“How can I streamline my manufacturing order fulfilment process?” If you look into Google, you can see that this is a question many manufacturers have asked as they seek solutions to improve efficiency and customer satisfaction. It is a proven fact that relying on just one order fulfilment method can lead to delays, higher costs, and poor customer experiences. In today’s fast-moving market, manufacturers have no option but to adapt to increasing customer demands and fluctuating supply chains. But how is it possible? ‘Omnichannel fulfilment’ is the answer.
What is omnichannel fulfilment in manufacturing? How can this process help manufacturers boost their operations? This article covers everything about that.
What is omnichannel fulfilment in manufacturing? How can this process help manufacturers boost their operations? This article covers everything about that.
What is Omnichannel Fulfillment?
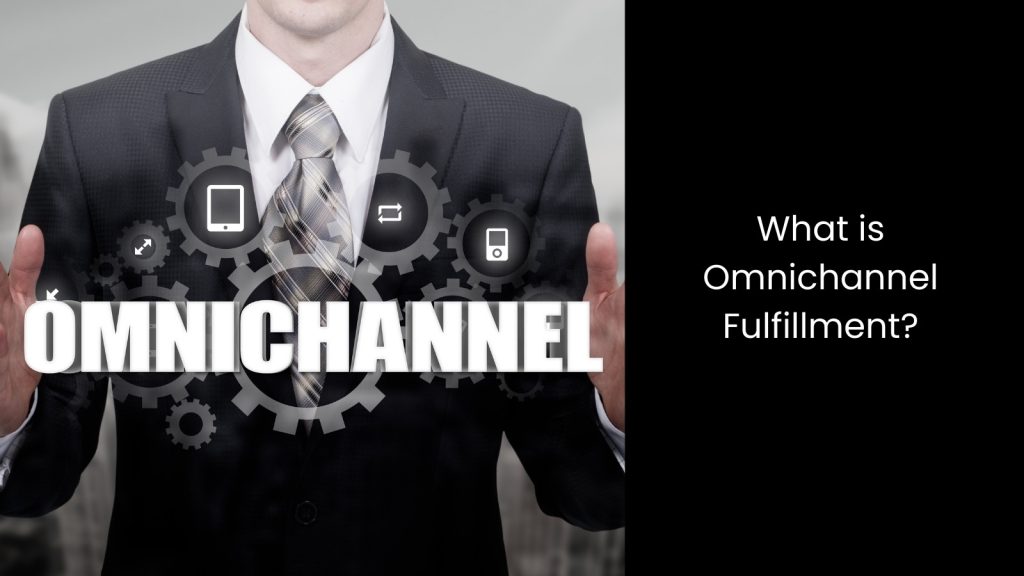
- You need to understand that this is a multi-faceted approach that any sort of business can implement. So, what exactly is this?
- Omnichannel fulfilment is a smart way businesses handle orders across different sales channels without creating separate fulfilment setups. This approach keeps everything in one place, making it easier to receive, store, process, pick, pack, and ship products efficiently.
- With a centralised system, logistics providers keep up with changing demands, optimise workflows, and move orders faster, whether they come from online stores, physical shops, or third-party marketplaces. With this approach, businesses can automate tasks, cut down on errors, and speed up deliveries, which makes customers happy and increases profits in today’s competitive market.
- However, the main point is that a strong inventory management system sits at the core of omnichannel fulfilment. It allows businesses to track, allocate, and shift inventory seamlessly across multiple channels. This way, customers easily find and order what they need through their preferred platform, eliminating the hassle of separate fulfilment processes for each sales channel.
