In this article, we examine the multifaceted benefits of implementing an Ordering Management System for the manufacturing industry in Singapore.
Exploring Ordering Management System
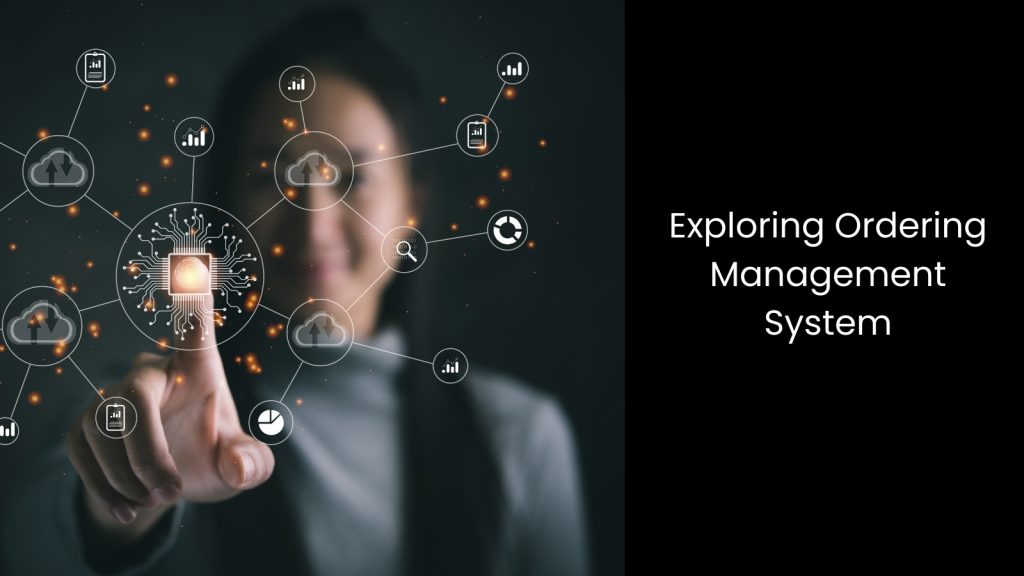
- This is basically a kind of software tool that helps businesses handle their orders from start to finish. It allows companies to track and manage every step of the ordering process, starting when a customer places an order and ending when the customer receives the product.
- An OMS keeps everything organised by automatically entering order details into the system, checking if items are in stock, and updating inventory levels in real-time. This system also helps companies manage their supply chain by coordinating with suppliers and ensuring that products are available when needed.
- With such a tool, businesses can quickly see the status of each order, which helps them fulfil orders faster and more accurately. It also provides valuable data about customer preferences and sales trends, which helps businesses make better decisions and improve their service.
- The best benefit of the latter is its integration capacity. As it can connect with other systems like accounting or customer relationship management tools, this tool helps businesses keep all their information in one place and reduces the chance of mistakes.
- If we specifically look into its application in the manufacturing domain, we see manufacturers face challenges like order errors, inventory mismanagement, and slow processing times. An Ordering Management System solves these issues by automating order entry, providing real-time inventory updates, streamlining workflows, etc. This is indeed why modern manufacturers are interested in occupying OMS in their operations.
