Industrial robots are typically used in factories to carry out various manufacturing tasks. According to the International Standards Organisation, a robot, in this context, is an “automatically controlled, reprogrammable, multipurpose manipulator, programable in three or more axes, which can be either fixed in place or mobile for use in industrial automation applications”. In the World Robotics 2022 report published by the International Federation of Robotics, robot density was identified as one of the key indicators used worldwide to measure a country’s rate of automation in the manufacturing industry. The report records that, as of December 2021, Singapore is the fifth most automated country in manufacturing. The 2022 report further notes that Singapore has 670 robots installed per 10,000 employees, making it the second-highest robot density country globally, with an average growth of 24 per cent annually since 2016. This demonstrates that any factory manager needs to automate their factories with the integration of robots to stay within the competition of the manufacturing industry.
This article will act as a guide for any factory manager that is wondering what needs to be done to deploy robotic machinery on their factory floor.
But First - Why Are Robots Required in a manufacturing facility?
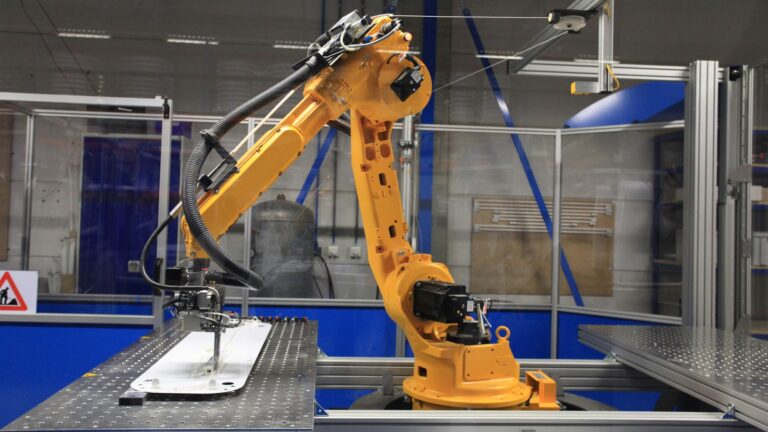
A high level of attention is required when working in industrial factories as it consists of repeated processors. Hence, if a human workforce were in charge, the probability of an error occurring would be much higher. Unlike machines, humans require rest and only work for a limited number of hours. The absence of one worker could drastically affect the progress of work, leading to increased downtime. Additionally, since factories include multiple assets, which, if not maintained properly, could lead to a hazardous work environment, employees in the factory could be at risk of facing a workplace accident. Such concerns have been a few significant reasons why industrial robots are incorporated into factory operations. Incorporating robots has reportedly led to a significant decrease in operational costs, decreased downtimes, maximum labour productivity, reduced waste, improved product quality and more.
Tips to Keep in Mind When Deploying Robotic Machinery
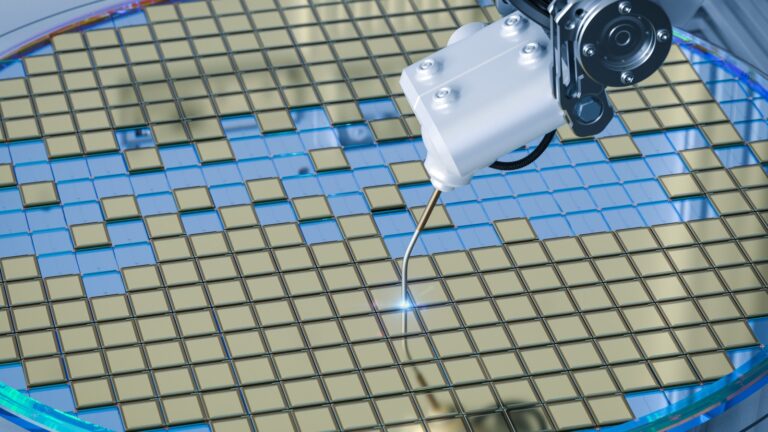
It is always best to form a plan before investing in robotics for your factory. Suppose an organisation intends to ensure they get their money’s worth and achieve their desired outcomes. In that case, they should take a reasonable time period to understand what they expect to gain from incorporating robots into their operations, as the implemented process greatly depends on it. Here are five tips to keep in mind when deploying robotic machinery for the first time.
Identify What Tasks You Want to Automate
Although ideally, a company should invest in a full-automation strategy, it may not be most feasible for SMEs. Hence, to slow the automation process, consider what tasks can be replaced with industrial robots. This can be done by identifying which tasks are the most time-consuming or have caused employees to be injured. A factory manager should, in other words, first comprehensively understand their own existing processors and the desired future state and select which functions should be automated. Generally, most factories contact a Robotic System Integrator, which handles the planning, designing and deployment of a robotic system. Alternatively, a company that is finding it difficult to make such an assessment can reach out to a team of experts and let them carry it out instead.
Is It Possible For the Robort to Do the Function Better?
Keep in mind robots are not the best option for all functions. They are usually most suitable when you want them to carry out repetitive functions which require a high degree of precision and accuracy or are dangerous. Hence, do not simply introduce robots on the blind belief that it is a leading key technological tool implemented when automating a manufacturing factory. Attempting to introduce a robot to carry out a function that is complicated will not optimise your factory operations. Additionally, the factory floor must be suitable for robots to make their way to the desired destination. Hence, while automated factories are known for requiring only a little space, make sure that the space has made it easy for robots to navigate within the production floor.