Exploring the Importance of Omnichannel Fulfillment in Manufacturing
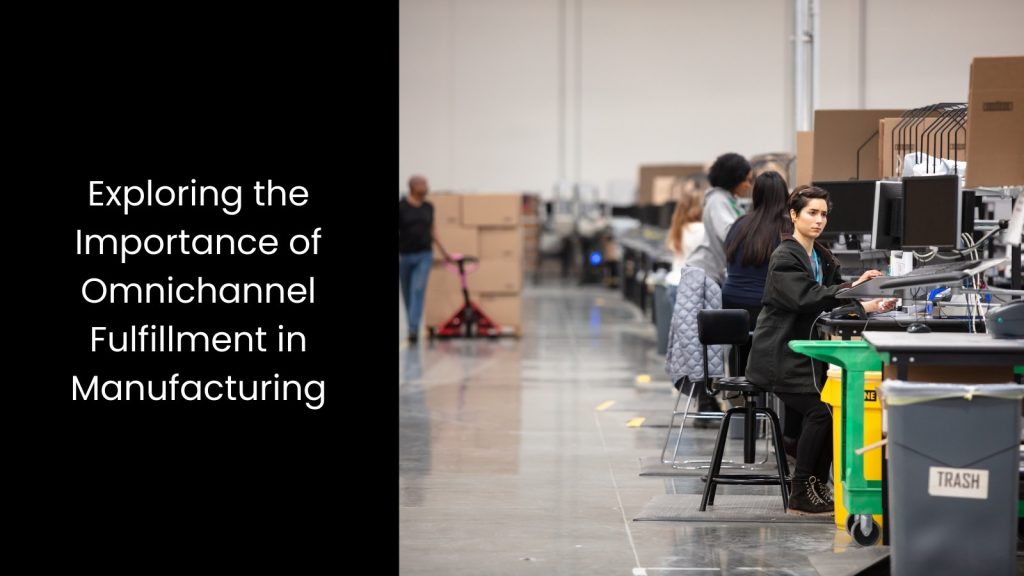
Omnichannel Fulfillment Helps Optimise Inventory Management
Manufacturers put so much pressure on their inventory and its management because every delay, shortage, or excess stock affects profits and customer satisfaction. Omnichannel fulfilment helps solve these problems as it creates a smooth and connected system that tracks stock levels in real time.
With a centralised inventory, manufacturers can easily move products between different sales channels without confusion. Real-time tracking makes it simple to know exactly how much stock exists, where it is stored, and when to restock. This setup removes the guesswork, and it will help businesses avoid stockouts that frustrate customers or overstocking that ties up cash in unsold goods.
Instead of relying on outdated tracking methods, omnichannel fulfilment connects warehouses, factories, and distribution centres under one system. This certainly allows fast updates and accurate forecasting. If one channel experiences a sudden spike in demand, inventory quickly shifts to meet the need without slowing down fulfilment.
This approach reduces wasted space, prevents unnecessary production, and speeds up order processing, making it easier to dispatch products without delays.
With a centralised inventory, manufacturers can easily move products between different sales channels without confusion. Real-time tracking makes it simple to know exactly how much stock exists, where it is stored, and when to restock. This setup removes the guesswork, and it will help businesses avoid stockouts that frustrate customers or overstocking that ties up cash in unsold goods.
Instead of relying on outdated tracking methods, omnichannel fulfilment connects warehouses, factories, and distribution centres under one system. This certainly allows fast updates and accurate forecasting. If one channel experiences a sudden spike in demand, inventory quickly shifts to meet the need without slowing down fulfilment.
This approach reduces wasted space, prevents unnecessary production, and speeds up order processing, making it easier to dispatch products without delays.
Omnichannel Fulfillment Simply Increases Operational Efficiency
Manufacturing is a complex procedure that involves handling raw materials, managing production lines, and fulfilling orders across multiple sales channels. Therefore, keeping everything organised without slowing down operations can feel impossible without the right system in place.
This is where omnichannel fulfilment changes the game through its ability to automate order processing and fulfilment, cutting out manual work that often leads to costly mistakes. Instead of juggling multiple systems, manufacturers use one connected platform that syncs warehouses, suppliers, and shipping carriers, making sure every step runs smoothly.
