Did you know manufacturers lose anywhere from 5% to 20% of their total productivity due to downtime? Unfortunately, this can turn into significant financial setbacks. The more frequent and prolonged these interruptions are, the greater the impact on both productivity and profits. Beyond the financial costs, excessive downtime also affects employee morale, increasing stress levels and putting their safety at risk. In the worst-case scenario, it could even lead to legal troubles due to unsafe working conditions. The key to turning things around lies in addressing and reducing downtime as much as possible. But how can this be achieved?
In this article, we will explore the top strategies that can help manufacturers minimise downtime, optimise operations, and improve both worker well-being and financial performance.
We will discover
Best 6 Strategies to Reduce Downtime in Manufacturing
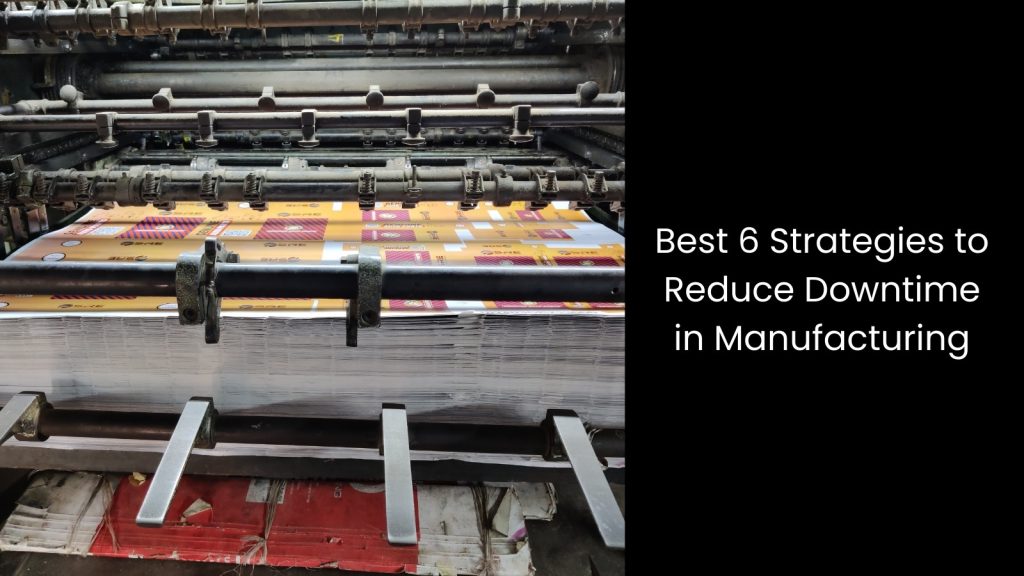
Cross-Functional Collaboration
Manufacturing downtime eats into productivity, but strong cross-functional collaboration keeps everything running smoothly. This is where the maintenance, production, and supply chain teams must talk to each other constantly as a small issue in one area can cause a chain reaction of delays.
It works this way: When maintenance teams get real-time updates from production, they can fix small faults before they turn into expensive breakdowns. Similarly, production crews need supply chain teams to keep materials flowing, so no machine sits idle waiting for parts. As you can see, a well-connected workforce stops bottlenecks before they start, ensuring machines, materials, and manpower stay in sync.
Regular stand-up meetings, shared dashboards, and open communication channels make sure no one works in a silo, reducing unexpected shutdowns. If a machine shows warning signs, instant alerts help maintenance step in before things go south. If raw materials get delayed, alternative sourcing kicks in without pausing production.
A team that shares insights and reacts quickly turns downtime from a disaster into a rare hiccup. So, yes, smooth communication builds efficiency, keeps machines humming, and ensures every shift maximises productivity.
Spare Parts and Inventory Management
No matter how efficient your production floor is, if you do not have enough spare parts when there is downtime, everything grinds to a halt.
In such a situation, machines break down, and without the right components on hand, repairs take longer than they should. This is how the manufacturing downtime drags on, killing productivity and throwing schedules into chaos.
However, if manufacturers keep essential spare parts in stock, it eliminates that headache, allowing maintenance teams to swap out faulty components fast and get production back on track.
It is obvious that long lead times for replacements create unnecessary delays, especially when suppliers struggle with shortages or shipping issues.
