This article deep dives into the numerous advantages of SLM, exploring its potential to revolutionise manufacturing processes and product design in the dynamic Singaporean landscape.
What is Selective Laser Melting?
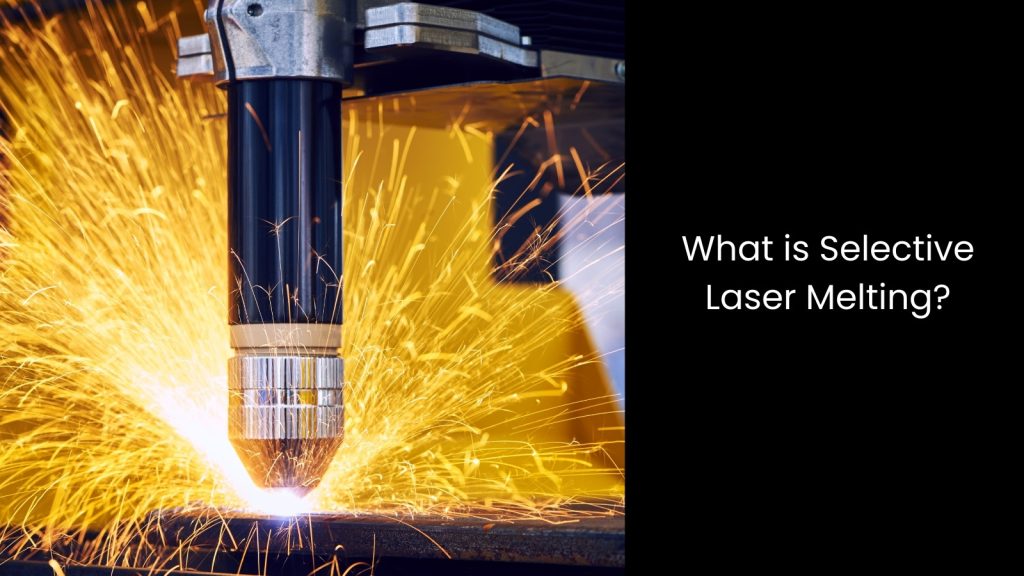
- Before stepping into the world of its benefits, let us give you a 360-degree view of the SLM concept or process.
- In the simplest terms, this is an advanced manufacturing technique that creates complex parts by melting metal powders with a laser. Unlike traditional methods that cut away material from a solid block, SLM builds up objects layer by layer, using a high-powered laser to melt and fuse the powder particles together.
- This process starts with a digital 3D model of the part, which the machine reads to guide the laser. The machine spreads a thin layer of metal powder on a build platform. The laser then scans the layer, melting the powder according to the design. After each layer is melted, the platform lowers slightly, and a new layer of powder is applied.
- Then the laser melts the new layer, bonding it with the previous one. This continues until the entire part is built. This is how the entire process goes on.
- Anyway, SLM stands out from other manufacturing methods because it allows the creation of highly detailed and complex shapes that would be difficult to make with traditional techniques. It does not need moulds or tooling, which cuts down on costs and time. The ability to build parts with intricate internal structures and custom designs makes SLM especially useful for industries like aerospace and medicine, as we stated before. This is what basically makes SLM a powerful tool for modern manufacturing.