As a part of that, automation speeds up tasks like order verification, inventory updates, and shipment tracking, reducing delays and human errors that disrupt the supply chain. When businesses handle orders from different platforms, retail stores, and wholesalers all at once, a slow or outdated fulfilment process creates chaos.
This is why they require a smart approach like omnichannel fulfilment. It keeps everything in sync, ensuring that every order reaches the right destination without mix-ups. This efficiency helps manufacturers move products faster, cut down on wasted time, and improve coordination across all fulfilment points.
This is where omnichannel fulfilment changes the game through its ability to automate order processing and fulfilment, cutting out manual work that often leads to costly mistakes. Instead of juggling multiple systems, manufacturers use one connected platform that syncs warehouses, suppliers, and shipping carriers, making sure every step runs smoothly.
As a part of that, automation speeds up tasks like order verification, inventory updates, and shipment tracking, reducing delays and human errors that disrupt the supply chain. When businesses handle orders from different platforms, retail stores, and wholesalers all at once, a slow or outdated fulfilment process creates chaos.
This is why they require a smart approach like omnichannel fulfilment. It keeps everything in sync, ensuring that every order reaches the right destination without mix-ups. This efficiency helps manufacturers move products faster, cut down on wasted time, and improve coordination across all fulfilment points.
Cost Reduction Occurs through Omnichannel Fulfillment
In the production world, there is no other outstanding benefit than cost reduction because every dollar saved strengthens the bottom line.
Omnichannel fulfilment helps manufacturers slash expenses by fine-tuning warehouse locations, optimising transportation routes, and streamlining order processing. Instead of running multiple fulfilment centres with separate inventories, businesses consolidate stock into strategically placed warehouses. No need to say that the latter cuts down on storage costs and reduces wasted space.
In another way, such a centralised system allows orders to be processed faster, and it eliminates the need for extra labour and minimises human errors that often lead to costly returns or delays. Smart routing ensures that shipments take the most efficient paths, avoiding unnecessary detours and reducing fuel expenses. Manufacturers can save money by shipping products from the nearest warehouse instead of paying high costs to move goods across long distances.
With better inventory distribution and seamless logistics coordination, businesses reduce wasted resources, maintain profitability, and keep customers happy with on-time deliveries. So, yes, omnichannel fulfilment turns fulfilment into a cost-efficient machine, allowing manufacturers to stay competitive without sacrificing quality or speed.
Omnichannel fulfilment helps manufacturers slash expenses by fine-tuning warehouse locations, optimising transportation routes, and streamlining order processing. Instead of running multiple fulfilment centres with separate inventories, businesses consolidate stock into strategically placed warehouses. No need to say that the latter cuts down on storage costs and reduces wasted space.
In another way, such a centralised system allows orders to be processed faster, and it eliminates the need for extra labour and minimises human errors that often lead to costly returns or delays. Smart routing ensures that shipments take the most efficient paths, avoiding unnecessary detours and reducing fuel expenses. Manufacturers can save money by shipping products from the nearest warehouse instead of paying high costs to move goods across long distances.
With better inventory distribution and seamless logistics coordination, businesses reduce wasted resources, maintain profitability, and keep customers happy with on-time deliveries. So, yes, omnichannel fulfilment turns fulfilment into a cost-efficient machine, allowing manufacturers to stay competitive without sacrificing quality or speed.
It Paves the Way for Greater Supply Chain Resilience
The supply chain is one complicated aspect that every manufacturing domain has to manage with extreme precision because any disruption can throw operations into chaos. Omnichannel fulfilment builds a stronger, more flexible supply chain by diversifying order fulfilment strategies.
This will allow manufacturers to stay on top of shifting demands and unexpected disruptions.
Instead of relying on a single distribution channel, businesses use multiple fulfilment options, including direct-to-consumer shipping, in-store pickup, and third-party logistics. This setup ensures that even if one fulfilment route faces delays, alternative options keep orders moving without slowing down operations.