When a mechanism for smart inventory management is there, it ensures the right balance. This means enough stock to cover emergencies without overloading storage with unused parts. At the same time, tracking usage trends and predicting wear-and-tear patterns help teams reorder parts before they run out.
Predictive Maintenance
If a manufacturing plant is strengthened with the predictive powers of IoT sensors and AI-driven analytics, unplanned downtime becomes a rare problem instead of a constant headache.
Machines never fail out of nowhere, small warning signs surely appear long before a breakdown happens. Predictive maintenance taps into these early signals, using real-time data to detect abnormal vibrations, overheating, or wear before they turn into full-blown failures.
IoT sensors collect nonstop insights from equipment, while AI analyses patterns to flag potential issues before they disrupt production. Maintenance teams no longer waste time on unnecessary inspections or scramble to fix sudden breakdowns. Instead, they schedule repairs exactly when needed, swapping parts before failure strikes. This strategy eliminates costly surprises, maximises equipment lifespan, and keeps production lines moving without hiccups.
This way, manufacturing downtime drops because machines stay healthy, and teams stay ahead of problems instead of reacting too late.
Automated Process Monitoring
A real-time look into production keeps manufacturing downtime from creeping in when no one is actually keeping a closer look. Machines, assembly lines, and systems run nonstop, and without automated process monitoring, small inefficiencies can go unnoticed until they snowball into full-scale breakdowns.
But when there are real-time monitoring systems, they can easily track every movement, pressure level, and temperature shift, feeding live data into advanced analytics that spot even the slightest irregularities. The moment something drifts out of the normal range, alerts go off, giving teams a chance to fix problems before they escalate.
Manufacturers do not have to wait for a machine to fail or production to slow down. These quick interventions keep everything moving without disruptions. Data analytics also reveals patterns over time, helping manufacturers fine-tune workflows, eliminate bottlenecks, and optimise efficiency. Instead of reacting to downtime after it happens, factories that rely on automated monitoring predict and prevent it, ensuring machines stay in peak condition.
Every second of uninterrupted production means higher output, fewer repair costs, and a smooth-running operation that does not rely on guesswork to stay ahead.
Regular Preventive Maintenance
Not only does predictive maintenance keep machines running, but regular preventive maintenance stops manufacturing downtime before it even has a chance to start. Waiting for equipment to fail creates chaos, delays orders, and piles up repair costs.
This is where routine inspections catch worn-out parts early, while scheduled servicing keeps every component in top shape. Maintenance crews check belts, bearings, and circuits before they wear down, replacing them on time instead of after a breakdown shuts everything down. Lubrication schedules, filter changes, and calibration checks ensure machines work at full efficiency without unexpected hiccups.
No doubt skipping preventive maintenance turns small issues into massive disruptions, forcing emergency repairs that eat up time and resources. A factory that runs on planned maintenance avoids last-minute scrambling and keeps production steady.
Utilising AI Technology
It is indeed a wise strategy if manufacturers use AI technology to avoid manufacturing downtime and boost plant efficiency.
AI-driven systems can predict machine failures before they happen. It offers a level of insight that traditional methods cannot match. These systems continuously monitor equipment performance and analyse vast amounts of data in real time.
Further, AI spots patterns in wear and tear, making it easier to schedule maintenance and inspections just in time to prevent issues from turning into costly breakdowns. Rather than relying on a set schedule or waiting for a failure to occur, AI helps prioritise which machines need attention based on their real-time condition. This not only prevents unnecessary downtime but also ensures that the maintenance crew focuses on the most urgent tasks.
AI technology also optimises the entire workflow, suggesting improvements that reduce strain on machines and keep everything running smoothly. When manufacturers adopt AI, they turn downtime from an unpredictable event into a rare occurrence, keeping production lines working at their best.
