Did you know that service request management is a crucial aspect of running a successful manufacturing operation? This actually means handling requests from employees for various services, like equipment maintenance or repairs, in a smooth and efficient manner. If the service requests are not handled well, the manufacturing companies will have to encounter various challenges such as downtime, delays in processes, order fulfilment delays, obstacles in customer retention, etc. This is why a manufacturing company in today’s customer satisfaction-driven landscape has to take care of service requests promptly.
In this article, we will explore the concept of ‘Service Request Management’ and look into the best practices of service request management for the manufacturing realm.
We will know
What is Service Request Management in Manufacturing?
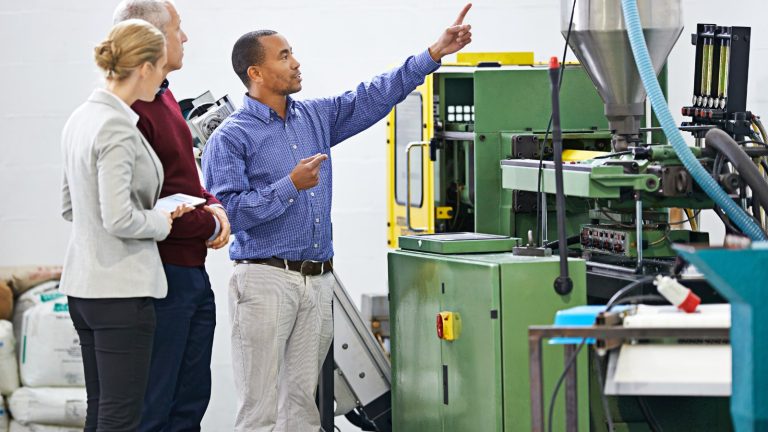
- This concept receives the spotlight when it comes to the manufacturing industry, and the latter refers to the structured process by which manufacturing companies handle and fulfil internal service requests efficiently.
- It actually includes the entire lifecycle of a service request, from submission to resolution, ensuring timely and effective responses to various needs within the organisation. Do you know why this mechanism is crucial for manufacturing companies? They require it in order to streamline operations, enhance productivity, and maintain high standards of customer satisfaction, which are the main objectives.
- In a traditional framework, the process involves multiple parties, such as employees, supervisors, support staff, etc. Certain requests keep flowing through various departments based on their nature and requirements. Requests in the sense of maintenance, repairs, procurement, or any other service necessary for smooth operations can be involved.
- If manufacturing companies opt for a well-defined, systematic approach to handling service requests, they must be documented, prioritised, assigned, and tracked to ensure prompt resolution while optimising resource utilisation.
Why is Service Request Management Important?
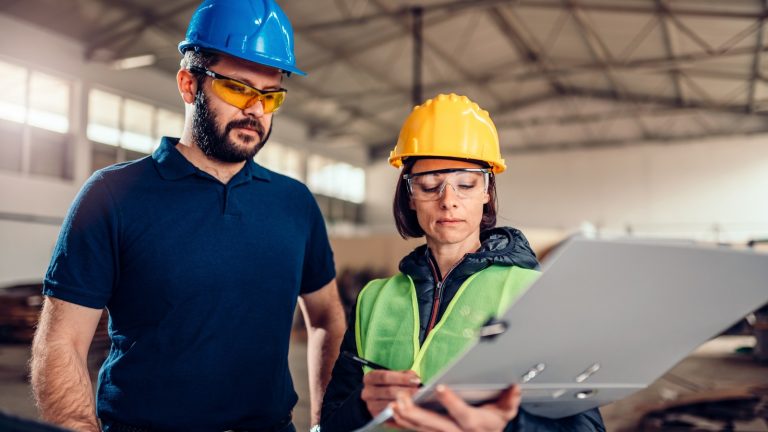
- If you wonder why a manufacturing company needs an effective service request management ecosystem, then you should know that it ultimately contributes to improved operational efficiency. Not to mention that it helps reduce downtime and enhance better resource allocation within manufacturing enterprises.