A connected system helps manufacturers shift inventory between warehouses, reroute shipments, and prioritise urgent orders in real-time, reducing downtime and lost sales. Omnichannel fulfilment also allows businesses to respond quickly to demand fluctuations by redistributing stock to high-demand locations before shortages happen.
When peak seasons hit or supply chain bottlenecks appear, automated workflows ensure that products reach customers without unnecessary delays. Instead of scrambling to fix supply chain breakdowns, manufacturers stay ahead of disruptions with better visibility and improved coordination between suppliers, warehouses, and retailers if they implement this mechanism.
This will allow manufacturers to stay on top of shifting demands and unexpected disruptions.
Instead of relying on a single distribution channel, businesses use multiple fulfilment options, including direct-to-consumer shipping, in-store pickup, and third-party logistics. This setup ensures that even if one fulfilment route faces delays, alternative options keep orders moving without slowing down operations.
A connected system helps manufacturers shift inventory between warehouses, reroute shipments, and prioritise urgent orders in real-time, reducing downtime and lost sales. Omnichannel fulfilment also allows businesses to respond quickly to demand fluctuations by redistributing stock to high-demand locations before shortages happen.
When peak seasons hit or supply chain bottlenecks appear, automated workflows ensure that products reach customers without unnecessary delays. Instead of scrambling to fix supply chain breakdowns, manufacturers stay ahead of disruptions with better visibility and improved coordination between suppliers, warehouses, and retailers if they implement this mechanism.
Omnichannel Fulfillment Facilitates Faster Order Processing and Delivery
When you rely on just one fulfilment method, there will be no control over delays. The reason is a single issue can slow down the entire process.
However, if you have omnichannel fulfilment, it eliminates these bottlenecks by integrating multiple fulfilment methods like direct shipping, in-store pickup, and third-party logistics, making order processing and delivery much faster.
Instead of waiting for a centralised warehouse to handle every order, businesses fulfil purchases from the closest and most efficient location.
A well-connected system automatically routes orders through the best fulfilment option, ensuring customers receive their products without unnecessary delays. Manufacturers reduce congestion in distribution centres by using retail stores as mini fulfilment hubs, speeding up local deliveries and cutting down shipping distances.
Omnichannel fulfilment also enables third-party logistics providers to step in when needed, expanding delivery options and reducing strain on in-house operations.
However, if you have omnichannel fulfilment, it eliminates these bottlenecks by integrating multiple fulfilment methods like direct shipping, in-store pickup, and third-party logistics, making order processing and delivery much faster.
Instead of waiting for a centralised warehouse to handle every order, businesses fulfil purchases from the closest and most efficient location.
A well-connected system automatically routes orders through the best fulfilment option, ensuring customers receive their products without unnecessary delays. Manufacturers reduce congestion in distribution centres by using retail stores as mini fulfilment hubs, speeding up local deliveries and cutting down shipping distances.
Omnichannel fulfilment also enables third-party logistics providers to step in when needed, expanding delivery options and reducing strain on in-house operations.
