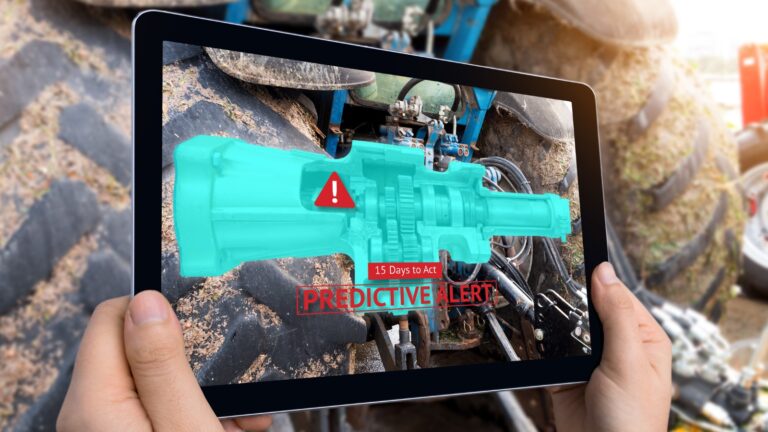
Predictive maintenance refers to a method whereby the system detects anomalies in assets in advance, warning asset managers to take steps to rectify them. Hence, instead of manufacturing companies facing downtime, predictive maintenance ensures that risks are eliminated, removing the possibility of the anomaly affecting the organisation’s overall operations. However, research studies have emerged noting certain drawbacks of predictive maintenance in terms of inaccessibility for SMEs as it requires advanced monitoring and data processing technologies. The lack of a statistical model moreover heightens this. Due to this, researchers have found the Failure Mode and Effective Analysis (FMEA) technique to be a better indicator for identifying maintenance time. This blog will describe what FMEA is and its relationship with predictive maintenance.
What is FMEA?
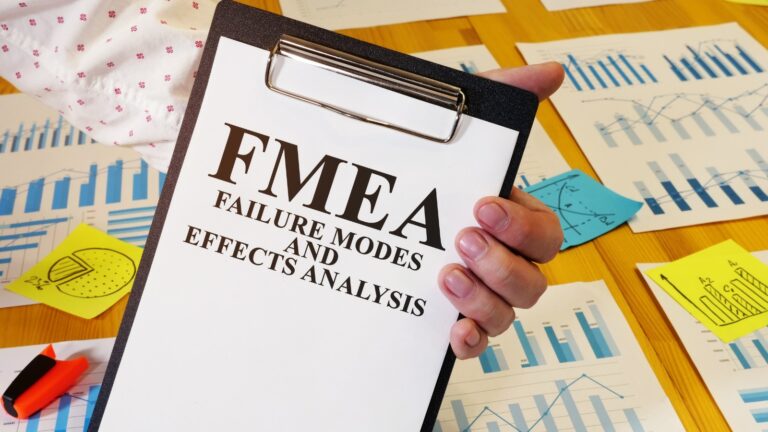
FMEA refers to a method adopted to identify failure modes to improve the reliability of products or components. Some refer to it as a qualitative reliability engineering method. This concept gained traction in the 1940s with the United States military, which was at the time trying to find a way to identify possible failures in design, manufacturing or the assembly process. Due to this, it is commonly also regarded as a process analysis tool.
In breaking down the exact concept of FMEA, ‘Failure Mode’ looks at defects that may potentially affect the consumer. ‘Effects analysis’, on the other hand, refers to the process of studying the results or consequences of those failures. A central aspect of FMEA is that it prioritises risks with the highest risk based on how serious the consequences are, how frequently they occur and how easily they are detected.
FMEA particularly allowed organisations to identify failures during the design phase or in some other aspect of the manufacturing process and address them before the end product is made. Consequently, two forms of FMEA emerged: Design FMEA (DFMEA) and Process FMEA (PFMEA). In the former, the methodology considers any tolerances, material properties, geometry, engineering noises and other factors to explore the possibility of a malfunction that may affect the lifecycle or safety of the product. The latter, in contrast, considers human and environmental factors, the machines and material used, and the methods used while processing to determine if anything has happened that could impact reliability, quality and safety. Some also consider a third category to be functional FMEA (FFMEA), which focuses on avoiding possible failure before corrective action is taken.
How Does FMEA Work?
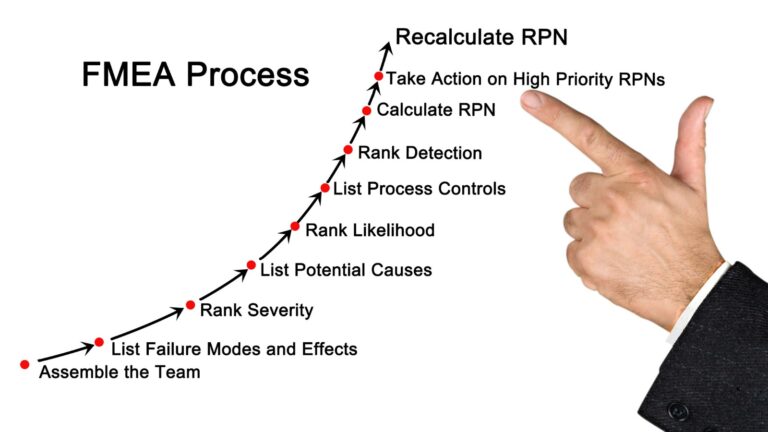
FMEA is typically adopted during a product’s designing or redesigning stage and is followed throughout. An example where FMEA is commonly used is in lean production. Whenever an organisation attempts to implement this methodology into their corporation, a specific order must be followed. While the exact number of steps may defer, approximately eight mandatory aspects must be regarded. Firstly, knowledge must be collected, particularly in terms of what consumers want based on design, quality, reliability and related factors. Using this knowledge, a company can secondly identify the scope of the product and define it. This afterwards broke down into a step-by-step process into different components. Fourth, start assessing each of the stages of manufacture and determine points of failure. This is followed by analysing the reasons behind failure and the effects of it. Based on the assessment made, a company would rank each failure as a sixth step. All of this will act as a foundational structure for step seven, which is when the company will develop strategies to detect, minimise, mitigate and solve failures.