Key Benefits of Ordering Management System for Manufacturers in Singapore
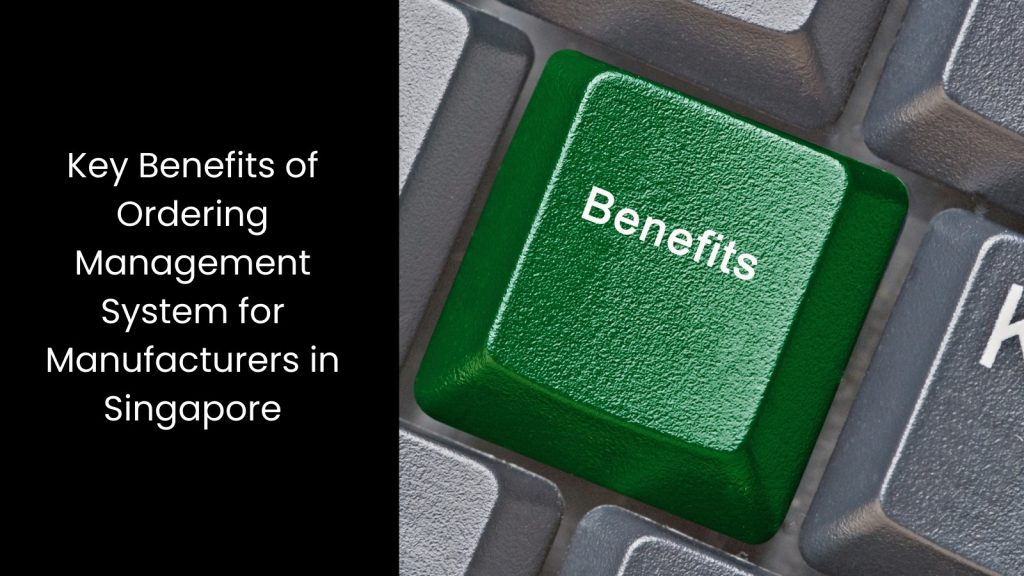
Improving Order Accuracy
For example, manual order entry can lead to mistakes like incorrect product codes or quantities, which can cause production delays and increase costs. Plus, tracking orders manually also makes it hard to keep up with real-time changes and inventory levels, leading to further mistakes and confusion.
This is where the Ordering Management System helps solve these problems with several useful features. No need to emphasise that it reduces errors by automating order entry and processing, which ensures accurate order fulfilment and lowers the chance of costly mistakes. The system automatically captures order details from customers and inputs them correctly, eliminating manual data entry errors.
It also updates inventory levels in real-time, so manufacturers always know what they have in stock and can prevent issues like overselling or stockouts. Since it provides a clear view of each order’s status and integrates with other systems like inventory and accounting, an OMS helps manufacturers manage their processes more smoothly. This way, they can fulfil orders more accurately and quickly.
Real-Time Order Tracking Facility
You know that traditional methods usually rely on manual processes or outdated systems. This will lead to difficulties in monitoring each order’s progress and keeping accurate records. For instance, manufacturers might struggle with delays or errors when tracking orders using spreadsheets or paper logs, which can lead to confusion about where each order is in the production or shipping process. This can result in slow response times and frustrated customers.
An OMS solves these problems with its advanced features. It provides visibility into order status and inventory levels, allowing manufacturers to track orders in real-time. This means the system automatically updates order information and inventory levels as they change, so manufacturers can see exactly where each order is and how much stock is available at any moment.
Boosted Efficiency
However, it will not be that difficult if they have an OMS in place. The latter addresses efficiency-related challenges by improving efficiency in several ways. It streamlines order processing workflows, which means it automates many tasks that used to be done by hand.
For example, the OMS automatically captures order details from customers, updates inventory levels, and schedules production runs, reducing the need for manual intervention. This automation speeds up order fulfilment by quickly moving orders through each stage of the process without delays caused by human error.
Most importantly, the OMS also integrates with other systems, such as inventory and accounting software, as we mentioned above, to ensure that all information is up-to-date and accurate. As it could provide a unified view of the entire manufacturing process, the OMS makes things faster.
Cost Reduction
Costs are the main element that directly affects a company’s profitability and competitiveness.
High costs can come from various sources, including inefficient processes, errors, and poor inventory management. When manufacturers rely on conventional order management, it involves manual tasks, and these methods can lead to mistakes, delays, and wasted resources, which drive up costs.
This is where the Ordering Management System shines. It helps solve these cost-related issues with its advanced features, as the latter minimises operational costs by automating repetitive tasks, which reduces the need for manual input and decreases the chance of errors.
For instance, the OMS automatically processes orders and updates inventory levels, eliminating the time and cost associated with manual tracking and data entry. It also helps optimise inventory levels by providing real-time updates on stock, allowing manufacturers to avoid overstocking or running out of items.
When it helps with predicting demand and adjusting inventory accordingly, the OMS prevents waste and reduces holding costs. Not to mention that the OMS integrates with other business systems, ensuring accurate and efficient communication across departments, which helps avoid costly mistakes and delays.
