This article explores the top five technologies that scale up stainless steel cone manufacturing companies and their operational framework.
We will understand
- Why Do Stainless Steel Cone Manufacturing Companies Need Modern Technology?
- Top 5 Technologies Stainless Steel Cone Manufacturing Companies Can Employ
- Cerexio Powered Industry 4.0 Integrations for Stainless Steel Cone Manufacturing Companies
- Optimising Operations of Stainless Steel Cone Manufacturing via Digitalisation
Why Do Stainless Steel Cone Manufacturing Companies Need Modern Technology?
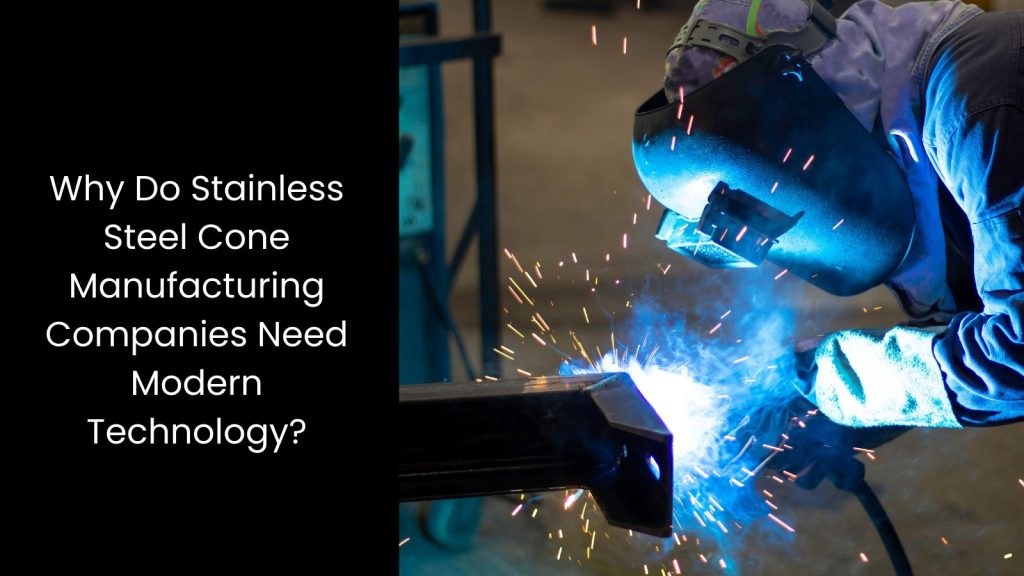
- It is visible that today’s stainless steel cone manufacturing companies tend to rely on modern technology to meet the growing demands for precision, efficiency, and durability across industries like chemical manufacturing, construction, and engineering.
- The main reason is that integrating advanced machinery and techniques enhances the production process for materials like stainless steel, alloy steel, and carbon steel, ensuring high-quality outputs. With tools like CNC machining, manufacturers achieve unmatched precision in shaping steel plates into durable cones, which is crucial for industrial applications.
- On the other hand, advanced welding techniques ensure seamless joins in materials such as cold-rolled steel, abrasion-resistant steel, mild steel, and even titanium alloys, delivering products that withstand extreme conditions. Also, modern industrial furnaces play a critical role in heat treatment, improving the strength and flexibility of steel alloys and other metals like aluminium.
- These technologies allow manufacturers to create cones that meet strict specifications for applications in chemical manufacturing and steel mills, where high resistance to heat and abrasion is a must. The ability to process high-strength steel and other specialised materials boosts performance while reducing material waste and saving time and costs.
