In a manufacturing landscape full of various technologies and manufacturing realms, there is still a debate going on to choose what is best. It is truly a difficult thing to decide, as some of them follow traditional mechanisms and the rest follow new and modified strategies to produce goods. Amongst all of them, Additive Manufacturing stands tall as one of the key players in the manufacturing world. Although many manufacturers are attracted to this method, modern companies tend to stay away from it stating that it has many flaws and limitations.
In this article, we will look into the Additive Manufacturing arena and explore the major limitations that restrict smooth production in this dynamic manufacturing world.
We will know
Exploring Additive Manufacturing
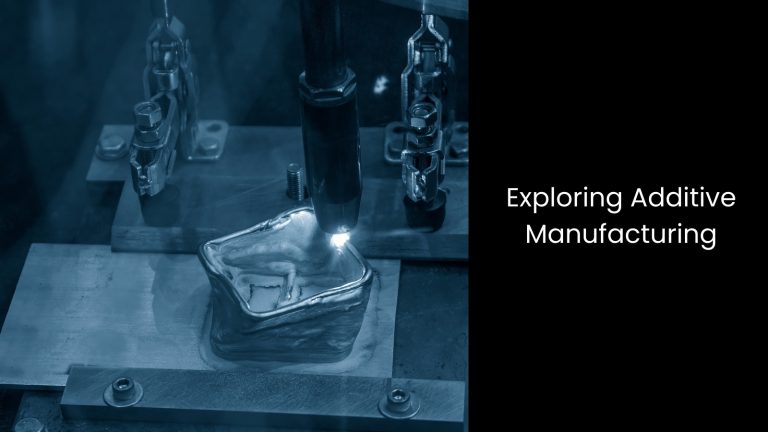
- Additive Manufacturing or, as you may know, AM, is another name for a process called 3D printing. This is a process where digital designs are transformed into physical objects by adding material layer by layer.
- Unlike traditional manufacturing methods like subtractive manufacturing, which involves cutting away material from a solid block, AM builds up objects from the ground up. This is special because it clearly minimises waste. This method is a bit different from the rest of the manufacturing world just because of its ability to create complex and intricate designs that are difficult or impossible to achieve with conventional techniques.
- What sets it apart? This one has some special features, which include rapid prototyping, allowing for quick iterations and modifications of designs, and customisation, enabling the production of unique, tailored products. This technology is popular among manufacturers because it reduces material costs and shortens production times. Not to mention that the latter allows for more design flexibility.
- Where does this apply? This actually cannot be applied everywhere. Yet, it has an extended application, from medical implants and prosthetics to aerospace components, automotive parts, and even consumer goods like jewellery and fashion items.
- As you can see, the ability to produce strong yet lightweight structures and the potential for on-demand production make AM a revolutionary tool in modern manufacturing.
Main 6 Major Limitations of Additive Manufacturing
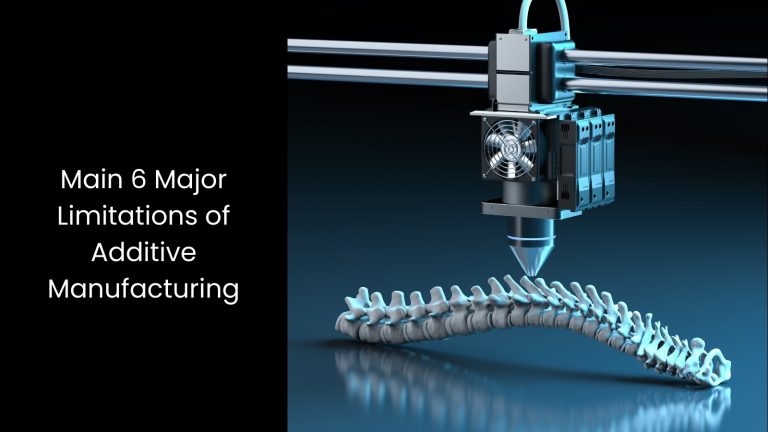
Environmental Restrictions
One of the major limitations of additive manufacturing is environmental restrictions.
When using this technology, support structures, which are needed during the printing process, and failed prints can be difficult to remove and manage. If the manufacturers do not try to recycle or properly dispose of these materials, they can harm the environment.
For example, plastic waste from failed prints and excess material might contribute to pollution if not handled correctly. Plus, some materials used in 3D printing can be toxic or non-biodegradable, posing further environmental risks.
This is why manufacturers must ensure proper waste management practices, such as recycling and safe disposal, to minimise these impacts. But these are quite expensive.
These environmental challenges make it essential for the industry to develop more sustainable practices and materials to protect the environment. It is not all about benefiting from the advantages of additive manufacturing.
Limited Materials
Another major limitation of additive manufacturing is the restricted variety of materials that can be used simultaneously. It is true that in today’s world, the range of available materials is expanding. However, it remains much smaller compared to traditional manufacturing methods.
This limitation can impact the performance, durability, and quality of the final products. For instance, while conventional manufacturing can combine various metals, plastics, and composites in a single process, additive manufacturing is often restricted to using one type of material at a time or a few compatible ones.
This can lead to products that do not meet the desired strength, flexibility, or longevity requirements.
Consequently, this restriction on material choices can limit the broader adoption of additive manufacturing for certain applications. This is especially where diverse material properties are essential for the product’s functionality and lifespan.
Limited Quantities
A major issue with additive manufacturing is its ability to produce only small quantities of items.
