This article talks about the role of collaborative robotics in the chip fabrication landscape.
What is Collaborative Robotics?

- When the industrial world pushes for more efficiency, collaborative robotics steps in as the latest trend. These advanced robots, known as cobots, work safely alongside humans without bulky safety barriers.
- Let us explain where its uniqueness lies. Unlike traditional robots that operate in isolated spaces, cobots use sensors, force control, and AI-driven programming to respond to human presence in real-time. Industries need this technology because automation alone cannot handle complex, fast-changing tasks that demand human adaptability. Cobots bridge this gap by handling repetitive jobs while allowing workers to focus on precision tasks.
- Their mechanism relies on lightweight builds, flexible joints, and responsive software that adapts to various production needs. Built-in vision systems and machine learning algorithms enable them to recognise objects, adjust movements, and refine accuracy. Manufacturers programme them through intuitive interfaces, making reconfiguration quick.
- Unlike rigid industrial robots, cobots fit into dynamic workspaces, assisting in assembly, inspection, and logistics without slowing operations. This blend of automation and human collaboration defines the future of industrial robotics.
Key Ways Collaborative Robotics Can Be Utilised in Chip Fabrication
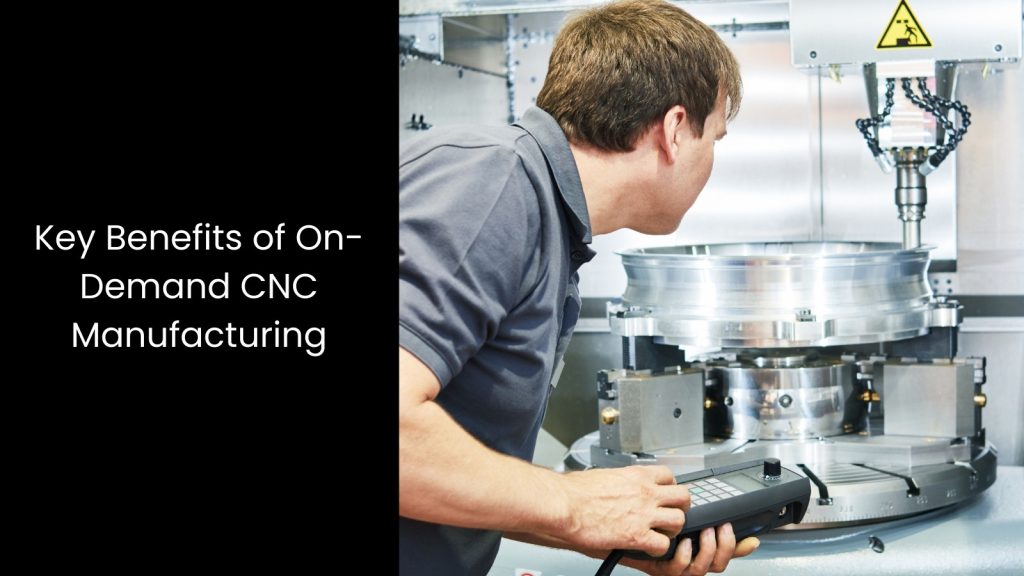
Wafer Handling & Transport
You know that those human operators can leave behind microscopic particles or apply uneven pressure. But when it comes to cobots, they use soft-touch grippers, vacuum suction, and AI-driven motion control to handle wafers with extreme care. Their high-resolution vision systems and force sensors keep alignment perfect, and this prevents misplacement that could ruin an entire batch.
With programmed pathways and real-time monitoring, cobots navigate through cleanroom environments without unnecessary exposure to airborne particles. They automatically adjust grip strength based on wafer thickness and ensure a firm but gentle hold to prevent cracks or scratches.
If a slight misalignment occurs, their adaptive control systems instantly correct positioning before moving to the next process. Unlike traditional automation, which follows rigid sequences, cobots adapt to different wafer sizes and layouts without disrupting production.
Their precision-driven transport systems keep chip manufacturing efficient.