Cerexio AI-Powered Solution for Optimised Omnichannel Fulfillment
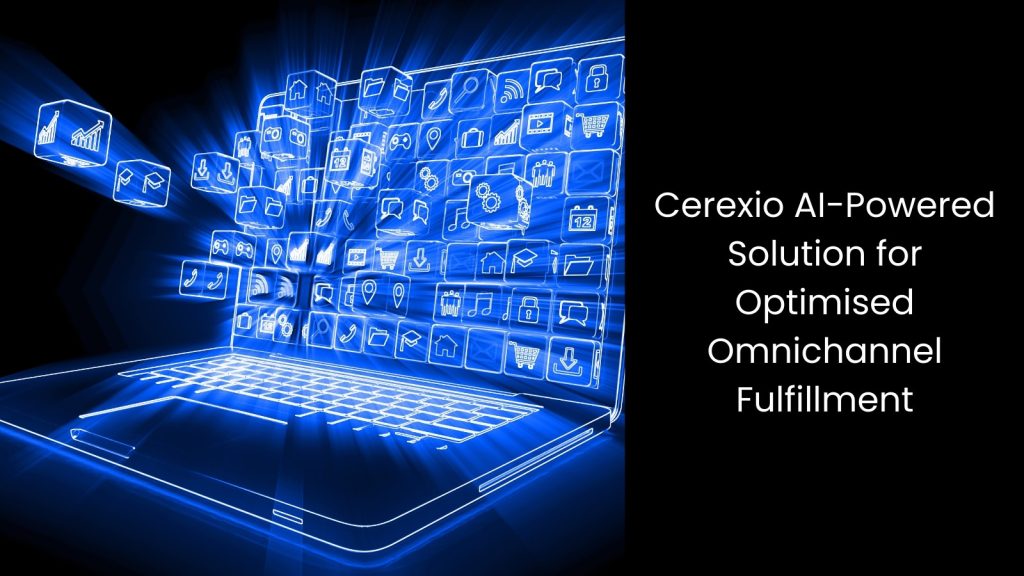
Cerexio’s AI-powered Production Order Management System revolutionises omnichannel fulfilment for manufacturers as our system can optimise your order processing, automate workflows, and ensure real-time inventory accuracy all under one screen. This intelligent solution accelerates deliveries, reduces costs, and adapts to demand shifts effortlessly, keeping fulfilment seamless across multiple channels.
Integrating Omnichannel Fulfillment for Better Customer Service in Manufacturing
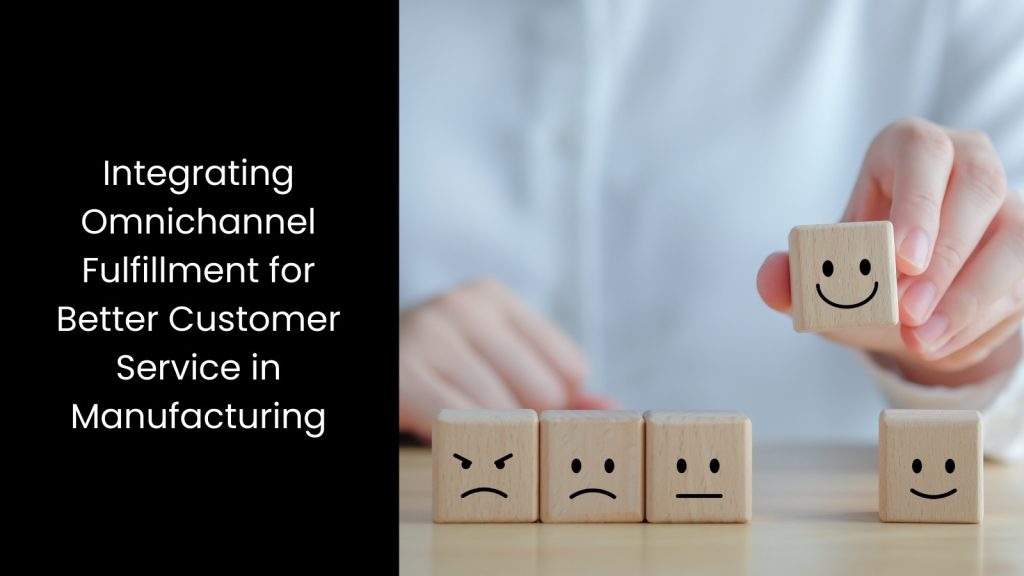
Manufacturers embracing omnichannel fulfilment unlock a new level of customer service. As demand grows, staying agile with smart fulfilment strategies keeps businesses ahead, meeting customer expectations with precision and speed. So, it is time for a change!