Find A Suitable Vendor For the Installation
Finding a suitable vendor is central to successfully deploying different types of industrial robots. This is because the solution the company implements will effectively decide whether it is compatible with other solutions embedded in your system. Make sure to do ample research on the standards the vendor meets, its speciality and whether it holds certifications in data security, for instance. Also, consider how many years of experience they have in the field in addition to their number of testimonials. Go through reviews they have gotten and take note to clarify whether they offer prompt after-installation support. Remember that a company enters a long-standing partnership when they choose its vendor. Hence, it is important to ensure they are as interested in helping the company reach success in the future.
Follow Up After Installation
An important step most companies fail to adhere to is following up after the installation. Similar to any other asset, remember that robots also require routine maintenance. Hence, having an effective system in place would help ensure that unexpected downtime and increased costs will not occur. It would be helpful in this respect to invest in a full manufacturing execution system (MES) that not only looks into robotic automation. A powerful MES solution powered by data analytical, AI and ML capabilities can help track anomalies in their initial stages and ensure the factory functions well 24/7. In this respect, it is therefore also important that the vendor that is chosen consistently send updates so as to guarantee they meet future demands in the market.
Cerexio MES: A One-Size-Fit-For-All Automation System
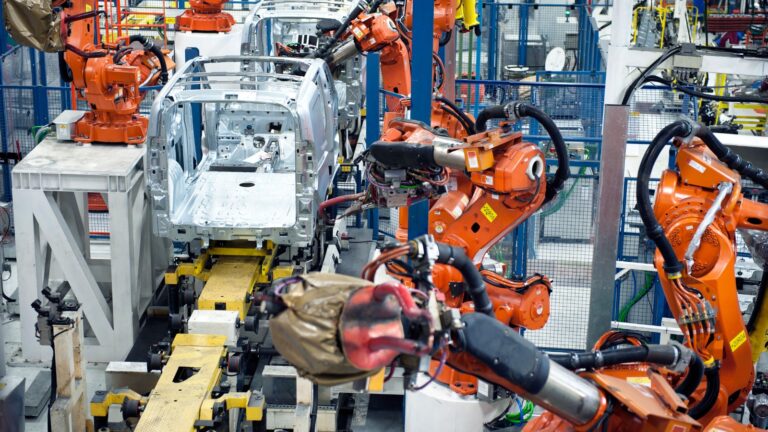
Cerexio MES is a leading solution made by one of the few technology vendors specialising in enabling globally recognised solutions for modern manufacturing. It is currently one of the leading software solutions powered by industry 4.0 and is ranked at the top in Asia and the world. With the integration of AI, ML, data analytics, digital twins, simulation technology and others, this is an all-in-one solution that helps you to automate all factory processors. It offers an infrastructure that can easily connect with multiple machines, including industrial robots such as RGVs, IGVs, AGVs, AMRs and other in-house equipment. It moreover tracks and traces all assets connected to your ERP, WMS, supply chain and other systems. Detect the root cause of asset anomalies in one go and schedule repairs or maintenance based on criticality, thereby smartly strategising your finances. Moreover, detect the level of carbon emissions, maximise labour utilisation and improve yield, throughput, and quality to meet standards of manufacturing excellence.
Connect with us to schedule a consultation with our team of experts to get help infusing a solution that can seamlessly deploy robotic machinery.
It Is All About the Thought Process
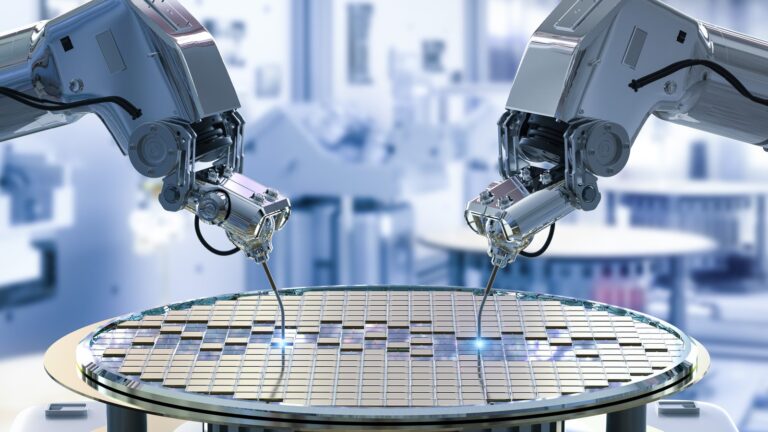
Thinking that everything will be resolved by deploying robots is the wrong attitude. Making an informed decision, however, helps you see rewards in your investment and monitor your company’s progress. This means not only should factory managers make a proper implementation plan on their own, but take the advice of a professional consultation body, refer to industry experts, do ample research and then figure out the best course of action. Remember that it does not stop from the installation stage. You need to consistently monitor, test and fix any problems before they become out of your control.
This article is prepared by Cerexio, a leading technology vendor that offers specialised solutions in the Advanced Manufacturing Technology Sector. The company is headquartered in Singapore and has offices even in Australia. Cerexio consists of a team of experts that have years of experience and hold detailed knowledge on a range of subject matters centric to the latest technologies offered in manufacturing and warehouse operations, as well as in predictive maintenance, digital twin, PLC & instrumentation setup, enterprise integrator, data analytics and total investment system.