Photolithography Assistance
It is a key step in defining intricate circuit patterns. Collaborative robotics steps in to make this process more precise by handling the delicate task of loading and unloading wafers into photolithography machines without errors. These cobots use high-precision robotic arms, vision-guided alignment systems, and pressure-controlled grippers to place each wafer exactly where it needs to be. Even the slightest misalignment can ruin an entire batch, so cobots constantly adjust in real-time to ensure accuracy.
Their AI-driven motion tracking detects even the smallest positional shifts. This helps correct them instantly before exposure begins. With their ability to work nonstop, they eliminate inconsistencies that come with human handling, reducing defects and improving efficiency.
Equipped with cleanroom-compatible designs, they move wafers without introducing contaminants and keep the process smooth. Also, cobots quickly adapt to changing production needs.
Their seamless coordination with photolithography systems ensures every wafer aligns perfectly under the exposure light.
Chemical Processing
Etching and cleaning processes use dangerous chemicals like hydrofluoric acid and sulphuric peroxide, which can cause serious harm if mishandled. Cobots take over these dangerous tasks, using sealed robotic arms, corrosion-resistant materials, and precision-controlled dispensing systems to handle chemicals safely.
Their AI-powered sensors and automated flow controls ensure the right amount of chemical reaches each wafer. This is what prevents overexposure or contamination. There is a possibility that human operators may risk accidental spills or inconsistent application. However, cobots maintain steady, repeatable movements, reducing defects. Their real-time monitoring systems detect irregularities in chemical flow and adjust immediately to keep processing stable.
With automated chemical handling, cobots also minimise waste and ensure manufacturers use only the necessary amount of each substance.
Designed for cleanroom environments, these robots work without introducing airborne particles, keeping the fabrication process clean and efficient.
Deposition Process Automation
These cobots handle wafers with soft-touch grippers and vacuum-based lifting systems. This prevents scratches or contamination before the deposition starts. Using high-precision motion sensors and AI-driven alignment controls, they place each wafer at the exact coordinates required for uniform film coating.
Manual handling can introduce misalignment or uneven coatings. However, cobots maintain consistency by adjusting their grip and placement based on wafer thickness and deposition chamber requirements. Their real-time feedback systems detect any shift in positioning and instantly correct errors, ensuring smooth and even film layers.
Moreover, these robots prevent dust particles from interfering with the semiconductor fabrication process. With adaptive programming, they handle different wafer sizes and deposition techniques without requiring extensive reconfiguration.
Metrology & Inspection
You know that semiconductor manufacturing requires precise measurements at microscopic levels, and even the tiniest defect can impact chip performance. These robotic inspection systems ensure each wafer gets scanned under the same conditions every time. Cobots use AI-powered alignment systems, vision-guided positioning, and ultra-precise robotic arms to move wafers under optical, electron-beam, and X-ray metrology equipment without causing misalignment or vibrations.
Their real-time adjustment features detect irregularities in positioning and instantly recalibrate for sharper accuracy. With non-contact handling mechanisms, they prevent contamination that could affect measurement accuracy.
Plus, these robots also integrate seamlessly with automated defect classification systems, allowing fabs to detect, analyse, and sort defective wafers faster than traditional inspection methods.
The best part is that instead of relying on slow manual processes, fabs now use automation with collaborative robotics to keep quality control fast, efficient, and highly reliable.