- Let us elaborate on this a bit for you. If service requests are not handled effectively in manufacturing companies, they face a massive amount of challenges. First and foremost, unaddressed or delayed service requests can lead to increased downtime, impacting production schedules, and ultimately affect revenue.
- Another fact is that such unresolved issues might escalate, causing equipment failures or quality issues, which can damage reputation and customer satisfaction.
- Imagine a manufacturing company functions with poorly managed service requests; then they will have to face situations where they run out of resources as employees spend more time dealing with preventable issues rather than focusing on core tasks.
- Without proper tracking and prioritisation, critical requests can get lost or neglected, and this will exacerbate operational inefficiencies. As you can see, it will be a chaotic situation without proper service request management.
Key Service Request Management Best Practices for Manufacturing
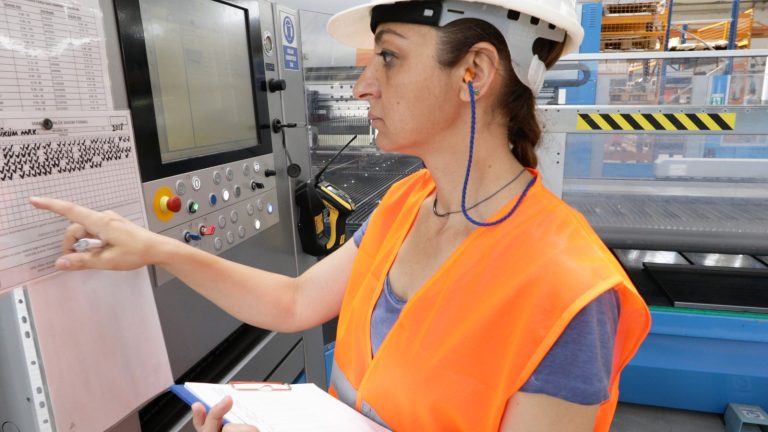
Making Request Submission Easy
This is considered a best practice in service request management for manufacturing companies due to several compelling reasons.
Simplifying the submission process streamlines communication between employees and support staff, ensuring that issues are reported promptly and accurately. This ease of submission encourages employees to report problems or request services without hesitation. It prevents potential issues from escalating.
In one way, a user-friendly submission system reduces the likelihood of errors or incomplete information, which will facilitate faster and more effective resolution. In another way, by providing multiple channels for request submission, such as online portals or mobile apps, companies can accommodate diverse employee preferences and work environments. This will further enhance accessibility and convenience for all the parties involved.
Furthermore, easy request submission supports proactive maintenance and preventive measures, as employees are more likely to report minor issues before they develop into major problems.
It will not cost anything to make the request submission easy, yet it helps you build a culture of collaboration, transparency, and responsiveness within manufacturing companies. This will undoubtedly lead to improved operational efficiency, reduced downtime, and enhanced employee satisfaction.
Automating Service Request Alerts
Why would you manually interfere with service request handling when you can automate its flow? Yes, this is another best practice, considering the efficiency and effectiveness it offers. If the authorities can automate the alert system, they can instantly notify relevant personnel or departments about new service requests, ensuring timely attention and response.
Why is this so needed in the manufacturing realm? That is because automation reduces the reliance on manual notification methods while minimising the risk of delays or oversights. Plus, automated alerts can be customised based on factors such as priority level or type of request. The ultimate result would be the swift allocation of resources and the appropriate escalation of urgent issues.
On the other hand, automation enhances visibility and accountability by providing real-time tracking and monitoring of service requests. With this capacity in hand, managers are empowered to identify bottlenecks or trends and optimise workflow processes accordingly.
Automating notifications is the best way to keep all the departments on alert!
Giving Priority to Service Requests
Prioritisation of service requests is a best practice in service request management for manufacturing companies since it has the ability to optimise resource allocation and minimise disruptions to production processes.
How this mechanism occurs is interesting to explore. As you can see, by assigning priority levels to service requests based on factors such as criticality, impact on production, and customer requirements, manufacturing companies can ensure that urgent issues are addressed promptly. On the other hand, they have to keep focusing on non-critical requests efficiently as well.
