge to provide only the best, value for money and safest items to its consumers. Note that it is up to you to set out the documentation for quality management. A QMS will only help you to streamline and ensure that such quality measures are in place.