Cerexio Production Order Management System for a Scalable Business
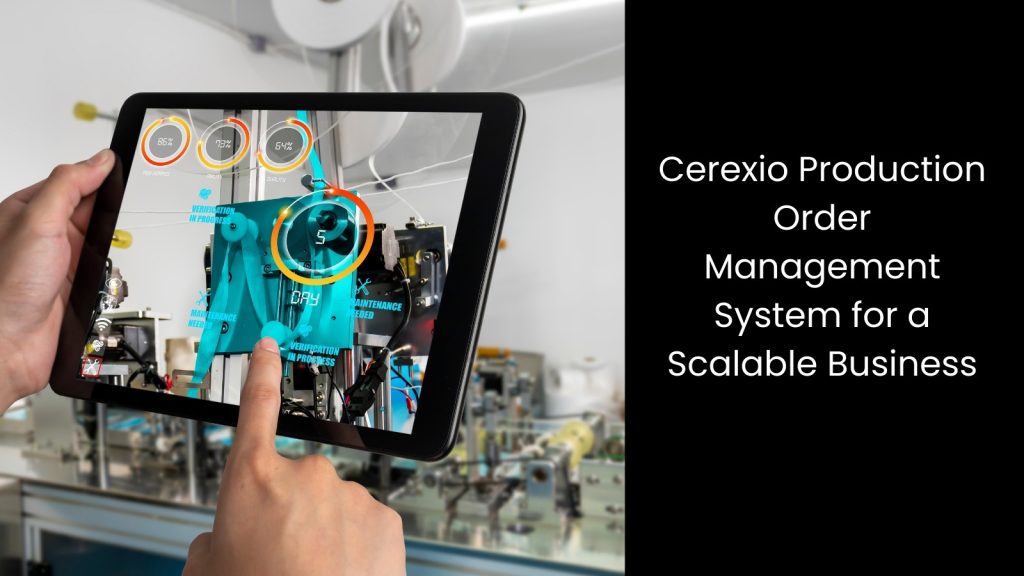
Cerexio Production Order Management System supports scalable manufacturing as it automates order processes, integrates with inventory and supply chain systems, and manages increased order volumes seamlessly. It allows businesses to handle growth without additional manual effort, streamline production workflows, and maintain efficiency. This scalability ensures that as production demands rise, the Cerexio solution continues to support smooth and effective operations.
Simplifying Production Floor Operations via the Ordering Management System
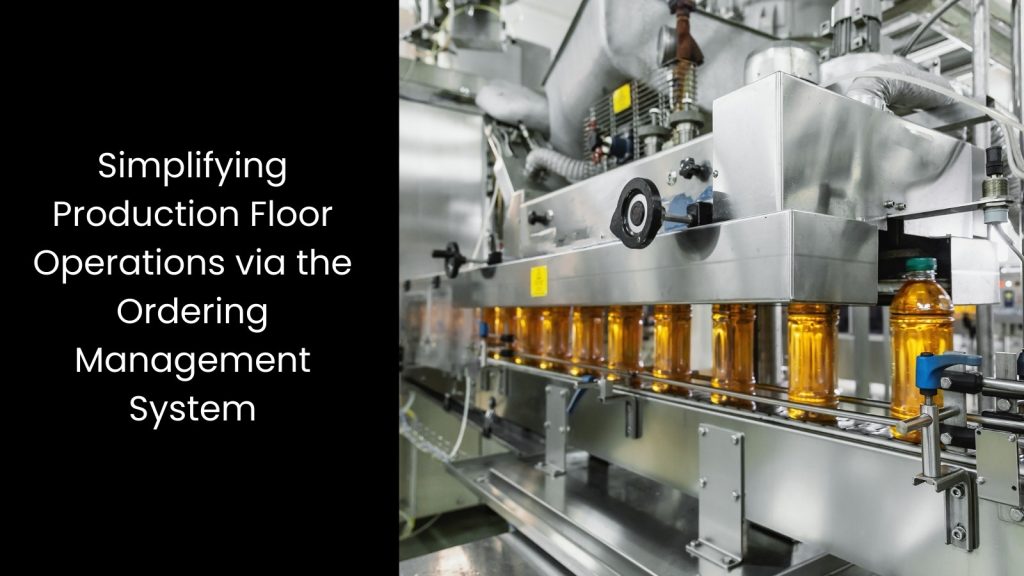
Singapore is in a venture to become the global hub for manufacturing in the upcoming years. Outstanding customer service and order fulfilment are what bring Singapore towards this goal. Holding hands with a robust featured Ordering Management System from a reputed supplier helps simplify production floor operations and means one more step closer to the ultimate goal.