Singapore owns a versatile manufacturing sector that is a vital cog in the country’s economic engine. Renowned for its innovation and precision engineering, Singapore constantly sets out to stay at the front line of global technological advancements. One such technology that plays a crucial role in the manufacturing of Singapore is Electro Discharge Machining or, in short, EDM.
In this blog, we will discover why it has become indispensable for manufacturing in Singapore, and we will unpack the unique capabilities of EDM, showcasing its advantages over traditional machining methods.
We will know
What is Electro Discharge Machining?
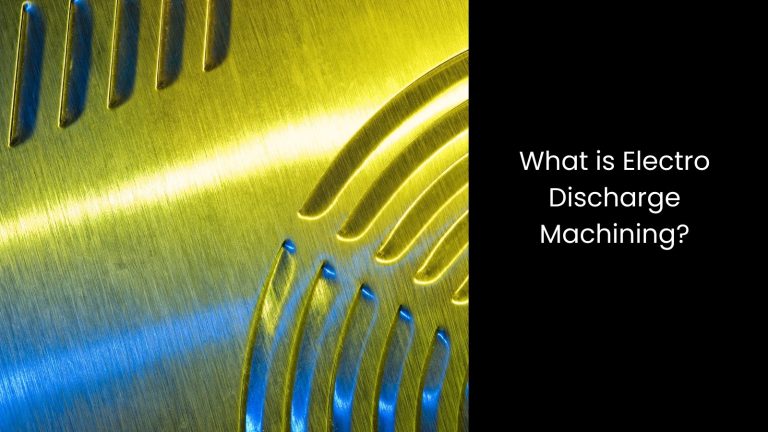
- This is a special process used in manufacturing to shape hard metals and other conductive materials. How is it different? Let us explain.
- Instead of using a cutting tool that touches the material, EDM uses electrical sparks to erode the material. Now let us show you how this is done on the production floor. The machine creates an electric field between an electrode and the workpiece. The electrode, which usually has the shape of the desired cut, moves close to the workpiece without touching it.
- When they come close enough, the electric field becomes strong and generates sparks. These sparks are very hot and melt or vaporise tiny amounts of the material. The machine flushes away the melted material with a liquid, usually deionised water or oil.
- This process repeats many times per second, gradually shaping the workpiece.
- As you can see, EDM is great for making intricate shapes, fine details, and very accurate cuts. It can work on hard metals like titanium and hardened steel, which are tough to cut with regular methods.
Top 5 Advantages of Electro Discharge Machining for Manufacturing
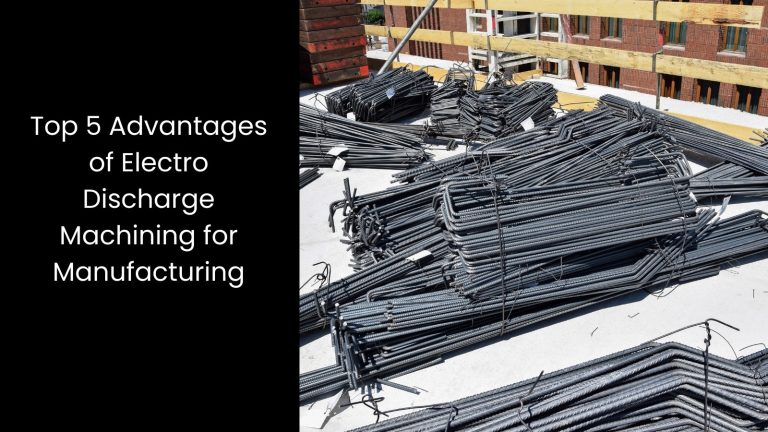
Reducing Tool Wear
Electro-discharge machining helps reduce tool wear in manufacturing by using a unique method that does not rely on direct contact between the cutting tool and the material. Unlike traditional machining methods, where tool wear can be a significant issue, EDM uses electrodes that do not make direct contact with the workpiece. This surely results in minimal tool wear and consistent performance over extended periods.
Since the electrode and the workpiece never touch, there is no friction to cause wear on the electrode. This means the electrode lasts much longer than traditional cutting tools, which get worn down from the constant friction and heat of cutting. Since the electrode maintains its shape and size, it can produce consistent, precise cuts over long periods of time.
This is especially important for making complex shapes and detailed parts that require high accuracy. As it can reduce tool wear, EDM helps save on costs because you do not need to replace the electrodes as often as you would with traditional tools. It also means less downtime for changing tools, leading to higher productivity.
So yes, EDM’s method of using electrical sparks instead of direct contact to cut materials undoubtedly helps reduce tool wear and maintain consistent manufacturing performance.
Smooth Surface Finish
Smooth surfaces are a top priority in manufacturing, as they improve the performance and longevity of parts. When parts have smooth surfaces, they experience less friction, which leads to less wear and tear. This is important for moving parts like gears or engine components.
Smooth surfaces also enhance the appearance of finished products, which is vital for consumer goods. However, with traditional machining, the manufacturing industry struggles to achieve smooth surfaces because cutting tools leave behind tiny ridges or tool marks. These imperfections can cause increased friction and wear on the parts, reducing their lifespan and efficiency. Traditional methods also require additional finishing processes like grinding or polishing to smooth out these imperfections, which takes extra time and effort.
This is where EDM helps solve this problem by using electrical sparks instead of cutting tools to shape materials. The sparks create tiny craters on the surface of the workpiece, which are much finer and more uniform than the ridges left by traditional machining tools. This results in a very smooth surface finish right from the start.