Top 5 Technologies Stainless Steel Cone Manufacturing Companies Can Employ
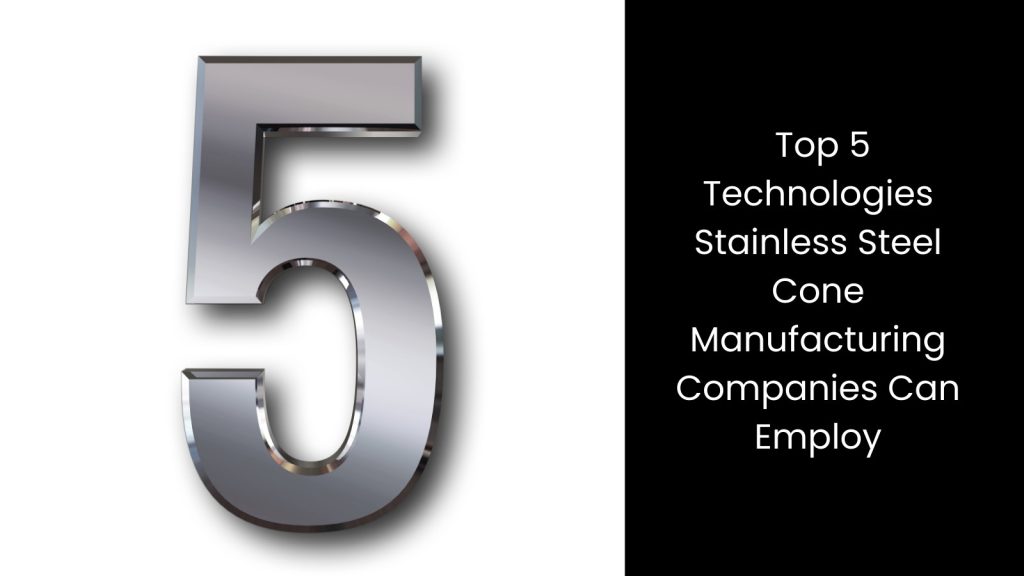
Non-Destructive Testing (NDT) Methods for Optimised Stainless Steel Cone Manufacturing
However, by using non-destructive testing or NDT methods, these companies can evaluate the integrity of metals, including specialised materials like titanium, nickel-chromium, and resistant alloys, without compromising their structure. NDT techniques like ultrasonic testing and radiographic inspection enable manufacturers to detect flaws in welded assemblies or seamless cones while maintaining their durability. This is especially critical for applications in the sand gravel industries, where light wall cones and material handling cylinders must endure harsh conditions.
Advanced methods like dye penetrant inspection and magnetic particle testing effectively identify surface defects on ducts and components with phosphate coating services, ensuring optimal performance. Flat laser cutting processes further benefit from NDT by confirming precision and quality.
Companies all around the world employ vacuum-based technologies such as vacuum metallising to enhance surfaces without affecting structural integrity, making NDT indispensable in quality assurance.
Robotic Material Handling for Stainless Steel Cone Manufacturing Companies
These advanced technologies streamline the production of common product types, such as conical segments, by automating repetitive tasks, reducing errors, and ensuring consistent precision. Robotic systems enable manufacturers to handle heavy or delicate materials accurately, minimising damage and waste.
For example, companies can use robotic arms to transport raw materials and finished conical segments across production lines, significantly improving workflow speed. These systems also enhance workplace safety by reducing the need for manual handling of heavy stainless steel components and then protecting workers from potential injuries.
Further, robots equipped with sensors and programming capabilities adapt quickly to different product requirements, ensuring seamless integration with existing processes. This flexibility is particularly beneficial for producing diverse cone types, where customisation is often required.
Computer-Aided Design (CAD) Software
This is one of the main reasons that steel cone companies use CAD software. This way, they can optimise precision, efficiency, and innovation in their production processes. This advanced technology enables engineers to create detailed blueprints for components like cones and supports mould designing, ensuring perfect dimensions and seamless compatibility with industrial requirements.
When integrating CAD, stainless steel cone manufacturing companies can visualise and simulate the performance of materials such as nickel chromium molybdenum, known for its exceptional strength and heat resistance, before actual production begins. CAD software also enhances the design of cones used in high-temperature applications, allowing engineers to account for the performance of the furnace environment and ensure the product’s durability.
The ability to adjust designs in real time minimises costly errors and accelerates production timelines. With CAD, manufacturers can efficiently manage custom designs, meeting client-specific needs while maintaining the structural integrity of stainless steel components.
Laser Cutting Technology
By integrating laser cutting, manufacturers can produce high-quality products, such as cones and other custom components, faster and with minimal waste. The technology allows companies to handle a wide range of materials, including stainless steel, alloy steel, and other metals, ensuring versatility and adaptability to diverse industrial requirements.
Moreover, laser cutting eliminates the need for extensive tooling, reducing setup times and enabling seamless adjustments for design modifications during production. Additionally, the precision of laser technology ensures smooth edges and superior finishes, which minimises post-processing work and enhances overall efficiency.
With the ability to cut intricate patterns and handle both small and large-scale projects, laser cutting empowers manufacturers to meet client demands quickly and cost-effectively. If they adopt this technology, stainless steel cone manufacturing companies will improve product quality, optimise resource utilisation, and maintain a competitive edge in an industry that prioritises innovation and reliability.
Industry 4.0 Integration
Another thing is that intelligent systems can regulate the performance of critical equipment like industrial furnaces, maintaining precise temperature control for heat treatments that improve the durability of cones and components. Likewise, advanced data-driven insights help manufacturers streamline processes, minimise waste, and reduce downtime when handling steel plates and other raw materials.
It is also proven that Industry 4.0 allows manufacturers to predict maintenance needs and avoid unexpected equipment failures, enhancing productivity. Opting for them will help stainless steel cone manufacturing companies stay competitive, produce high-quality products, and meet the evolving demands of global industries.
