Manufacturing Execution Systems (MES) are popularly known to be the perfect solution to digitalise a factory. In other words, it is the starting step to transitioning to a smart manufacturing factory, allowing companies to face fewer errors, anomalies, waste and costs. However, the advantages of an MES may not be visible the moment it is installed into a system. Careful consideration should be made to ensure the MES is adequately implemented. Failure to do so will not only mean that a manager will not receive their money’s worth, but the company will also not experience the actual benefits such a solution promises. This article will guide managers on how they should implement their MES solution.
Order of Steps When Implementing an MES
No golden hierarchy has been officially recognised when implementing an MES solution. There are, however, important steps that you cannot miss. Here are a few of the most vital steps that you must follow.
Step One: Do You Really An MES?
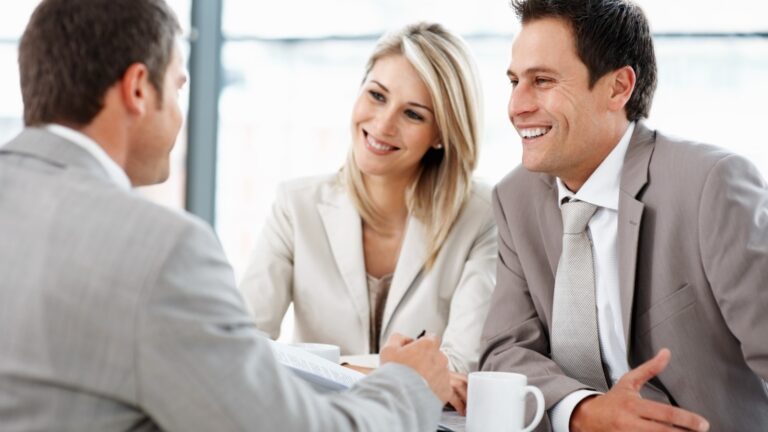
While a simple google search would advise manufacturers to adopt an MES solution, blindly doing so just because it is recommended or is a common trend in the business world is insufficient. A company needs to consider why they, in particular, want such a solution. They must list their expectations and what they hope to achieve through implementation. Finding the key reasons for implementation is sometimes referred to as forming the problem statement. This is regarded as an essential step since it is integral for a company to understand that there is no one MES solution for everyone. Hence, what may work for one manufacturer may not work for another. Thus, identifying your objective and critical requirements gives the organisation a clear idea of what features are essential for the MES. This highlights the need to plan and develop a detailed strategy. Without a valid reason, an MES implementation is likely to fail.
Step Two: Identify The Scope
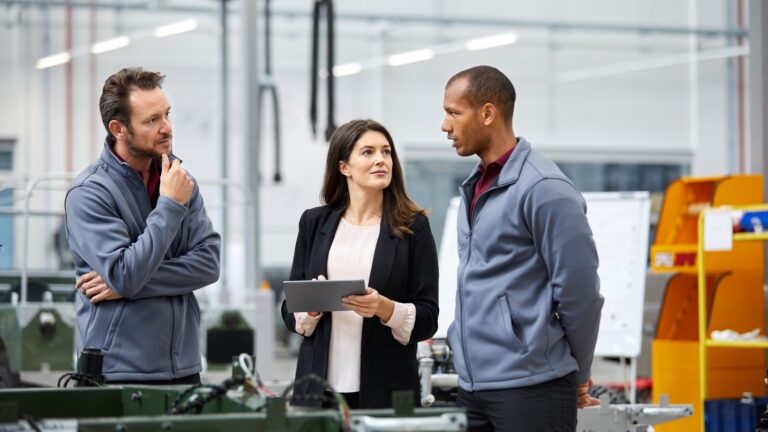
Objectives tend to be broad. Hence, as much as it is important to identify them, it is equally essential to identify the scope the company is willing to take. This will greatly depend on the financial viability of the organisation. For example, the more features required to carry out a number of changes the more money will need to be invested, thereby prolonging the implementation stage. This is also the stage where companies need to decide on the number of customisations that will be required. Note that the more customised an MES solution is, the more it deviates from a standard MES. This is because a customised MES may include features which are, for the first time, being engineered into the solution. Hence, time is required to guarantee the solution is a success. Talking to the relevant personnel in the organisation is vital when identifying the project’s scope. Hence, talk to the IT consultants and the executives in the company.
