This article covers key ways to reduce yield loss in manufacturing.
What is Yield Loss in Manufacturing?
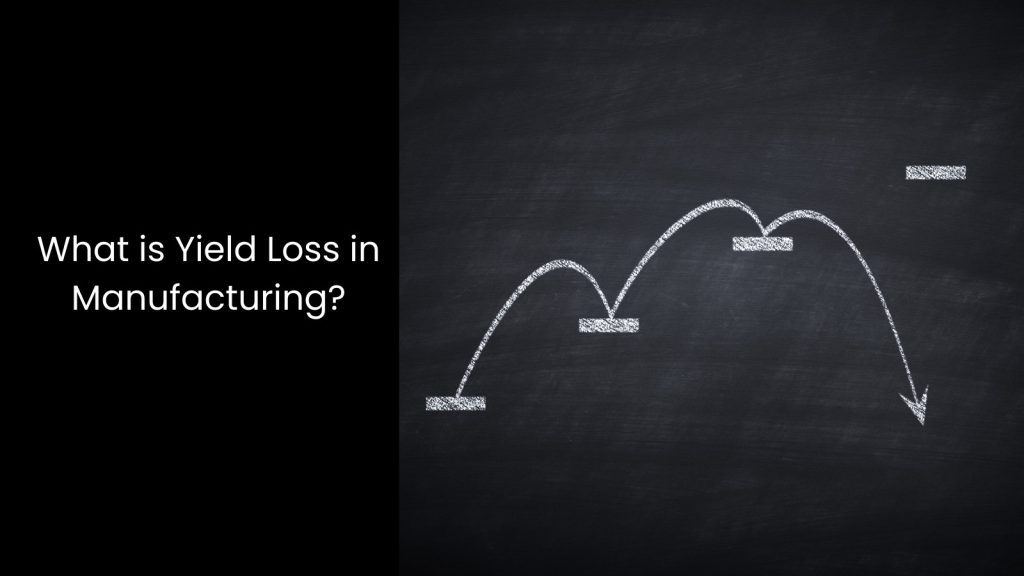
- Yield loss in manufacturing occurs when the actual output of a production process falls short of the expected output due to defects, inefficiencies, or wastage. It represents the difference between the total potential yield and the usable products produced.
- If we look into the matter closely, we can witness some factors like equipment malfunctions, human errors, inconsistent raw materials, and process deviations that contribute to yield loss. Manufacturers experience financial strain and reduced efficiency because of lower production volumes and increased costs in addressing quality issues.
- If they need to reduce yield loss, manufacturers must focus on maintaining quality control, minimising production waste, and optimising processes beyond traditional limitations. It is proven that businesses tend to achieve higher productivity and profitability when they minimise yield loss and maintain consistent production standards.
Top 5 Ways to Reduce Yield Loss in Manufacturing
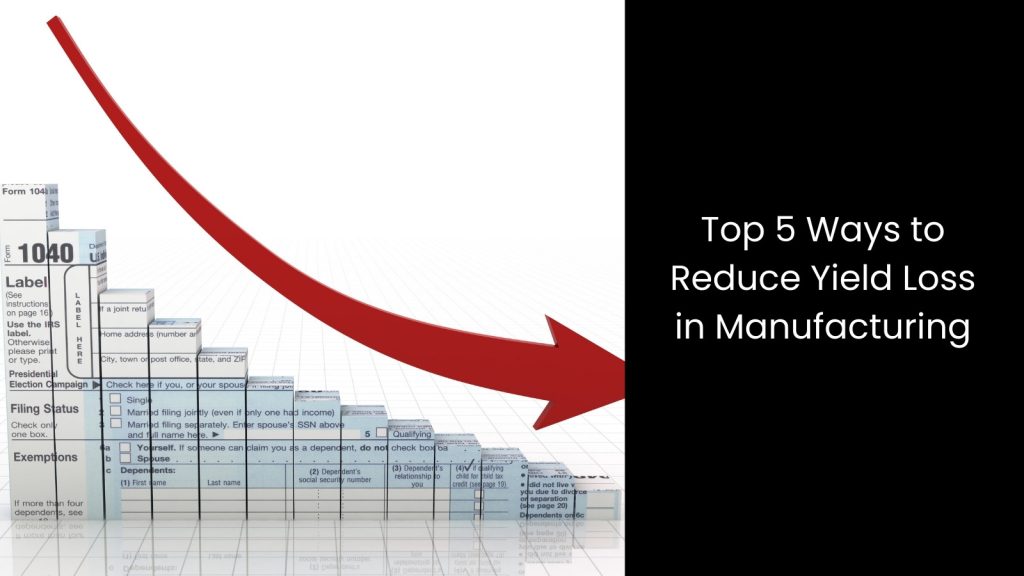
Implementing Root Cause Analysis (RCA)
Manufacturers can conduct RCA to identify the underlying causes of defects and implement corrective actions to prevent recurrence. When defects occur, manufacturers must avoid quick fixes and instead investigate what went wrong and why. This is where RCA helps uncover patterns and hidden factors causing yield loss, such as equipment failures, inconsistent raw materials, or improper process settings.