Cerexio Digital Solution for Optimised Chip Fabrication
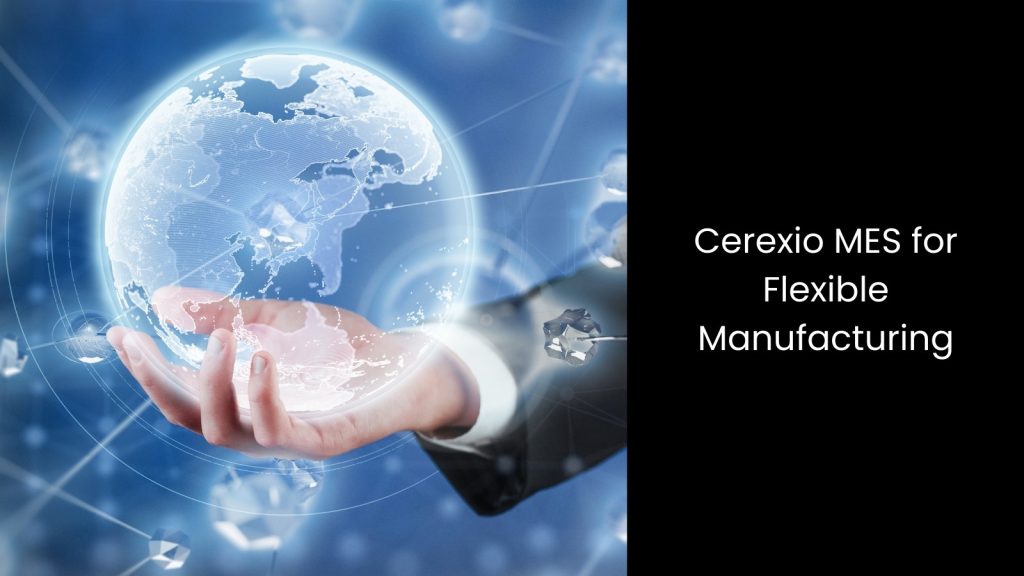
Maximise chip fabrication efficiency with Cerexio MES Digital Solution that seamlessly integrates collaborative robotics for precise wafer handling, inspection, and automation. Our Cerexio product helps you reduce errors, enhance real-time monitoring, and accelerate production with intelligent cobot coordination. Boost yield, quality, and throughput with smart MES-driven automation powered by Cerexio! We are making way for the future of semiconductor manufacturing!
Using Modern Tools to Enhance the Precision of Chip Fabrication
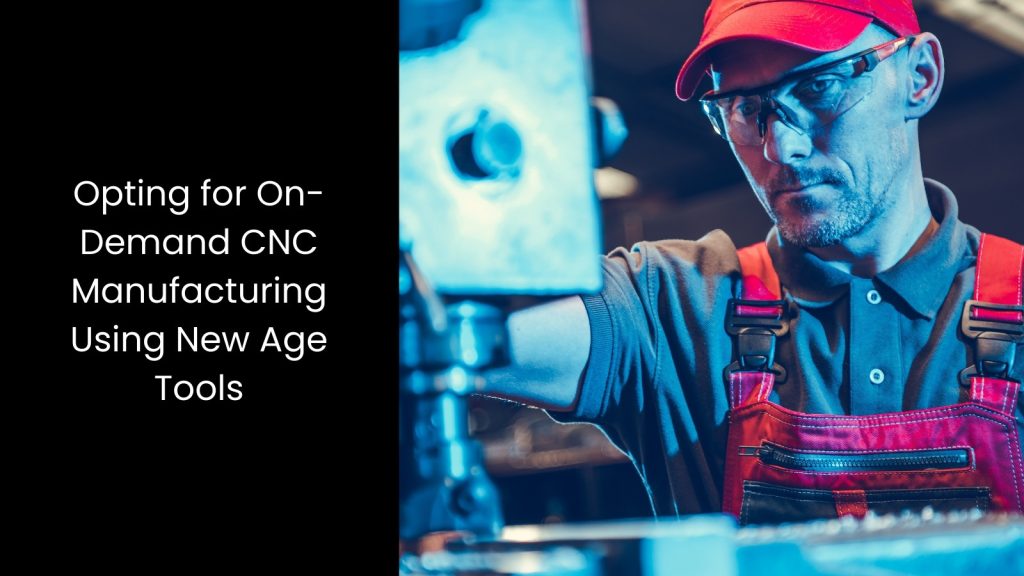
Don’t you think it is time to enhance chip fabrication with next-gen precision tools? You can achieve this by simply integrating collaborative robotics, metrology systems, and AI-driven automation to achieve flawless wafer production. If you seek precision, these modern tools will clear the path for you!