Step Three: Selecting An MES Vendor
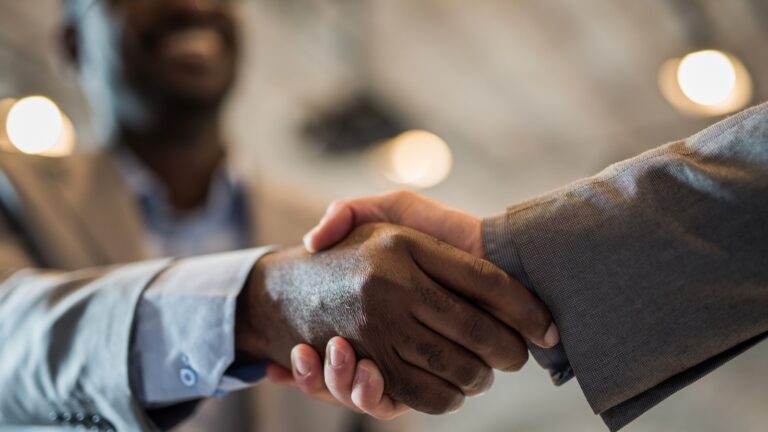
What often makes and breaks MES implementation is the software itself. Ensuring it has the advanced features that have been tried and tested before guarantees successful implementation. In other words, questioning whether the vendor can customise its solution to fit your needs without much complication is a good indication that they are the most suitable. Hence, a significant responsibility of the company is to make an intelligent decision on who the vendor will be. Doing ample research and seeking advice from other professionals is the best way to find the most suitable vendor. Consider how successful and recognised its MES solution is. A vendor may stand out due to its unique features. However, assessing the potential relationship you will form with them is crucial. Keep in mind that the vendor will possibly be a life-long partner of your company who will work on system updates that align with your future goals. Thus, being confident that the vendor offers good after-support is essential.
Step Four: Implementing Phased Implementation
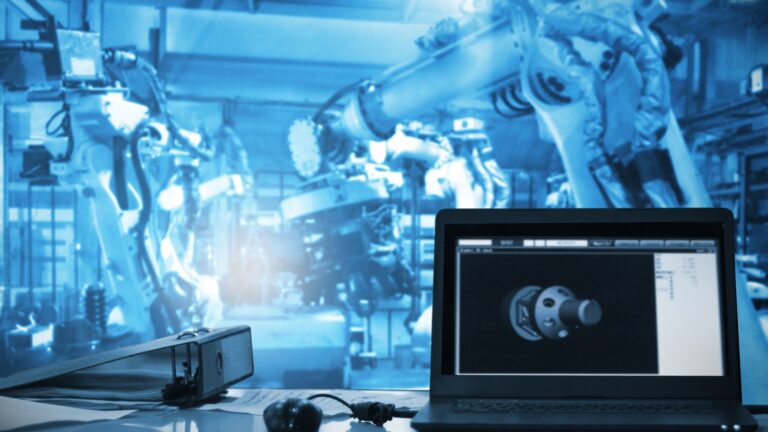
Implementing an MES solution can get very complicated. Companies will have to pay a large sum of money on the on-set, making it particularly expensive for SMEs. It also risks the factory from facing more risks than before. This is why, instead of completely implementing the MES solution in one go, break it down into phases. Deciding how to phrase it exactly would be up to the company and vendor. This is where the objectives that were initially identified come into play. Prioritising which challenges need to be prioritised and addressed at the very beginning. This also indicates that implementing an MES is not a fast solution. It takes time to install it and see results, requiring companies to be patient and act smartly in their approach to phase implementation. In this step, companies will also have to consider what systems need to be integrated. The key to implementation is to start early by introducing it to one part of a company instead of its entirety.
Step Five: Helping Your Employees To Adpt to the Cultural Change an MES Solution Brings
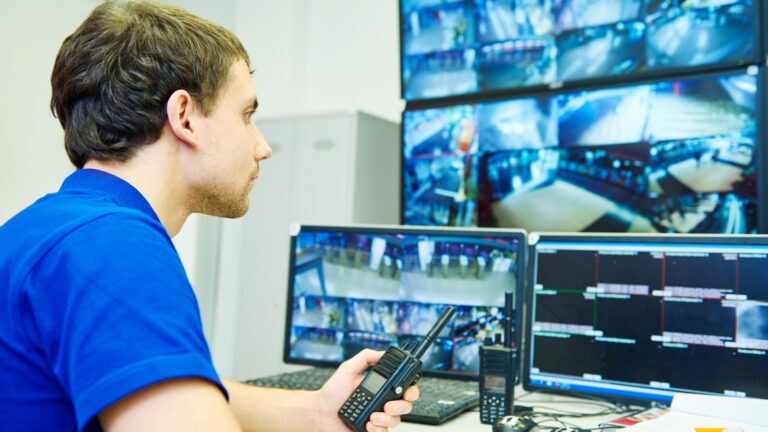
MES is not only a technical change but also a cultural change. This is because it changes the way employees are required to work while at the same time requiring production specialists and other key persons to play an active role during implementation. Some would also fear whether technology will lead to their jobs being replaced. Due to these reasons, it is essential to take the time to explain to an organisation’s entire staff the importance of implementing an MES for the company. Underlying the long-term benefits and ensuring they are understood is central. Removing any tension within the organisation, which would lead to unnecessary delays, a factor an MES was ideally meant to solve, would occur. In this respect, training the staff to use the MES solution is also essential. Most vendors offer training services, helping companies completely familiarise themselves with the software. This helps to ensure all the advanced features are part of the software for their benefit.