Manufacturers have the ability to use methods like the ‘5 Whys’ or fishbone diagrams to break down complex problems and find root causes. For example, if defective parts consistently arise, RCA might reveal that a machine requires recalibration or an operator needs more training. Addressing these findings immediately boosts production efficiency and product quality.
Further, RCA encourages data-driven decisions and prevents the same issue from reappearing, saving time and costs. Manufacturers who adopt RCA as a routine practice create a culture of continuous improvement, where every defect becomes an opportunity to refine processes. This approach ensures that production remains stable, waste decreases, and output aligns with expectations. Yield loss drops significantly when manufacturers focus on long-term solutions instead of temporary fixes.
Utilising Statistical Process Control (SPC)
The manufacturing industry can monitor and control production processes using SPC to detect deviations from acceptable standards and maintain process consistency. SPC relies on control charts to visualise process performance and identify variations that may lead to defects. These charts help teams quickly pinpoint when processes drift out of control, such as equipment wear, improper machine settings, or material inconsistencies.
When manufacturers catch these deviations early, they can correct issues before they escalate into significant yield loss. SPC also provides valuable insights into process trends, helping teams refine operations and reduce waste over time. For instance, consistent monitoring may reveal patterns like a specific machine overheating after extended use, allowing manufacturers to schedule maintenance proactively.
When focusing on process stability, SPC minimises fluctuations that cause defective products, improving both efficiency and quality. This method enables manufacturers to set precise benchmarks, ensuring every production stage stays within tolerance limits.
As evident, yield loss decreases significantly when manufacturers integrate SPC into daily operations because it promotes a data-driven approach to quality management.
Optimising Raw Material Quality
Manufacturers indeed can reduce yield loss if they source high-quality raw materials and work closely with suppliers to ensure consistent material specifications that meet manufacturing requirements.
The point is that low-quality materials tend to introduce defects and inconsistencies into production, causing higher waste and lower usable output. When manufacturers prioritise quality materials, they prevent many issues before production begins. This is when collaborating with reliable suppliers builds a strong relationship that guarantees regular quality checks and clear communication about specifications.
For instance, if a material’s tolerance or purity levels fall short, it can disrupt production processes or damage equipment. This will lead to significant yield loss. Testing incoming materials thoroughly ensures they meet all production standards, reducing the risk of problems further down the line.
This way, manufacturers can also adopt material traceability practices to identify and isolate any subpar batches quickly.
Implementing Advanced Quality Control Systems
These automated inspection systems, such as vision sensors and laser scanners, enhance precision and speed, eliminating human error and ensuring every unit meets quality standards. Early detection prevents wastage, rework, and delays, which contribute to yield loss. The real-time monitoring also tracks production trends, highlighting inefficiencies like equipment misalignments or process deviations that might lead to recurring defects.
This way, advanced systems integrate seamlessly with production lines, offering instant feedback and actionable insights that empower teams to optimise processes continuously. Moreover, advanced quality control systems create a streamlined operation where fewer resources go to waste, and output aligns with expectations.
Enhancing Process Standardisation
They can develop and enforce standardised operating procedures (SOPs) to minimise variability and human error during manufacturing. When everyone on the production team follows clear, detailed instructions, processes become more predictable, and the chances of defects or errors decrease.
SOPs outline specific steps, equipment settings, and quality checks, ensuring that tasks are performed the same way every time. This consistency helps prevent issues such as incorrect machine calibration, improper material handling or skipped quality checks, all of which contribute to yield loss.
Manufacturers who invest in training their workforce on SOPs improve efficiency and reduce misunderstandings that can lead to production delays or defective products. Regularly reviewing and updating these procedures keeps them aligned with current production goals and technological advancements. Process standardisation also makes it easier to identify and address the root causes of any deviations, as every step of the operation is clearly documented.