Top Advantages of Selective Laser Melting for Manufacturing Singapore
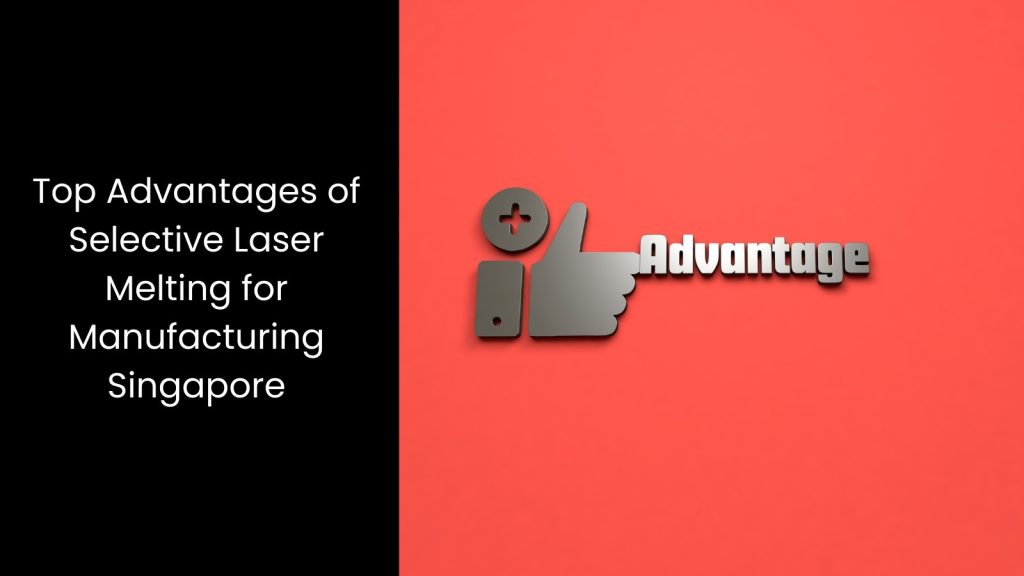
Tooling Elimination
In traditional manufacturing, creating parts usually requires specific moulds or tools, which can be costly and time-consuming to make. These moulds are essential to shaping the material into the final part, and if a design changes, manufacturers usually have to make new olds. Not to mention, this adds extra costs and slows down production.
However, SLM simplifies this process as it eliminates the need for moulds and tools altogether. Instead of using moulds, SLM builds parts directly from a digital 3D design. It does this by using a laser to melt metal powder layer by layer, fusing the powder together to form the part. This method allows for much more flexibility in production because manufacturers do not have to invest in new moulds or reconfigure tools every time they want to make a different part.
For Singapore, where production needs can change quickly, this flexibility is certainly valuable. SLM enables production companies to produce small batches of parts or custom components without extra setup costs or delays. The ability to quickly switch between different designs and production runs without needing new tools makes SLM a cost-effective and efficient choice.
Intricate Geometries
When you make parts with complicated internal structures or very fine details, it can be extremely difficult or even impossible with these methods. SLM, on the other hand, excels in this area. How is it possible?
It builds parts layer by layer directly from a digital 3D design, using a laser to melt metal powder as we described above. This layer-by-layer approach allows SLM to create complex shapes and detailed features that traditional methods cannot easily achieve. For example, SLM can produce parts with intricate internal channels or detailed lattice structures that are not possible with conventional techniques. This capability not only improves the performance of the parts but also opens up new possibilities for innovation in product design.
Minimised Material Waste
However, this is different when it comes to the SLM. It uses a different method. You already know it builds parts layer by layer directly from a digital 3D design. The process begins by spreading a thin layer of metal powder on a build platform. A laser then melts only the powder needed to form the part according to the design. After each layer is completed, the platform lowers slightly, and a new layer of powder is added and melted.
This precise approach makes sure SLM uses only the exact amount of material needed to make the part. There is no extra waste because the laser melts only the powder that is required, leaving any unused powder in the build chamber to be reused in future prints.
Enhanced Mechanical Properties
This improvement occurs as SLM builds parts layer by layer from a digital model using a high-powered laser to melt metal powder. This precise process results in a denser and more uniform material structure. The laser fuses the powder particles at a very high temperature, which creates strong bonds between them.
This strong bonding improves the overall strength of the part, making it more resistant to stress and wear. Recall those traditional manufacturing methods, like casting or machining, for a moment. You had to leave parts with weaker spots or imperfections, right?
In industries like aerospace, automotive, and medical devices, where parts need to withstand extreme conditions and high stresses, having enhanced mechanical properties is a number one concern. This is where SLM’s ability to produce parts with superior strength and durability offers significant benefits. It allows manufacturers to create components that perform better and last longer, reducing the need for repairs or replacements. This improvement in mechanical properties helps businesses meet demanding industry standards and deliver products that are both reliable and high-performing.