Due to expanding new methods, this technology excels at creating small batches of goods. However, it is not yet suitable for large-scale production. This limitation arises because additive manufacturing is a relatively slow process. You know, when it comes to the latter, each item is built layer by layer. This certainly can take a considerable amount of time, especially for complex or large parts.
As a result, when a large volume of parts is needed, this method becomes inefficient and time-consuming compared to traditional manufacturing techniques. If we look at the other types, they can mass-produce items quickly and economically.
Therefore, although additive manufacturing is ideal for prototyping, custom items, and small production runs, it struggles to meet the demands of high-volume manufacturing. This is the most practical issue manufacturers find in the above-said manufacturing type.
Surface Quality Challenges
Another challenge of the latter is indeed achieving good surface quality.
The surface finish of 3D-printed parts usually falls short. This is particularly true when producing complex structures.
The problem lies here: Unlike traditional manufacturing methods, which can create smooth surfaces more easily, additive manufacturing builds objects layer by layer. This can result in a rough or uneven finish, with visible layer lines and imperfections.
You know that achieving a smooth surface requires additional post-processing steps, such as sanding or polishing. However, this can be time-consuming and costly.
So, as a fact, these surface quality challenges can affect the aesthetics, functionality, and mechanical properties of the final product. It will limit the use of additive manufacturing for applications where a high-quality finish is essential.
Even though it comes out with many advantages, the inability to consistently produce smooth surfaces remains a notable challenge of additive manufacturing technology.
Limitations in Sizes
If you look into its capacity, this is surely additive manufacturing, which imposes a notable limitation.
It constrains the size of producible objects! You know that in the manufacturing production line, the printer’s dimensions and available workspace determine the maximum size.
Printing larger objects requires multiple parts and requires subsequent assembly. However, this approach can prove time-consuming and challenging as it demands precise alignment and bonding.
On the other hand, producing larger items surely necessitates specialised equipment, escalating both production costs and complexity.
Consequently, while additive manufacturing provides flexibility and customisation, its size limitations undoubtedly prevent efficient and economical production of large-scale items.
Complexity Limitations
Additive manufacturing encounters challenges when considering the complexity of the designs that can be produced.
While it allows the creation of buildings and objects with intricate shapes, the process struggles with designs that are overly complex.
Such designs usually require additional support structures or post-processing steps. This increases both time and costs.
The need for these extra elements arises because complex shapes may lack the structural integrity to be printed successfully without support. Not to mention that such intricate designs will present challenges during printing. The latter leads to errors or defects that require further refinement, for sure.
Cerexio MES for Limitless Manufacturing Perfection
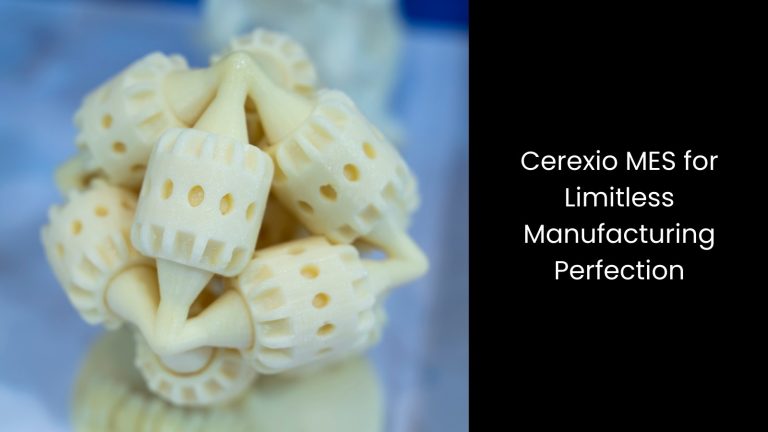
No matter what type of manufacturing process you follow, Cerexio MES is there with robust features and functionalities specifically tailored to your needs. As this solution is powered by Industry 4.0 digital capabilities and provides every aspect under one canopy, it is easier for you to stay away from production inefficiencies and accomplish the desired quality without errors.
Clearing Out Challenges in Manufacturing with Modern Tools
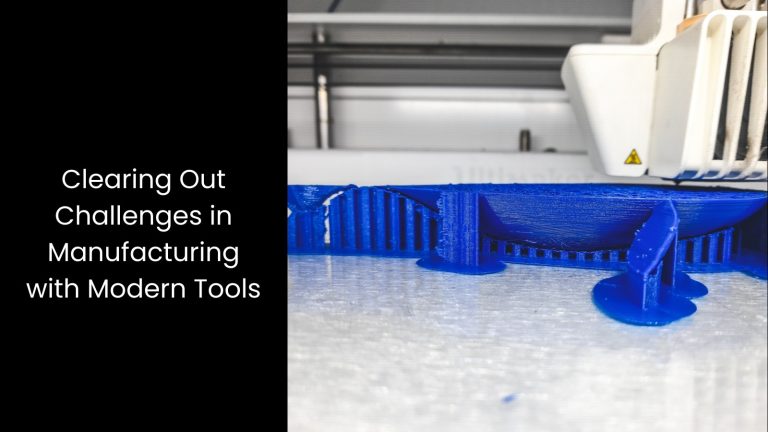
There is no process in the manufacturing realm that 100% avoids challenges. It is up to you to decide which path you follow. However, it is a must to understand your industry specifications and requirements with the expected manufacturing process through modern tools.