The Relationship FMEA Has with Predictive Maintenance
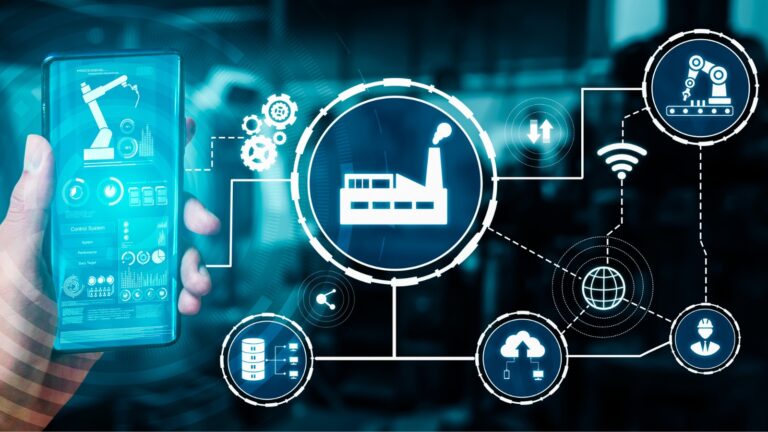
FMEA has been at the heart of many maintenance strategies, including reliability-centred, predictive, and preventive maintenance. In considering its complementary role in predictive maintenance, an FMEA provides a baseline to create a preventive maintenance schedule. Note, however, that this will require constant upgrades, requiring you to consider work orders and repair histories. Organisations should note that FMEA will be subject to changes based on whether a new asset is installed or designed into the factory, a new operator joins the team, or the machine’s operating mode specs are changed, a new reason for failure occurs and experience something new from a failed asset. FMEA, therefore, encourages companies to review their models for it to be an effective strategy that drives companies to fix the anomaly before the failure occurs.
While predictive maintenance today refers to integrating technologies such as the Internet of Things, it does not mean this is not part of the FMEA process. FMEA essentially provides the blueprint to run the predictive maintenance operations, without which a company’s preventive maintenance may not be as effective. One core reason why technology may be of relevance in FMEA is due to its reliance on data. The more data there is, the better it is for FMEA to help a business predict future breakdowns. But what kind of data is required? OEM guidelines, interviews with operators and technicians and work order data.
You Do Not Have to Replace One With Another
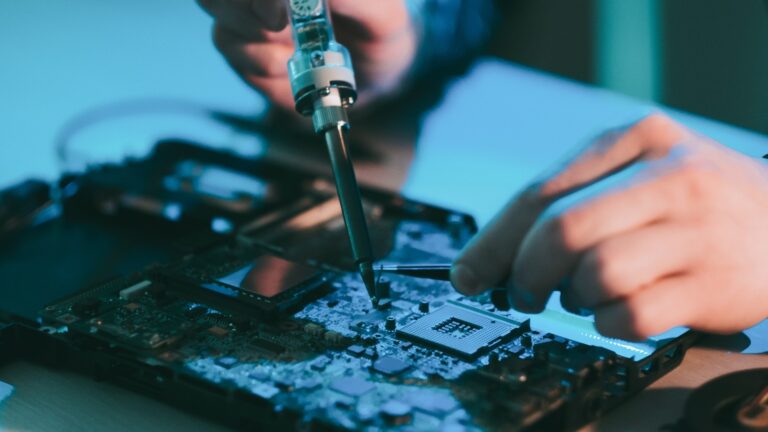
FMEA and predictive maintenance are not contradictory to one another. Hence, rather than asking yourself whether your predictive maintenance is effective, you need to consider whether it has a well-thought-out maintenance plan. This is where FMEA comes into play. Without a proper structure of the foundation in place, no matter how advanced your predictive maintenance system is, it will not be the most useful. To utilise smart predictive solutions and gain a paper return on investment, start by identifying all potential risks for an FMEA.
This article is prepared by Cerexio, a leading technology vendor that offers specialised solutions in the Advanced Manufacturing Technology Sector. The company is headquartered in Singapore and has offices even in Australia. Cerexio consists of a team of experts that have years of experience and holds detailed knowledge on a range of subject matters centric to the latest technologies offered in manufacturing and warehouse operations, as well as in predictive maintenance, digital twin, PLC & instrumentation setup, enterprise integrator, data analytics and total investment system.