This prioritisation allows for better utilisation of the workforce and equipment. It maximises productivity and minimises downtime. In addition, as it has clearly defined priority levels and pre-established escalation procedures, companies can establish accountability and ensure that resources are allocated effectively to meet service-level agreements and customer expectations.
Implementing Service Request Management Software
Although there are several good practices in the scenario, nothing can match the efficiency levels offered by suitable service request management software. Do you agree? Yes, this is why this is known as a top-level strategy in manufacturing. The latter offers a centralised platform to streamline and optimise the entire service request process.
This software automates request submission, tracking, and resolution, enhancing efficiency and accountability. It provides real-time visibility into the status of requests, allowing for better resource allocation and prioritisation.
Also, service request management software provides a grid to facilitate communication and collaboration among departments and stakeholders. This effort will reduce response times and improve customer satisfaction in the end. Likewise, it paves the way for data-driven decision-making by generating insightful analytics and reports, helping identify trends, bottlenecks, and opportunities for improvement.
If the manufacturing companies could implement such a robust technology to handle service requests, there would be zero errors and delays in fulfilling requests.
Cerexio Pioneered Service Request Management System
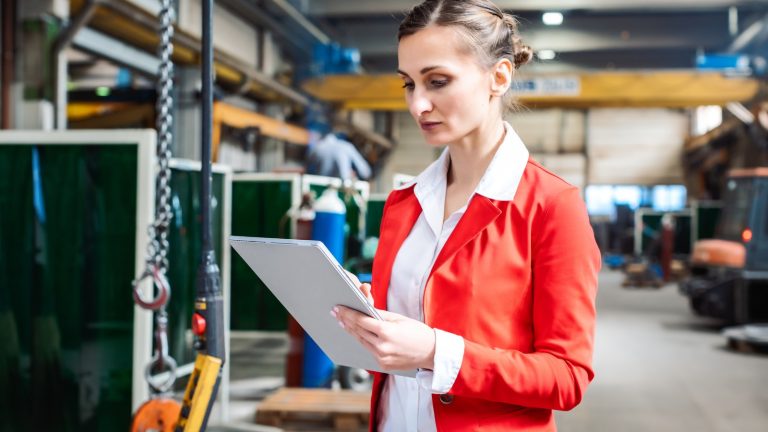
Cerexio is introducing our manufacturing Service Management System which is dominated by Industry 4.0 technologies, to offer you the best experience in handling all the service requests. Our unified digital solution integrates predictive analytics, AI, and IoT to streamline machinery operations. With error-free workflow automation and advanced capabilities, the Cerexio solution ensures optimal performance in manufacturing plants.
Implementing Best Practices for Better Service Request Management
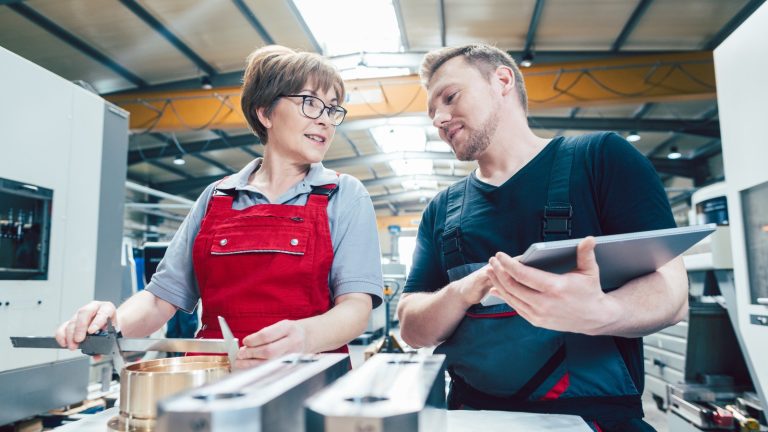
Nobody believes handling service requests is an easy task. However, if you need to enhance customer satisfaction, you have to find a new way to facilitate better service request management within your manufacturing plant. Implementing best practices and strategies will help you achieve the best results without compromising the quality of your work as well.