Cerexio Predictive Maintenance Platform to Walk Away from Downtime Strategically
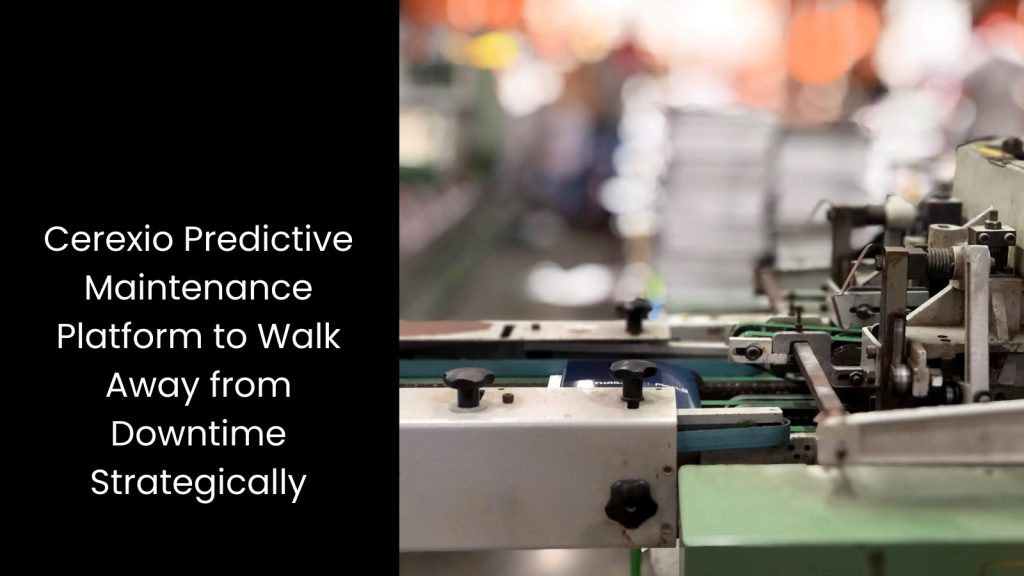
Cerexio has developed a robust Predictive Maintenance Platform that offers manufacturers a strategic way to walk away from costly downtime via the full power of Industry 4.0 technologies. This platform uses advanced data analytics, AI, and IoT sensors to monitor equipment health in real time, predicting potential failures before they disrupt production. With the power of Industry 4.0, the Cerexio platform integrates seamlessly with existing machinery to help reduce downtime.
Saving Manufacturing Resources Utilising the Right Tools
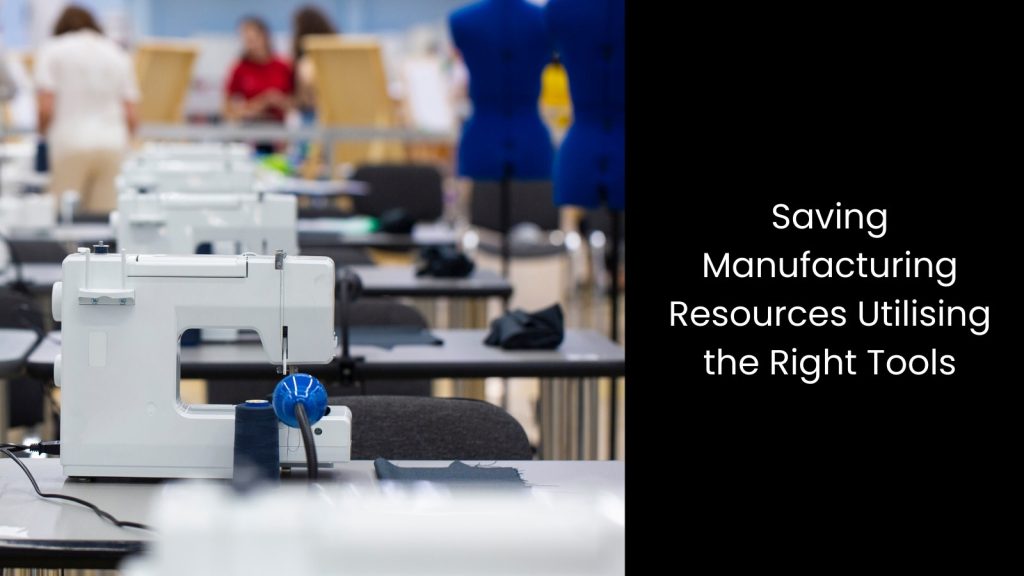
Are you struggling to save valuable resources in your manufacturing plant? Then, choosing the right tools is the best strategy that you have been waiting for! When every part of the process works together, you can cut waste, boost productivity, and create a more sustainable operation. The future of manufacturing starts with smart choices!