Cerexio: World Recognised MES Vendor and Expert
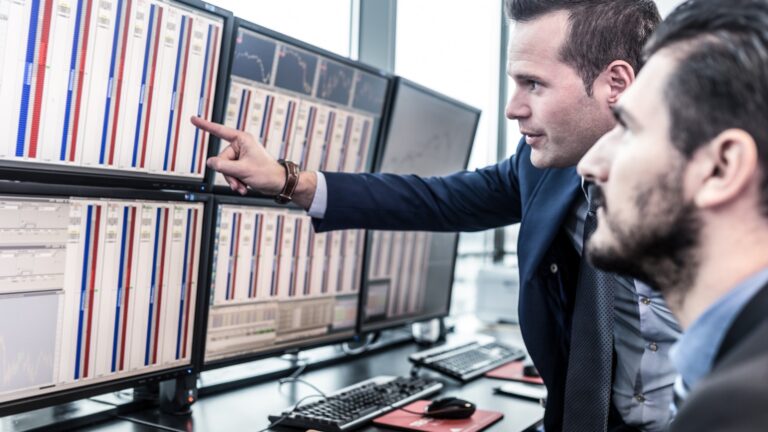
Cerexio MES is a compact solution that helps you gain end-to-end control of your manufacturing operations. It interconnects, advances and automates all processors within a single console and presents it via one smart visual screen. It is one of the few technology vendors that specialise in providing solutions for the manufacturing field, making its MES solution the best in South Asia and the world. One reason behind this is the advanced digital technologies the solution is packed with. It houses a range of industry 4.0 tools, including Artificial Intelligence (AI), Machine Learning (ML), digital twin, predictive and prescriptive analytics, Internet of Things (IoT) and more. It monitors your manufacturing assets 24/7, improves yield, throughput and quality, maximises labour utilisation and minimises carbon emissions and energy costs.
Cerexio also offers consultation services for companies struggling to understand how an MES solution can help them. In other words, Cerexio’s team of experts can identify critical objects and long-term goals your corporation can meet with its MES implementation. It also offers excellent after-service support and extensive training for your team to familiarise themselves and use their investment best.
Connect with us to schedule an appointment.
Unlock The Best Version of Your Factory with An MES
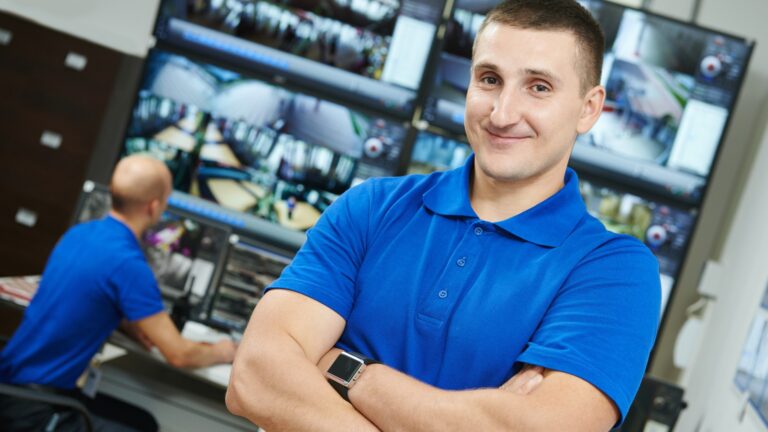
A smart MES solution properly implemented offers multiple benefits. It powers you up with advanced technologies that contribute to automating the entire factory operations, monitors the health of each asset, plays a proactive role in risk mitigation, standardises quality management, increases transparency in supply chains and becomes a leading manufacturer that implements sustainable practices. In essence, an MES is guaranteed to improve the operational performance of the production floor extensively once implemented properly.
This article is prepared by Cerexio, a leading technology vendor that offers specialised solutions in the Advanced Manufacturing Technology Sector. The company is headquartered in Singapore and has offices even in Australia. Cerexio consists of a team of experts that have years of experience and holds detailed knowledge on a range of subject matters centric to the latest technologies offered in manufacturing and warehouse operations, as well as in predictive maintenance, digital twin, PLC & instrumentation setup, enterprise integrator, data analytics and total investment system.