EDM can achieve very smooth surface finishes, which can reduce or eliminate the need for additional finishing processes, such as grinding or polishing. Since this can reduce the need for these extra steps, EDM saves time and reduces costs in the manufacturing process.
Material Versatility
Machining any material is important in manufacturing. This is mainly because different parts require different materials based on their function and the conditions they will face. For example, some parts need to be very hard and wear-resistant, while others need to be lightweight or corrosion-resistant.
Traditional machining cannot help with this, as it relies on cutting tools that wear out quickly when working with very hard materials like titanium or tungsten. These hard materials can dull or break traditional cutting tools, making it difficult and expensive to machine them. On the other hand, softer metals can also pose problems, as traditional methods can create burrs or deformations.
The latter helps overcome these challenges by using electrical sparks to shape the material instead of traditional cutting tools. EDM can machine any conductive material regardless of its hardness, including hard metals like titanium, tungsten, and tool steels, as well as softer metals. When they use EDM, manufacturers can easily machine hard metals without worrying about damaging the tools. This allows for the creation of durable parts for industries like aerospace, automotive, and medical devices, where high-strength materials are often needed.
No Mechanical Stresses
This helps reduce mechanical stresses in manufacturing by using a non-contact process to shape materials. Traditional machining methods involve direct contact between cutting tools and the workpiece, which can exert significant mechanical stresses.
These stresses can cause deformation or damage, especially on delicate or thin components. The pressure and force from the cutting tool can bend or warp these parts, leading to inaccuracies and potential failure in their final application.
Since EDM is a non-contact process, it does not exert mechanical stresses on the workpiece, reducing the risk of deformation or damage, especially on delicate or thin components. Instead of cutting the material, EDM uses electrical sparks to erode it. The electrode, which shapes the material, gets positioned close to the workpiece without touching it. When they come close enough, an electric field between them generates very hot sparks, melting or vaporising tiny amounts of the material. This process happens many times per second, gradually shaping the workpiece without any physical pressure or force.
Capability to Machine Hard Materials
The latter excels at machining hard and brittle materials that are tough or impossible to machine using traditional methods. Traditional machining relies on cutting tools that are harder than the material they cut. When these tools encounter extremely hard materials like hardened steels, carbides, and superalloys, they wear out quickly or break. This makes machining hard materials costly, time-consuming, and sometimes impractical.
EDM solves this problem by using electrical sparks to erode the material instead of cutting it. The process involves an electrode and the workpiece, both of which are conductive. Since there is no need for physical cutting, the hardness of the material does not affect the tool’s wear. EDM is particularly effective for machining hard and brittle materials that are difficult or impossible to machine using traditional methods, such as hardened steels, carbides, and superalloys.
As you can see, if they can use EDM, manufacturers can easily machine very hard materials without worrying about damaging or wearing out the tools. This allows for the creation of high-strength parts needed in demanding industries like aerospace, automotive, and medical devices.
Cerexio Solutions for Better Manufacturing Accomplishment
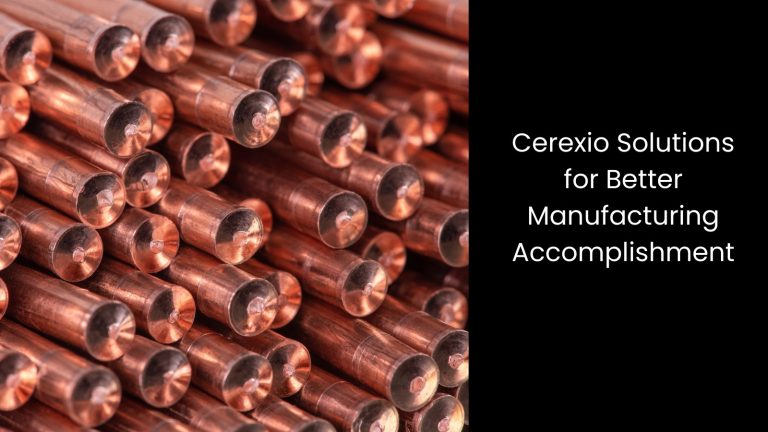
If you are targeting high levels of productivity in the manufacturing realm, you also need manufacturing solutions that can scale up your operations easily. Cerexio offers cutting-edge digital solutions that can cater to any sort of complex workflow easily due to its Industry 4.0 strengths.
Achieving High Levels of Manufacturing Precision via Electro-Discharge Machining
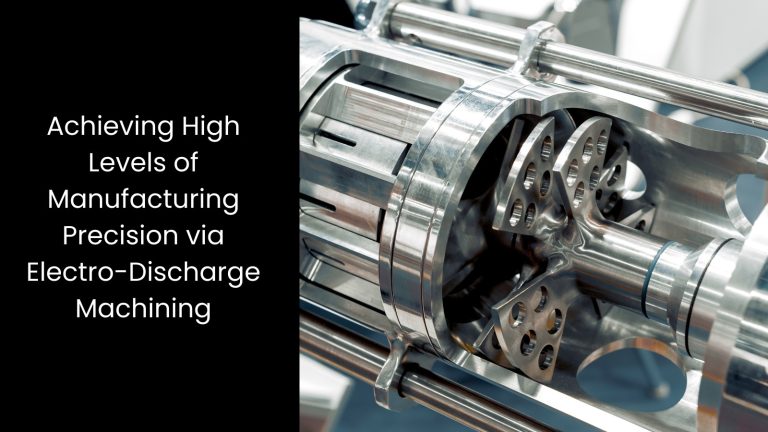
As you can see, EDM is a great way to stay away from inefficiencies on the production floor as it helps with machining various sorts of materials. If you need a sophisticated solution, EDM is your final destination, for sure.