Cerexio Solution for Gaining Maximum Yield in Manufacturing
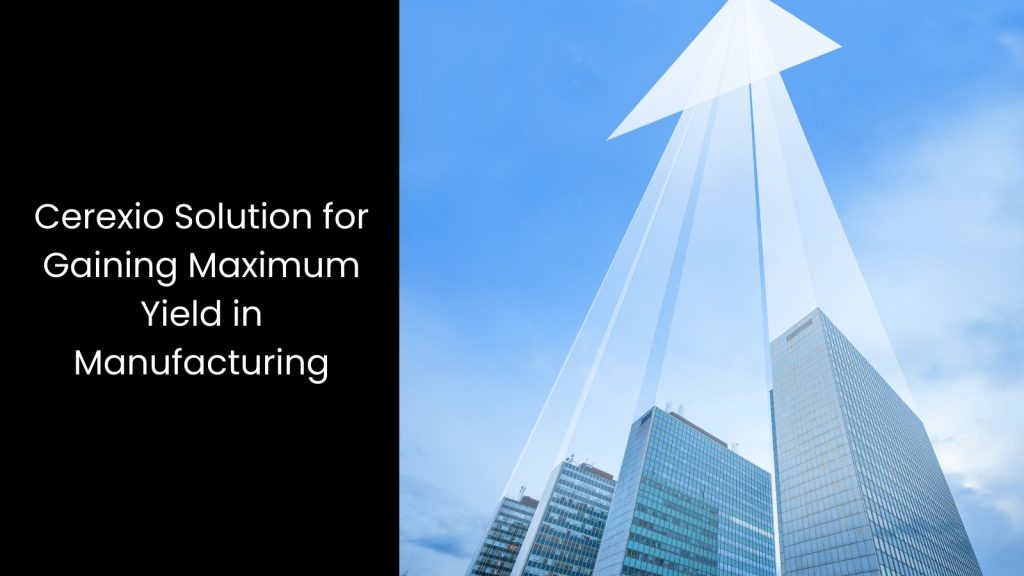
Cerexio Production Yield Optimiser Syetm helps manufacturers achieve maximum yield as our solution deploys advanced analytics, real-time monitoring, and AI-driven insights. This system detects inefficiencies, predicts potential defects, and streamlines processes to reduce waste and improve productivity. Its automation capabilities ensure consistent quality, while comprehensive data integration empowers decision-makers to enhance performance and meet production goals with greater precision and efficiency.
Reducing Yield Loss Strategically via Modern Technology
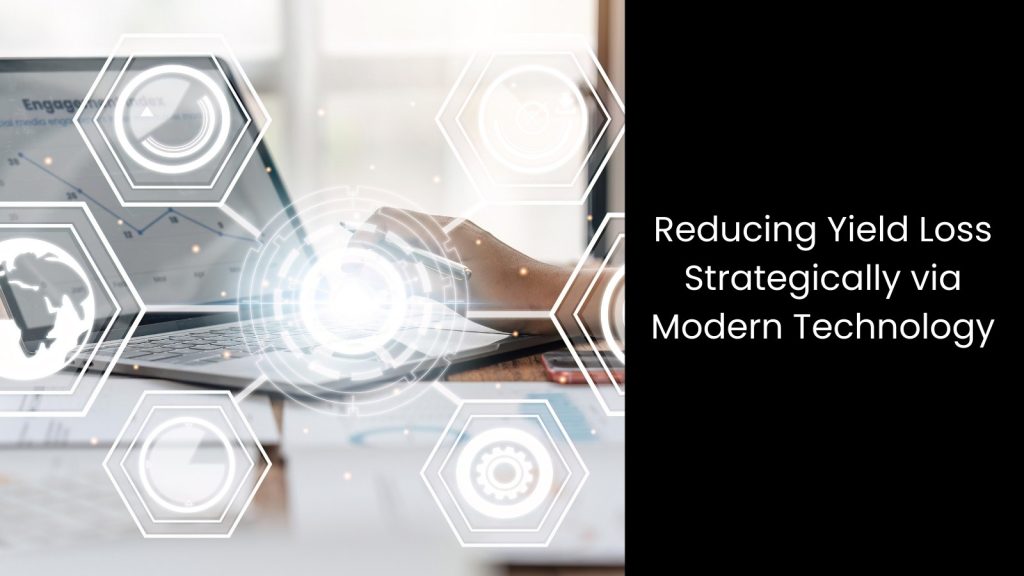
The road to minimising yield loss is more straightforward than ever with the power of cutting-edge technology! Manufacturers who opt for data-driven insights and automation have a great chance to gain a significant edge in reducing waste and improving consistency. The future of manufacturing is here, and it is time to embrace it for better outcomes.