Cerexio Powered Industry 4.0 Integrations for Stainless Steel Cone Manufacturing Companies
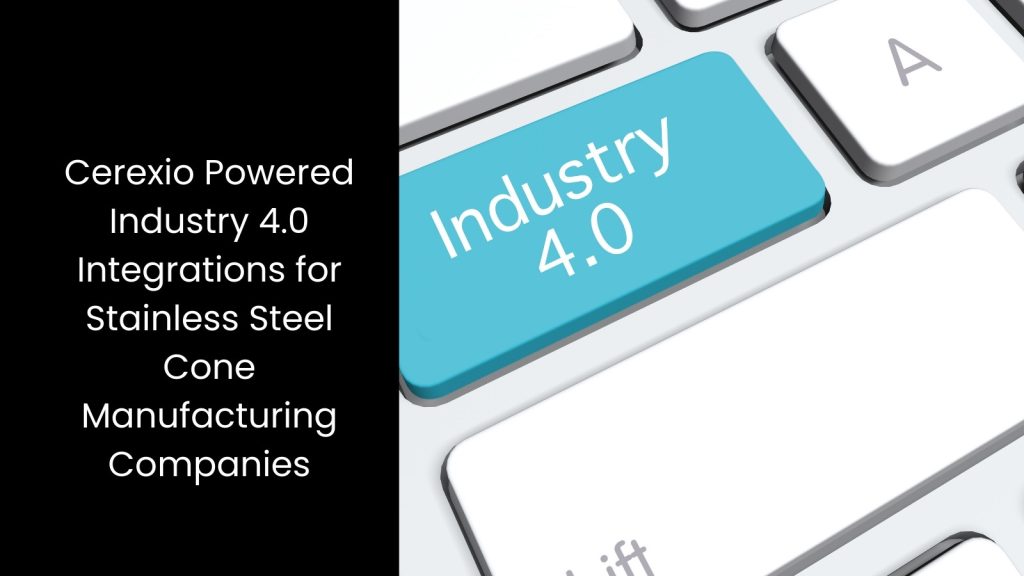
Cerexio empowers modern stainless steel cone manufacturing companies with Industry 4.0 integrations through our advanced solutions like the Manufacturing Execution System and Manufacturing Control Tower. Through AI, IoT, Digital Twin, etc., these robust tools optimise production, enable real-time monitoring, and enhance operational efficiency, ensuring precise control over processes and delivering unmatched quality for modern manufacturing needs.
Optimising Operations of Stainless Steel Cone Manufacturing via Digitalisation
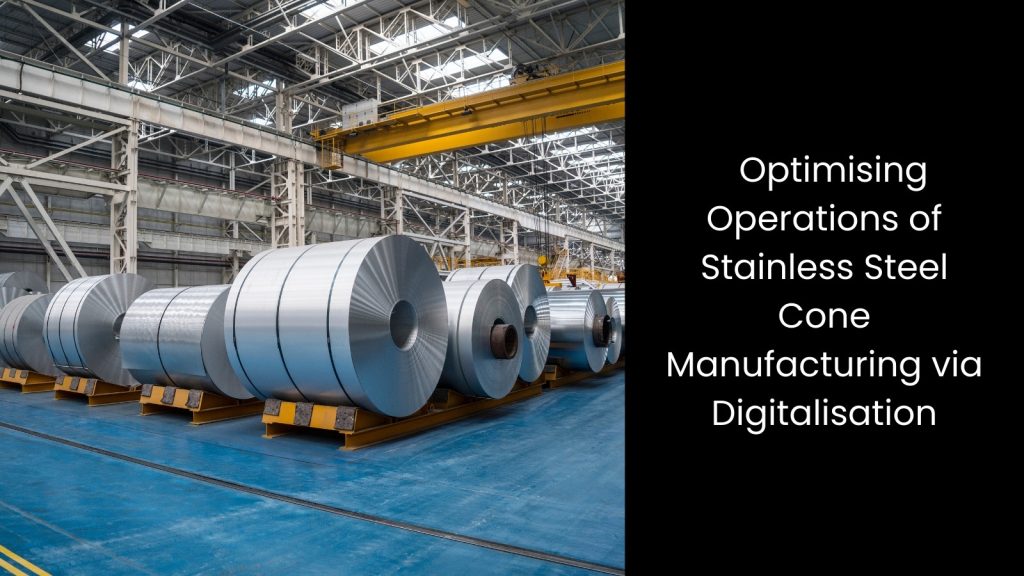
It is quite evident that the integration of digitalisation into stainless steel cone manufacturing holds the promise of transformative change. Embracing advanced technologies will help companies optimise their processes, reduce operational costs, and boost profitability. The power of cutting-edge innovation is undeniable, positioning businesses to thrive in an increasingly competitive marketplace.