Cerexio MES for Any Manufacturing Technique in Singapore
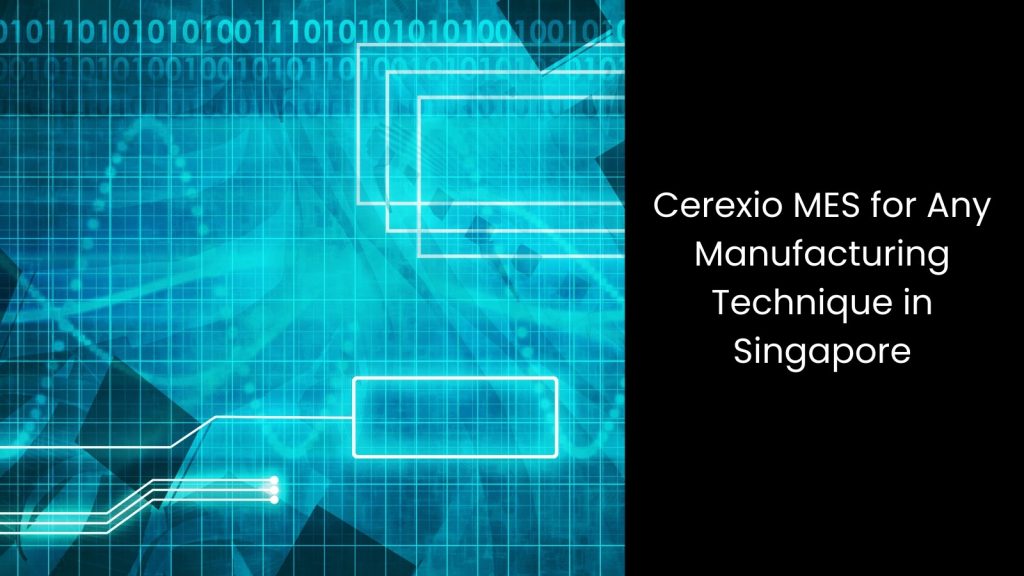
Cerexio presents a robust Manufacturing Execution System (MES) that can enhance any manufacturing technique, like SLM, by providing real-time data, streamlining processes, and ensuring quality control. Our solution integrates with various production methods to optimise your manufacturing operations up to 100%. If you need to scale up your production floor operations, Cerexio MES is the right path to walk down.
Enhancing Production Efficiency with SLM Process-Enabled Solutions
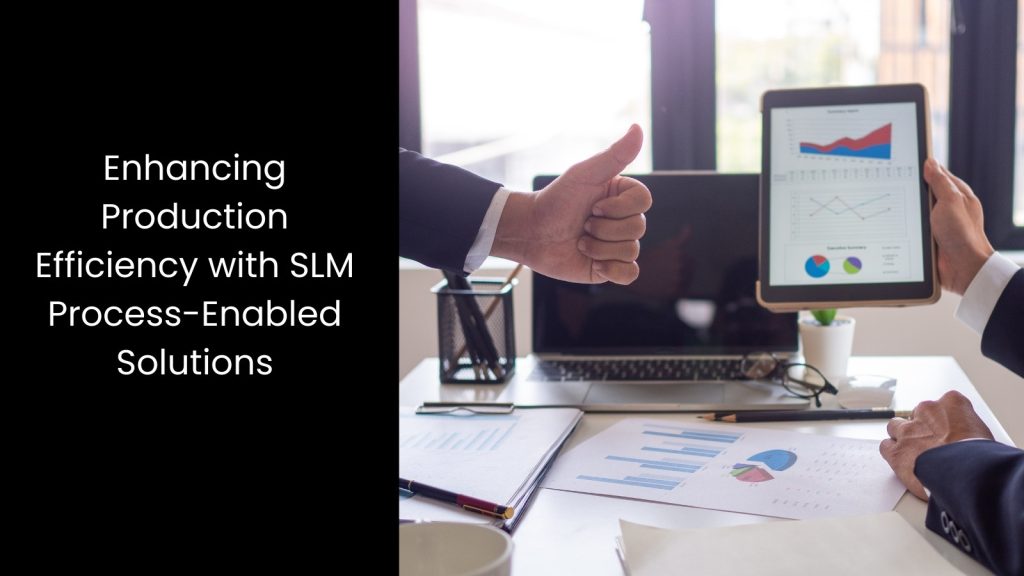
You have already witnessed how SLM technology transforms manufacturing by enhancing production efficiency and accuracy. When you utilise SLM solutions, your company can achieve higher precision, lower waste, and faster turnaround times. Investing in SLM-enabled advanced tech solutions from a reputed supplier ensures that your business stays ahead in a competitive industry, delivering superior products on time.